Revolutionize Safety in Manufacturing With the Digital Twin and IIoT
Standard safety measures aren’t sufficient anymore. Discover how the digital twin and IIoT pave the way to a bright new safety era despite ongoing disruptions.
As the global manufacturing industry faces more disruptions than ever before, companies need to find ways to elevate workplace safety. However, they are challenged by lengthy risk assessment procedures, extensive effort to improve workplace layouts and sub-optimal production rates due to safety measures that inadvertently restrict a factory’s full performance.
With the digital twin and industrial internet of things (IIoT), manufacturers can create safer work environments without compromising time, resources or productivity.
A factory’s digital twin is an accurate and detailed representation of the actual factory. With an integrated platform that offers a digital twin capability, manufacturers can simulate the impact of different manufacturing safety scenarios before executing decisions in the real world. IIoT connectivity utilizes factory data to maintain an exact digital twin and provide a single source of truth at all times.
Create Safer Factories With Simulation Technology
Learn how manufacturers can leverage simulation to promote safer work environments.
How Do the Digital Twin and IIoT Create a Safer Workforce Together?
The digital twin provides a testing environment for manufacturers to discover the best safety procedures for their unique factory. With IIoT integration that connects the factory, manufacturers achieve closed-loop synchronization where industrial safety is quickly realized in the real world.
Together, the digital twin and IIoT create visibility to manage all elements of operations in the manufacturing lifecycle for a safer workforce at every stage:
- Facility Planning
- Process Planning
- Manufacturing Execution
Facility Planning
The digital twin helps manufacturers define and validate the facility floor while reducing the potential for design-induced risks to workers.
Process Planning
Manufacturers can virtually model processes and avoid risks from real-world testing. Through the digital twin, manufacturers can simulate social distancing and plan for ergonomic work conditions without interrupting factory operations.
Manufacturing Execution
IIoT and management on a single platform provide constant visibility, enabling manufacturers to swiftly identify areas for maintenance and enhance response time to unplanned events.
Drawing on simulation technology, the digital twin visualizes endless possibilities for safe working environments.
Within this virtual environment, you can simulate various scenarios by changing equipment, parameters and layout. Then you assess the impact of these changes on production performance as well as worker safety.
Using simulation results, manufacturers derive and confidently implement appropriate countermeasures that help prevent the spread of airborne hazards without compromising on manufacturing safety or factory performance. Through IIoT connectivity, safety decisions are swiftly reflected in the real world.
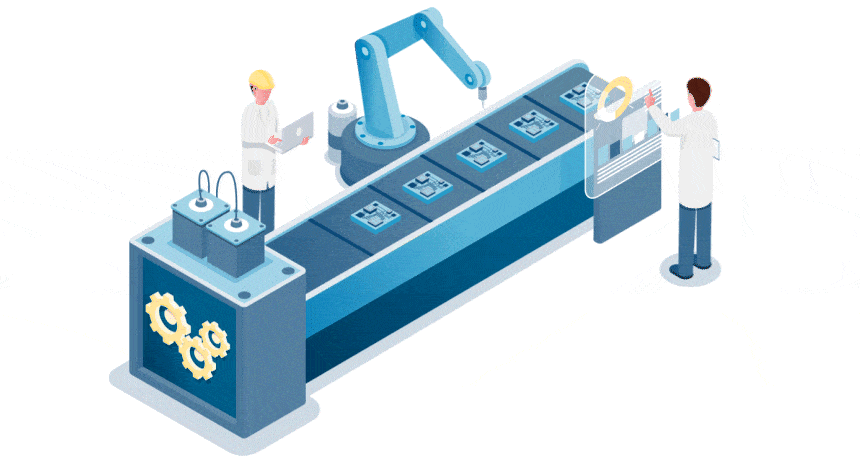
A New Era of Safety
In the face of ongoing disruptions, manufacturers are pressured to accelerate industry digitalization. For manufacturers who want to spearhead industrial safety, it’s critical to incorporate the digital twin and IIoT on the right platform.
Dassault Systèmes 3DEXPERIENCE® platform is an integrated cloud-based solution that enables manufacturers to achieve digital transformation. With full visibility throughout the operations, stakeholders work collaboratively to enhance efficiency and promote industrial safety in a revolutionary way.
By leveraging the virtual twin experience on the 3DEXPERIENCE platform, manufacturers can utilize the digital twin and IIoT to continuously improve operations, redefine best practices and lead the way to a bright new era of manufacturing safety.
Read our top articles on Operational Optimization
Explore our Industry Solution Experiences
Learn more about how our industry solutions can help you to achieve your professional ambition and business objectives