Moldeo por inyección
Descubra qué es el moldeo por inyección, cómo funciona y sus usos en la industria.
¿Cuál es la historia del moldeo por inyección?
El moldeo es el proceso de dar forma a una materia prima líquida o flexible utilizando un marco rígido llamado molde. Este proceso, muy popular hoy en día en muchas industrias, despegó en plena Segunda Guerra Mundial, cuando aumentó la necesidad de fabricar productos en masa.
El auge industrial del moldeo: La producción en masa
En 1872, el inventor estadounidense John Wesley Hyatt y su hermano Isaiah crearon la primera máquina de moldeo por inyección. Era una máquina sencilla que utilizaba un pistón para empujar el plástico a través de un cilindro caliente hacia un molde. La máquina se empleaba principalmente para la producción en masa de artículos como botones y peines.
El químico alemán Arthur Eichengrün desarrolló la prensa de moldeo por inyección en 1919. En 1939, presentó una solicitud de patente para el moldeo por inyección de acetato de celulosa plastificado, que era mucho menos inflamable que las soluciones utilizadas entonces.
Cuando estalló la Segunda Guerra Mundial, aumentó la necesidad de productos baratos y producidos en masa. Por ejemplo, la guerra en Asia y los ataques en el mar interrumpieron la producción de caucho. Los tanques y otras aplicaciones de guerra generaron una demanda masiva de metal. Los plásticos se utilizaron para llenar estos vacíos, proporcionando un sustituto asequible. James Watson Hendry creó entonces la primera herramienta de moldeo por inyección de tornillo, que se popularizó rápidamente por su precisión y control, y por tanto por su mejor calidad de producción.
Durante toda la posguerra, los plásticos siguieron siendo populares. Cuando los líderes empresariales reconocieron las enormes ventajas de coste sobre los materiales de la competencia, reevaluaron las cadenas de suministro globales. Los plásticos se afianzaron en la economía y los procesos de fabricación de mediados del siglo XX.
La invención del moldeo por inyección hasta nuestros días
En los años 70, Hendry desarrolló el primer sistema de moldeo por inyección asistido por gas. Esta técnica permitió fabricar piezas complejas que podían enfriarse rápidamente. Esto mejoró enormemente la flexibilidad y la resistencia de los objetos fabricados, al tiempo que redujo el tiempo y el coste de producción. En 1979, la producción de plástico superó a la de acero y, en 1990, el moldeo por inyección utilizó ampliamente los moldes de aluminio. Hoy en día, las máquinas de inyección de tornillo representan la gran mayoría de las máquinas de inyección. Otros métodos de moldeo ampliamente utilizados son el moldeo por soplado, el moldeo por compresión o el moldeo por vacío (termoformado).
Actualmente, el mercado del moldeo por inyección ha alcanzado los 300.000 millones de dólares. Este proceso produce más de 5 millones de toneladas de piezas de plástico al año en todo el mundo. Casi todos los sectores manufactureros lo utilizan: electrónica, automoción, electrodomésticos, etc. El moldeo por inyección de plástico sigue siendo un método asequible y eficaz para producir piezas y productos de alta calidad. Recientemente, la demanda de materiales biodegradables ha aumentado por razones medioambientales.
La tecnología utilizada hoy en día es bastante parecida a la que se utilizaba en el pasado. Sin embargo, los ordenadores han facilitado todo el proceso de diseño y fabricación. Los resultados son también más precisos, y las piezas de plástico son ahora a menudo la opción preferida para las aplicaciones tecnológicas y científicas avanzadas.
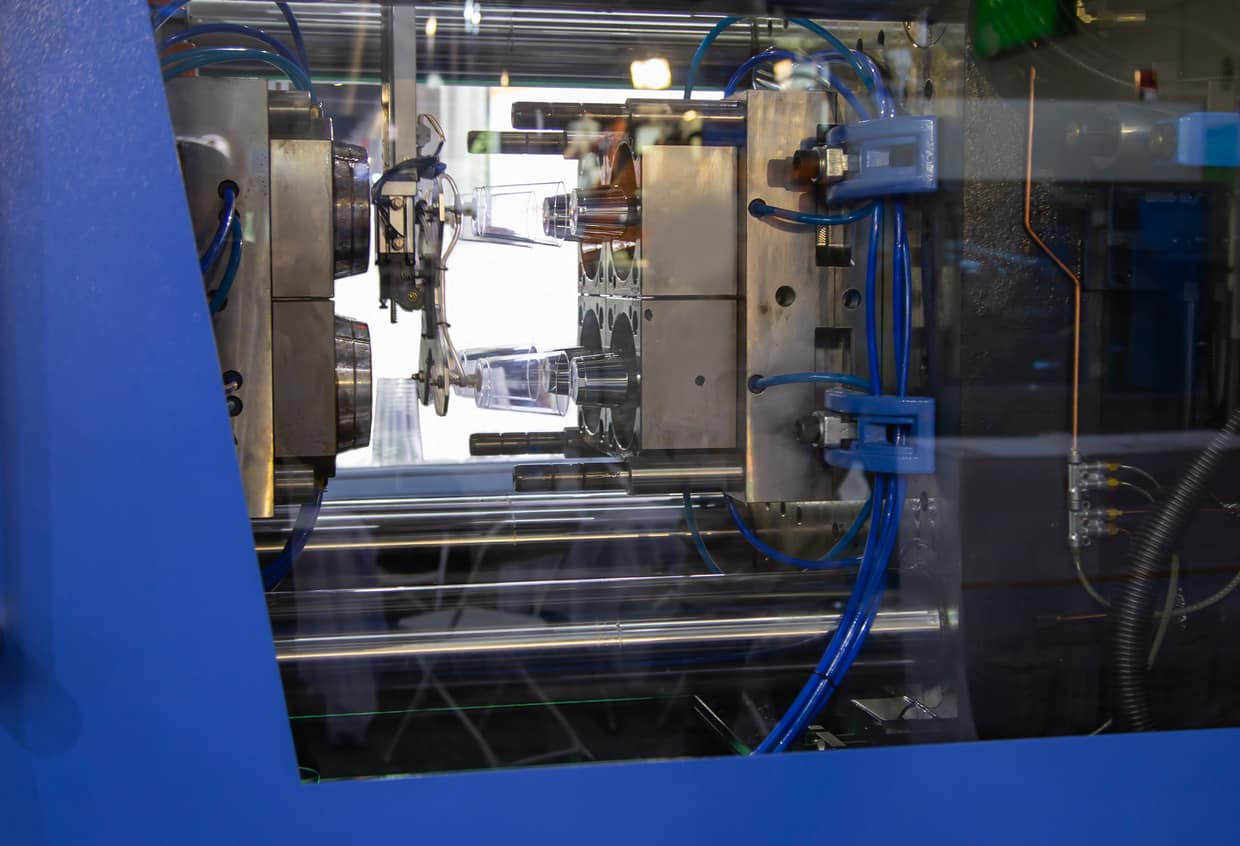
¿Qué es el moldeo por inyección?
El moldeo da forma a una materia prima, líquida o flexible, empleando un marco rígido llamado molde. Se trata de un bloque hueco relleno de materiales como plástico, vidrio, metal o materias primas cerámicas. Ésta se endurece o congela dentro del molde, adquiriendo su aspecto final. Entre los distintos procesos, los más comunes son el moldeo por inyección, por soplado, por compresión y por vacío. Mientras que el diseño de los moldes y sus prototipos puede dificultar la complejidad y la financiación, la impresión 3D se convierte en una solución relevante gracias a su rapidez de ejecución y su precisión en la realización.
Moldeo por inyección
En el moldeo por inyección, el material se funde y luego se inyecta a presión en un molde. El plástico líquido se enfría y se solidifica. La operación puede realizarse con muchos materiales (metales, vidrio, termoplásticos, etc.). Sin embargo, los más utilizados son
- El polipropileno (PP) representa alrededor del 38% de la producción mundial. Por ejemplo, se utiliza para los tapones de las botellas, ya que es apto para el contacto con productos alimentarios, y el ABS, que representa el 27% de la producción. Lego lo aprecia por su gran resistencia al impacto. Así, cada ladrillo se diseña con tolerancias de hasta 10 micrómetros,
- polietileno (PE), un 15%,
- poliestireno (PS), 8%.
Teniendo en cuenta todas las demás tecnologías de fabricación posibles, el moldeo por inyección de estos cuatro materiales representa por sí solo más del 40% de todas las piezas de plástico producidas anualmente en el mundo.
La industria del automóvil es uno de los sectores que participa en su crecimiento, ya que casi todos los componentes de plástico del interior de un coche se moldean por inyección. La industria explota especialmente
- El polipropileno (PP) para las piezas no críticas,
- El PVC por su buena resistencia a la intemperie,
- el ABS por su gran resistencia al impacto.
Al menos uno de estos materiales puede incorporarse a más de la mitad de las piezas de plástico de un vehículo, incluidos los parachoques, los paneles interiores de la carrocería y los salpicaderos.
En otro ámbito, las carcasas de la mayoría de los aparatos electrónicos de consumo se moldean por inyección. El ABS y el poliestireno (PS) son los más populares por su increíble durabilidad y buen aislamiento eléctrico.
Este proceso es cada vez más popular debido a su bajísimo coste unitario en la producción de grandes volúmenes. Por ejemplo, esta tecnología puede producir de 1.000 a 100.000 unidades por entre 1 y 5 dólares cada una. Ofrece una gran repetibilidad y una buena flexibilidad de diseño.
Moldeo por soplado
El moldeo por soplado es un proceso mediante el cual se forman y ensamblan piezas huecas de plástico, vidrio u otros materiales.
Hay tres tipos principales de moldeo por soplado: extrusión, inyección y estiramiento por inyección.
Esta técnica comienza fundiendo el plástico y dándole forma de parisonte. Este término se refiere a una pieza de plástico en forma de tubo, con un agujero en un extremo por el que puede pasar el aire comprimido.
El parisón se sujeta en un molde antes de soplar aire en él. La presión empuja el material hacia fuera para que encaje en el molde. El molde se abre una vez que el plástico se ha enfriado y endurecido. Por último, se expulsa la pieza.
Moldeo por compresión
El moldeo por compresión es una técnica en la que el material, normalmente precalentado, se coloca en una cavidad de molde abierta y calentada. El molde se cierra con un miembro de fuerza superior o tapón. Se aplica presión para forzar el contacto del material con todas las áreas del molde hasta que el material se haya endurecido.
Este proceso tiene la ventaja de moldear piezas grandes y bastante complejas. Además, este método de moldeo sigue siendo uno de los menos costosos y desperdicia relativamente poco material.
El moldeo por compresión se está desarrollando principalmente para fabricar piezas de composite, en sustitución del metal. Esta técnica se utiliza generalmente para diseñar piezas más grandes, planas o moderadamente curvadas. Se utiliza mucho en el sector del automóvil para fabricar piezas como capós, guardabarros, alerones y objetos más pequeños y complejos.
Moldeo por vacío
El moldeo por vacío es una versión simplificada del termoconformado, en la que una lámina de plástico se calienta, se estira sobre un molde de una sola superficie y se empuja contra él mediante el vacío. Este proceso transforma el plástico en objetos permanentes, como señales de tráfico y cubiertas protectoras.
Es posible formar piezas relativamente profundas si la lámina se estira mecánica o neumáticamente antes de ponerla en contacto con la superficie del molde y aplicar el vacío.
Los materiales adecuados para el moldeo por vacío son generalmente termoplásticos. La lámina de poliestireno es la más común y fácil de utilizar, con una gran resistencia al impacto. Puede moldearse con casi cualquier forma. Puede retener tanto el calor como la forma cuando se aplica agua caliente. Esto hace que sea la opción preferida para envasar productos sensibles al sabor y al olor. Esta técnica también es adecuada para materiales transparentes como el acrílico, que se utiliza mucho en la industria aeroespacial, como los toldos de las ventanas de las cabinas de pasajeros de los aviones militares de ala fija y los compartimentos de los aviones de ala rotatoria.
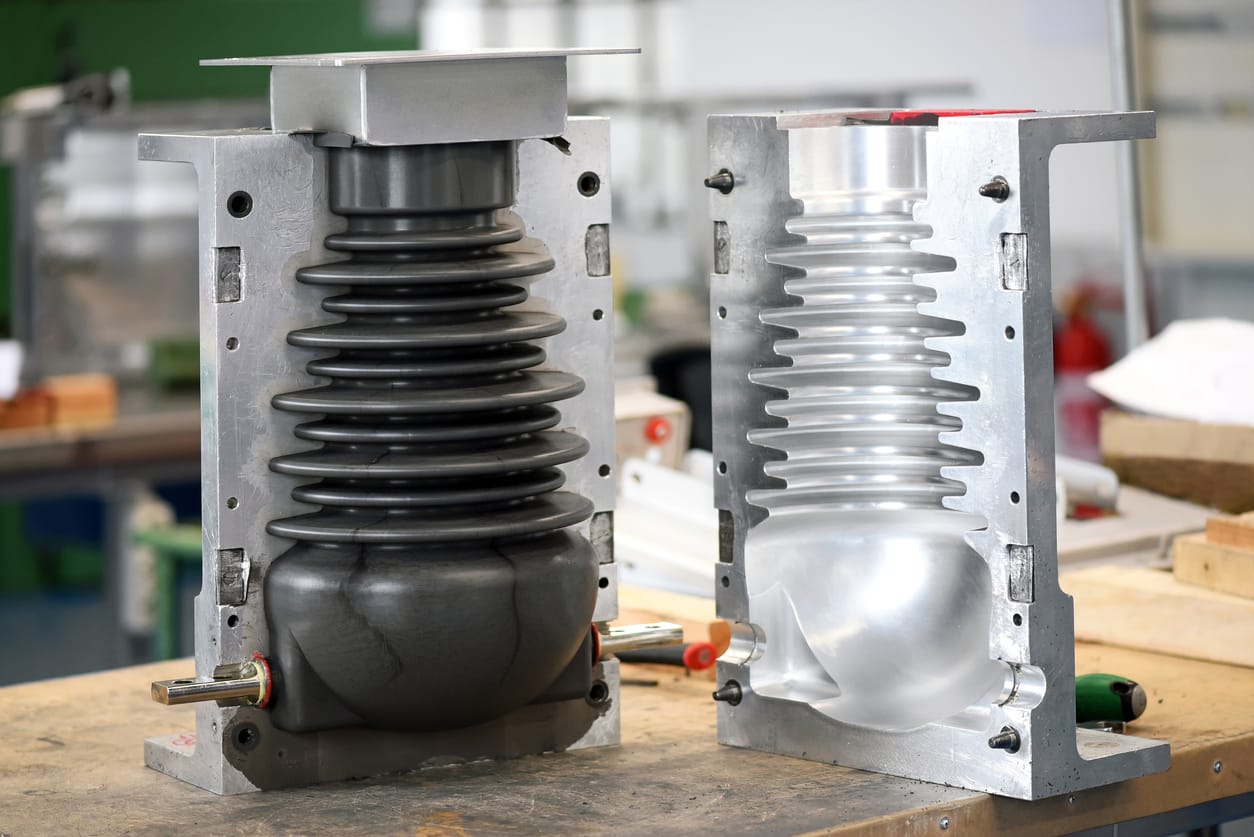
Reciba múltiples presupuestos para sus piezas en cuestión de segundos
Obtenga varios presupuestos para sus piezas en segundos