Knust-Godwin
Knust-Godwin uses Dassault Systèmes’ 3DEXPERIENCE platform, including the ENOVIA and SIMULIA applications, to help customers improve product manufacturing and maximize the benefits of additive manufacturing.
Additive manufacturing transforms speed and quality of parts production
Additive manufacturing (AM) is transforming how industry makes products by cutting costs, increasing efficiency and creating parts previously thought too complex or expensive to produce.
The AM process creates parts one layer at the time. There are a multitude of techniques including powder bed fusion, direct energy deposition and fused-filament fabrication. In essence, all techniques have one thing in common: Heat is used to turn a non-solid material into a solid object, with nearly no constraints regarding its design. AM is currently transforming from a prototyping only approach to serial quality production. To ensure the necessary quality upfront, all potential scenarios require visualization to enable informed decisions and to close the gap between as-designed and as-printed.
Katy, Texas-based Knust-Godwin, which specializes in high-quality, precision components for complex, downhole instrumentation products for MWD/LWD (Measurement/ Logging While Drilling) used in the oil and gas industry, exemplifies how AM is enhancing and improving complex part production. The company produces instruments which collect data from harsh environments deep within a drill hole that require complex, accurately manufactured parts. Its customers include the four major oil and service tool companies that serve many of the world’s leading oil and gas exploration and extraction companies.
These businesses are under pressure to make their operations more efficient, increasing demand on Knust-Godwin to manufacture parts quickly and cost effectively. To improve its manufacturing operation, Knust-Godwin must constantly evolve and invest in new technologies. Bringing 50 years of knowledge and experience in subtractive manufacturing techniques, such as milling, turning, and drilling, and combining them with AM makes Knust-Godwin one of the few precision parts manufacturers to offer the advantages of both methods.
Working with our customers on their designs and using the 3DEXPERIENCE platform, we can show them the results that they’re looking for before we ever print a product.
3DEXPERIENCE uniquely poised for design challenges
Knust-Godwin was looking for a solution that could showcase how AM could improve production. After a thorough search, the company selected the design and simulation capabilities of the 3DEXPERIENCE® platform from Dassault Systèmes.
“Our biggest challenge is to educate customers about designing for additive manufacturing,” Corliss said. “The [additive manufacturing] technology is so new that our customers don’t have the experience of how to use and apply it. And working with our customers on their designs and using the 3DEXPERIENCE platform, we can show them the results that they’re looking for before we ever print a product.”
“Dassault Systèmes brought everything together on one platform that allowed us to generate and analyze the code,” said James Hyder, additive manufacturing engineer in R&D at Knust-Godwin. “And eventually we’ll be able to analyze and compare the data that the machines capture and then improve our predictive modeling capabilities with it. No other platform today that I’m aware of offers that.”
The 3DEXPERIENCE platform was implemented by Adaptive, a Dassault Systèmes platinum Value Solutions partner, and they remain closely connected to Knust-Godwin by providing on-going training and consultation when questions arise. “Adaptive has been instrumental in getting us up-to-speed,” Hyder said. “Their support and working at our pace of adoption has been excellent. There have been challenges, but we’ve worked together, and I couldn’t have asked for a better relationship.”
Transforming production of high-quality precision parts
Knust-Godwin is transforming how it manages and produces high-quality precision parts by combining their knowledge and know-how of subtractive and additive manufacturing with the capabilities of the 3DEXPERIENCE platform.
"Knust-Godwin has the confidence, resources and knowledge to apply additive manufacturing to its core competency of subtractive manufacturing. This provides customers with the precision quality products that they are accustomed to seeing from subtractive processes,” Corliss said. “Traditionally, oil and gas product manufacture can take up to 24 months to produce from conception to commercialization. With additive manufacturing we’re able to provide this in a shorter time, like eight months, and in some cases post-machining processes have been cut from 12 steps to two steps.”
The 3DEXPERIENCE platform has been particularly effective in helping Knust-Godwin maximize its AM expertise.
“I see a lot of customers who come to us with a plain and simple design, or need multiple parts for an assembly,” said Chris Philpott, additive manufacturing engineer at Knust-Godwin. “But then we show them what we can do with 3DEXPERIENCE and additive manufacturing. Customers have been genuinely shocked how we are able to combine multiple components into a single 3D-printed part.”

Before using the 3DEXPERIENCE platform, Knust-Godwin would print the part, measure it, determine distortions and manually correct the model, which was both time-consuming and costly. Now Philpott uses the platform to simulate models that will be 3D-printed and iron-out problems beforehand, including the prediction of build failures such as cracking or thin-wall buckling.
“We had a customer who wanted a filter tube,” Philpott continued. “After printing, we found it was too distorted. We decided to run it through the reverse-shape optimization app in 3DEXPERIENCE. I was amazed watching the simulation run, how it looked exactly like the distorted part we’d just printed. Then we were able to reverse shape [the 3D model] to create a perfectly straight part.”
One of Knust-Godwin’s biggest simulation challenges is to predict distortion, and largely the problems depend on the material they use to print.
“One big reason for picking 3DEXPERIENCE over other solutions is the full thermal-mechanical simulation to measure stresses within a material,” Philpott said. “We can introduce a material we’ve never used before, enter that material’s parameters and simulate it. This allows a lot of flexibility in determining material properties and reactions in manufacturing. We have a lot of thin-walled pieces and pieces where thick and thin walls are combined which makes for a lot of complexity in the part. 3DEXPERIENCE is able to handle that well.”
Facilitating greater collaboration and knowledge sharing
Working as a small engineering team, Knust-Godwin is supported by engineering students from local universities who also need real-time access to their project data.
“The 3DEXPERIENCE platform allows the team to work closely together and streamline workflows,” Hyder said. “The technology helps facilitate knowledge movement across our team – some of whom are located off campus. Before we used email, servers and data documents; it was very cumbersome to keep current on modifications made by different team members.”
This improved collaboration is helping with other business processes, including task management and quote generation.
“The task manager feature in 3DEXPERIENCE supports the quotation process from start to finish,” Hyder said. “When the quotation comes in, we’ll put it through the system. Then each one of us will get our own roles that we’re required to fill out so that we work in unison to get the quote out to the customer faster.”
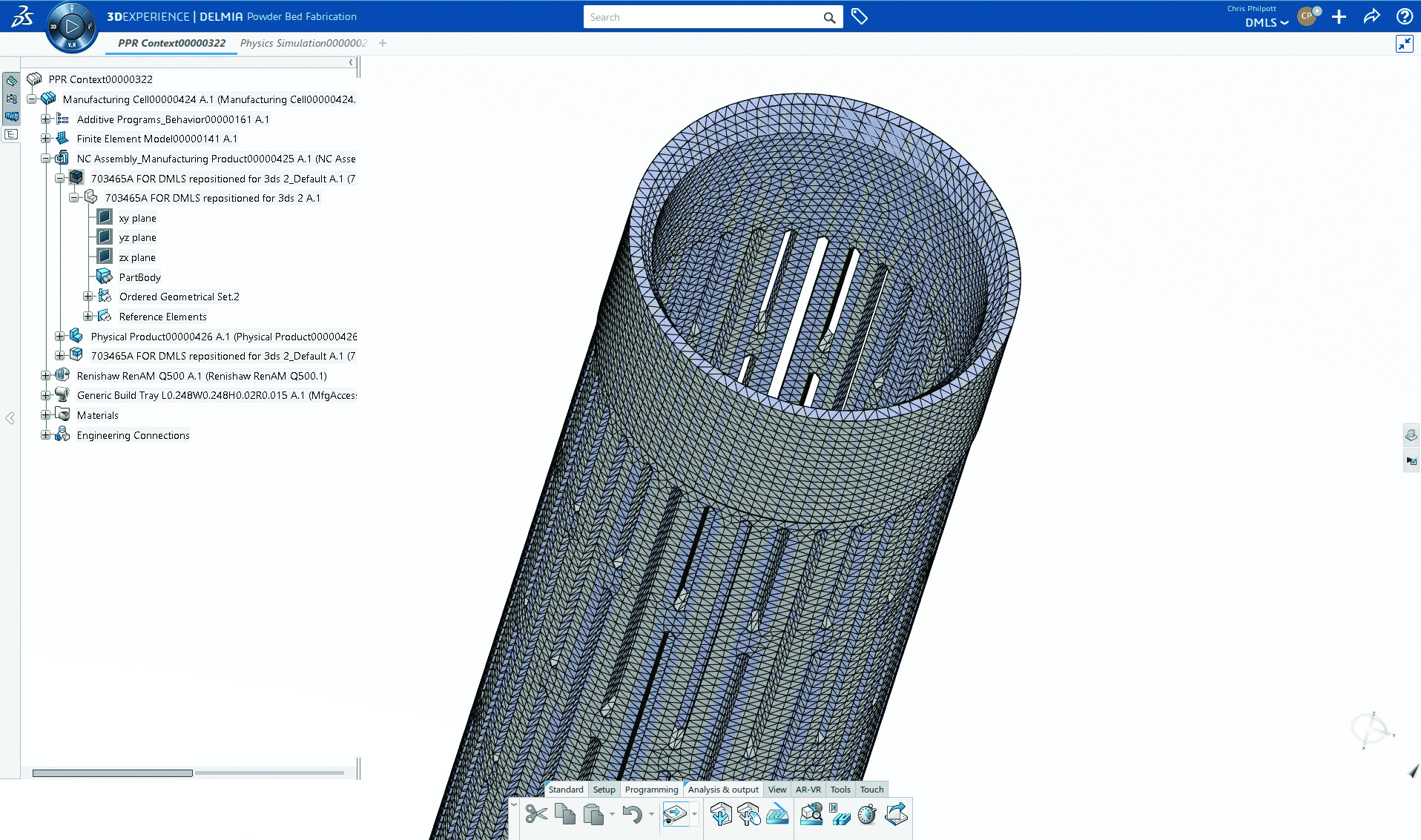
Growth for the future
AM is a key business opportunity for Knust-Godwin, and the company expects demand for its AM services to grow annually by 20% over the next few years.
“The 3DEXPERIENCE platform means we can provide unique capabilities for products that are hard to manufacture or produce with traditional additive manufacturing software,” Corliss said. “It gives us an edge in the industry. This results in providing our customers with precision quality products they have come to expect from Knust-Godwin.”
Setting the customer expectations early is helping Knust-Godwin win business and earn customer loyalty.
“A lot of people think that you can make anything because it’s 3D-printed,” Philpot said. “We often see parts that are not appropriate for additive manufacturing or with some minor changes could be. With 3DEXPERIENCE we can demonstrate how a part behaves in the additive manufacturing process and even re-engineer it so that it can be re-designed for the additive process.”
For the future, Corliss added, “Knust-Godwin’s long-term goal is to grow and develop with the 3DEXPERIENCE platform and get to where technology starts using AI, machine learning and neural networking to become revolutionary and we start to manufacture products we never thought possible before.”

Focus on Knust-Godwin
Knust-Godwin has been providing high-quality precision production machining services for over 55 years to businesses in the oil and gas, geophysical/seismic, semiconductor, aerospace and medical industries. The company provides customers with a complete manufacturing solution from concept, to engineering, to prototype, to production runs. It produces high-precision part components as well as complicated turn-key assemblies. The company has the following certifications: API Spec Q1, ISO 9001:2015 and AS9100D.
Location: Katy, Texas
For more information https://www.kgsbo.com

Focus on Adaptive Corporation
Adaptive Corporation enables innovation by applying technology to streamline business processes, reduce costs and improve efficiencies throughout the product life cycle.
Adaptive’s unique “Digital to Physical” product portfolio includes CAD, CAE, PLM, business analytics, metrology and 3D printing. Our solutions help our customers reduce costs and cycle times throughout product planning, development, manufacturing and after-market service.
Location: Hudson, OH
For more information http://www.adaptivecorp.com