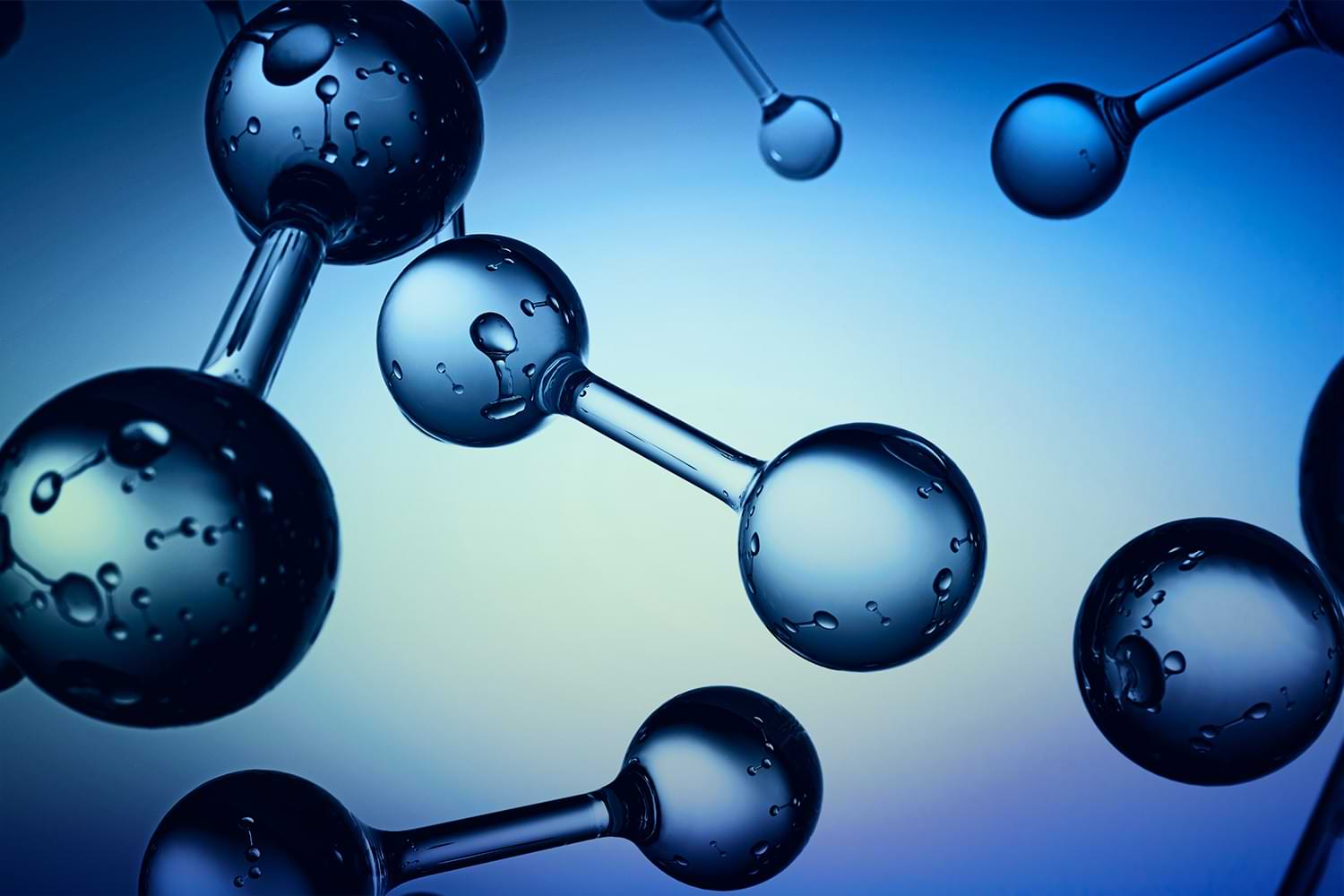
Unlocking the Potential of Hydrogen in Aviation: Certification, Supply Chain and Infrastructure
Learn about the challenges of certification, supply chain and infrastructure for hydrogen-powered systems with our two experts.
Designing Impactful Innovation podcast – episode 4
In this second episode of our series dedicated to hydrogen in aviation, Jean-Baptiste Quincy, Aerospace and Defense industry solution experience director, and Isaac Benzaquen, Aerospace and Defense airports industry solution experience director, tell us more about the challenges faced by aerospace companies and how the 3DEXPERIENCE platform can support them.
How can manufacturers certify their hydrogen-powered aircraft and systems successfully? What kind of infrastructure will airports need to develop to accommodate hydrogen-fueled aircraft? What different supply chain options exist today to supply airports with hydrogen fuel? Tune in to find out.
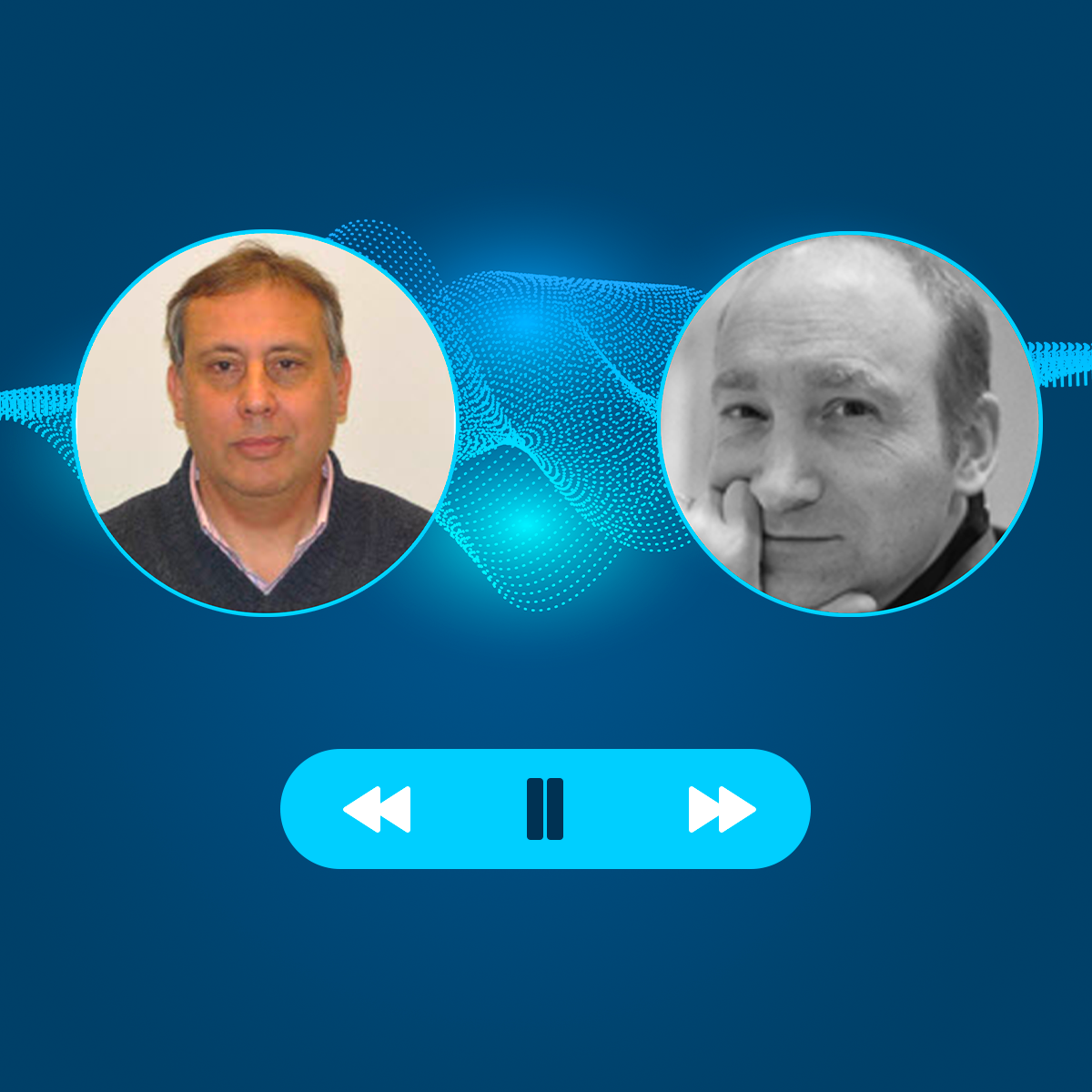
Meet our speakers
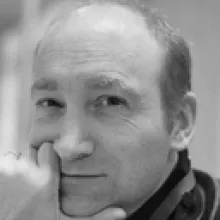
We want to shift from pure physical test campaigns for certification to a more hybrid approach. Ultimately, the larger or most expensive tests that sit on the program critical path will be replaced by simulation, supported by less costly and less time expensive tests.
A strong collaboration is required among energy suppliers, OEMs, airports and airlines to tackle these challenges successfully. Building a global ecosystem with all value chain players is likely the key to achieve a truly competitive and sustainable hydrogen fuel industry.
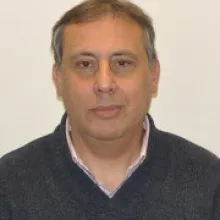
You can follow the "Designing Impactful Innovation" podcast on Apple podcasts, Spotify, Deezer, YouTube or by RSS.
Stay tuned!
Read the transcript
Clara: Hello and welcome to the Designing Impactful Innovation podcast. I’m Clara, your host and today we’re continuing our discussion about hydrogen in aviation. In our previous episode, Dr. Lisa Belkhichane told us about the different options aerospace industry players have to implement this alternative energy source. We also talked about the different challenges they faced in terms of entry into service, aircraft systems, infrastructure and certification.
We were curious to know more about the challenges surrounding hydrogen regarding certification, supply chain and infrastructure, so we sat down with two of our experts to learn more.
Jean-Baptiste: Sure. So my name is Jean-Baptiste Quincy. I’ve worked at Dassault Systèmes actually for a long time. I joined the company since ‘99. I've worked ten years developing simulation capabilities and then ten years working with our customers. And now, since three years, I'm part of the industry Aerospace and Defense portal and I'm responsible for one of our industry solution experiences, which is called “Cleared to Operate” and which is providing a lot of simulation-centric processes and capabilities related to quality, safety assessment and certification.
Clara: All right. Thank you and thank you for joining us today.
Jean-Baptiste: Sure. So where have to start… I think the first thing is to understand the detailed physics that take place during the nominal operation of the product. So whether it's the aircraft itself or the propulsion system or any of the equipment. So that's traditionally – this nominal operation – where the product should be most efficient at performing its duty. And, nevertheless, some parts of the operating conditions – of the operating domain – are, however, a bit more challenging than others. So these more challenging parts of the domain are typically near the boundary of the operating domain. For example, during takeoff and landing, the external floor on the aircraft is much more complex than during cruise or ascent.
So for airworthiness certification, one needs also to study how the product and its system will behave in degraded conditions.
So, these degraded conditions can either come from the environment – an example is icing accretion on the wings. So this will affect the external flow around the wing and it can – it will decrease the lift and if the aircraft is too susceptible to this, it can lead the aircraft to not be able to fly anymore.
So, in other cases where these degraded conditions can be triggered when a failure mode is occurring: so if this failure mode is not extremely unlikely, then you have to demonstrate how your product will continue to operate safely, at least long enough until you can bring everybody in a safe place.
Jean-Baptiste: So to predict the behavior of the product being designed, we can simulate the different physical phenomena involved, such as external flows, stress, fatigue, thermal effects, electromagnetic effects, and so on.
And actually, Dassault Systèmes proposes a comprehensive set of high fidelity simulation technologies that can be used from aircraft level down to material level even and whose robustness and diversity really enables to cover the whole envelope of operations. So the brands from Dassault Systèmes that deliver these physics-based simulation capabilities are SIMULIA, CATIA and BIOVIA.
And these capabilities are provided either natively on the 3DEXPERIENCE platform: for example, you have structural simulation with Abaqus simulation technology, which is natively integrated, available as an app – as a set of apps – or, it can be provided via external applications which are then connected to the 3DEXPERIENCE platform by means of a “Power’By” integration.
So this out-of-the-box integration that Dassault Systèmes provides greatly accelerates building and updating the simulation model, which is where the most time is spent. So from the design and also to complete the loop sharing back the simulation results, back to all the stakeholders. So, to provide – to enable – a streamlined and more continuous design simulation loop. So that's what we call ModSim at Dassault Systèmes. And this way, our customers can develop their product much faster and make sure their product will behave safely in all possible circumstances encountered during the mission.
Jean-Baptiste: At a higher level, at governance level, in order to drive the technological risk down to an acceptable level throughout the development program, a test incremental strategy is defined early on. And this test strategy will be composed of a set of test campaigns covering product requirements in a comprehensive manner – of course, focusing on the new technologies that have not been embarked already in similar products. And physical test campaigns require a large amount of time and money and often sit on the program critical path. So, it's really important to take care of these aspects because they have an impact at program level.
Along with the test plans that are part of this incremental test strategy, the associated test means – that will implement, enable us to execute this test – are also specified early on and they will have to be developed as well. So for example, companies have to test specific architectures or maybe they have already have that in their test center, or maybe they have to procure some test center facility. But all the equipment, it's in the end not so far from manufacturing, when you design the manufacturing system.
Jean-Baptiste: Before talking about acceleration – let's look first at how to avoid being late. So as we said, certification will traditionally require a significant amount of physical testing. This physical testing has to be produced and as such, it's not trivial to have the test means ready on time to start the campaign. Having all stakeholders synchronize on the same test plan with the test means requirements associated to it and continuously updating this plan is the right path to be on time. Because if you use disconnected tools, people are not aware of the changes, then when the D-day comes and they were not aware of the changes… you cannot perform the test, you lose some days, sometimes more.
For example, in the context of large-scale testing such as Iron Bird, the suppliers which participate to the program development are meant to deliver their equipment and subsystems – and often there are late stage changes, especially on the software control area. If the delivery of some equipment is late, there could be some ways to adapt or fix the plan in a way not to impact the end of the overall test campaign. For example, you could imagine switching with another test or perhaps adapting the test, like using a lower fidelity representation of that equipment until it's available. Then you change the plan, and that has impact on other people and so it's important that everybody is synchronized on the same test plan.
So after making sure that the test is performed on time, of course the test needs to be successful in the sense that the products must pass the test.
So there is de-risking of that physical test that can be done by leveraging virtual testing upstream of the test. So if you leverage high fidelity simulation and you take care of the quality of the engineering simulation process – are you performing the simulation on the right input? Are you using the right methodology? – then you bring the risk level of the products failing the test to a very low level. So, no bad surprises.
And finally, it's worth saying that the test is only relevant provided the requirements that it checks or it verifies, are relevant. So if some requirements have evolved, it's important of course, to update the test plan.
Jean-Baptiste: Definitely. So traditionally, experiments and simulation, have been, you know, two different worlds in terms of people, in terms of processes, of tools. And these worlds often oppose each other. Nobody believes the simulation results except the analyst; everybody believes the physical test results, except the experimentalist. So there is, you know, traditionally this kind of opposition.
And the change of way of working is to synergize both worlds: simulation, helping to design and de-risk the test, and the physical test, ensuring simulation is trustworthy.
So in order to achieve this common framework, a unified framework and a common set of tools need to be put in place to streamline this collaboration between the physical test, simulation and the customer – the design office. So that's where a platform such as the 3DEXPERIENCE will really provide the end-to-end solution and enable this virtual plus real testing synergy.
Another change is that we want to shift from pure physical test campaigns for certification to a more hybrid approach. Ultimately, the larger or most expensive tests that sit on the program critical path will be replaced by simulation, supported by less costly and less time expensive tests. In some areas it will take a long time, but that's the direction that we are heading towards.
So this can only be achieved, of course, if the simulation is trustworthy: so if a proper simulation credibility assurance framework is put in place. So data quality, data traceability test article conformity, uncertainty quantification, are key aspects for which executing this end-to-end process on the 3DEXPERIENCE platform makes a significant difference.
Clara: You talked about the fact that traditionally, virtual simulation and physical testing were quite separate and that moving forward we will see a shift towards hybrid approaches that take advantage of the best of both these approaches.
Jean-Baptiste: There are several benefits of performing this approach. So, saving money by removing these large-scale tests, or at least performing fewer physical tests, but also reducing the lead time. So triggering the simulation much earlier than the physical test also enables to optimize the design against this performance criteria when it's still time to make changes on the design.
Often, these large physical tests, if you have an issue, you can only put some “band-aid” on your design, you cannot change drastically any – it's too costly to make drastic changes. Left-shifting the test is definitely the benefit to take into account this performance criteria much earlier and securing the performance of the product.
Another aspect is that a platform which provides end-to-end traceability of the tests and means to retrieve the test data based on several criteria will enable in some cases to reuse previous testing and avoiding going through another test. This is true capitalization of engineering IP. And what we see today is that people, sometimes they have performed the test, but they don't trust exactly what have been the conditions of this test. They don't have sufficient information or sometimes they're not sure that this information is the right one. So they say, okay, they decide to relaunch the test. So here it's really to capitalize and to capitalize with trust and with full clarity on what has been done, because everything has been captured from end to end in the platform.
Finally, a virtual test enables to test many more configurations automatically and provide access to many more physical quantities that physical tests will ever produce and thus having a much better understanding of the product behavior, diminishing the unknown, which mechanically will enable to reduce margin. And when you reduce margin, you deliver a more efficient product to the market.
Jean-Baptiste: I would say it must evolve for the aviation industry to become carbon neutral by 2050. To reach that impressive objective, many new vehicles embarking disruptive technologies and novel architectures will have to be put on the market and therefore certified.
So this is going to put a lot of stress on the certification system, which could become a bottleneck if it's not being prepared. One of the enablers we are studying in Europe with some partners is to put in place a digital- and model-based certification framework at the level of the ecosystem. This will be the only way to make the certification process more agile, and reduce the overall lead time.
Clara: Well, this was really interesting Jean-Baptiste, thank you so much for your insights.
Jean-Baptiste: Thank you, Clara.
Clara: Jean-Baptiste talked to us about the certification process for hydrogen-powered aircraft, as well as the tools and approaches that can help accelerate it. So, let's say our hydrogen-powered aircraft is certified and ready to fly. What next? It will have to refuel at an airport, but hydrogen fuel has its own challenges and that requires specific airport infrastructure. We asked Isaac Benzaquen, our Aerospace & Defense Airports industry solution experience director, to tell us more about hydrogen infrastructure and its challenges.
Isaac: Yes, my name is Isaac Benzaquen. I'm part of the Aerospace and Defense industry solution in charge of airports and hydrogen.
Clara: All right. In our previous episode, we quickly talked about the impact that the transition to hydrogen systems will have on airport infrastructures.
Isaac: Yes, a shift to hydrogen will require airports to reinvent their existing infrastructure and logistic systems. As presented in episode one, aircraft will need to operate on liquid hydrogen if we want to increase the flight range. This hydrogen will have to be stored in airport tanks at -253 degrees Celsius to keep hydrogen in its safe-to-use liquid form, which generates a new level of safety management and logistical complexity.
This hydrogen is highly explosive at ambient temperature. As such, storage tanks must stay outside of the airfield to reduce the chance of chain reaction explosions. Following this, a significant increase in overall storage space must be expected. Meanwhile, the type of infrastructure that airports will require to accommodate liquid hydrogen will depend on how the airport chooses to source the fuel.
Therefore, a strong collaboration is required among energy suppliers, OEMs, airports and airlines to tackle these challenges successfully. Building a global ecosystem with all value chain players is likely the key to achieve a truly competitive and sustainable hydrogen fuel industry.
Isaac: So three possible scenarios: the first one is the lowest impact scenario. It will involve transporting liquid hydrogen to the airport by trucks. This scenario will require little extra infrastructure beside on-site storage tanks. Transporting the hydrogen by truck will lead to hundreds of vehicles a day needed to deliver the hydrogen, which just is not feasible, as hydrogen requires four times more volume than conventional jet fuel to supply the same quantities. Which means four times the truck traffic on top of already congested internal roadways of an airport.
Clara: So maybe not the best long-term scenario then. What about the other alternatives?
Isaac: Yes. The second scenario would involve building a pipeline to transform gaseous hydrogen, to airports, that will then be liquefied on site. This scenario will require the development of a gas pipeline and an on-site liquefaction plant. The liquefaction plant will require a reasonably large section of the airport’s real estate. It is a complex process since you are taking something that is in room temperature and you have to take it all the way down to -253 degrees Celsius, it will require quite a lot of energy to do that.
While this would mean a serious investment for an airport, for larger airports requiring very large volumes of liquid hydrogen, it would make sense. In fact, on-site liquefaction or electrolyzing of hydrogen will probably be the only effective method for a large airport.
The third scenario is about producing hydrogen at the airport. It could provide a new stream of revenue for the airport. This option must consider a large space availability as a key requirement using electrolyzers to produce the hydrogen.
These scenarios can be used by airports to provide a route to scaling up hydrogen availability over time. For example, a large airport may start by implementing scenario one for fueling aircraft, while the required infrastructure for the implementation of scenario two or three is being built.
Isaac: Yes, the 3DEXPERIENCE platform provides an end-to-end solution for airports to better strategize and plan their transition. It helps airports to modelize their as-is and analyze different to-be scenarios to help estimate the effort and cost of their transition, such as: define and optimize best airport configuration while ensuring safety and regulation, define hydrogen storage while taking in account the current demand needs, define new airport operation models while optimizing aircraft planning and respecting standards and regulations, provide a collaborative platform while improving collaboration and decision-making, define and optimize hydrogen supply chain while enabling full visibility of your upstream supply chain. And finally, continuous monitoring hydrogen business environment.
Clara: Well, that was really interesting, thank you, Isaac.
Isaac: Thank you and welcome.
Clara: Thank you for listening to Designing Impactful Innovation. To find out more, go to 3ds.com/cloud. Don't forget to subscribe for more insights and stories from our guest experts!
Learn more
Ready to learn more?
See how the 3DEXPERIENCE platform on the cloud can transform your business. Fill out the form to get in touch with our experts.