L'OCCITANE en Provence, Laboratoires M&L
Handling the formulation and production of natural cosmetics for L’OCCITANE Group, Laboratoires M&L – L'OCCITANE en Provence embraces simulation and virtual twins on 3DEXPERIENCE to run an efficient, sustainable and safer factory that prioritize workers’ health and safety.
Smart and safe factory for unique cosmetics experiences
Even from its wooden façade exterior, it’s clear that the production facility of L'OCCITANE en Provence – Laboratoires M&L set in Lagorce, France, is no ordinary factory. Set among the wilderness of the Ardèche region, this is a factory designed to blend into the surrounding environment and co-exist with nature.
Responsible for producing natural cosmetics, oils and fragrances for L’OCCITANE Group brands L’OCCITANE and Melvita, the facility has 1,800 m² of green roofing, 12 light wells, 80 m² of solar panels for preheating water and 10,000 m² of Finnish willow trees to cleanse production sewage after processing by its wastewater treatment plant. It also has more than 4,500 m² of photovoltaic panels, which produce enough electricity for up to 25% of the site's needs, targeting 90% by 2030. Inside, workstations are configured to promote good posture and comfort for each individual operator, and digital technologies simulate shop floor conditions to prioritize worker safety.
For a company that prides itself on carefully sourcing and creating some of the most sustainable and natural cosmetic products on the market, it’s fitting that Laboratoires M&L puts the well-being of its people first too. “It’s essential to have our employees work in a safe, comfortable, inclusive and diverse environment so that this can shine through internally and externally,” said Richard Vinardi, industrial strategies director at Laboratoires M&L, L’OCCITANE Group.
The virtual twin allowed us to evaluate situations that cannot be observed in everyday life
Driving Laboratoires M&L’s proactive health and safety policy is an initiative called MyHealth@Work – in which Dassault Systèmes contributes with the 3DEXPERIENCE Cloud platform to develop a virtual twin of the Lagorce facility and its production lines to monitor and prevent occupational health hazards. With over 200 employees working at the Lagorce site, composed of 60% women and 40% men, all of various ages, the company wanted to assess individual postures at workstations to determine the risk of joint or musculoskeletal issues and understand how different genders could be affected.
“MyHealth@Work aims to evaluate work areas, especially ergonomic postures at workstations and on packaging lines,” said Maxime Plazolles, innovation engineering project manager at Laboratoires M&L, L’OCCITANE Group. “We started from simple observations: the increase in illnesses and reported issues related to discomfort on packaging lines. We then screened a wide range of postures according to population percentiles. The virtual twin allowed us to evaluate situations that cannot be observed in everyday life.”
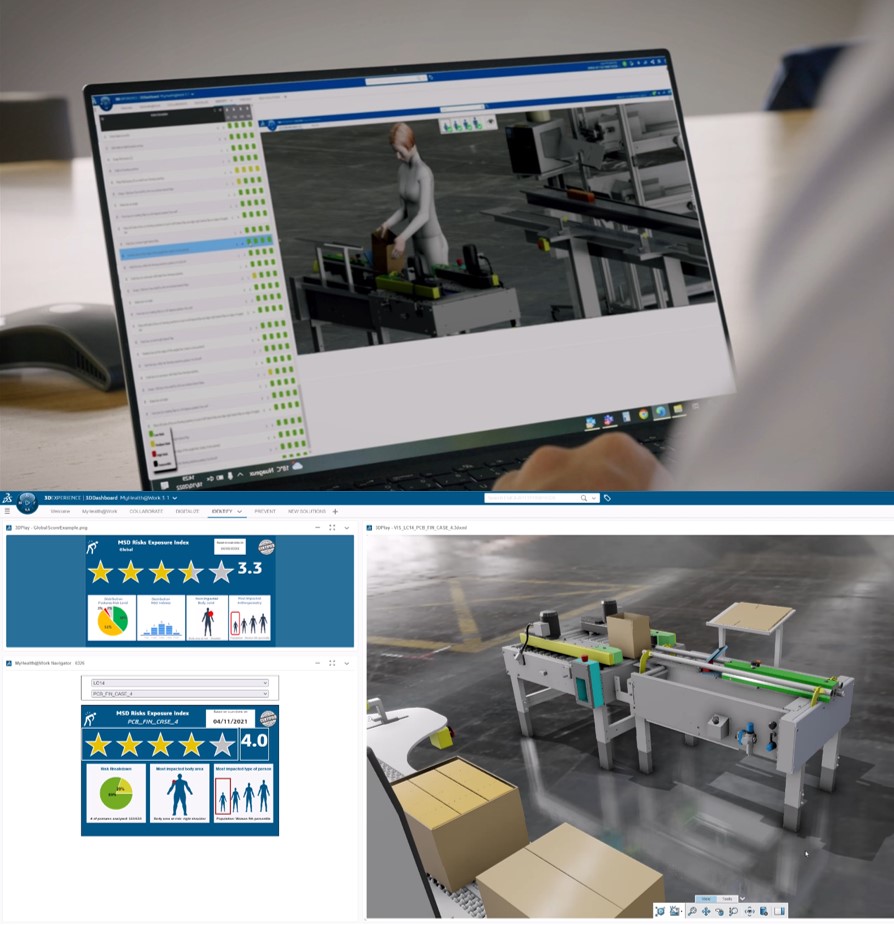
Virtual twin on the shop floor and beyond
What began as a standalone proof of concept (POC) – a project to simulate workstations and prevent the occurrence of musculoskeletal disorders among staff members – has since evolved into an exciting partnership between Laboratoires M&L and Dassault Systèmes. Together, they are exploring how else virtual twins can be used to enhance staff well-being and improve operational efficiencies.
“We ended up scanning the entire plant, because we realized that the solution offered real evolutionary power, which could allow us to invest in new lines, but also to ensure that, when purchasing new lines, we were closer to getting it right the first time, which is ultra-important in our sector,” Plazolles said. “It’s a partnership which allows us to generate knowledge, develop skills and benefit from emerging technologies in a pioneering way and identify areas of value.”
The vision for Laboratoires M&L’s Lagorce site is to create a new local industrial model to connect people, performance and nature.
“In this vision, we have people at the center of what we do, and for them we have an ambition for zero accidents on site,” said Aurélie Declef, Lagorce plant director at Laboratoires M&L, L’OCCITANE Group. “For us, zero accident is a choice, not a chance.”
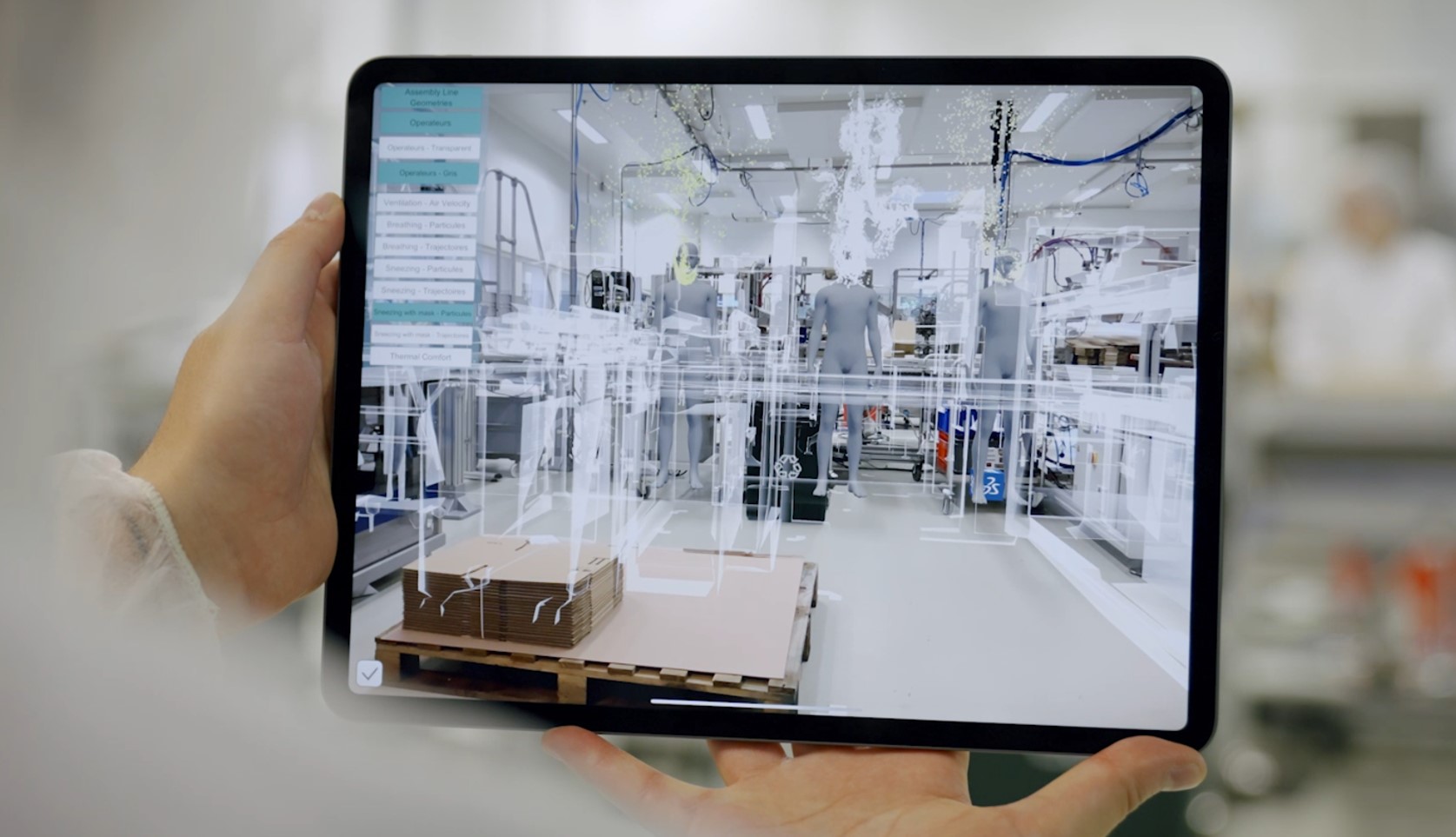
Understanding pathogen transmission
A great example of MyHealth@Work in action was when Laboratoires M&L wanted to better understand the spread of the viruses and determine how to better protect its workers and maintain high productivity levels on the production line. Dassault Systèmes was tasked with simulating the scenarios.
Laboratoires M&L provided 3D models of the facility’s architecture and the Dassault Systèmes team computed airflow data – air renewal, air recirculation, outside air supply, and air outflow. This was used to create a virtual twin of the full shop floor to run airflow and pathogenic propagation scenario simulations of the packaging line using DELMIA and SIMULIA fluids solutions.
“Thanks to SIMULIA PowerFlow, we have been able to make visible the invisible,” Plazolles said.
As a result of the simulations, the company discovered there were measures it could put in place to protect its workers, including repositioning air vents to avoid creating zones that are less ventilated than others.
“We also discovered that the plexiglass screens we’d installed on the shop floor were not as effective as masks for protecting workers,” Plazolles said. “This kind of data can be fully capitalized on for the new lines we may purchase in future.”
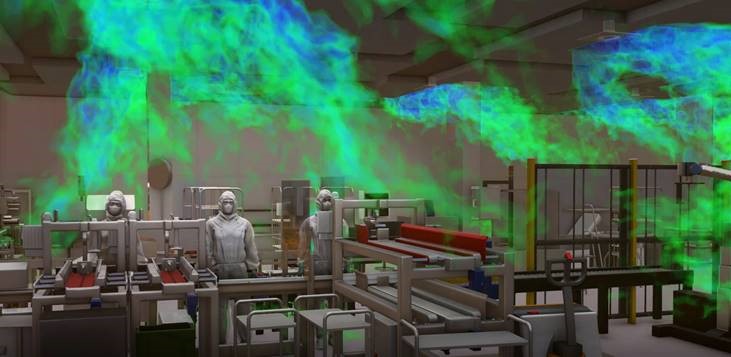
Simulating thermal flows
In combination with pathogen circulation, Laboratoires M&L wanted to understand the thermal conditions of the Lagorce facility, particularly how much certain areas of the shop floor heated up during specific periods. Workers reported times when they were too warm and Laboratoires M&L felt there were steps it could take to improve their comfort.
“The goal was to understand increases in temperature, how heat is generated, and where from,” Plazolles said.
Again, using the same virtual twin of the shop floor, the Dassault Systèmes team carried out thermal simulations of the environment, covering equipment like small conveyor motors, which radiate heat. SIMULIA fluids solutions enabled the team to simulate production scenarios at different times of the day to determine which areas of the shop floor radiated heat and were exposed to sunlight, and how it affected the comfort of the operators during hot, summer days.
“SIMULIA enabled us to question the temperature settings of the area, taking into account solar radiation, so that temperature rises can be controlled right to the edge of a room,” Plazolles said. “It would have been so complicated to measure this in the real world. Yet with the virtual twin and the simulations, we could visualize these scenarios and understand what was happening.”
Laboratoires M&L sees benefit in simulating conditions in advance before making changes.
“In the future, we also see the value of carrying out noise simulations, especially in areas where earplugs are compulsory, and seeing the relationship between thermal and aeraulic systems,” Plazolles said.
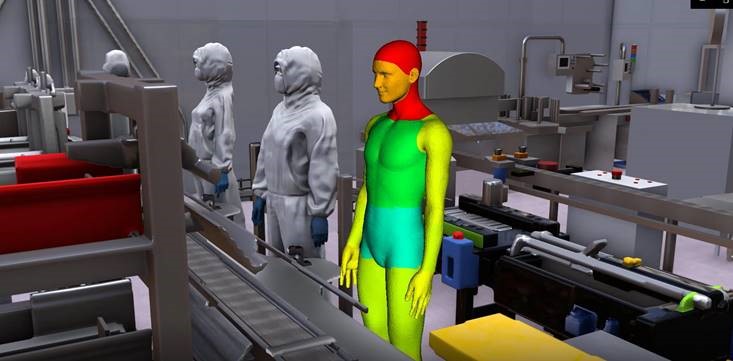
Why outsourcing made sense
Outsourcing these kinds of projects to Dassault Systèmes and taking advantage of the Virtual Twin as a Service approach was a win-win for Laboratoires M&L.
“We realize that the 3DEXPERIENCE platform requires expertise to be used to its full advantage,” Plazolles said. “This activity is not our core business. However, it's Dassault Systèmes’. Outsourcing to its teams enables us to carry out several projects at the same time. They work to our schedules and allow us to test new technologies.”
Through this partnership, Laboratoires M&L has the opportunity to try out emerging technologies and provide input to get the desired outcome. The partnership also allows the company to quickly scale up, bring in additional resources when needed to keep projects on track, and bring transformational benefits to the organization.
“I can detach and dedicate tasks to the Dassault Systèmes teams to expand my bandwidth and get faster results,” Vinardi said. “We also benefit from expertise that we don't necessarily have internally. The teams we worked with were able to enrich the projects, adding value through their experiences from other sectors and partnerships.”
While the company recognizes that this type of arrangement is not commonplace in its industry, it believes that outsourcing specific IT projects is the way forward.
“This approach allows us to gradually get our feet wet without the need to develop this type of skill in house with all the associated infrastructure,” Plazolles said. “We’ve become a hybrid organization that moves ahead and pursues digital innovation while controlling costs.”
And because all these digital projects are handled in the cloud, Laboratoires M&L benefits from round-the-clock access and all the collaboration benefits that come from working in a centralized, online environment.
“Internally, we are based on several different sites,” Plazolles said. “The 3DEXPERIENCE Cloud platform enables us to exchange messages, share documents, and benefit from content and deliverables in the cloud. It also allows us to easily work with Dassault Systèmes. Ultimately, everything converges on the platform.”
Evaluating production lines virtually
Laboratoires M&L is now looking at how it can use the 3DEXPERIENCE Cloud platform, virtual reality and Dassault Systèmes’ simulation services to optimize the setup of its production lines.
“Before, when we bought a packaging line, there were a lot of things that we discovered as we went along,” Plazolles said. “Ramp-up phases could last from 6 to 18 months. The objective is to reduce these ramp-up phases, and to quickly increase throughput using immersion in virtual reality to anticipate what we call clashes – blocking points, safety and environmental issues.”
“By virtually simulating real future situations and involving operational staff as well as stakeholders, we can identify situations that would only have been observed after the project was completed,” Vinardi added.
Today, Laboratoires M&L can use the simulations to determine when it needs to buy new equipment, but also how to integrate new production lines into its manufacturing facilities.
“We have just invested in a new tube line,” Declef said. “With Dassault Systèmes, we created an immersive experience using virtual reality allowing operators to project themselves in the future of this new line, and ensure that the workstations are set up according to their feedback.”

Staying on task in production
Laboratories M&L has used DELMIA since 2013 to manage its production and procurement flows. Over the years, the solution has helped the company to optimize its production and logistics processes at all levels.
“DELMIA brought a great deal of discipline, traceability and organization to production,” Plazolles said. “It has really enabled us to increase output and better organize ourselves.”
When the company sought to improve collaboration and transform its meetings and follow-up processes on the shop floor it made sense to try out DELMIA 3DLean functionality. The production teams use the digital visual management dashboard and shared environment on the cloud to support their meetings, share daily tasks and make informed decisions.
“Before, we had several whiteboards, which workers referred to every day to carry out their roles,” Plazolles said. “3DLean allows us to manage these tasks on digital screens, and give team managers, activity managers and manufacturing operators a clear view of what’s happening.”
DELMIA 3DLean not only helps to improve communication between different teams, but also shares information in more intuitive and accessible ways.
“It helps us respond to different issues and improve scheduling,” Plazolles said. “Work instructions are given to the right people and we can see a live visualization of each worker’s location. We already have field managers directly controlling production with this solution and achieving great results.”
Building a healthy sustainable workplace
Laboratoires M&L takes its role as a steward of the planet seriously and believes digital technologies unlock many opportunities to further reduce the company’s environmental impact across the value chain.
“The long-term opportunities of digital solutions, especially of virtual twins, are very clearly to accelerate our ecological transition and maximize energy efficiency opportunities,” Vinardi said.
“I am firmly convinced that we can generate real value in other fields such as AI, formulation, task automation, supply chain and lifecycle analysis,” Plazolles added. “For example, to measure the ecological and environmental impact of a product, to decide whether to use a particular packaging line or another to mitigate its carbon impact. In the future, we might qualify and simulate the entire energy consumption of a building to better identify the opportunities to reduce it.”
Working with Dassault Systèmes, Laboratoires M&L is able to continue focusing on its own decarbonization and biodiversity initiatives, while building its digital capabilities to achieve positive, meaningful change. “Ultimately, we’ve found value, efficiency and opportunities for a cleaner, greener future,” Plazolles concluded. “The partnership gives us reliable, robust results. It will help us to write a new chapter in the history of Laboratoires M&L for the L’OCCITANE Group.”
Discover more about the Integrated Built Environment industry solution experience.
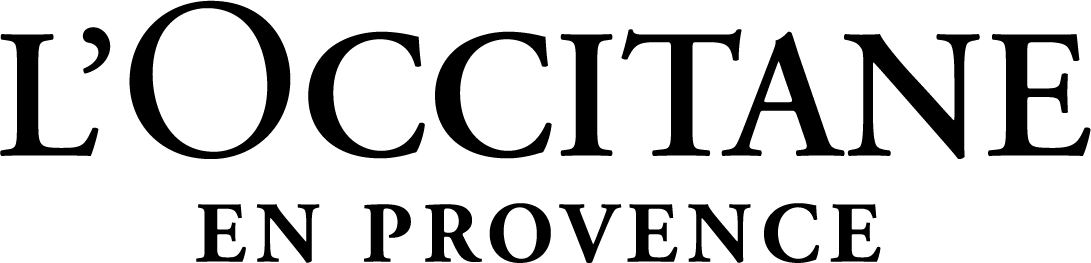
Focus on Laboratoires M&L, L'OCCITANE en Provence
Laboratoires M&L handles the formulation, production and primary logistics of cosmetics and well-being products for L’OCCITANE Group, a major international manufacturer and retailer of skincare, beauty and wellness products based on natural or biological ingredients. Its portfolio of premium beauty brands includes L’OCCITANE en Provence, Melvita, Erborian, L’OCCITANE au Brésil, LimeLife by Alcone, Elemis, Sol de Janeiro and Grown Alchemist. With its nature-positive vision, L’OCCITANE Group is committed to investing in communities, biodiversity, reducing waste and to finding regenerative solutions in order to create a better and healthier planet.