Mitsubishi Chemical Performance Polymers
MCPP was looking for a simple and collaborative planning and scheduling solution.
With DELMIA, we estimate a planner’s time savings to be around 25%, from two to three hours a day thanks to reliable planning and better visibility.
Challenge
Mitsubishi Chemical Performance Polymers had difficulty managing its production rates due to the conduct of two parallel business activities that were managed by manual wall planning boards, which hindered planners’ capacity for proactive management.
Solution
The company chose Dassault Systèmes’ DELMIA Ortems Supply Chain Planning and Optimization solution to manage its global production facilities.
Results
Digital planning with DELMIA Ortems has reduced the time spent on planning activities by 25% (2 to 3 hours per day for each planner). Collaboration between the workshop manager, planning managers and the purchasing, procurement, production, IT and sales teams has improved resulting in less stress at work. Delivery commitments are better kept, resulting in an increase in customer satisfaction.
International Influence
Since the historical manufacture and production of shoe soles, Mitsubishi Chemical Performance Polymers (MCPP) France, a subsidiary of the Japanese group Mitsubishi Chemical, has considerably diversified to become one of the market’s leading manufacturers of thermoplastic elastomer (TPE) and polyvinyl chloride (PVC) products in advanced sectors.
The MCPP group has developed a network of production sites in the United States, Brazil, Asia Pacific and Germany and relies on three large plants in Poland and in France, the latter of which is MCPP’s largest manufacturing site. The group serves the automotive industry (airbag covers, seals, etc.), which is its leading market with a turnover of approximately 60% of its total activity as well as the building (shutters, pool covers), packaging, cable, consumer goods and medical industries.
Looking for a simple and collaborative scheduling and planning solution interfaced with SAP
MCPP France was finding it difficult to optimally manage its production rates due to the conduct of two parallel business activities, TPE and PVC. Two wall planning boards were required to manage these two activities, resulting in two daily manual data updates with SAP.
“Until recently, we were working on a wall planning with small paper cards that would at times fly away or fall down sometimes preventing tasks from even being processed. You can imagine the loss of time and the consequences caused by late deliveries or forgotten production,” Frédéric Gaborieau, responsible for TPE Market Planning at MCPP France, said.
These planning boards were difficult to manage because volumes were large and it was hard to make schedule changes caused by unexpected, last-minute or seasonal orders. This lack of flexibility prevented planners from being proactive, negatively impacting production deadlines. Moreover, the absence of an interface with SAP rendered management of raw materials tedious. What made things even worse was that only two experts mastered the wall boards, creating bottlenecks when they were not available.
“Controlling manufacturing deadlines and reducing cycle times are at the heart of our daily concerns,” Christophe Delafosse, IT manager at MCPP France explained. “Poland has its own planning tool and there is no identical information system in Europe; we cannot rely on a single common reference model today, which complicates data management for MCPP Europe”. To remain a leading provider of TPE products, it is crucial to take into account the production constraints of complex industrial environments and to work together with our colleagues in other departments.
To have better visibility on production planning while streamlining collaboration throughout the organization required questioning the company’s processes and work habits. MCPP France needed a simple and collaborative scheduling and planning solution that produces a single interdepartmental planning combining both its TPE and PVC activities and that would interface with SAP. The solution also had to optimize planning reliability for a period of more than two weeks, and to enable the company to anticipate seasonal orders and overall workload in order to meet delivery commitments while contributing to a harmonious relationship between the company’s various departments. MCPP France opted for Dassault Systèmes’ DELMIA Ortems Supply Chain Planning and Optimization solution to define a single interdepartmental planning repository to improve visibility and management of its global facilities.
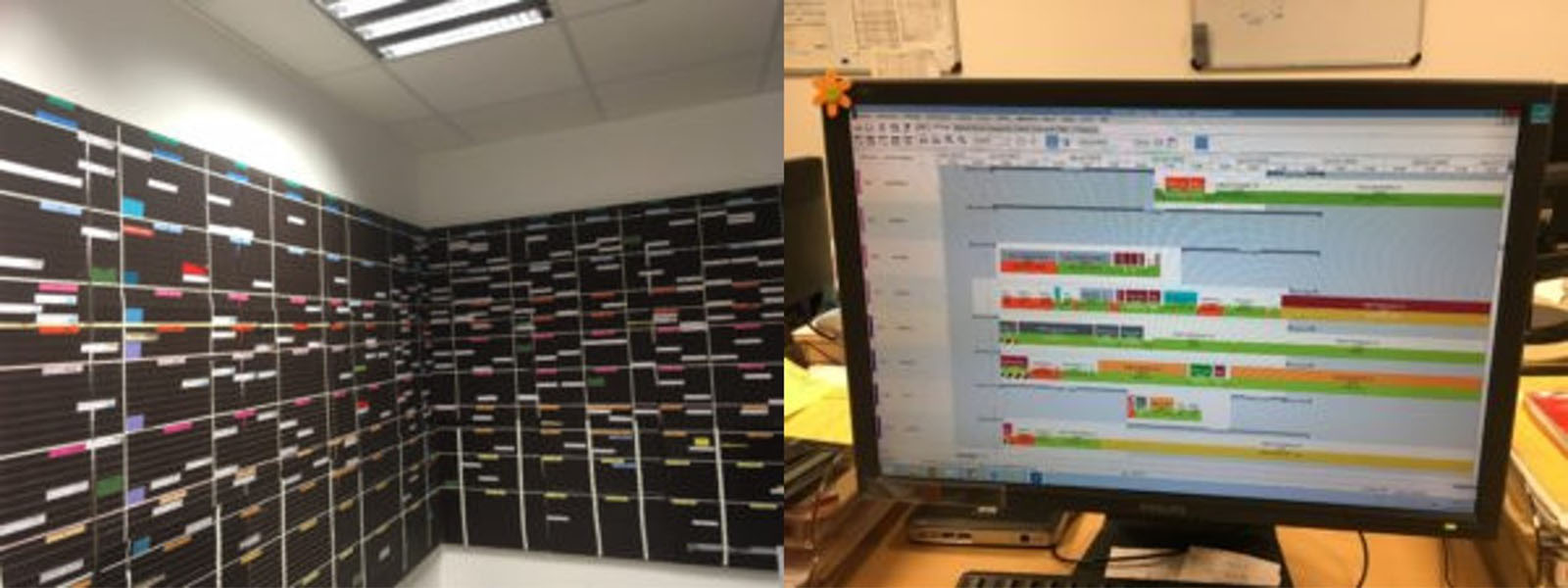
DELMIA: A collaborative solution based on a single repository
Processes are modeled and capitalized in the system along with planners’ expertise, ensuring the continuity of MCPP’s operations even when unexpected situations arise and the expert planners are not available. “When planners deliver by the end of the week the schedule for the weekend’s production activities and on Saturday there is an issue with delivery of a certain material or a machine breaking down, we need to retune the planning,” Frédéric Gaborieau said. “Since processes are capitalized in the system and thanks to DELMIA’s intuitive interface, we don’t need to call our expert planners in from their weekend to reschedule. The workshop manager can step in and use the system in a matter of minutes and can even perform the necessary simulations before actually reorganizing production. Since the system is linked with SAP, production can continue and everyone can go home less stressed. DELMIA helps us easily resolve many difficult situations,” he said.
Moreover, efficiency and responsiveness are increased within the various purchasing, supply, production, logistics, IT and sales teams. “We now save 50% of our time, which was previously spent on the phone between trade and supplies,” Frédéric Gaborieau said. With DELMIA, the workshop manager can now anticipate his workload and his material and staff needs. This is all the more crucial as it takes at least three weeks to train an operator. From now on, alerts concerning shortages can be used to optimize orders in advance. A real breakthrough has been made within the company in a matter of weeks since DELMIA was implemented.
“It’s much easier to plan, it’s visual and the solution interfaces well with SAP, which saves us a lot of time. In effect, we can now manage 150 sheets per TPE machine, impact management is under control and we can more efficiently group our orders together. DELMIA helps us make better decisions,” Frédéric Gaborieau said.
Substantial productivity gains
Time savings were significant and immediate. DELMIA optimally schedules orders to reduce machine cleaning times between two productions. In addition, the solution, by reorganizing MCPP production, makes it possible to limit the number of changes and optimize preparation, cleaning and mass production times. The interface with SAP enables the company to anticipate raw material shortages. Moreover, it is now possible to take into account orders for the next six months.
“We estimate our time savings to be around 25%,” Christophe Delafosse said, “because each planner can save two to three hours a day and can consider evolving toward other missions in the short and medium term. We have a reliable planning for each of our two activities - TPE and PVC - and this, with better visibility.”
Improved collaboration between all stakeholders thanks to better visibility of the planning also enhances productivity and reliability in terms of meeting delivery dates. This is because decisions are based on common, shared and up-to-date information.
Even the Sales Administration department, which manages its working methods differently, assimilated the changes brought about by the new solution. The sales department now enters the delivery time given to the customer as soon as the order is placed, which positively impacts the way sales teams manage their time.
Improve cash flow
Extending the solution to MCPP’s Polish facilities would drive productivity up even further.
“Implementing DELMIA in our factory in Poland would allow us to have a global planning solution since we manufacture the same products as in France,” Christophe Delafosse said. “Moreover, we soon plan to use this tool to measure the impact of the way the plant is managed. Thanks to this solution, we could even reduce our inventories and, thus, better manage our cash flow.”
A fast ROI in less than 10 months
The implementation of the DELMIA Supply Chain Planning and Optimization solution was a real success due to the strong involvement of the MCPP and DELMIA Ortems teams. “We worked hand-in- hand with real solution experts,” Christophe Delafosse said. “The solution was deployed and operational in less than 10 months.”
“Overall, the specification and optimization phases went well “to such an extent that only two days after the launch, we decided to remove the wall panel even though we initially planned to keep it as a back-up solution for one month,” Frédéric Gaborieau said.
The project continues to move forward thanks to a very efficient team of third party maintenance experts, who always provide pertinent answers and regularly present us with new opportunities for improvement,” Christophe Delafosse concluded.
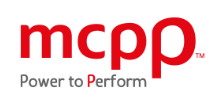
Focus on Mitsubishi Chemical Performance Polymers
Specializes in polymer design and compounding for the development and production of specialty thermoplastics
Products: Thermoplastic Elastomers, flexible & rigid vinyl compounds, compounds for slush molding, functional polymers, polyolefins, biodegradable polymers
Employees: Part of Mitsubishi Chemical Holdings Corporation (MCHC) with over 68,000 employees
Headquarters: Tokyo, Japan
For more information: mcpp-global.com
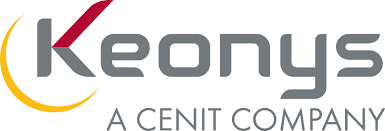
Focus on KEONYS
KEONYS, a Cenit Company, is the #1 value-added reseller of Dassault Systèmes worldwide, and of the entire software portfolio: CATIA, DELMIA, ENOVIA, SIMULIA, 3DVIA, and the 3DEXPERIENCE® platform. KEONYS is a major player in supporting and advising companies in their digital transformation in line with the objectives of the Industry of the Future Plan.