Additive Manufacturing for Stronger, Lighter and Better Parts
Improve operational flexibility and agility with on-demand manufacturing.
Additive manufacturing or 3D printing has come a long way since its introduction in the 1980s. As the technology matured in the last two decades, mainstream manufacturers are adopting it to overcome the constraints of traditional manufacturing.
Today, additive manufacturing levels the playing field for innovation and more cost-effective product development. With the support of an integrated digital platform, additive manufacturing can be part of a complete, hybrid manufacturing solution that integrates different manufacturing techniques for the best results.
Additive Manufacturing for Greater Flexibility
Find out how additive manufacturing helps manufacturers to produce stronger, lighter and better parts where and when they’re needed.
Research by Essentium shows that two-thirds of companies have more than doubled their use of industrial-scale additive manufacturing over the past year. We speak to Jean-Marc Cauzac and Dominique Galmel for their thoughts on how manufacturers can use additive manufacturing to their advantage from an innovation and business perspective.
Jean-Marc Cauzac
Jean-Marc has been with Dassault Systèmes for over 30 years. He currently handles the fabrication portfolio and specializes in the additive and subtractive manufacturing domains.
Dominique Galmel
Dominique began his career with Dassault Systèmes developing automotive powertrain manufacturing solutions. His current portfolio covers digital manufacturing, supply chain planning and optimization, manufacturing execution systems and additive manufacturing.
JM: The attraction to additive manufacturing is not the same for different domains. Manufacturers that want to deploy the technology need to be clear about what it can contribute to their production and business.
For marine and offshore, it's the ability to quickly print spare parts to replace damaged ones. As more than one million parts can make up an oil rig, it is impossible — and not cost-effective — to keep spare parts for all of them on the platform. Requests for replacement parts from suppliers may also take days or weeks.
DG: The aerospace industry is leading the way in using additive manufacturing to produce parts, and in particular metallic parts for end-use. Weight reduction and optimization that improve performance and reduce costly fuel consumption are key drivers.
DG: It is now possible to produce metallic parts using additive manufacturing. However, replication difficulty and deformation hinder the implementation of the technology for large-scale manufacturing. Instead of adopting additive manufacturing as a new way to make parts, manufacturers can combine the technology with traditional manufacturing for the best results.
JM: Metal deposition is opening up more opportunities for manufacturers that previously relied on the powder bed. They are no longer limited by product size and the manufacturing environment. They're now able to produce and repair bigger parts such as blades for wind turbines.
JM: In traditional manufacturing, production begins with a big block of material, which needs to be stored somewhere, ready for use. When the material is worked on, most of it will be removed.
In the aerospace industry, that's around 90%, so there is much wastage. Materials also need to be transported. So, implementing additive manufacturing reduces logistic costs, fuel consumption and carbon impact.
Additive manufacturing generates vast amounts of data with countless iterations, each with a different impact. Data collection can be wholly beneficial if supported by a digital business platform that can extract meaningful patterns from these data sets.
Unlock the Full Value of Additive Manufacturing on the 3DEXPERIENCE® Platform
Additive manufacturing generates vast amounts of data with countless iterations, each with a different impact. Data collection can be wholly beneficial if supported by a digital business platform that can extract meaningful patterns from these data sets.
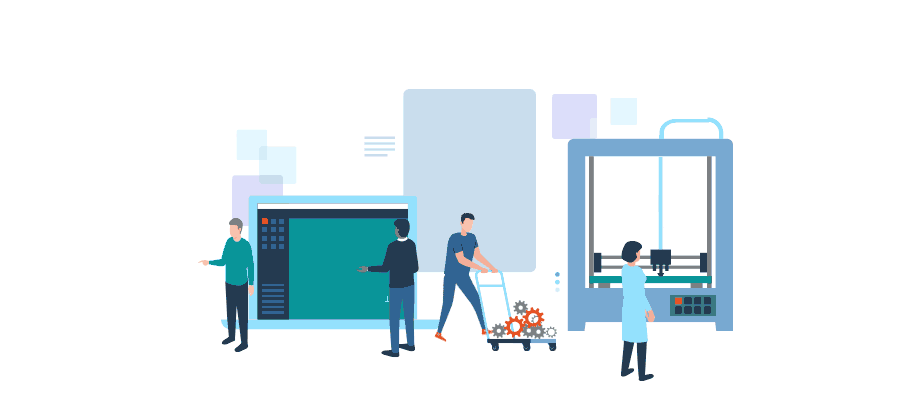
The 3DEXPERIENCE platform covers the entire manufacturing process from end to end. Data is streamlined and stored on the platform, offering manufacturers certification and replication capabilities. Manufacturers can extract past machine parameters to get the same results if an item needs to be reprinted in the future. Additive manufacturing leverages a 3D printer's stored data of characteristics, materials and laser paths.
The platform offers two levels of integration. The first level integrates the complete process and information flow from material research to parts production using optimization and simulation. The second level involves integrating additive manufacturing into the overall product development, including other production techniques such as stamping or molding.
The 3DEXPERIENCE platform enables automation and simulation, ensuring process updates every time something is changed. For example, manufacturers can develop several prototypes for COVID-19 masks.
A user's face is scanned and the manufacturing process is updated.
Parts are printed according to facial morphology.
Dassault Systèmes' simulation solutions help validate the parts.
The parts are printed right the first time, minimizing wastage.
In the last 40 years, Dassault Systèmes has been the preferred and trusted partner to industries that led the way with additive manufacturing. This level of confidence and decades of research and development makes us the right choice for companies embarking on additive manufacturing.
Read our top articles on Future Proof Systems
Explore our Industry Solution Experiences
Learn more about how our industry solutions can help you to achieve your professional ambition and business objectives