Directrices de diseño y acabado de fresado CNC
¿Está planeando su próximo proyecto de producción de piezas? Asegúrese de conocer las pautas de acabado y diseño del fresado CNC que debe tener en cuenta.
Introducción al acabado de fresado CNC y directrices de diseño
El fresado CNC es un proceso de mecanizado que elimina el material de la materia prima para realizar el diseño final previsto. El fresado CNC utiliza fresas redondas que desmenuzan el material lateralmente. En el fresado CNC de 3 ejes, la pieza se fija en su lugar mientras la herramienta gira y se mueve hacia arriba y hacia abajo mientras elimina el material. Además, el lecho de la fresadora CNC de 3 ejes se mueve de atrás hacia adelante y de lado a lado.
Como el fresado CNC es una forma de fabricación sustractiva, las marcas de la herramienta se verán en su pieza cuando salga de la máquina. La buena noticia es que se pueden emplear diferentes métodos de acabado para aumentar la suavidad, la resistencia al desgaste y a la corrosión y la estética de las piezas fresadas con CNC.
En este artículo, examinamos más de cerca varias directrices clave de diseño de fresado CNC, así como las opciones de acabado de fresado CNC más comunes que debe conocer cuando comience a planificar su próximo proyecto de producción de piezas.
Directrices de diseño de fresado CNC
Asegúrese de que las características son compatibles con las herramientas de fresado CNC más comunes
Cuando empiece a considerar el diseño de su pieza, es beneficioso saber qué herramientas se utilizan más habitualmente en el fresado CNC. Lo ideal es diseñar características y geometrías en su pieza que sean compatibles con las herramientas de fresado estándar. Esto se debe a que puede reducir el tiempo de entrega y el coste total. Al fin y al cabo, el fabricante no tendrá que gastar su dinero y su tiempo en fabricar o adquirir herramientas de fresado a medida.
Evite las esquinas internas afiladas
El fresado CNC utiliza herramientas redondas. Como resultado, las esquinas internas afiladas deben quedar fuera de los diseños de sus piezas. Además, las esquinas radiadas deben ser más grandes que la herramienta de corte. De hecho, el radio de la esquina será la mitad del diámetro de la herramienta de corte. Además, es esencial tener en cuenta que los filetes se utilizan cuando una superficie inclinada o dibujada se une a un borde afilado o una pared vertical.
Intente mantener las ranuras estrechas y profundas fuera de su diseño
Cuando diseñe su pieza, recuerde que la profundidad final de un corte de fresa no debe ser mayor que 5 veces el diámetro para el acero, 10 veces el diámetro para el aluminio y 15 veces el diámetro para los plásticos. Esto se debe a que las herramientas largas pueden vibrar y volverse inestables durante el mecanizado, lo que crea acabados superficiales con muchas marcas de herramientas. Como alternativa, pruebe a aumentar el diámetro de la herramienta de corte (lo que puede obligar a aumentar la anchura del elemento) o a reducir la profundidad del elemento o la ranura. Además, si el fabricante puede acceder al elemento desde dos direcciones, podría reducir la longitud de la herramienta. Sin embargo, esto implicará una configuración adicional, lo que aumenta el tiempo y el coste de su proyecto.
Utilice los mayores radios internos posibles
Una de las mejores formas de reducir el coste de su proyecto y acelerar el plazo de entrega es diseñar su pieza para que sea compatible con los mayores radios internos posibles. El motivo es que cuanto más grande sea la fresa, más material podrá eliminarse en una sola operación, lo que se traducirá en menos herramientas y en plazos de entrega más cortos. Como regla general, intente asegurarse de que los radios sean de al menos 0,8 mm siempre que sea posible en el diseño de la pieza. Además, diseñe los filetes en su pieza para que sean un poco más grandes que el radio de la fresa. Esto creará una trayectoria más suave para la fresa, lo que dará a su pieza un mejor acabado superficial.
Asegúrese de que el grosor de la pared es el adecuado
Asegúrese de que el grosor de su pared es superior a 0,50 mm para el material plástico y a 0,25 mm para los metales. La razón es que las paredes demasiado finas son difíciles de mecanizar porque presentan problemas a la hora de mantener las tolerancias y la rigidez. Además, si el fabricante retira demasiado material, las paredes de su pieza podrían ser demasiado finas, lo que daría lugar a deformaciones y/o tolerancias comprometidas.
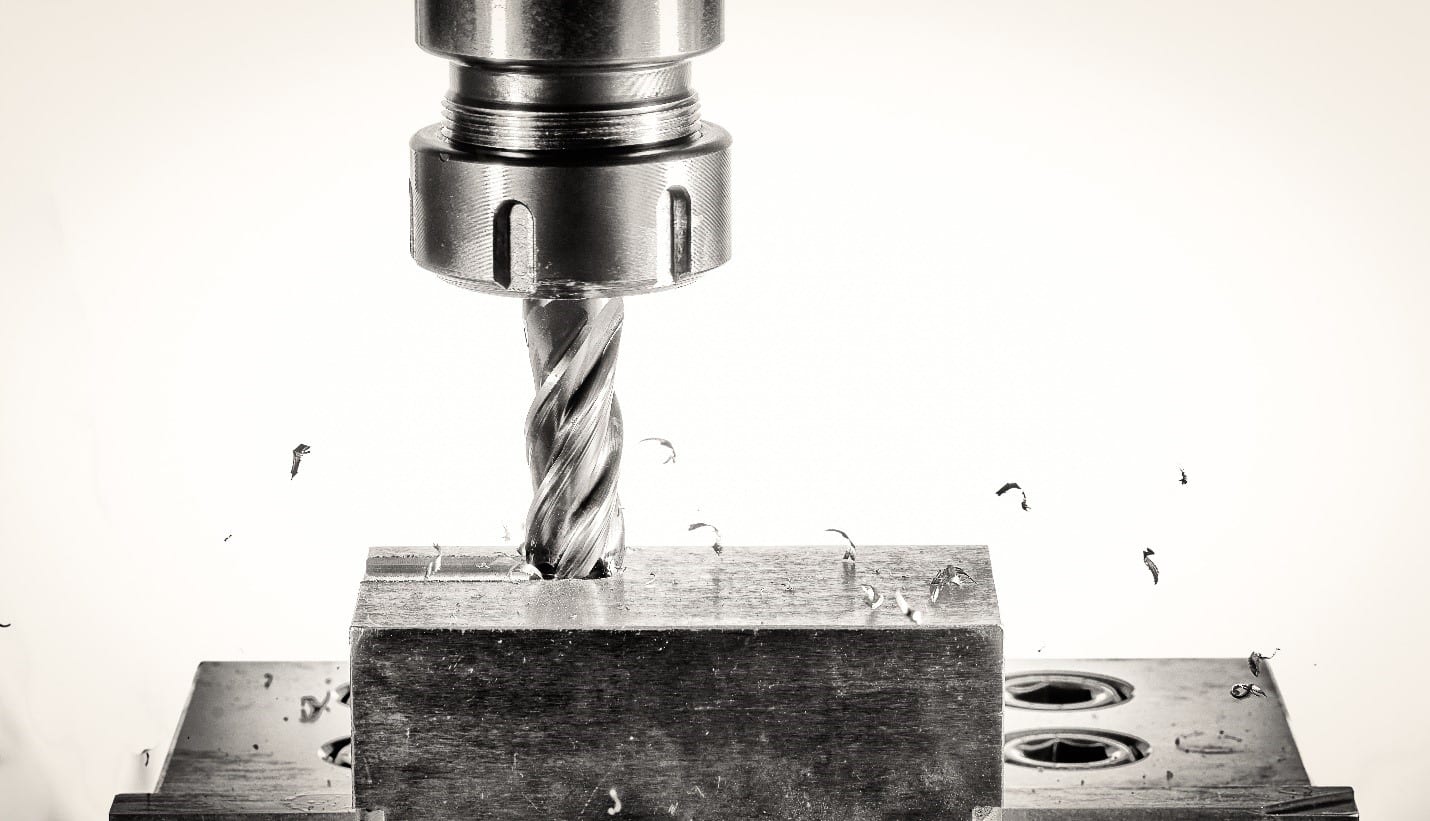
Opciones de acabado de fresado CNC
La sencillez de los acabados tal y como están mecanizados
Al utilizar el fresado CNC para muchas piezas y diseñadores de prototipos, un acabado "tal como está mecanizado" es más que suficiente para sus necesidades. Con un acabado tal y como está mecanizado, la herramienta de corte puede realizar una pasada de acabado adicional para reducir la rugosidad, o la pieza puede aceptarse tal y como está, sin una pasada de acabado y con las marcas de la herramienta a la vista. La rugosidad estándar de la superficie mecanizada suele ser de 3,2 μm. Si se realiza una pasada de corte de acabado, la rugosidad superficial puede disminuir a 1,6, 0,8 o incluso 0,4 μm. Las pasadas de acabado en el fresado CNC aumentan obviamente el coste de producción debido a los pasos adicionales que conlleva.
Además de realizar una pasada de acabado con la herramienta de corte del fresado CNC, como las piezas mecanizadas pueden pulirse y alisarse más si se desea, pero al hacerlo se eliminará algo de material superficial, lo que podría afectar a las tolerancias finales de su pieza. No obstante, como los acabados mecanizados generalmente proporcionan las tolerancias más ajustadas de cualquier proceso de acabado para el fresado CNC.
El chorreado de cuentas proporciona un acabado aún más suave
Algunos diseñadores de piezas desean un acabado superficial más refinado para sus piezas que un acabado mecanizado. El granallado es una opción para estos diseñadores porque proporciona un acabado suave, satinado o mate, y también elimina las marcas de las herramientas.
En el proceso de chorreado de cuentas, se fuerzan pequeñas perlas de vidrio contra la superficie de la pieza a alta presión de aire. El fuerte contacto resultante de las perlas elimina el material de la superficie, lo que da lugar a un acabado más suave. Es esencial tener en cuenta que si su pieza tiene características con tolerancias críticas, como agujeros, puede enmascararlas durante el chorreado para evitar que se alteren sus dimensiones.
El recubrimiento en polvo proporciona una protección adicional
El recubrimiento en polvo es otra opción de acabado para las piezas fresadas con CNC. Durante este proceso de acabado, se aplica una fina capa de polímero a la pieza para proteger su superficie. Esta capa de polímero es duradera y resistente a la corrosión, lo que ayuda a proteger la pieza del desgaste. Una de las ventajas del recubrimiento en polvo es que puede adaptarse a cualquier material metálico. Además, el granallado puede utilizarse en combinación con el recubrimiento en polvo para conseguir acabados superficiales suaves.
El método utilizado en el proceso de recubrimiento en polvo es muy parecido al de la pintura en spray, salvo que se pulveriza polvo seco en lugar de pintura líquida. Para comenzar el proceso de recubrimiento en polvo, la pieza suele imprimarse para mejorar la resistencia a la corrosión. Una vez imprimada, un pulverizador electrostático recubre la pieza con polvo seco. Por último, la pieza se cura en un horno de alta temperatura. Al igual que el anodizado de Tipo II, el recubrimiento en polvo puede ser necesario para conseguir una variedad de colores con fines estéticos.
Anodizado Tipo II y Tipo III para protección y estética
Otra opción de acabado de piezas mediante fresado CNC es el anodizado. El anodizado crea una fina capa superficial de cerámica que proporciona protección contra el desgaste y la corrosión. El recubrimiento resultante es muy duradero, no conduce la electricidad y puede adoptar la forma de muchos colores diferentes con fines estéticos. Los diseñadores e ingenieros deben saber que el anodizado sólo puede realizarse en aleaciones de aluminio y titanio.
En el proceso de anodizado, la pieza se sumerge en una solución de ácido sulfúrico y una carga eléctrica pasa entre el componente y el cátodo. La reacción electroquímica resultante convierte la superficie de la pieza en óxido de titanio o aluminio endurecido. Se puede realizar un enmascaramiento previo para cubrir las zonas de la pieza sensibles a la tolerancia o conductoras de la electricidad, de modo que la precisión dimensional no se vea comprometida y esas zonas puedan seguir conduciendo la electricidad después del anodizado.
El anodizado adopta dos formas: Tipo II o Tipo III. A continuación se ofrece un resumen de cada tipo:
- El anodizado de tipo II -comúnmente llamado anodizado "decorativo"- puede producir revestimientos con un grosor de hasta 25 μm. Esta forma de anodización produce piezas con una superficie lisa en varios colores, al tiempo que garantiza una buena resistencia a la corrosión.
- El anodizado de tipo III -comúnmente llamado anodizado de "capa dura"- puede producir revestimientos de hasta 125 μm de grosor. Esta forma de anodizado proporciona una excelente resistencia al desgaste y a la corrosión. Esta durabilidad superior hace que estos revestimientos sean excelentes para aplicaciones funcionales.
Reciba múltiples presupuestos para sus piezas en cuestión de segundos
Obtenga varios presupuestos para sus piezas en segundos