Efatech
As it continued to expand globally, Turkey-based manufacturer of sewing automation systems Efatech wanted to complement its existing 3D design software with effective product data management capabilities. The company implemented the Dassault Systèmes' platform on the cloud and its Digital Equipment Continuity industry solution experience as well as Collaborative Designer for SOLIDWORKS, unlocking new efficiencies in every part of its design and development process.
Transforming the textile industry with sewing automation systems
Textile manufacturing remains one of the most labor-dependent industries worldwide. Processes such as hemming jeans, attaching washing machine instructions or ribbon loops for hanging – and even turning trousers inside out – are laborious, time-consuming jobs that are still largely done by hand.
Turkey-based company Efatech believes it is time for the textile industry to catch up with other sectors. That’s why it has developed a range of sewing automation systems that can do in seconds what can take many minutes for a human to do.
Efatech’s founders pride themselves on their extensive knowledge of the textile industry, which enables them to deliver innovative, customized automation solutions that meet their customers’ needs. Since its inception in 2014, Efatech has grown considerably by delivering a personal, high-quality service. Today, it exports 70% of its products and serves customers in over 40 countries worldwide – and it is expecting these numbers to grow as it leverages more of Dassaults Systèmes' solutions on the cloud.
With the Dassault Systèmes’ platform on the cloud, we can access the right information at the right time, from anywhere in the world. We can showcase our products to customers on mobile, evaluate change requests faster than ever before and minimize mistakes.
Challenge
As Efatech has expanded its geographic reach, its complexity has also increased. Its portfolio of robotic machines has grown considerably, and each product can consist of thousands of parts – many of which are customized to meet bespoke customer requirements. The design data related to these products and parts is created in SOLIDWORKS®, and stored across various servers that were painfully slow to access, particularly from outside of the local network. As a result, Efatech’s distributed research and development (R&D), sales and manufacturing teams were finding it difficult to get timely access to the data they required and often were unsure if the data they did manage to access was up to date.
Change management was also time- and resource-intensive. Sales staff were showing customers physical drawings of their products, and then verbally communicating change requests to the R&D team. Working in this way often resulted in multiple iterations and a lot of emails back and forth.
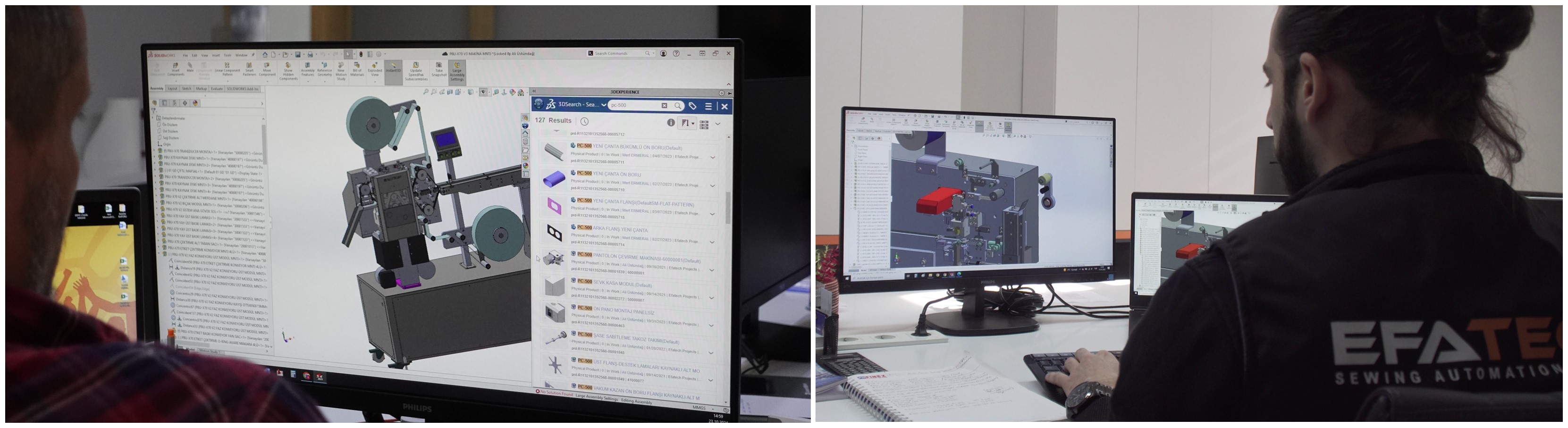
Solution
Efatech already had a good working relationship with Dassault Systèmes business partner Yenaplus, who had managed the initial implementation of its SOLIDWORKS design software. Having turned to the partner again for help, Yenaplus demonstrated how the Dassault Systèmes' platform on the cloud, including ENOVIA for product data management, could help it gather all information related to its products in a single, centralized location.
The company was particularly impressed by the cloud-based infrastructure that would enable its various teams to securely access and collaborate on design data from any location, as long as they had an internet connection. Sales teams are now able to share up-to-date 3D drawings with the customer on-site from their mobile phone and even manage change requests remotely.
Yenaplus provided initial training and helped the company to import its legacy data – a process that was completed in just two months. The teams at Efatech were able to familiarize themselves with the platform immediately as the company was implementing a cloud-based solution right out-of-the-box.
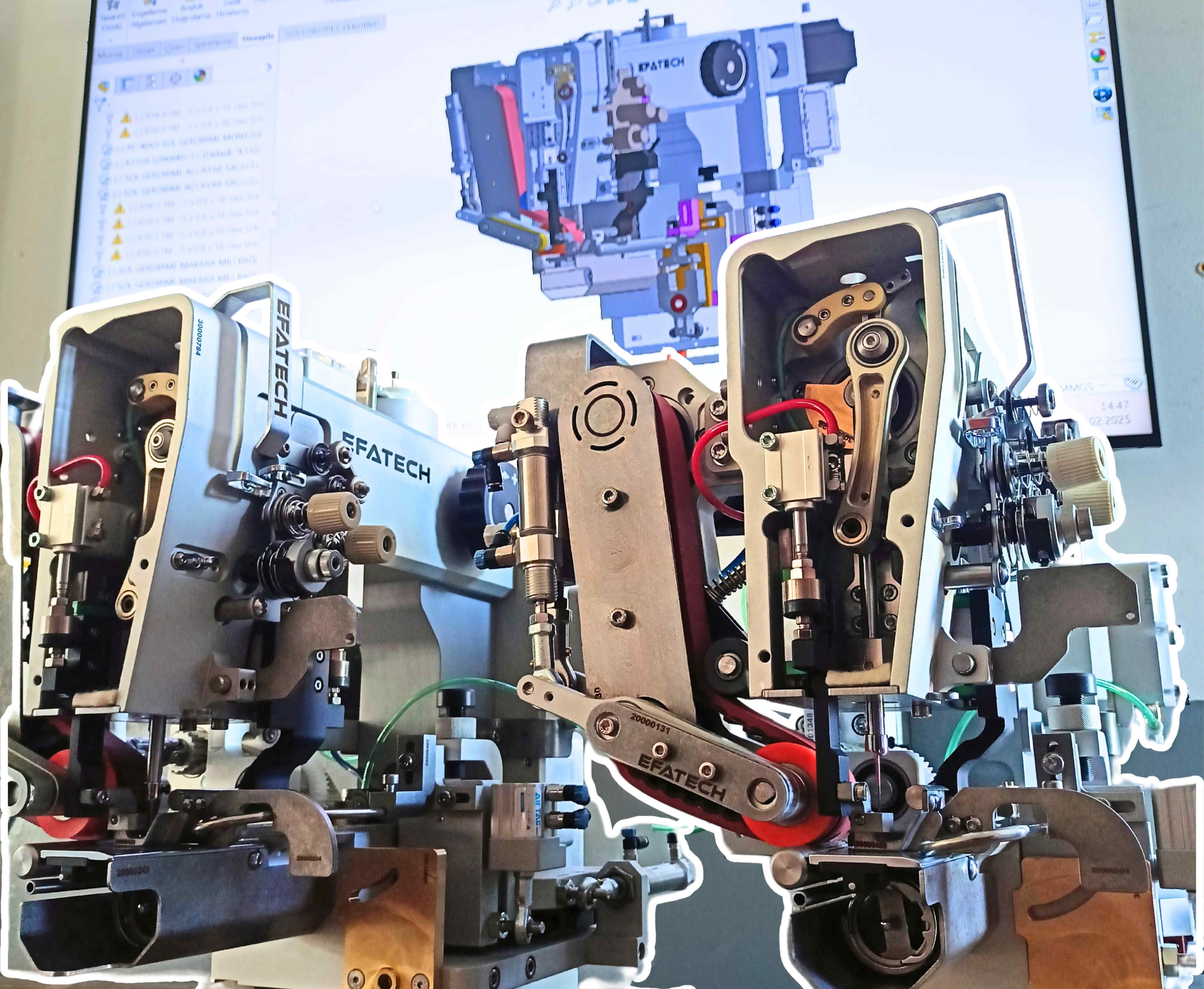
Benefits
By adopting the Dassault Systèmes' platform on the cloud, Efatech has been able to unlock new efficiencies in every part of its design and development process.
For example, using Collaborative Designer for SOLIDWORKS, Efatech can store, access and share design data within its native SOLIDWORKS design interface on the platform. Having all data in a single location, all departments can see and collaborate on up-to-date versions of a machine’s design in real-time.
With ENOVIA’s product data management capabilities, the SOLIDWORKS designs and the huge amount of data related to those products and all their individual parts – such as the materials used, paint details, and any hardening, anodizing, rubber coating or chemical processes required – are saved in an organized manner. Each part is labeled with a unique code, for error-free communication, reducing the likelihood of mistakes at the design, manufacturing and post-production stages.
Change management has also improved. Now that Efatech has a comprehensive parts library, it’s easy for designers to reuse existing parts in future products, saving a significant amount of development time.
Once a product has been engineered according to a particular customer’s needs, sales staff can showcase the designs in 3D using their phone or tablet. Depending on the customer feedback, they can add comments or make change requests for the R&D team directly within the platform. This process is already accelerating the approval stage of product development.
In the coming years, Efatech hopes to benefit from even more of Dassault Systèmes platform’s capabilities. For example, the company is considering leveraging DELMIA to define, compare, manage and update a manufacturing bill of materials (BOM) from an engineering BOM to facilitate design for production.
This future vision will help Efatech grow its production capacity further with less complexity. Being able to operate with greater operational efficiency and productivity will help it export up to 100% of its machines – and ultimately position the company as a market leader.
Q&A textile industry
Textile automation companies like Efatech are facilitating automated processes for textile manufacturing companies the world over. Efatech’s innovative solutions leverage robotics to do in seconds what can take many minutes for a human to do. In a single hour, its bottom hemming machine can hem 250 pairs of jeans, its loop attacher can sew in 1,250 loops, and its turning machine can turn 350 pairs of trousers inside out. Meanwhile, its label sewing machine can easily do the work of six people – and there’s no need for an operator.
One vision for the future of automation in the textile industry is ‘dark factories’ that leverage both AI and automation technology to operate without the need for humans. Fully automated factories can improve productivity and enhance operational efficiency – reducing the costs of textile manufacturing.
Discover more about the Digital Equipment Continuity industry solution experience.
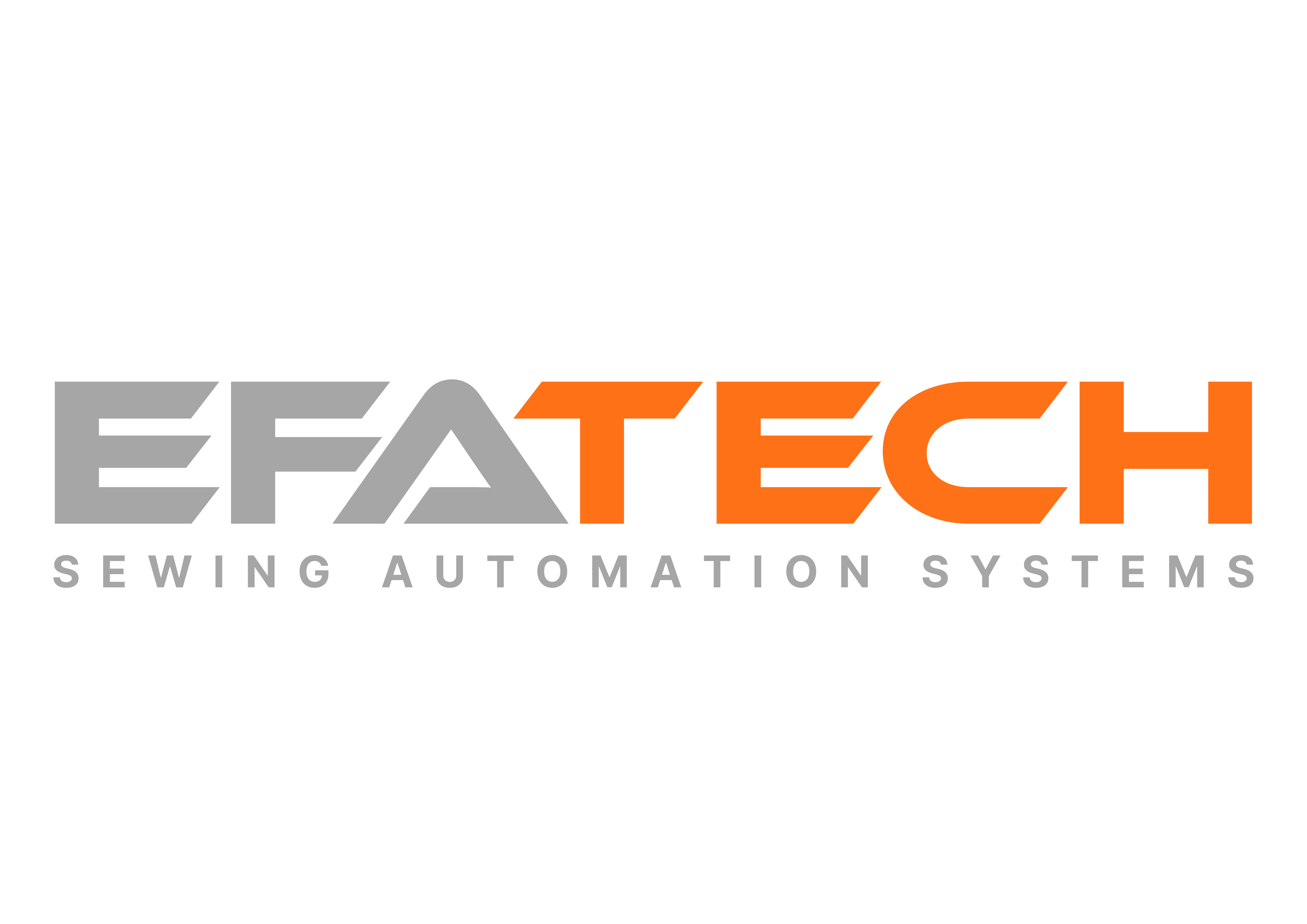
Focus on Efatech
Founded in 2014, textile automation software company Efatech provides innovative robotics systems for textile manufacturers across the globe. Since its beginnings, the company has prided itself on its ability to listen carefully to its customers’ precise needs and deliver customized, patented machines that are built to last. Today the company employs over 30 people and serves customers in over 40 countries.
For more information: https://efatech.com.tr/en
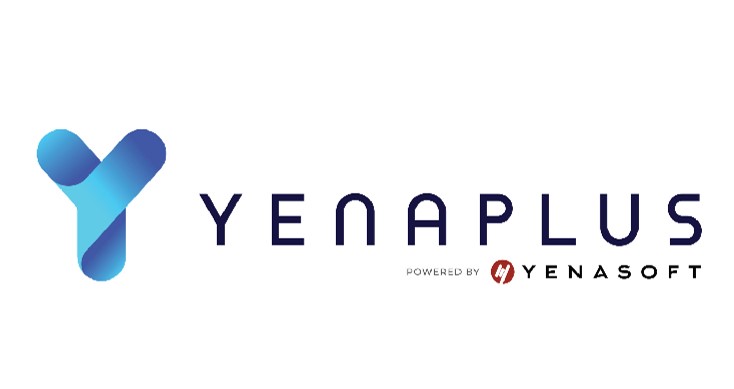
Focus on Yenaplus
With over 25 years of experience in the software industry, Yenaplus is a Dassault Systèmes channel partner with a focus on delivering exceptional customer service. By integrating the full capabilities of the 3DEXPERIENCE platform, including the ENOVIA, CATIA, SIMULIA and DELMIA solutions, Yenaplus ensures that its clients remain one step ahead of their digital transformation journey. Thanks to its purpose-built Yenaplus software called Yenatools, the partner can complete the tedious work that used to take days in seconds, saving its customers both time and money.