Extrusión
Descubra qué es el proceso de fabricación por extrusión y su uso en la industria.
Introducción a la extrusión
El proceso de extrusión permite crear objetos con perfiles transversales fijos empujando un material, normalmente metales, polímeros, cerámica, hormigón, arcilla para modelar y productos alimenticios, a través de una matriz de la sección transversal deseada. Esto es beneficioso para crear secciones transversales muy complejas y con materiales frágiles porque el material sólo está expuesto a tensiones de compresión y cizallamiento. Una de las principales ventajas es el excelente acabado de la superficie. Otra es la mayor resistencia de los objetos metálicos producidos con extrusión.
Existen dos tipos de extrusión: continua o semicontinua. La extrusión continua implica la producción de un material de longitud indefinida; la semicontinua implica la producción de muchas piezas. El material puede ser caliente o frío. Extruidos es el término que designa los objetos producidos con extrusión.
En 1797, el inventor inglés Joseph Bramah patentó el primer proceso de extrusión para fabricar tubos con metales blandos. El metal se precalentaba y se forzaba a través de una matriz mediante un émbolo accionado a mano. Más tarde, en 1820, Thomas Burr puso en práctica este proceso con un tubo de plomo y una prensa hidráulica llamada "squirting". Alexander Dick amplió el proceso de extrusión a las aleaciones de cobre y latón en 1894.
El proceso de extrusión también tiene algunos inconvenientes. Entre ellos están el agrietamiento superficial e interno, las líneas superficiales y el "tubo", que es un patrón de flujo que arrastra los óxidos superficiales y las impurezas hacia el centro del producto.
Cinco procesos de extrusión
Los cinco procesos de extrusión diferentes son:
- La extrusión en caliente se realiza por encima de la temperatura de recristalización de un material para evitar que se endurezca por el trabajo y para que sea más fácil empujar el material a través de la matriz.
- La extrusión en caliente se realiza por encima de la temperatura ambiente pero por debajo de la temperatura de recristalización del material. La temperatura puede oscilar entre 800 °F y 1800 °F (424 °C y 975 °C). El uso común es equilibrar las fuerzas requeridas, la ductilidad y las propiedades finales de la extrusión.
- La extrusión en frío se realiza a temperatura ambiente o casi. La falta de oxidación, la mayor resistencia debida al trabajo en frío, las tolerancias más estrechas, el mejor acabado de la superficie y las velocidades de extrusión rápidas si el material está sometido a la falta de calor son las principales ventajas de la extrusión en frío.
- El Instituto de Soldadura del Reino Unido inventó la extrusión por fricción y la patentó en 1991. Inicialmente se utilizaba para producir microestructuras y distribuciones de partículas homogéneas en materiales compuestos de matriz metálica. La extrusión por fricción difiere de la extrusión convencional en que la carga (tocho u otros precursores) gira alrededor de la matriz de extrusión. Se aplica una fuerza de extrusión para empujar la carga contra la matriz. En la práctica, tanto la matriz como la carga pueden girar o contragirar.
- La microextrusión es un proceso de extrusión por microfilmación realizado en el rango submilimétrico. Al igual que la extrusión, el metal se empuja a través de una abertura de la matriz, pero la sección transversal del producto resultante puede caber en un cuadrado de 1 mm.
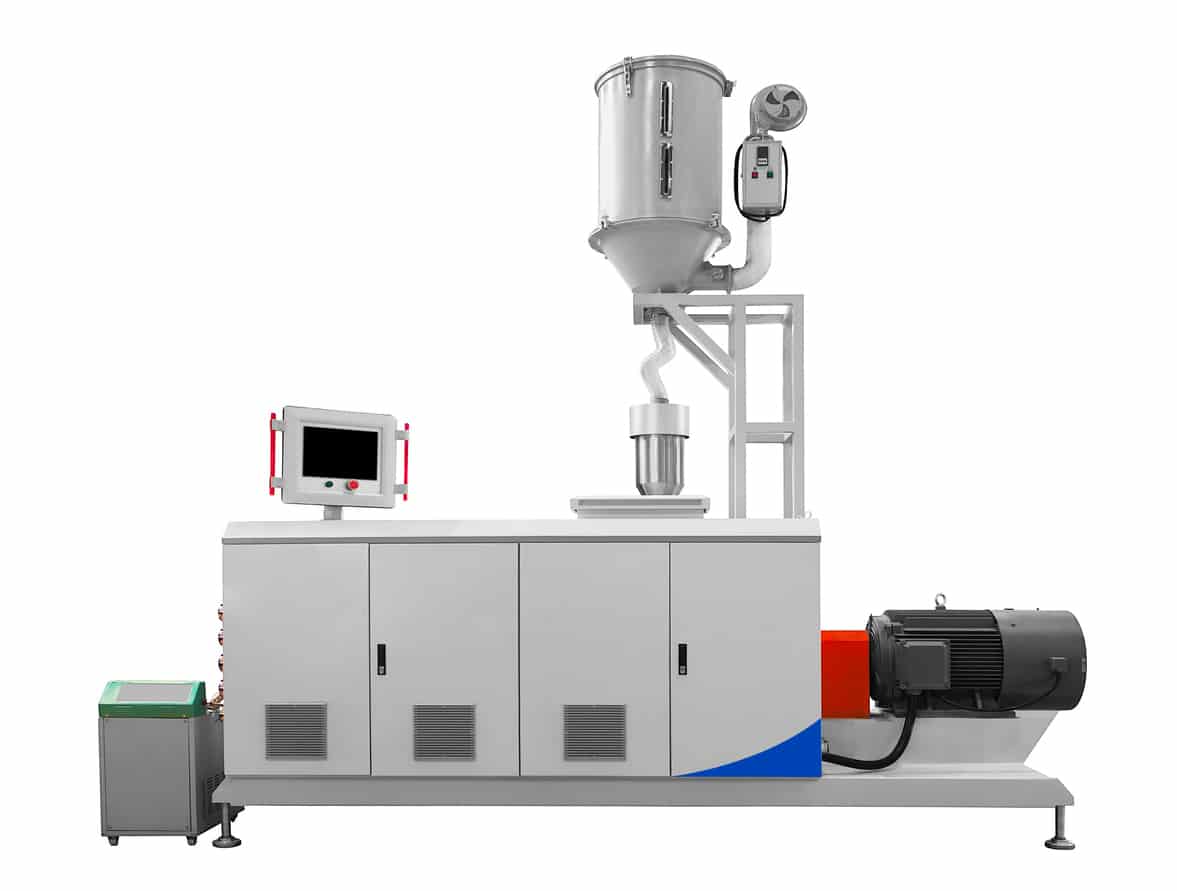
Reciba múltiples presupuestos para sus piezas en cuestión de segundos
Obtenga varios presupuestos para sus piezas en segundos