Sauder Woodworking
Sauder Woodworking Co. began in 1934 in Archbold, Ohio, in the backyard garage of Erie Sauder. The company stayed relatively small until 1951 when Sauder developed the world’s first ready-to-assemble (RTA) table. The rest is history.
We were doing about 130 SKUs (customer-specific product versions) per year before ENOVIA SmarTeam, and now we have exceeded 200. That’s an increase of more than 50 percent with the same number of resources.
Backyard business becomes furniture powerhouse
Sauder is now North America’s leading manufacturer of RTA furniture and the sixth largest furniture company in the United States. Its 3,000 employees design and manufacture 30 furniture collections that include more than 800 items sold by some of the world’s largest retailers.
With 5 million square feet of manufacturing and warehouse space, Sauder ships 37,000 items per day and had 2005 sales of $500 million. The company is still privately owned by the second and third generations of the Sauder family.
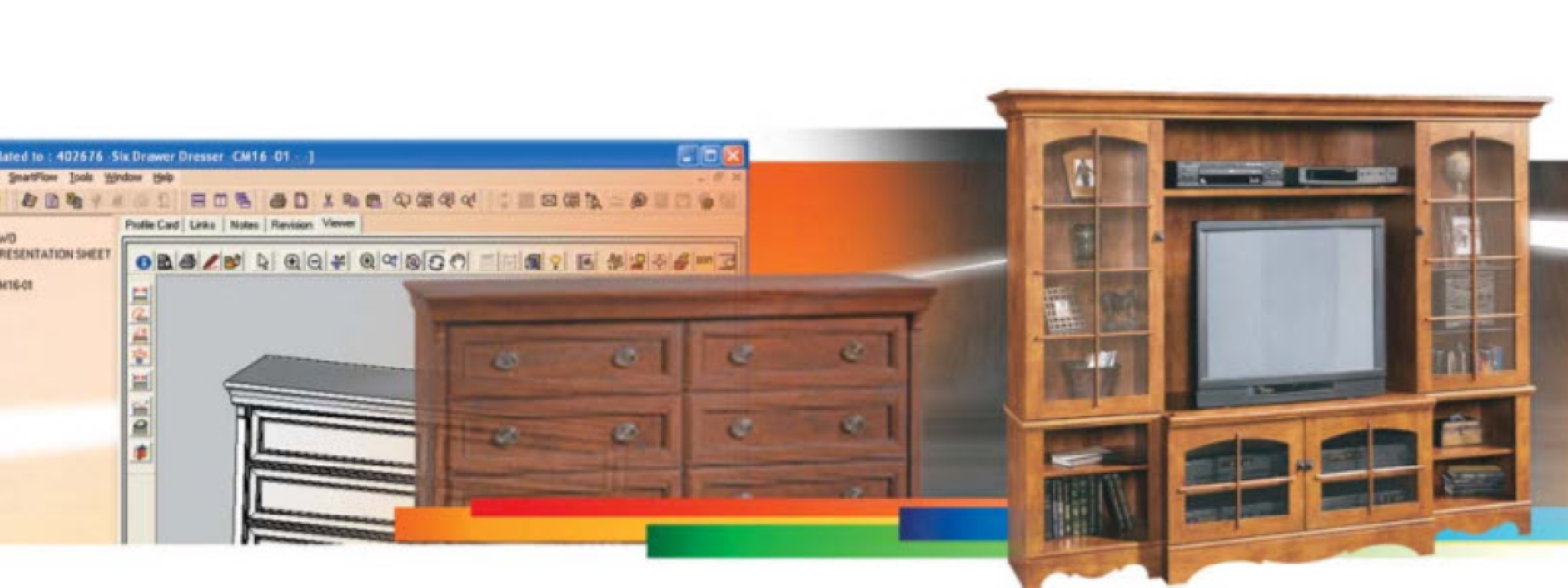
Success creates new challenges
As Sauder has grown, so has the challenge of tracking the simultaneous development of as many as 60 new products and 200 new SKUs (customer-specific product versions) per year. Each new design has its own unique collection of wood parts, screws and fasteners, so parts number in the thousands.
To manage the complexity, employees developed numerous spreadsheets. “We had more than five spreadsheets and databases,” remembers Wendell Short, Sauder’s Director of New Product Development. “Purchasing had two, the test lab had one, there were two for the schedule. Over time, we had added a team of people doing manual data entry, trying to keep those spreadsheets up to date with a lot of duplicate information.”
Despite the resources dedicated to data management, Sauder wanted to achieve a higher level of confidence in the accuracy of the information. “Drawings on the manufacturing floor sometimes didn’t match the ones in Product Engineering,” Short said. “Sometimes we would receive parts for the wrong revision of the product design. We’re not a just-intime manufacturer but we’re close, so receiving the wrong parts from a supplier leaves a costly void in our pack schedule.”
We had been averaging more than 12 weeks per design. With ENOVIA SmarTeam we’re averaging less than eight.
Doubtful data become trusted data with ENOVIA SmarTeam
To overcome these challenges, Short envisioned a single, digital 3D database shared by the company’s engineering, ERP and MRP (Manufacturing Resource Planning) systems, ensuring that data stayed up to date. Early in the company’s search, Short thought a document management system could provide the needed functionality. But when he discovered ENOVIA SmarTeam, Dassault Systèmes’ collaborative Product Lifecycle Management (PLM) solution for the SMB market, he realized it could carry Sauder far beyond what document management could do.
“Since ENOVIA SmarTeam was a Product Lifecycle Management solution, it provided functionality that went way beyond what we could get from a document management system, out of the box,” Short said. “We challenged the other suppliers to quote the same functionality, but it would have required so much custom development that it just wasn’t a contest.”
ENOVIA SmarTeam also runs on the Windows platform, the standard at Sauder, and uses Microsoft ® SQL Server.™“Any other platform would have been viewed as a negative,” Short said. “Because it’s Windows-based, it increases our ROI by holding down our cost to implement and maintain, since everyone who works here is already familiar with the Windows environment.
“It also helps that it uses Microsoft SQL Server. If it had been on some other database it might have been an issue, because we already had a lot of SQL Server databases and a lot of in-house support for SQL Server. So that was a plus for us.”
At the same time Sauder implemented ENOVIA SmarTeam, it moved from 2D to 3D CAD, made a number of changes in its processes, and added project managers to its staff. The single greatest change, however, was the creation of a single source of up-todate data.
According to Short, the results have proven ENOVIA SmarTeam’s value. Trust in the accuracy of the company’s data has been established, and improved efficiency trimmed Sauder’s design cycle by one third. “We had been averaging more than 12 weeks per design and now we’re averaging less than eight. Plus, we were doing about 130 SKUs per year before ENOVIA SmarTeam, and now we have exceeded 200 with no increase in staff. That’s an increase of more than 50 percent.”
ENOVIA SmarTeam enables Sauder to manage its growing data management needs with ease, contributing to the company’s success in the marketplace. Producing more SKUs is critical to Sauder’s success, Short said, because its retail customers don’t want to see a competitor offer the same product they sell. That demand for exclusivity continues to put upward pressure on the number of SKUs Sauder must manage, which significantly increases the company’s data management complexity and its need for ENOVIA SmarTeam.
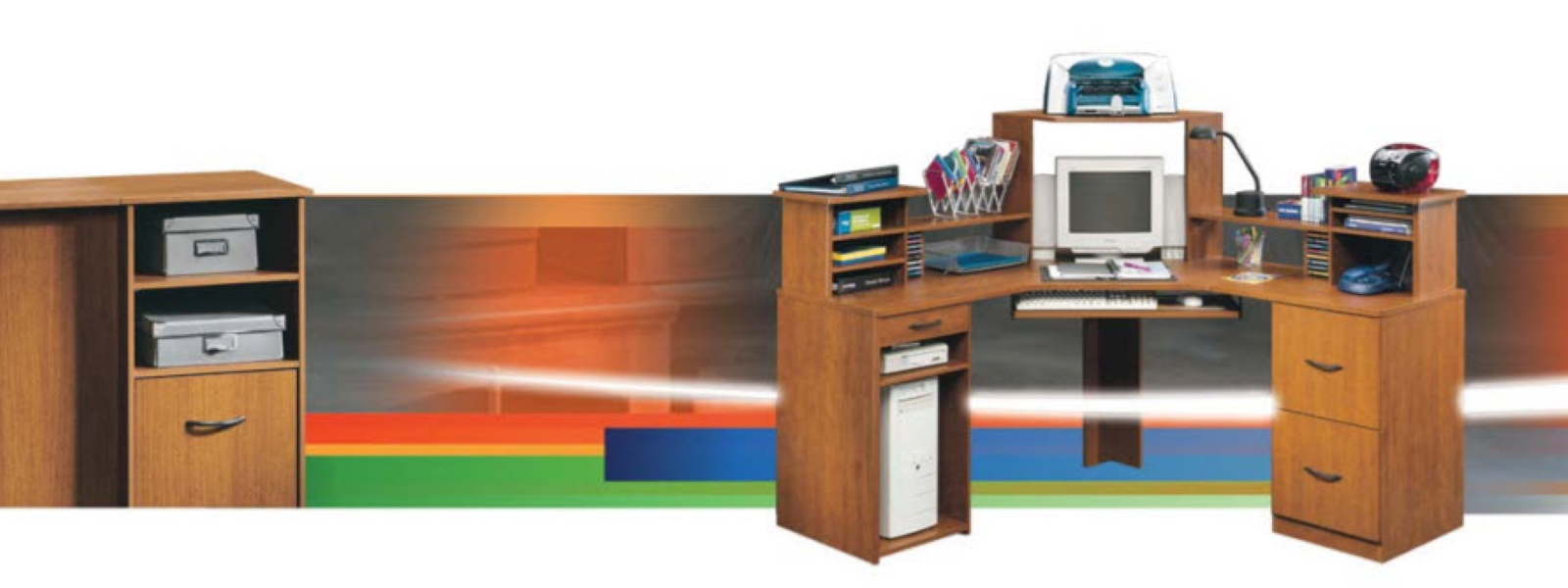
ERP, MRP integrations multiply value of ENOVIA SmarTeam
By integrating ENOVIA SmarTeam with the company’s CAD, ERP and MRP systems, Sauder has eliminated its need for manual data entry and streamlined the production of everything from purchase orders to packing lists.
“Our CAD system is used to create the design, but when it’s time to produce a bill of material (BOM), the CAD system leans on ENOVIASmarTeam to tell it the part number for the screws, all the relationships between the parts, the placements of the hardware. CAD creates the geometry, but ENOVIASmarTeam manages the BOM.”
ENOVIA SmarTeam allows Sauder to associate related documents with each project, including e-mail files, project notes and meeting minutes. “You can even save an Outlook message to a text file and then link it to the drawing,” Short said. “Whatever you need, it’s all right there in ENOVIA SmarTeam, organized by project.”
ENOVIA SmarTeam also provides input to Sauder’s ERP system. Once a product design is finished, ENOVIA SmarTeam transfers the necessary information to the ERP system to issue purchase orders and shipping documents, automatically filling in the necessary fields. The ENOVIA SmarTeam user interface proved so popular with users, in fact, that Sauder now allows many of its employees to use ENOVIA SmarTeam screens rather than ERP screens to do their work.
“It used to take six MRP screens to do what we can now do with one ENOVIA SmarTeam screen,” Short said. “We can transfer the data that already exists in ENOVIA SmarTeam with one simple command and get the same information in half the time.”
ENOVIA SmarTeam also provides the product data required by the MRP system, which embellishes that information with detail needed to manufacture the parts. “The manufacturing BOM is more detailed than the engineering BOM, down to what glue is used,” Short said. “But ENOVIA SmarTeam can supply the MRP system with everything it needs to know to build the m-BOM.”
ENOVIA SmarTeam provided functionality out of the box that went way beyond what we could get from a document management system.
From marketing to sales, everyone uses ENOVIA SmarTeam
ENOVIA SmarTeam also provides the data needed to create packing diagrams that show precisely how all of the parts can be fit into the smallest possible box. Workstations on the floor allow the packing department to print these instructions or view them onscreen.
Writers, meanwhile, use the product data in ENOVIA SmarTeam to create assembly instructions. Sales uses ENOVIA SmarTeam online reports to track the development of new products and learn when they will be available for sale, and manufacturing uses it to see what new units need to be produced and when. “The lion’s share of the company’s employees use one of those two reports,” Short said. “And providing the data they need doesn’t require any additional work from me or my team. With ENOVIA SmarTeam, we’re now out of the spreadsheet maintenance business for status tracking.”
If the need for another type of document does crop up, however, ENOVIA SmarTeam can populate Microsoft Office Word documents and Microsoft Office Excel® spreadsheets and check those documents in and out to ensure that everyone who uses them has the latest version. “That’s another benefit of the fact that ENOVIA SmarTeam is Windowsbased,” Short said. “We use the Microsoft Office system extensively, and our ability to use ENOVIA SmarTeam data in Windows applications is virtually seamless.” ENOVIA SmarTeam also can be used to populate executive summary documents required in StageGate, a system Sauder uses for tracking internal approvals.
Future holds new uses, new benefits
Short expects ENOVIA SmarTeam to continue to play an important role in Sauder’s future.
“Ultimately, I’d like to roll ENOVIA SmarTeam out to our suppliers,” he said. “Implementing the Community Workspace functionality would let us link directly to some of our vendors. We could stop e-mailing PDF files of drawings, and they could know, just as we know, that they’re working with the latest data. It would increase the timeliness of delivery and the accuracy, which is critical to our production schedules.”
The most important work has already been done. “I think we made the quantum move we needed to make already, and ENOVIA SmarTeam is a big part of that,” Short said. “It has helped our time to market and improved the efficiency of our New Product Development process. I can’t overemphasize the importance of having one centralized source of data that everyone knows they can trust.”
It has helped our time to market and improved the efficiency of our New Product Development process. I can’t overemphasize the importance of having one centralized source of data that everyone knows they can trust.