Design for Manufacturability and Assembly: Strategies for Product Optimization
Engineers and designers aim to design products, parts, and components that are cheap and easy to produce without sacrificing quality. The concept of Design for Manufacturing is critical to optimizing the manufacturing and assembly process.
What is DFM, Design For Manufacturing?
If you are researching product development or looking into mechanical design or mechanical engineering, then you may have come across the term Design for Manufacturing or DFM for short. In essence, Design for Manufacturing is the concept of simplifying and streamlining product manufacturing and assembly processes from design to production.
Design for Manufacturing starts at the very early stages of product development before any tooling or assembling begins. The exact steps in the Design for Manufacturing process will depend on the nature of the product, part, or component that is being produced. However, there are general core principles that are always adhered to such as lowering costs, reducing the number of parts required, and optimizing the manufacturability of a product.
All stakeholders are involved in the Design for Manufacturing process. Designers, engineers, manufacturers, material suppliers, and others all collaborate to create a design that is cost-effective, elegant, and practical.
Discover all Dassault Systèmes store solutions for DMF
Dassault Systèmes specializes in providing designers and engineers with innovative and effective product design manufacturing solutions. Powerful software such as CATIA Mechanical Designer and CATIA Sheet Metal Designer can be used to create complex designs for single parts or large assemblies easily and quickly.
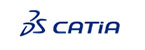
CATIA Mechanical Designer
Design on your terms with expert applications that cover the end-to-end mechanical design process
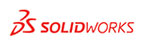
3DEXPERIENCE SOLIDWORKS
From mechanical 2D or 3D design to manufacturing, accelerate your processes at an affordable price.
The principles of design for manufacturing
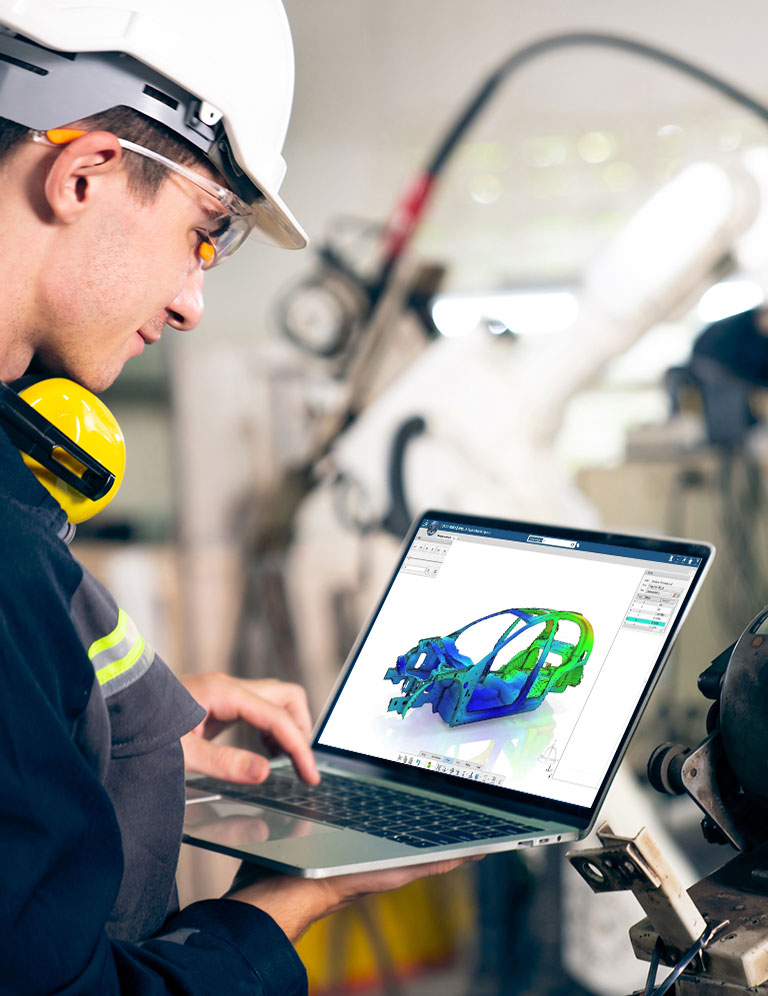
Most design experts agree that the main principles involved in Design for Manufacturing are:
- Designing for cost-effectiveness: All stages need to be optimized to reduce waste and cut costs. Simplifying the design will save time, reduce resource usage, and lower the overall cost of manufacturing the product.
- Designing with manufacturability in mind: Parts and components need to be designed in such a way that the manufacturing process is simple and fast.
- Designing for assembly and disassembly: Parts and components should be able to be assembled and disassembled as quickly as possible.
- Designing for standardization: Parts and components should be of a uniform size to streamline manufacturing.
- Designing for automation: Where possible, the design should take into account automated processes in the assembly line layout.
- Designing for sustainability: Parts should use materials and manufacturing processes that are environmentally friendly. Waste reduction and recyclability are key goals.
The design for manufacturing process
The Design for Manufacturing process differs depending on what type of product, part or component is being manufactured. However, there is a general structure that needs to be adhered to.
- The initial design concept, reviews, and analysis
- Prototype development and testing
- Final design and production planning
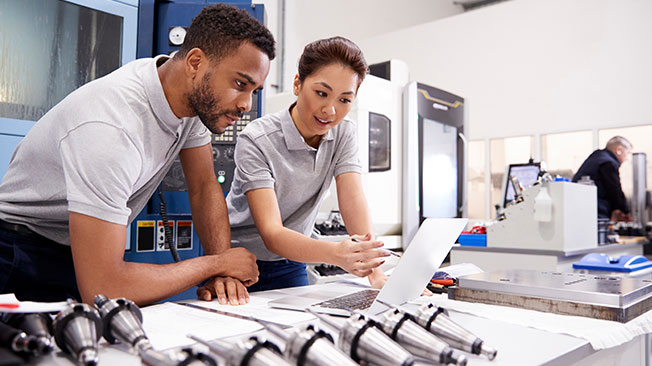
The initial design concept, reviews, and analysis
The first stage is to develop an initial design concept and finalize any requirements. There must then be an intensive design review process and feedback from all stakeholders should be gathered and addressed. The product layout design should undergo a rigorous manufacturability analysis. These stages aim to identify and solve any potential issues as early as possible.

Prototype development and testing
The focus should then be on allowing for as few iterations as possible during the product prototype development and testing phase. CAD 3D rendered modeling can help to eliminate the need to produce physical prototypes. An optimized design for additive manufacturing can also be used to produce 3D-printed prototypes, which can further reduce waste and production costs.
The key DFM concepts during this stage are design validation and optimization. All flaws must be identified and rectified to ensure that the product or part performs exactly as expected.
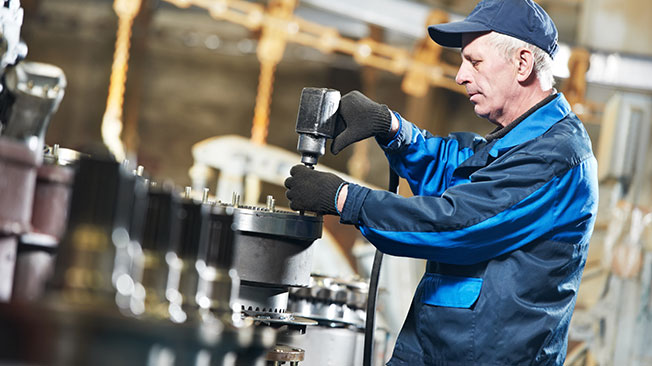
Final design and production planning
The final design and production planning stage must be based on the optimized Design for Manufacturing and assembly. Parts should be standardized for ease of production and the manufacturing layout should be scrutinized to ensure efficiency. Once a satisfactory production layout has been developed, then manufacturing can begin.
Tools and techniques for design for manufacturing
During the Design for Manufacturing process, professionals make use of a variety of different tools and techniques.
CAD and CAM software
Designers and engineers use sophisticated CAD or CAM software to develop and optimize their designs. By constructing 3D rendered models of proposed designs, engineers can effectively manage the entire product cycle in CAD. CAD modeling also assists with rapid prototyping and 3D printing processes.
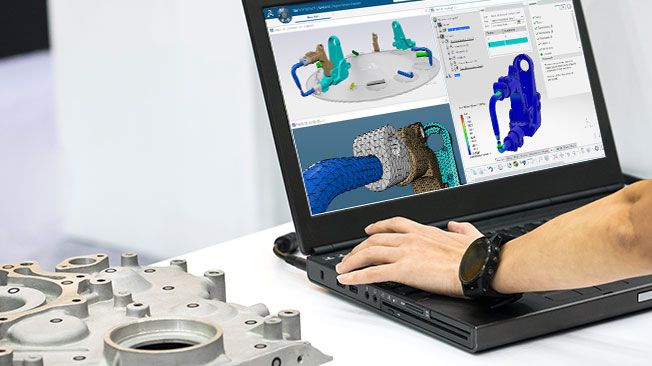
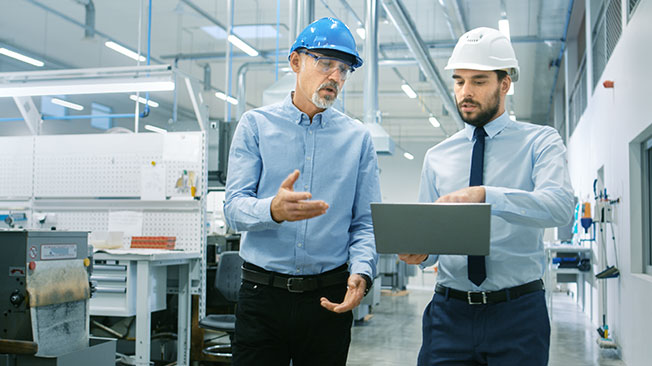
Design for Six Sigma (DFSS)
Many designers and engineers also employ techniques such as Design for Six Sigma (DFSS), which is a form of Lean design management that aims to streamline processes to eliminate waste at every stage.
Failure Mode and Effects Analysis (FMEA)
Failure Mode and Effects Analysis (FMEA) is a part of the Six Sigma methodology. FMEA is used to analyze all steps in the engineering product design process to identify areas that may fail and then assess what the impact of these failures may be.
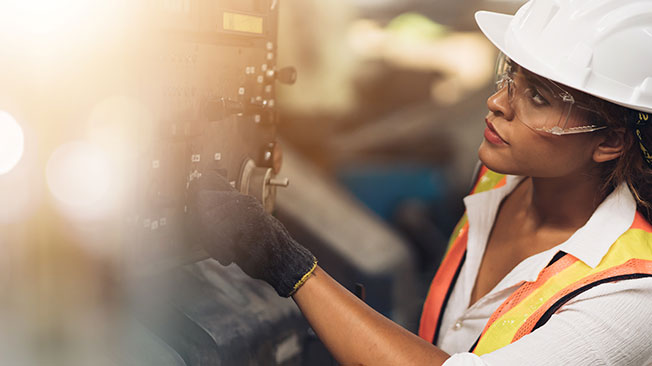
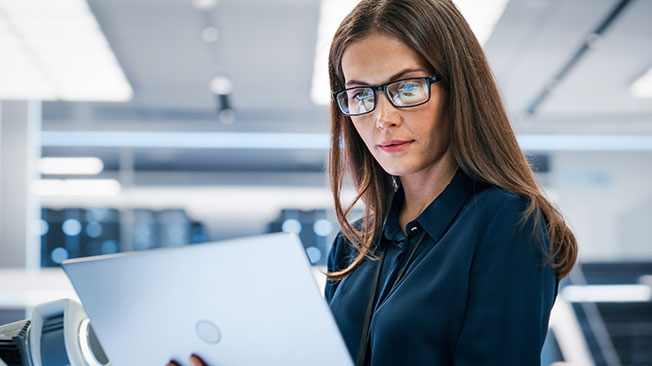
Design of Experiments (DOE)
Design of Experiments (DOE) is a data collection tool that uses applied statistics to analyze the impact of multiple input factors on the final outcome. Because DOE analyses multiple input factors instead of just one at a time, it can be used to assess different combinations of parts and materials quickly and accurately.
Value engineering
Value engineering is another methodology that focuses on achieving the highest quality product at the lowest possible cost. Value engineering is concerned with the functions of materials and components and not their physical characteristics. This methodology is used to assess what materials or parts could be substituted with cheaper alternatives. Value engineering’s main aim is to maximize the functionality of all components while minimizing production costs.
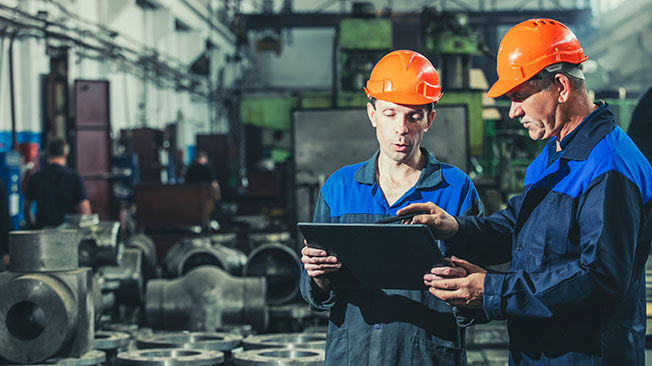
Browse all the Dassault Systèmes store applications
We feature in our store some of our best software to design, collaborate and innovate throughout the entire product lifecycle.
Content related to DFM
Design thinking research methodologies
The quest to improve the product design and manufacturing processes has resulted in the development of new methodologies. Design thinking research focuses on achieving lower production costs, reducing waste, improving product reliability, and enhancing efficiency.
The process of design thinking involves starting with a specific goal and then exploring as many options as possible toward achieving that goal. Design thinking arrives at solutions where need, possibility, and opportunity overlap.
Various design thinking methodologies have been developed, and chief amongst them is the concept of design for excellence (DFX). Design for excellence takes a holistic approach to product design. Its aim is to optimize all stages of the product development process.
Design for excellence has since been broken into different categories. Two of the main sub-categories of DFX are Design for Manufacturing and Design for Manufacturing and assembly (DFMA).
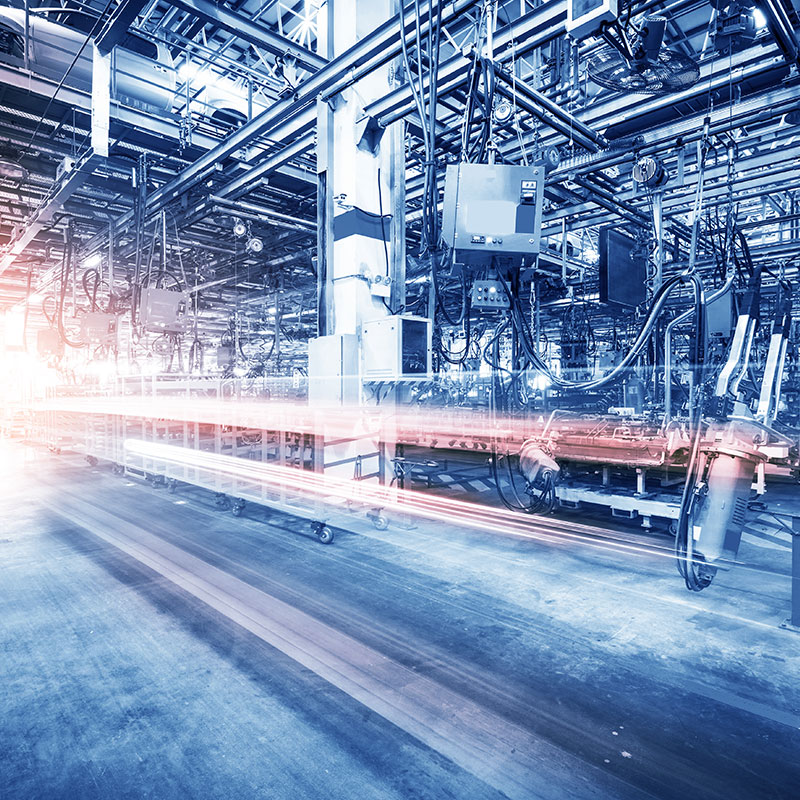
Best practices for design for manufacturing
Achieving the best outcome using the Design for Manufacturing methodology means ensuring that there is clear and effective communication between all stakeholders at every stage of the production process. There should be constant collaboration between the designers, engineers, and manufacturing teams. All teams should strive for continuous improvement by facilitating ongoing feedback loops.
Priority should be given to the standardization of parts and components to achieve a more streamlined manufacturing and assembly process. Detailed documentation must be generated so that design changes can be reviewed, and all stakeholders are kept up to date with iterations.
The design should be optimized for maximum flexibility and scalability. All materials need to be chosen with cost, sustainability, and ease of production in mind. To this end, designers and engineers should aim for total integration with supply chain management.
Design for manufacturing and assembly- DFMA
Design for Manufacturing and Assembly (DFMA) is a methodology that combines Design for Manufacturing (DFM) and Design for Assembly (DFA). It involves the careful analysis of all factors that are involved in manufacturing and assembling a product.
While DFA and DFM both have the same goal, to cut costs and enhance efficiency, DFA is focused on the assembly process while DFM is concerned with the design and manufacturing processes. In some cases, a process that is optimal for DFM will have a negative impact on DFA processes, nullifying the benefit of the change. DFMA seeks to align the interests of both DFA and DFM to ensure the entire product development cycle is as efficient as possible.
DFMA is concerned with tooling, raw materials, scalability, volume, automated production processes as well as other variables such as the skills of the labor force. The DFMA methodology involves analyzing how these factors influence product development and what can be done to make each of them more efficient. When DFMA principles are applied and all the factors are working together cohesively, it can result in a product being produced for less than half of the initial cost estimates.
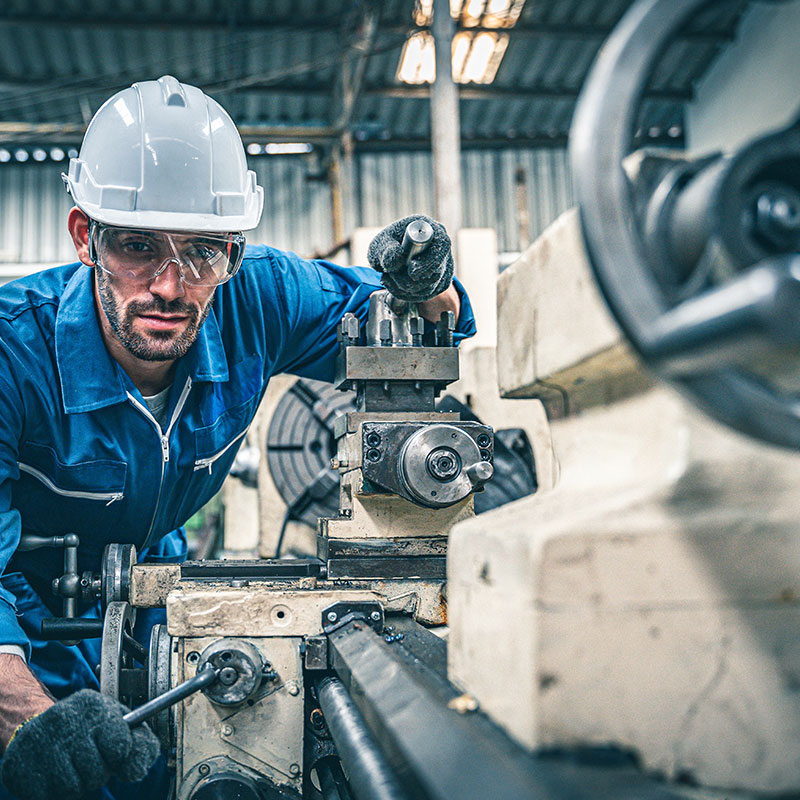
Explore Dassault Systèmes solutions
Discover the powerful browser-based modeling solutions from Dassault Systèmes. You can design whatever you wish, wherever you are with 3DEXPERIENCE.
Connecting data & people to foster innovation
The 3DEXPERIENCE platform on the cloud gives you access to a various set of applications that allow you to design, simulate, inform and collaborate on a project.
Conclusion : the importance of design for manufacturing
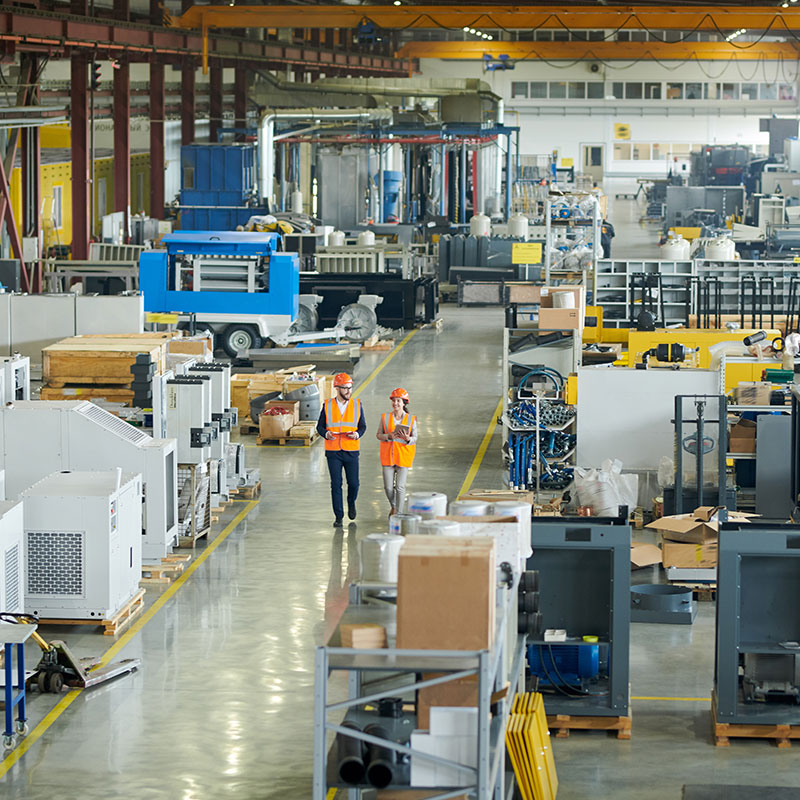
Regardless of what type of product a business is manufacturing, all enterprises want to minimize their costs and maximize their output. The principles of Design for Manufacturing are vital to achieving optimum design efficiency, enhancing the speed of manufacturing processes, and ensuring that maximum rates of production are attained.
It has been estimated that more than 70% of manufacturing costs are due to decisions made during the initial design process. Because DFM focuses so stringently on the design stages, it can lower final production costs and avoid budget overruns.
Using DFM can result in faster time-to-market, reduce production costs overall, and speed up manufacturing processes. A higher grade of quality can be achieved as DFM can be used to identify and eliminate issues early on in the design stages. Lean management principles of continuous improvement are more easily achieved using the DFM methodology, reducing waste and further enhancing the quality of the final product.
Explore inspiring content
Why choose Dassault Systèmes for your design for manufacturing needs?
The power of the 3DEXPERIENCE platform
Using the 3DEXPERIENCE platform, designers can harness immense computing power regardless of what type of machine they are using. Via the 3DEXPERIENCE platform, you can access industry-leading product creation tools such as CATIA Mechanical Designer and CATIA Sheet Metal Designer. Collaboration is made easier and more secure as users can share and store work in one digital environment from anywhere in the world, at any time. Explore the possibilities of the 3DEXPERIENCE platform today.
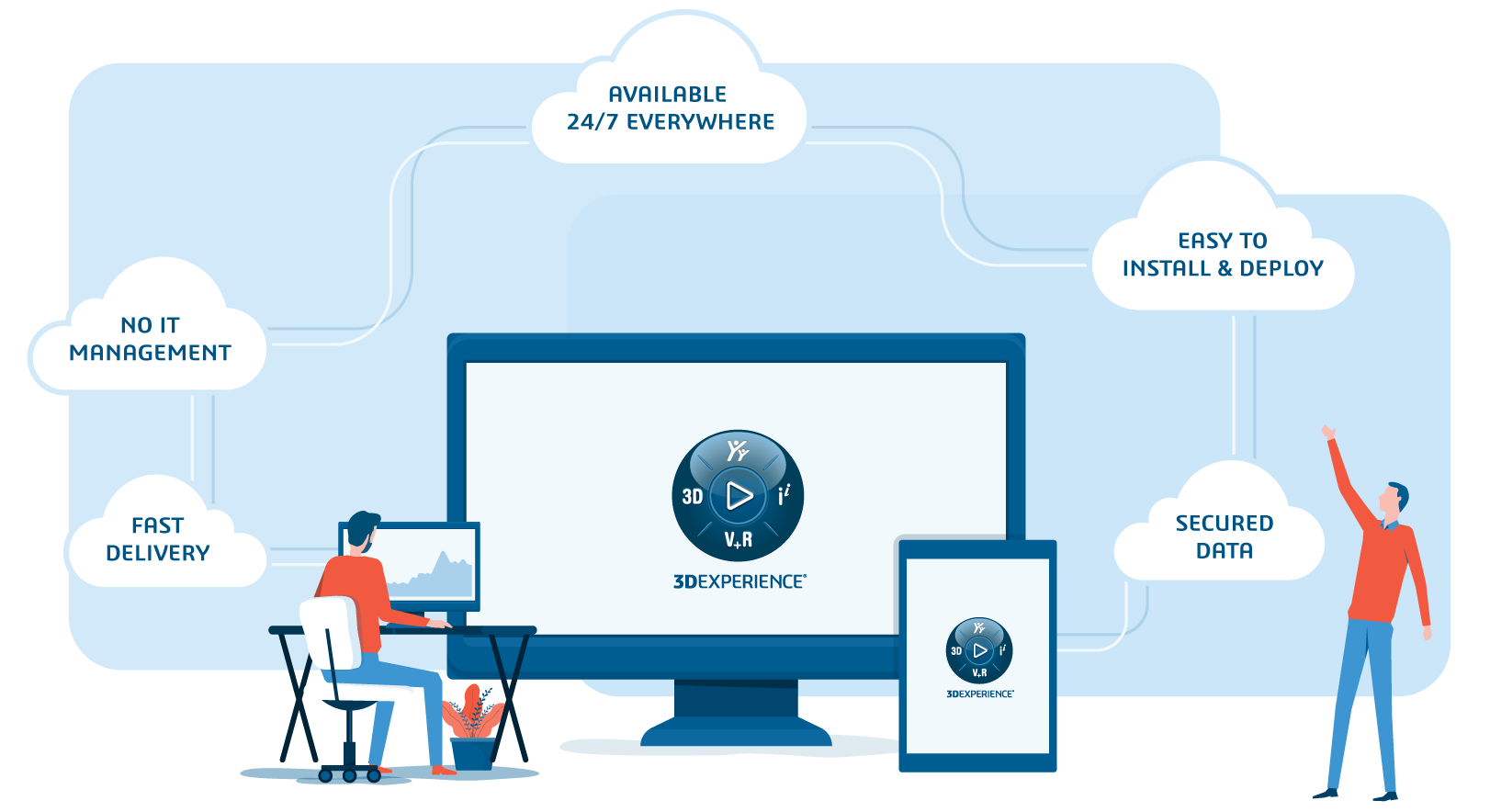
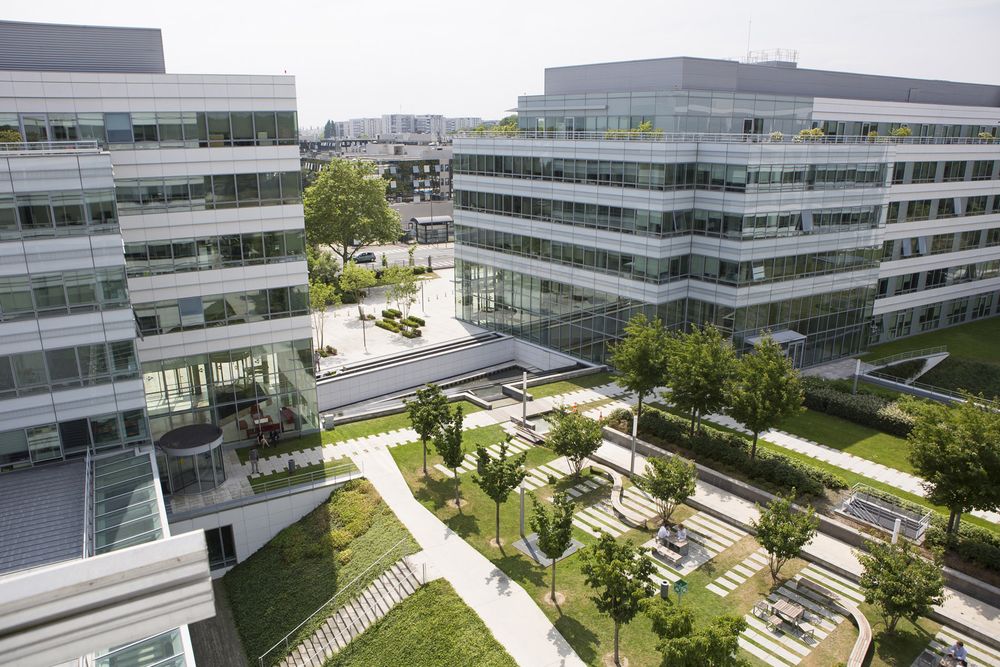
Benefit from more than 40 years of experience
Dassault Systèmes has stood at the cutting edge of CAD design for over four decades. We are proud of our reputation for innovation and creativity. Our goal is to provide elegant design solutions that can be used by both seasoned professionals and eager students. By actively listening to what our users require, we have been able to develop a suite of roles that fulfill the needs of designers, engineers, and artists across a wide spectrum of industries.
Discover the entire range of Dassault Systèmes roles at our online store.
Have access to DFM Training Courses
With the 3DEXPERIENCE platform you can access various training and formations based on your needs.