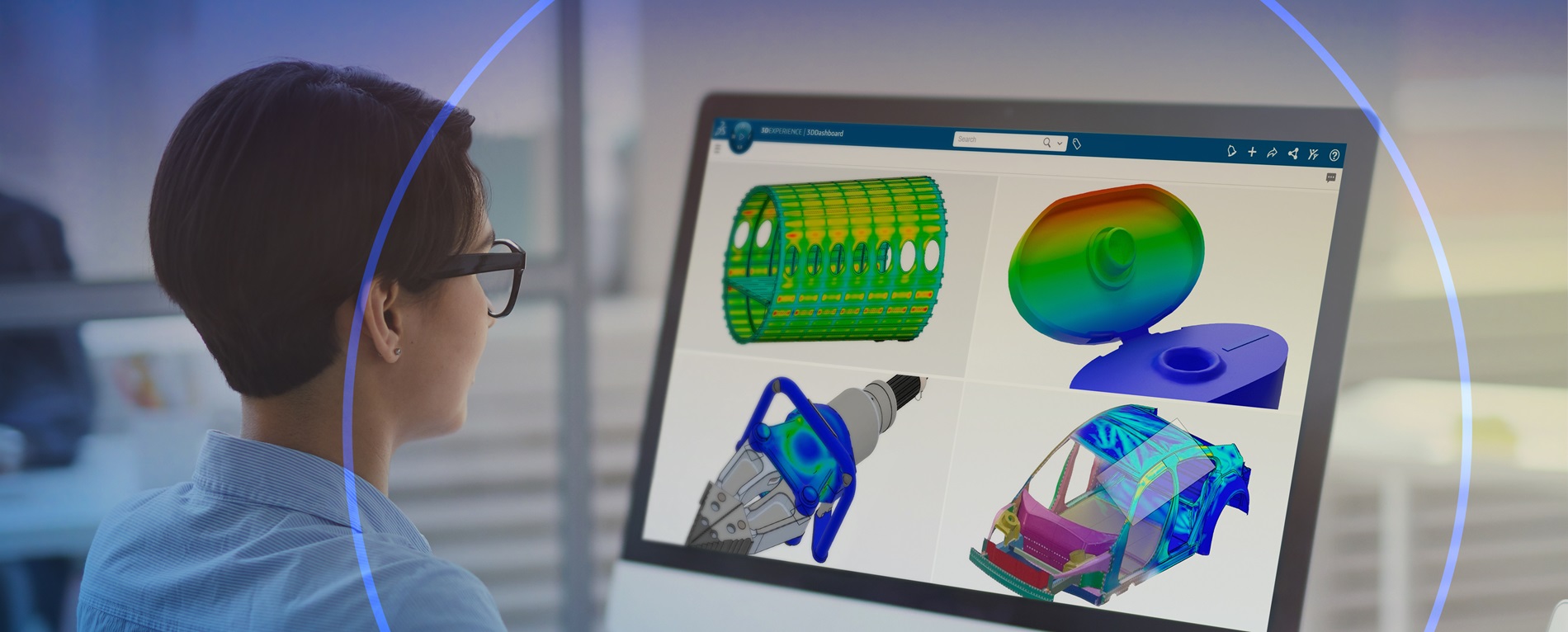
Maximizing Product Development Efficiency with MODSIM
Learn about the benefits of unified modeling and simulation for product development with two Dassault Systèmes experts.
Designing Impactful Innovation podcast - episode 24
In this episode, we delve into what unified modeling and simulation (MODSIM) is and how it empowers engineers and designers to improve their product development processes. Discover how companies, from startups to large enterprises, can use the power of MODSIM to innovate faster and develop more sustainable and higher-quality products.
Tune in with Daniel Pyzak, industry process consultant director at CATIA and Dhiraj Nahar, industry process expert director at SIMULIA.

Meet our speakers
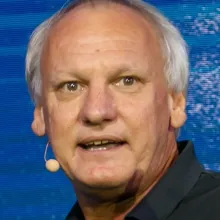
The idea of MODSIM is very simple: it’s a technology that unifies modeling and simulation. But it’s not just putting them together. It unifies modeling and simulation on a common data model, in a database. It will automatically, by nature, break some silos and really trigger true collaboration.
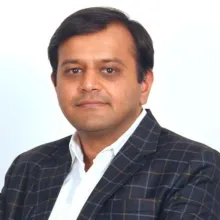
MODSIM provides complete associativity between the CAD and the CAE – or in other words, the simulation data – so that you can perform any multiphysics simulation on the same model. Because of this CAD and CAE associativity, these design iterations can be performed very quickly. Sometimes, even automatically.
You can follow the "Designing Impactful Innovation" podcast on Apple podcasts, Spotify, Deezer, YouTube or by RSS.
Stay tuned!
Read the transcript
Clara: Hello and welcome to Designing Impactful Innovation. I'm your host, Clara, and today we're talking about how MODSIM, or unified modeling and simulation, is helping companies optimize their product development processes and develop better products.
Joining me today are two Dassault Systèmes experts, Dhiraj Nahar, SIMULIA industry process expert director, and Daniel Pyzak, CATIA industry process consultant director. Let's dive in!
Dhiraj: Thank you, Clara. It is a real pleasure to join this podcast today. As you mentioned, I'm Dhiraj Nahar. I've been part of Dassault Systèmes for more than 20 years, and I have worked on modeling and simulation in my entire career so far.
I have a master's in mechanical engineering from Arizona State University. Since my engineering, I've been intrigued about product development. And the work I do at Dassault Systèmes has only helped me deepen my passion to work with our customers on challenging product development problems.
Together with our teams, we create new methods on modeling and multiphysics simulations to solve such problems. We effectively use all aspects of multiphysics simulation, such as structures, fluids, electromagnetics, and multibody dynamics so that one can gain deeper insights into the design problems, and thus we help create better products.
Clara: Daniel, on to you.
Daniel: My name is Daniel Pyzak. I am the French guy in the talk. I am located in the southeast of France. I started CAD, CAM, CAE a couple of years ago, in 1983. And it's always a pleasure to do CAD, CAM, CAE, PLM and especially now that we introduced, a couple of years ago, MODSIM, you will understand why later on.
My know-how is – I graduated in mechanical engineering. Like Dhiraj, but not in Arizona, in France, my know-how is about CAD for engineering design, but also tooling – tooling is important – with a focus on design for manufacturing, as parts are never designed like “that”. You take into account as quickly as possible the constraints coming from the manufacturing processes you select to actually produce the part.
It can be plastic injection, molding, stamping, casting, and, why not, now 3D printing. I was also involved in machining, rapid prototyping. And now I am part of – since 1999 when Dassault Systèmes took over my previous company – I am now in a team called the worldwide CATIA industry process expert team.
And I help my customers to make the best use of our 3DEXPERIENCE solution and of course help them to adopt MODSIM, but we will talk about MODSIM just after.
Clara: All right, thank you. Historically, modeling and simulation were separate processes handled by different teams within a company. Engineers used computer-aided design (CAD) systems to develop models, and analysts used computer-aided engineering, or CAE, software for simulation. Now, unified modeling and simulation, or MODSIM, brings them together.
Daniel: Yes, of course. First of all, history is still lasting. Historical traditions have a long life and to be honest, a lot of companies today – maybe 99% percent of them – are still in the traditional process that I will describe now.
You start by designing the product. You define its architecture, you do some concept studies, then you finally do the detailed product definition in the engineering office and you send this data, this detailed design part – the first version of the detailed version design – you send it to the stress analyst department, which is maybe somewhere else, not even close to where you are.
And the stress analyst takes your design, cleans the design, simplifies the design, prepares the finite element model, prepares the connection – because the part is never all alone, it's surrounded by some other parts within an assembly.
So, prepare, run the simulation set up, get the result of the simulation, evaluate it, maybe make some loops. And after everything is okay, give feedback to the designer. This takes weeks – still today – multiple weeks.
The idea of MODSIM is very simple. MODSIM – it's a technology. And it unifies modeling and simulation. That's important. But it’s not just putting them together.
It unifies modeling and simulation on a common data model, in a database. We no longer use files. So, in a database, with the same UI, the same user interface, and this is called the 3DEXPERIENCE platform.
It will automatically, by nature, break some silos and really trigger true collaboration.
Dhiraj: Sure Daniel. As Daniel mentioned, MODSIM is unified modeling and simulation on the 3DEXPERIENCE platform. It provides complete associativity between the CAD and the CAE – or in other words, the simulation data – so that you can perform any multiphysics simulation on that same model.
These multiphysics simulations could be related to structures, fluids, electromagnetics and multibody dynamics on the same model. So for example, if we take a car model: on that same model, you can perform an NVH simulation, you can perform a durability simulation, or you can perform any kind of component subassembly level crash simulation.
Now, we all know that no design can be done just in one shot. Every design goes through a couple of design iterations. Because of this CAD and CAE associativity, these design iterations can be performed very quickly. Sometimes, even automatically, with little to zero manual intervention.
Similarly, one can perform parametric design studies for design sensitivity studies. For example: you are designing ribs on a particular bottle and you want to get the exact dimensions of the ribs, the spacing of the ribs. Using parametric design studies, you can arrive at the right set of design parameters.
The MODSIM environment also enables design of experiments between multiple simulations. And this helps to really perform design trade-off studies and get your design absolutely right.
Once these methods are set up, the methods engineer, using concepts such as engineering templates on the 3DEXPERIENCE platform can democratize them across the entire company for other designers to use them.
For example, let's imagine that you're performing a complex brake squeal simulation. Now, once the methodology is all created, the methods engineer can publish that engineering template for the brake squeal. And the next time you're making any design changes or a different design for the brake, you can use the same engineering template and just execute the simulation. And this can be done by the design engineer.
So, one can basically end up creating complete virtual or digital twins of their product and drive a lot of virtual testing on that digital twin.
All this technology enables designers and engineers to design more sustainable products, lightweight them and create them faster. Since the 3DEXPERIENCE platform natively enables collaboration, the product development teams around the world can also collaborate on these projects, which can help them bring better products to the market.
Clara: There are a lot of benefits, speed in design iteration, widespread adoption throughout the company, better quality for the products, better sustainability as well.
Daniel: Of course, what Dhiraj stated is extremely important. Products become more and more complex – multiphysics, and you need to really take into account all those physics all together at the same time.
Otherwise, you will design a product, which will not have the high quality that you were targeting and your product will not be cool or innovative, and it will not be a success.
Besides this aspect, where MODSIM brings a lot of value, there is an important other aspect, which is sustainability. Especially startups. They want to have, you know, cool products. And a cool product is not only something which is nice, which is giving the maximum of service to the end user… a nice shape; but also, a sustainable, green product.
And thanks to MODSIM, one way of creating a green product is to reduce its weight as much as possible. So lightweighting is important, and lightweighting is part of the innovation. And thanks to our MODSIM approach, where we can combine both the modeling with CATIA, and simulation with SIMULIA; all together, and optimize the weight of any part, you will get a lighter part.
We call that generative design; it's based on topology optimization. We get a lighter part, which is better appealing and which will be more innovative.
An important topic is that innovation is not only to produce, for example for startups, new products, you can also improve the innovation. You can improve existing products just by adding new capabilities.
And this is the beauty of the platform, to have this multi-CAD approach. You can reuse CATIA V5 existing models. You can reuse SOLIDWORKS existing models. You can even reuse an existing non-Dassault Systèmes CAD modeling tool inside the platform, inside our MODSIM approach – optimize both a parametric model or a non-parametric model, lightweight it and get the best of your ideas into existing products.
Innovation is also based on reusing what is good from the past, but also improving, for example, its weight. So that's quite important.
And finally, what is also important is that MODSIM brings you the ability – or brings a company, especially as a startup – to deliver their product on time, as quickly as possible.
Because we are left-shifting this validation process, which, as Dhiraj explained, took some time in the past, as I was explaining earlier. So, these weeks of validation loops are no longer needed.
So you can quickly, not only try to design the optimal product right the first time – thanks to our parametric design study, generative design, topology optimization tools, and so on – but you can also validate it very quickly.
Time is important. Innovation is important. That's what MODSIM gives to our customers.
Clara: All right. So, bringing all these capabilities on the same platform with everyone involved on the project is really helping innovators to go faster, but also reuse pre-existing knowledge to innovate, as you said, and make even better products, right?
Dhiraj: Well, that's a very good question, Clara. And thanks for asking that. Yes, the 3DEXPERIENCE platform is fully available on the cloud. And the MODSIM environment on the cloud provides you full access – or the full suite – to the CAD and simulation portfolio on the platform. This means that now, the design and simulation technology is fully accessible to any innovator in the world. Isn't that cool?
Secondly, on the cloud, you get a single unified interface. You can share your information in real time. We spoke about collaboration earlier. It provides secure access to your data, CAD, and simulation models. And above all, it enables scalability, as there are no constraints on fixed infrastructure for running large-scale simulations.
Now, in the past, people might have had issues if they had big simulations. Because of non-availability of infrastructure, they may not have been able to execute such simulations. But this problem goes away with cloud, right? With the 3DEXPERIENCE platform on the cloud, both hardware and software come pre-configured and optimized as part of software as a service.
It provides you immediate access to the hardware you need, and which will, of course, help you to ensure rapid turnaround times for your simulations. And of course, the traditional burdens that have been there to set up and manage in-house computing environments, start installing software, all that is becoming obsolete.
This, of course, will mean that modeling and simulation technology is now democratized for all, and it can be put in good use for your product development through the latest technology, algorithms, and capabilities.
The world is changing fast. We are designing newer products which require new materials, and which might require new physics for those being able to simulate those new materials.
So, any such new material models that we are introducing in the 3DEXPERIENCE platform or new physics techniques required for such simulations will be instantaneously accessible to the users and they can avail all its benefits in their development work. I think this is, by itself, very compelling.
But now, while I end my note on this, let me also tell you one more secret. Once you have all your modeling and simulation data on the 3DEXPERIENCE platform, this, by nature, is going to enable machine learning. That’s amazing because we are now seeing machine learning entering our lives, or the design process quite a bit.
And the 3DEXPERIENCE on the cloud and all these capabilities are really going to help you create better products faster. And provide access to all this technology to everyone.
Clara: All right. So, I'm hearing a lot about accessibility. Just a single interface where everyone can share their information, and democratization across the company – instantaneous access, making things go faster, right?
Daniel: It's a very important question and the answer is definitely yes.
As Dhiraj mentioned: Let's start with the installation. It's very easy from the cloud to run it on any device, even on your smartphone, from everywhere because we are on the cloud. The software is automatically updated every 2 months so you are sure that you are always using the best capabilities of the software.
The training is very short, because it's a very modern UI with contextual pop-up menus, which are proposed depending on what type of entity you select on the screen. You have the same UI for all the applications of the 3DEXPERIENCE platform. Modeling, simulation, not talking about data analytics or manufacturing, but in our case, modeling and simulation, you have the same UI.
And all of this naturally triggers a very strong collaboration. You are sure that the stress analyst is working on the last version of the model, which has been released by the engineering office.
The stress analyst and the design engineer can chat because it's the same UI. “Hey guy, can you reduce the thickness of this strip? Can you hide it? Can you show it? Can you save it? Can you open it?” It's the same UI. Everybody's speaking the same language.
As Dhiraj mentioned, it's AI-ready. And to finish – and it's probably the most important, at least for me – let's talk about people. Remember: We have the design engineering office on one side, the stress analyst on the other, and now MODSIM brings them all together with the same UI, on the same platform, with the same model on the database.
That has first helped designers, and we have a true story of companies who implemented MODSIM with Dassault Systèmes’ 3DEXPERIENCE platform on the cloud solution, who moved and enriched their skills to get more and more know-how about FEA, finite element analysis.
And now these guys can do jobs that in the past were done by the stress analyst, which means that the stress analysts can focus on the very complex use cases that you have to deal with, so make more innovative products.
That's one thing. A good example is topology optimization: lightweighting. The tools that we deliver in CATIA and SIMULIA are very nicely done. Mechanical designers can easily define the simulation set up, the boundary conditions, the loads. They can quickly reconstruct the CAD model.
And finally, let's say, the final job of validation might be done by only the stress analyst, and sometimes even themselves. I also have examples, in France, of people doing that. The designers are also able to validate their model with a simulation.
You don’t only have designers who are making more and more analyses. On the opposite side, in Italy, I have a customer whose stress analyst guy is now doing a little bit more design, and also helps the designers to make a better design the very first time.
All those people are increasing their skills, which is very good. And, of course, having more time – the famous left-shifting – to innovate, look at other variants, look at parametric design studies and converge toward the optimal solution.
You know, in the past, it was not easy to make one, or two, or three, or four variants. Now you can do hundreds of variants thanks to the parametric design study capability of the platform. And you will converge with the optimal solution very quickly.
On the other side, you can also do very complex structures. Let's talk about body structures, car body structures at the concept level. We have this concept structure engineering capability on the platform where you can design and investigate the architecture of your car body structure.
And once this is done, you can quickly modify it. At the same time, you can get the finite element model, the mesh of this structure, almost instantaneously, but also the connection and run multiple simulations.
Yes. It's easy to implement. I have companies where we have only one guy on the cloud. So he's a MODSIM guy by himself, he's collaborating with himself – which is easy. But we also have a lot of companies with multiple people, and all of them, small, medium, large companies can implement MODSIM at their pace, facing their challenges and giving the maximum to their customers to develop a better product, and innovative products.
Dhiraj: Clara, I want to tell you something, Daniel and I have really cool jobs at Dassault Systèmes. We get to help our customers with the 3DEXPERIENCE platform and this MODSIM approach to create everything, from cars to bottles, from toothbrushes and electric shavers to airplanes.
So let me give you one really amazing example of how MODSIM can help bottle lightweighting. Any CPG company, or consumer products goods company, is making a new bottle and this bottle is for, let's say a shampoo product. When the shampoo product hits the market and it really catches up, they end up creating maybe a billion bottles of the same product around the world.
So, when these bottles are initially made, they might be 43 grams and 47 grams, and if you can reduce five grams out of that one bottle, imagine how much plastic savings you are going to have out of the billion bottles that are going to get manufactured of the same product, right? We can do all this bottle lightweighting on the platform.
When you are manufacturing a bottle, it undergoes various kinds of complex manufacturing processes like extrusion blow molding, then it has to be subjected to various loads that – a consumer, when they get a product at home, it has to be looking shining, you know, that product has to have all these objectives where the bottle has to sustain all these load cases and it has to be consuming as little plastic as possible.
MODSIM really enables that. And once you develop this methodology, it can be published throughout the company and they can use it over and over again for newer bottles and newer products that they are making, which can result in tons and tons of plastic savings. And this is a huge sustainability target that these companies are able to achieve.
And that's why I said we, Daniel and I, have very cool jobs at the office because we truly every day are living our company's vision and mission of harmonizing product, nature and life.
Clara: Well, that’s a lot to think about! And I thought that was really interesting; the example of the bottle lightweighting and the fact that you said we can do this from bottles to cars to airplanes. I can't even imagine the amount of material savings we're making with this.
Dhiraj: From my point of view, it is imperative for startups and entrepreneurs to embrace modeling and simulation in their product development process. As we’ve discussed throughout this session today, it will help them create better products.
Startups, when they are introducing new products, their products have to really shine compared to the competition out there, or maybe existing products out there.
Time is of essence for startup companies, they want to introduce their products faster to market. Now, if you can get to market faster, you're going to succeed, right? So that's where MODSIM will really help.
And of course, it will help them create cost-effective products, right? Products that are really amazing and offered at the right price, which are more durable and, very likeable, very desirable for consumers.
With the 3DEXPERIENCE platform on the cloud, along with MODSIM, one can be extremely innovative. There is just, we have removed all barriers to innovation. You have the software available at your fingertips anywhere in the world.
You can also, get very innovative and start thinking of new business models wherein this technology can actually be brought to the point of sale and help drive consumer decision-making.
So, summarizing, I would say that entrepreneurs should really embrace digital product development and virtual twins as they look to create cutting-edge products.
Daniel: I fully agree with what you said. And my conclusion sentence will be very short. Don't wait. You should adopt this solution as quickly as possible if you want to be innovative and successful and beat your competition. Don't wait. And I wish you a lot of success. Thank you.
Clara: Thanks Daniel and Dhiraj! This was really enlightening. We talked a lot about better quality, better sustainability, cost-effectiveness of products and even new business models. This was really fascinating. Thank you again for taking the time to join us today and sharing your insights with us!
Daniel: It was my pleasure.
Dhiraj: My pleasure as well. Thank you, Daniel. Thank you, Clara.
Clara: Thank you for listening to Designing Impactful Innovation. To find out more, go to 3ds. com/cloud. Don't forget to subscribe for more insights and stories from our guest experts.
The 3DEXPERIENCE Modeling & Simulation Summit
2025 MODSIM Summit
Hear how real-world customers are making the future a reality with MODSIM.
Discover more
Ready to learn more?
See how the 3DEXPERIENCE platform on the cloud can transform your business. Fill out the form to get in touch with our experts.