Changshu Innovation
In its quest for digital transformation, Changshu Innovation from China has adopted industry solution experience Digital Equipment Continuity. With the 3DEXPERIENCE platform on Cloud, Changshu Innovation's engineers can now share secure data with their colleagues while working off-site, and even invite their clients to collaborate directly.
Digital transformation for a traditional enterprise
When Hou Shi inherited Changshu Innovation, her father’s welding equipment business, she was determined to make it a success. For her, that meant challenging the company’s legacy practices and sharing the wisdom of her youth. She was particularly passionate about bringing the company into the 21st century through digital transformation and cultivating talent to maximize employee value.
Changshu Innovation supplies modern welding equipment, including Tungsten Inert Gas (TIG) welding robot workstations and various inspection tools, to auto part manufacturers. The company also supplies cross car beams, seat frames, door anti-collision rods, front and rear anti-collision beams, front and rear subframes, control arms, torsion beams and other arc welding products.
Challenge
Shi encountered a variety of problems when it came to modernizing Changshu Innovation. First, the company’s mode of management didn’t match its development needs. Isolated and fragmented information caused an information lag between the sales and mechanical design teams. What’s more, a reliance on document-based processes meant that internal communication was inefficient, work was often duplicated and there were regular misunderstandings.
At the same time, knowledge about key projects was held among a small fraction of the workforce. With no process in place to accumulate and transmit such business information, the company was at risk of losing its intellectual property. In addition, the R&D department preferred to work with existing, familiar technology solutions. This meant collaboration and knowledge transfer with the rest of the team wasn’t particularly effective. It was felt that the overall inefficiency of collaboration and knowledge transfer among team members, especially for new entry designers, was detrimental to the company.
In addition to this, as the team expanded and orders grew, it was struggling to keep on top of orders. This problem was exacerbated by its distributed file management which meant designs were often located on individual desktops and there was no central repository of parts. After-sales service teams conducting maintenance often felt disconnected since they had no way of accessing or sharing troubleshooting information from off-site locations.
What Changshu Innovation needed was an interactive collaboration platform that could improve efficiency and save costs. The platform needed to be accepted by its sales and R&D team, while helping it digitally transform at speed. Since the company doesn’t have its own internal IT team, the chosen platform also needed to be on cloud, so that it’s secure and easy to manage.
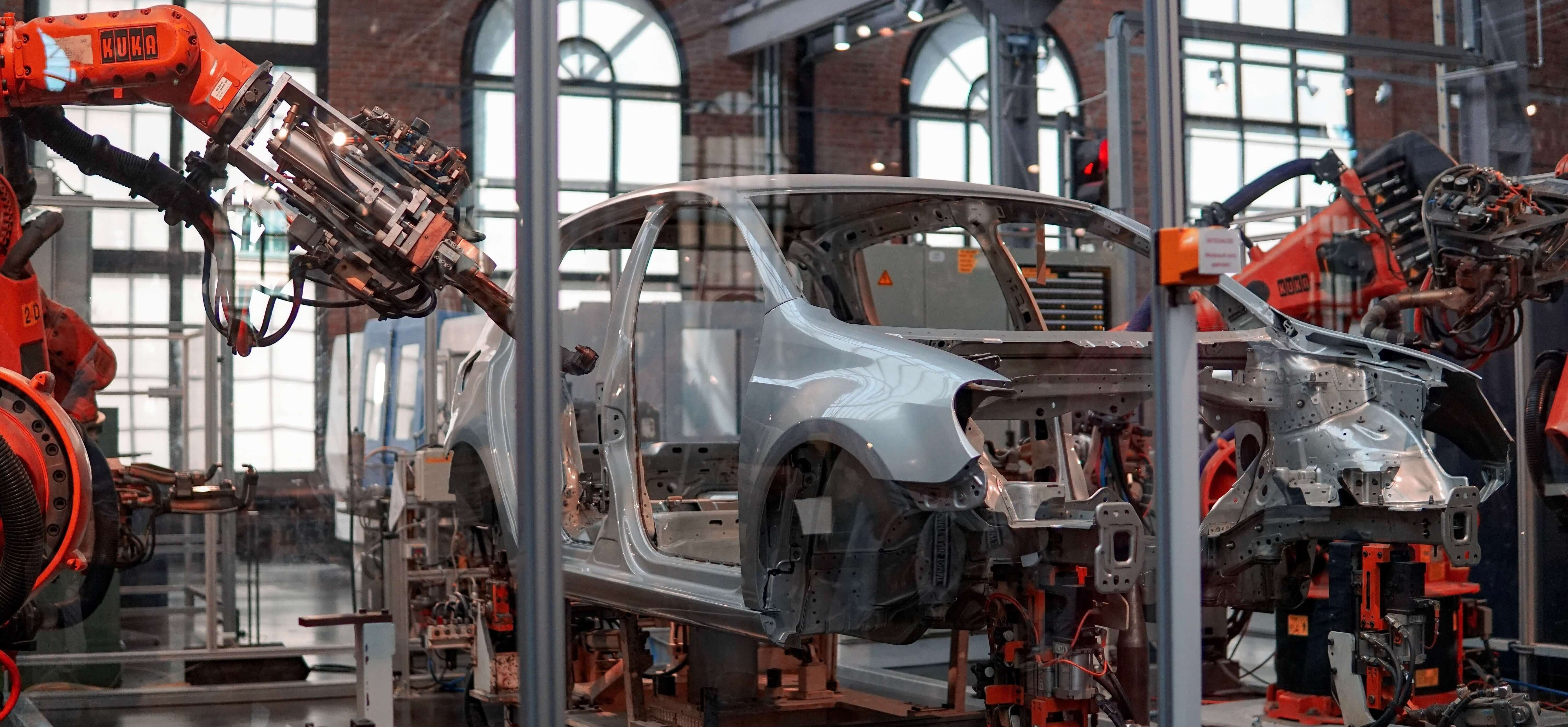
Solution
As a natural step on from its existing CATIA V5 environment, Changshu Innovation chose the 3DEXPERIENCE platform on Cloud with industry solution experience Digital Equipment Continuity. This would seamlessly bring together all stages of product development, using a familiar user interface, and without the need for hardware installation or IT management.
With ENOVIA powered by the 3DEXPERIENCE platform on Cloud, the company now benefits from capabilities like product lifecycle management (PLM), change management, intellectual property protection and reuse as well as easy collaboration across departments and improved project management.
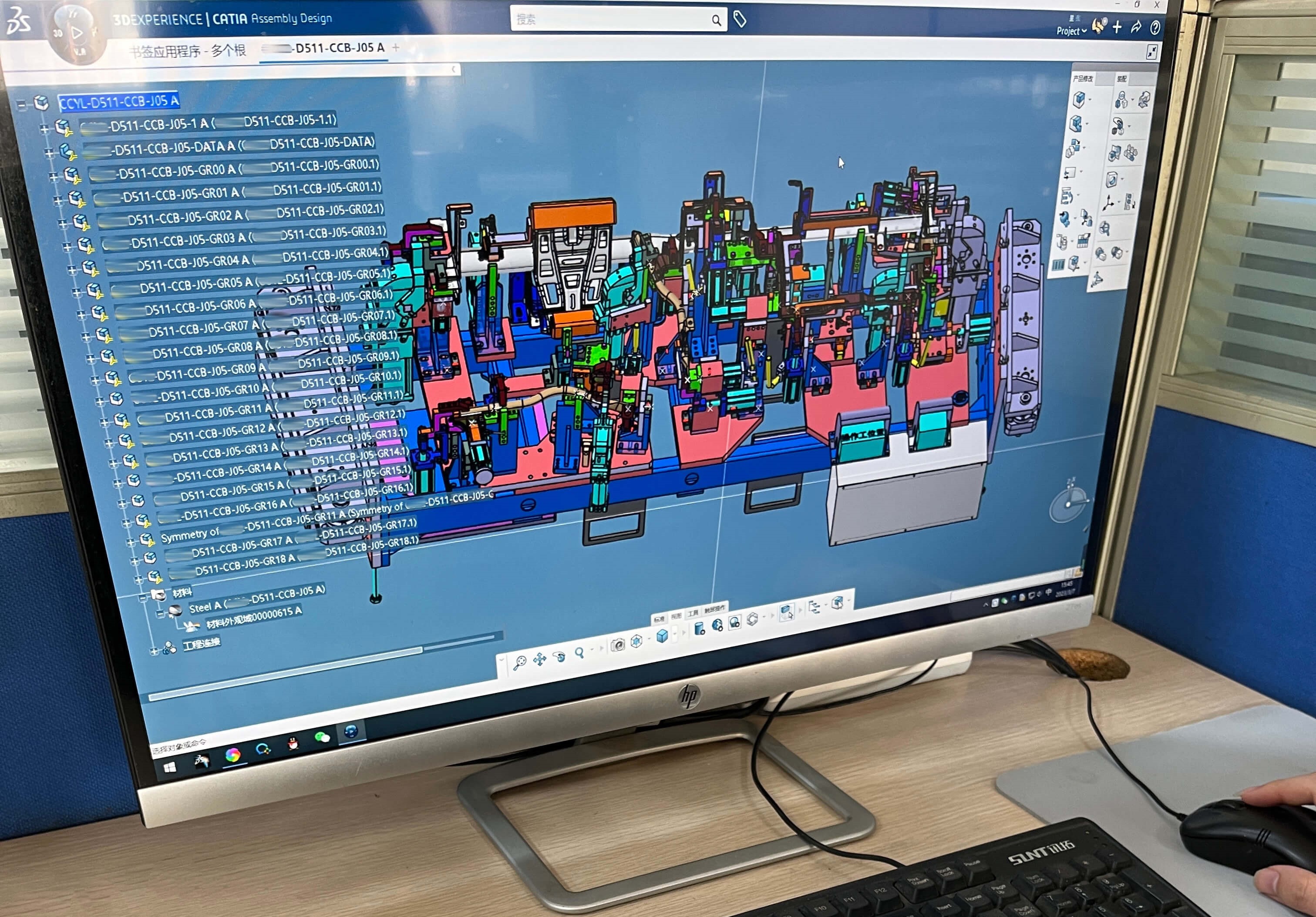
Benefits
Changshu Innovation expects to realize a wide range of benefits once it has transferred its legacy CATIA V5 data onto the 3DEXPERIENCE platform on Cloud. These include being able to design, manufacture and produce its complex machines much faster thanks to a new level of efficiency and collaboration – giving it the capability to easily keep up with orders. The platform acts as a single source of truth, where all design files are organized, managed and stored in a centralized location.
Workers’ knowledge and activities covering all disciplines can be captured and shared because of the 3DEXPERIENCE platform’s ability to store and make available a complete representation of Changshu Innovation’s products. This means that, as the company continues to expand, new recruits can quickly get up-to-speed with Changshu Innovation’s business processes. This will further help accelerate design cycles and improve speed to market.
With the knowledge transfer and collaboration benefits provided by the 3DEXPERIENCE platform, we are in a much better position to find solutions to our everyday challenges and modernize our business.
With real-time access to accurate information, the company’s engineers can collaborate on the latest version of designs, wherever they are. Using the immersive Digital Review collaboration function, they can share feedback on potential issues right at the beginning of the product development lifecycle.
The 3DEXPERIENCE platform’s cross-company collaboration features, including online widget apps such as ENOVIA’s 3D Markup, Issue Management and Issue 3D Review, will further improve collaboration, both internally and externally. Through either shared licencing or a simple invitation to edit, Changshu Innovation’s clients can access designs, offer valuable input and suggestions on product development. In addition, these online widget apps allow engineers to easily and securely share data with their colleagues when working on maintenance projects off-site, enabling more efficient troubleshooting. Issues on a virtual prototype are resolved real-time via collaborative digital reviews, without having to download CAD files locally.
Having everything they need available via the cloud means there’s no need for internal IT maintenance teams – everything is handled by Dassault Systèmes. This enables Changshu Innovation to focus on what’s most important to its business – scaling its operations and delivering a high level of service to its customers, at speed.
Discover more about the Digital Equipment Continuity industry solution experience.
She’s talented
Determined
And making waves
Upon inheriting Changshu Innovation, Hou Shi was set on making it a success by challenging the company’s legacy practices with the 3DEXPERIENCE platform on cloud.
"We're now in a much better position to find solutions to our everyday challenges and modernize our business."
- Hou Shi, CEO, Changshu Innovation
Knowledge transfer and collaboration benefits on the 3DEXPERIENCE platform enable Changshu Innovation's staff to manage growing orders and store important information such as intellectual property.
Technicians troubleshooting off-site can share data on-site with engineers.
With shared licensing and an invitation to edit, collaboration with customers is now smart and simple.
Changshu Innovation can now focus on what’s most important – scaling its operations at speed to serve the automobile industry at its best.

Focus on Changshu Innovation
Changshu Innovation supplies non-standard customized automatic welding solutions and equipment to auto parts manufacturers. The company also supplies products such as automotive instrument beam skeletons, car seats, anti-collision bars, front and rear bumpers, sunroofs, and various hinges. Additionally, Changshu Innovation also provides the R&D, design, production, assembly and sales of automatic welding workstations and production lines for the above products.