GEA
German-based GEA, one of the largest technology system suppliers in the food, beverage, pharmaceutical, and chemical sectors contracted Dassault Systèmes’ Engineering Services organization to simulate and visualize different scenarios for the re-opening of their cafeteria at its Oelde site using Computational Fluid Dynamics (CFD) simulation. The result: a comprehensive risk assessment for the re-opening after the lockdown in March due to COVID-19.
ENGINEERING FOR A BETTER WORLD
Roughly a quarter of all processed milk, half of all beer, and one-third of chicken nuggets worldwide are produced using equipment from GEA. As a leading technology systems provider particularly in the food & beverage sectors the company is used to reacting fast to changing market conditions. It is also committed to addressing urgent and pressing global issues that impact our future, such as climate change and the safeguarding of worldwide food supplies.
As COVID-19 spread across the world in early 2020, businesses faced the dual imperative of saving lives and livelihoods. They needed to be responsive to the dynamics of an evolving crisis and prioritize their people. For GEA, this was a prime opportunity to lean into the driving principle that connects its workforce: “Engineering for a better world.”
“We strive to be one of the world’s most respected technology groups and we’re driven by permanently changing markets,” said Erich Nitzsche, vice president of Engineering Standards and Services at GEA. “Engineering for a better world is really the energizing principle that connects all our employees and businesses we run.”
GEA’s commitment to “Engineering for a better world” has taken on even greater significance since the coronavirus pandemic. From the beginning, it has shouldered the responsibility of keeping its workforce as safe as possible while working closely with its customers to support them during this time. The company set up a global COVID-19 taskforce to facilitate the daily exchange of information and analysis, and keep all employees updated of the fast evolving situation and safety measures they were putting in place.
“Like many companies, we had pandemic preparations in place, but were not fully prepared for the impact of COVID-19,” Nitzsche said. “The China plant was shut down very quickly but, in the end, we only had to temporarily close three sites globally. Our risk awareness meant the impact on our business was very minimal. We had a fully running logistics chain at all times.”
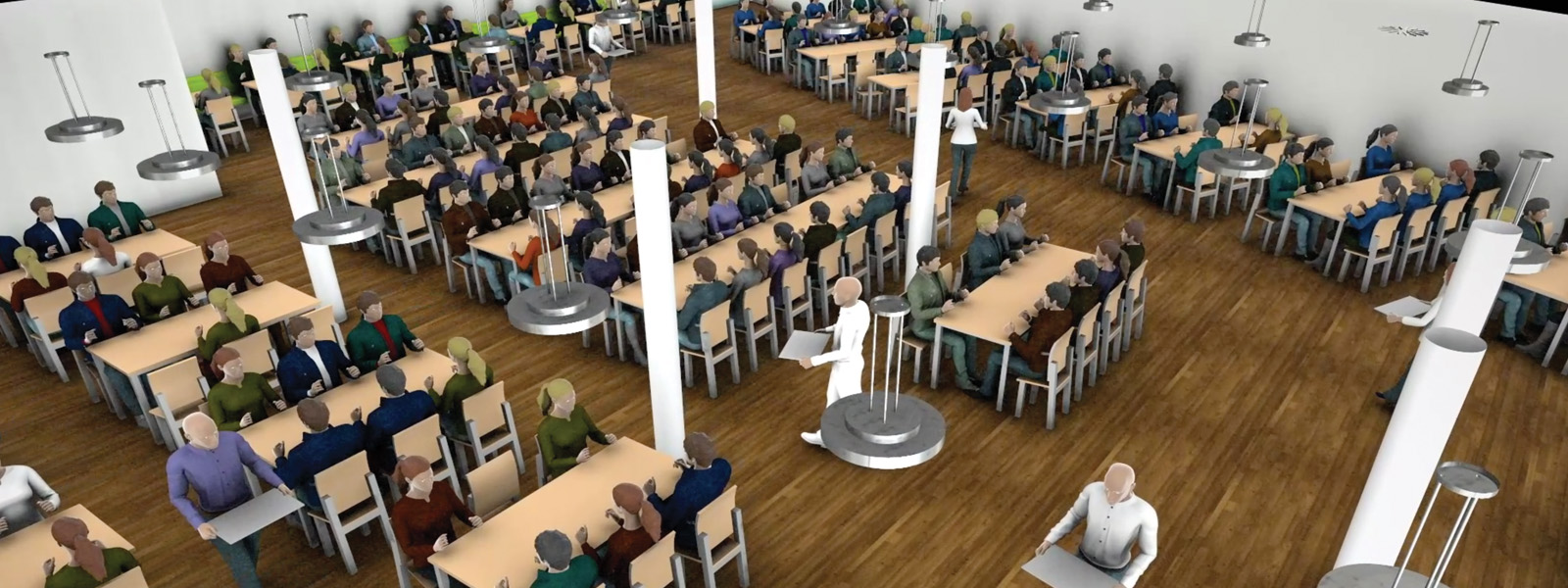
SAFETY THROUGH SIMULATION
In line with government regulations and to keep its workforce safe, GEA closed down its staff cafeterias, including the Oelde cafeteria – over 1,900 employees use this 645 square meter facility.
“The cafeteria is a really important place,” Nitzsche said. “Everyone goes here, it’s where we all get together to socialize and do business. We had to shut it down and clean it. But then you have to ask yourself the question, ‘how do I reopen it again safely?’. We needed a ramp-up strategy and to play out different scenarios to work out the best way of doing this.”
Mounting evidence showed that one of the main ways COVID19 can spread is through aerosol transmission. For GEA, then, it became a priority to understand the scope of virus propagation through airflows in the cafeteria, including through its heating, ventilation and air-conditioning system, and they decided to engage with Dassault Systèmes to launch a consulting project leveraging simulation.
“The idea was born to recreate our cafeteria as a full digital twin and to simulate the airflows and ventilation system to identify possible virus hotspots and to derive appropriate countermeasures,” Nitzsche said. “We picked simulation to bring light in the dark. For us it was a winning scenario as it presented no risk. We could learn from any number of scenarios and there would be no bad result as it’s all virtual. We know Dassault Systèmes and their competency on simulation, especially airflow simulation. It was a very easy decision to work with them and they executed exactly what we agreed.”
OUTSOURCING FOR PEACE OF MIND
Rather than taking on all the work themselves, it made sense for GEA to outsource the simulation project to Dassault Systèmes. Not only did this enable GEA to take advantage of Dassault Systèmes’ sophisticated IT infrastructure and server power to run the simulations on the cloud, it allowed them to tap into their technological expertise in Computational Fluid Dynamics (CFD) applied to HVAC systems and get the project underway quickly.
“What I really liked is that Dassault Systèmes took a very agile approach and this really eased our life,” Nitzsche said. “We would not have been able to ask the questions like they did. It would have taken us much longer if we’d have done it all internally. Outsourcing the project has allowed us to focus on our business and leave the experts to do the simulations. Of course, you can build up any kind of knowledge, but it takes time. Outsourcing gave us the agility we needed.”
The entire project was handled remotely due to the nature of the pandemic situation, but this didn’t hinder progress. From the start, Dassault Systèmes put a great deal of resources behind the project to ensure it was a success. “I’ve seen a lot of investment from the Dassault Systèmes side,” Nitzsche said. “I really liked the ramp up when we started. There was no messing around. On our first call 15 people dived in and for me as a customer, it was very cool. They asked all the right questions and you could almost sense that people went into action while we were on the phone. This investment at the beginning really paid off in the end. It left a great impression.”
Dassault Systèmes kept the team at GEA apprised of their progress at all times with regular communication and set clear milestones.
“I felt really comfortable at every phase of the project,” Nitzsche said. “What I particularly valued was that we were never overpromised anything. They communicated timelines clearly. I enjoyed that as it was very reliable and made my life easy as I could be sure we’d hit every target and milestone. They were always on time with content.”
Simulation has been the missing puzzle piece. We had the expectation that the results would be a basis for 20-30% of our decision. However, with the results that are now available, we have gained a confidence level of 60-70%.
IDENTIFYING HOT SPOTS
Using 2D blueprints and photos, Dassault Systèmes created an accurate digital twin of the cafeteria, including air vents, all furniture, including tables, chairs and counters, and used at-scale mannequins to create a realistic dining scenario. From there, it identified inlet and outlet air conditions and used vents documentation to simulate the right airflow behavior in the cafeteria, accounting for air leakages from emergency and entrance doors.
Numerous scenarios of people coughing in different areas were simulated using the SIMULIA PowerFLOW solver to understand how the virus could disperse around the cafeteria and kitchen areas.
“One of the most valuable observations has been to learn about the blind spots in this environment,” Nitzsche said. “That was the biggest surprise for me because our first approach for any re-opening is that we would have spread people out as much as we can in the cafeteria to dine. Now we can see that the places we would have put people in would have been danger zones as there is an extremely low exchange of air and viruses concentrate in these spots. It’s been a huge learning curve and completely opposite to our initial thinking.”
Indeed, the simulations clearly showed that the air is very stable in certain areas and could create concentration spots for aerosols. GEA also learned about how fast and far aerosols are likely to spread in the cafeteria environment too. “We’ve discovered that the entry point to the cafeteria is a high-risk area,” Nitzsche said. “If someone coughs or sneezes at the entrance, they could contaminate 700 square meters.
“Based on the results of the simulation, we can now initiate specific measures such as the revision of the entrance and exit concept as well as an adapted seating arrangement,” said Peter Brüggenkötter, head of HSE management at GEA. “The simulation makes us be more creative in our thinking and pushes us to solve these problems.”
The simulations also demonstrated how surfaces like plates, trays and tables could get contaminated during a normal lunchtime sitting. “We gained a deeper understanding of the air flow in our cafeteria and of the contamination of surfaces within the area,” Nitzsche said. “From these visualizations, our learning is that whatever we do in the future, we need to take specific actions to treat trays and plates in order not to create little bio bombs.”
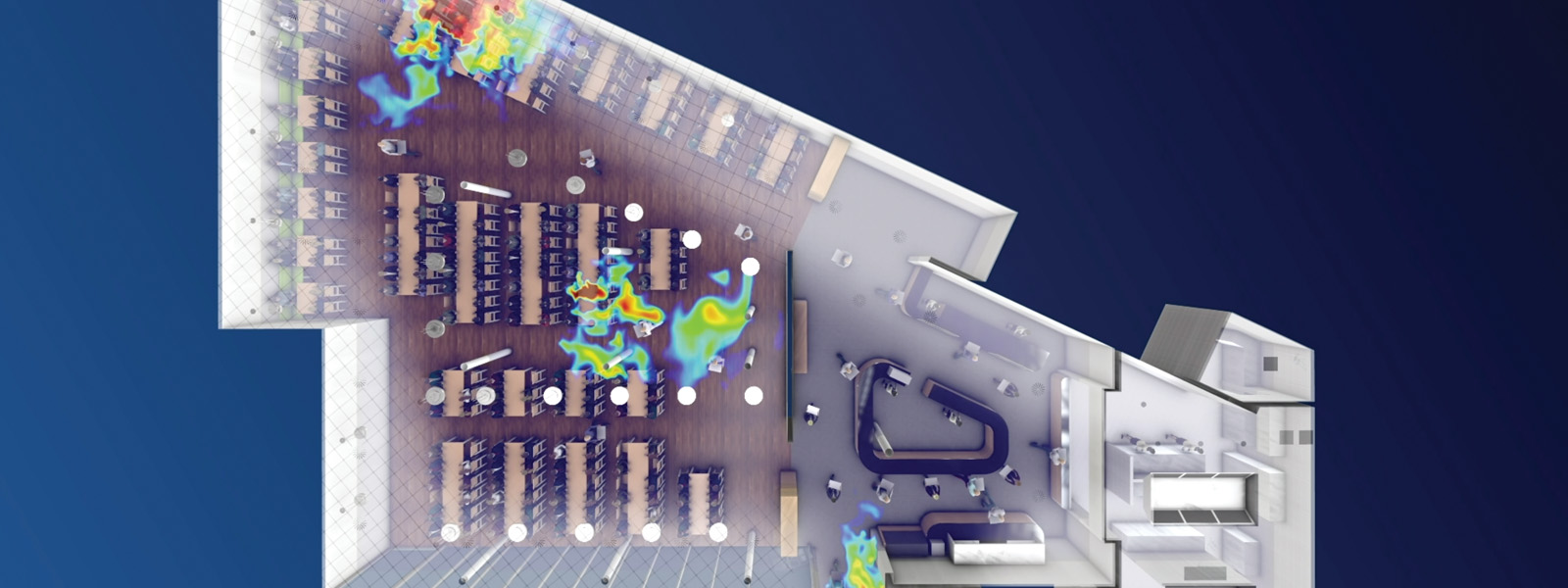
INFORMED NEXT STEPS
Using the simulation results, GEA now has a much clearer idea of the measures it must put in place to keep everyone safe when re-opening the cafeteria.
“We had the expectation that the results would be a basis for 20-30% of our decision,” Nitzsche said. “However, with the results that are now available, we have gained a confidence level of 60-70%. We hope to use the results with the derived measures to reopen the cafeteria soon. The simulation we have in our hands is very valuable in how we make decisions. We know what we need to do now. That is great progress for us. We wanted to make sure we acted in an ethical and social way and apply better safety measures based on technical facts beyond all governmental recommendations and legal requirements. It brings our “Engineering for a better world” principle to life”, Nitzsche continued.
The company also learned that it would need to apply additional safety measures in the kitchen area to protect its cafeteria workers.
“This was another new finding for us,” Nitzsche said. “Our first approach would have been to up the air extraction in the kitchen, but we were not aware that this would increase the air flow from the entrance into the kitchen, which would have put our workers in a really dangerous situation. We are now looking to separate the kitchen area from the catering area and make this mandatory. We have the option to play with the existing air conditioning technology and while we’re not totally sure of the most appropriate action yet, we know that our normal conditions wouldn’t be safe enough.”
For GEA, this simulation project is a win-win. Even if it decides not to re-open the cafeteria during the current pandemic situation – because of either safety or economic considerations – the company has valuable learnings about virus propagation that it can take to other areas of its business.
“The simulations help us make good decisions for our business and our people,” Nitzsche said.
The simulation supports us keeping our employees vigilant. The color coding makes it self-explanatory and easy for everyone to understand.
VISUALIZATION IS STRONGER THAN WORDS
As the pandemic continues, GEA plans to use the simulation results to communicate the measures it is putting in place, but also to encourage longer-term awareness and diligence to prevent a spike in cases of COVID-19.
“The simulation supports us keeping our employees vigilant,” Brüggenkötter said. “The color coding makes it self-explanatory and easy for everyone to understand.”
“This is especially valuable at a time when everyone is growing tired of this pandemic situation,” he added. “We need to motivate our people to stick to our safety measures at an enduring level and take every sensible action.”
In many ways, the simulation results and 3D renderings are a far more effective form of communication compared to other methods such as written materials.
“The visual picture is very beneficial for our people when we communicate and share this analysis,” Nitzsche said. “You can really see what’s happening. It offers huge value for us. In many ways, the video does the talking and requires little explanation; it’s not just preaching and setting rules. We also plan to share the simulation results with our customers to demonstrate our technical expertise. Throughout this situation, we’ve done everything we can to create customer intimacy and use our expertise to help them in a professional way. We will share these findings more widely among the global GEA too. We are quite unique with this approach and maybe other sites and divisions will learn from it too. Simulation has been the missing puzzle piece.”

Focus on GEA
“Engineering for a better world” is the driving and energizing principle connecting GEA’s workforce. As one of the largest systems suppliers, GEA makes an important contribution to a sustainable future with its solutions and services, particularly in the food, beverage and pharmaceutical sectors. Across the globe, GEA’s plants, processes and components contribute significantly to the reduction of CO2 emissions, plastic use as well as food waste in production.
For more information: http://www.gea.com