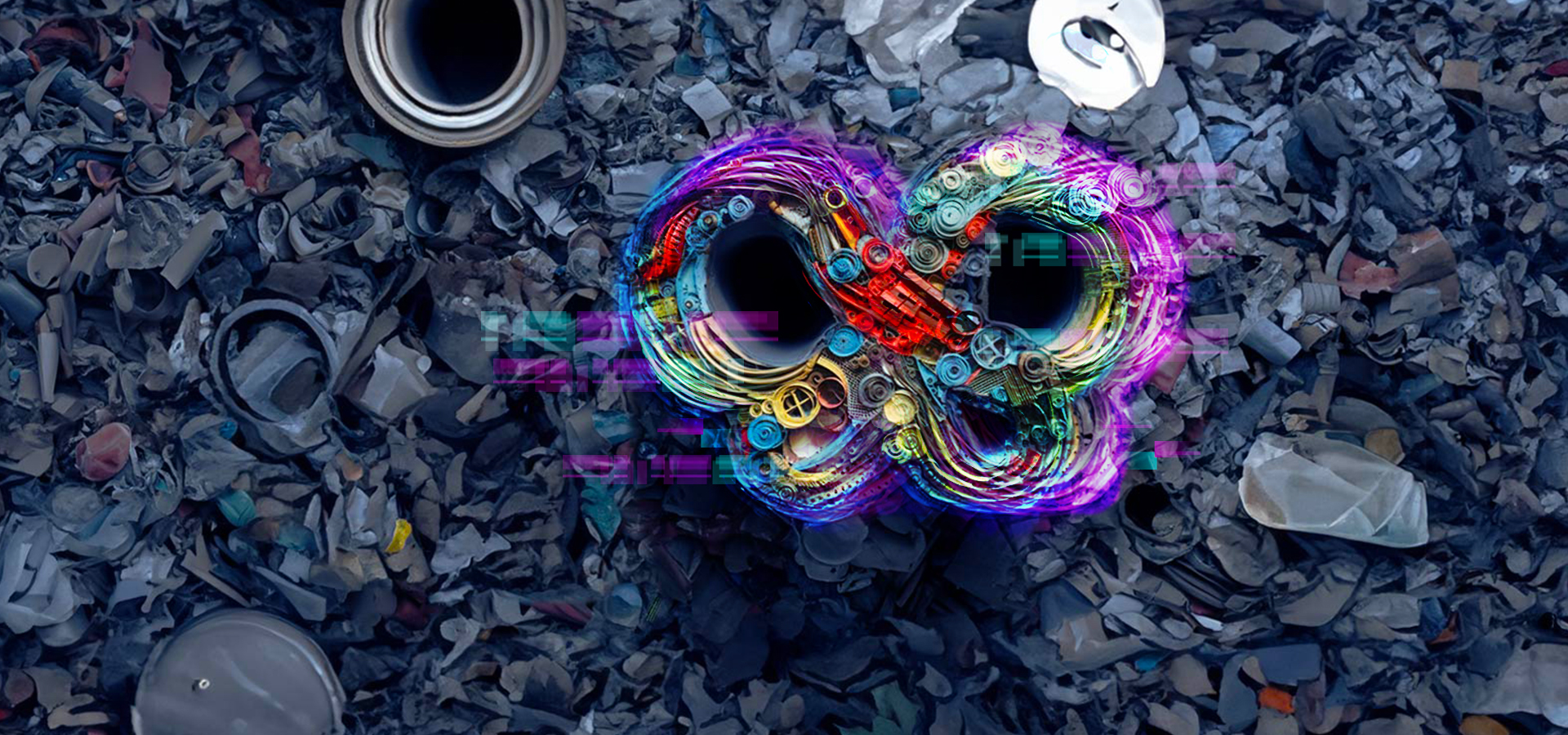
#08: How Do You Make Product Development Sustainable?
Embracing Circularity into Product Development through Sustainable Materials
#08: How Do You Make Product Development Sustainable?
The choice of materials can significantly impact your product’s environmental footprint. Listen to this episode as we explore how to infuse circular principles into product development through sustainable material design and innovation and learn how to make the best material selection. Discover more
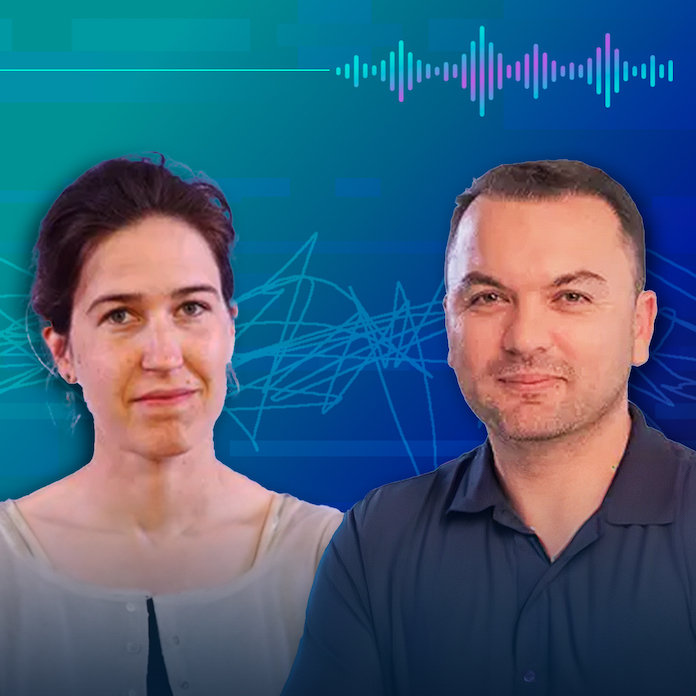
Meet our speakers
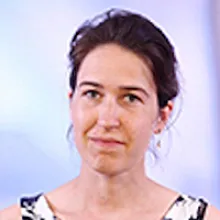

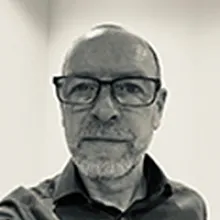
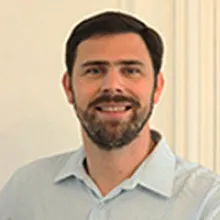
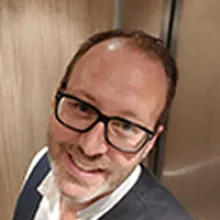
Read the transcript
Narrator: Welcome back to Disruptors Unleashed, where we look at the disruptive technologies shaping our world, and the trailblazers igniting change across industries. Previously, Mike Bradford from Dassault Systèmes looked at the digital revolution taking place in inventory management, and how it can improve efficiency, simplify processes, and increase collaboration across supply chains.
In this episode, we’ll be exploring how you can infuse circular principles into product development through material selection, design and innovation. Let’s get started.
Carlijn Goedhart: It starts with lifecycle assessment to know which material has the biggest impact on the final product. So, let me give some examples. If it turns out that the biggest impact is in supply chains, then optimizing your sourcing strategy may be helpful here. And that's going to be a true challenge because we have the amount of suppliers, the availability and the quality of the recycled materials. So, that may be an idea to look into.
Then, if the impact is in manufacturing, like in most industries, it’s actually easiest to just use virgin materials, but with optimization, we can enable the use of more recycled materials instead. For example, in the steel industry, chemical composition is very important. You cannot just put all scrap materials in for the final product, but you carefully need to mix and blend the right type of scrap materials together for that final product. And for that, matching the demands and the available recycled supply can be helpful.
Then, if the impact will be the most in the material itself, it may be worth looking into the recipe. For example, for cement, there is sand, water and some other ingredients. If you define in which ingredients the most waste is generated, then you may look into alternative ingredients to remove or reduce the amount of waste. So, these are just some examples, and Dassault Systèmes can enable companies to make these materials more circular.
Karim Fradj: Sustainable sourcing is the first step toward circularity. To achieve this, companies need to align their sourcing strategy with their ESG and sustainability goals globally. There are opportunities to easily achieve this by buying renewable energy, procuring energy efficiency technologies and deploying them into different production sites, purchasing other companies' and organizations' waste and byproducts, and then using those as raw materials. We can also acquire or buy carbon credits and other sustainability assets.
And here are some real-life examples of companies that succeeded in incorporating those practices into their operations. We have, for instance, IKEA. IKEA is participating in some councils like the FSC in order to make sure that they are managing the sourcing of their raw materials in a very sustainable way and also investing in programs that promote reforestation and biodiversity. We have, for instance, Patagonia. Patagonia's recycled materials initiative, Worn Wear, is where they encourage their customers to buy used clothes and, therefore, reduce the demand for new products. We also have the Unilever initiative, RSPO, where they have a goal of achieving 100% sustainable palm oil sourcing.
Mel Creasey: Innovating with new sustainable materials is not easy. This is not a trivial task, and companies need to quickly understand how a new material might behave throughout its entire lifecycle, from the initial conversion of that raw material into a packaging structure right the way through to the recycling and disposal of that product, or reuse, if that's the actual intent for the pack solution.
Any new material needs to be capable of satisfying a complex range of business and consumer requirements. With the right effort, these design requirements can be understood and satisfied with the use of simulation. Simulation greatly helps companies select the right materials and helps with concept creation, design development and scale-up. However, this is only possible if the material behavior itself is really well understood. This requires some effort to create good material performance.
When new and sustainable materials can be accurately modeled, this creates value opportunities in many ways. First of all, it allows design teams to understand the structural performance of a new pack design early in the design development process. It also creates the opportunity to simulate and understand the effects of real-world variation throughout the entire value chain: For example, variation in the raw material ingredients themselves or in the manufacturing process, and how this might affect material quality behavior and performance downstream. Variations through the factory, supply chain and distribution channels can be understood, and environmental factors like temperature and humidity — all these can affect material behavior and, ultimately, packaging performance. Being able to simulate and understand each of the above helps companies to quickly and confidently scale up new innovations so that they can be deployed into diverse markets, supply chains and diverse environments, where it can be safe in the knowledge that the material and the design are going to perform as expected and meet consumer expectations while satisfying the business environmental targets.
Whilst simulation is continuously advancing and developing, I think it's important to acknowledge that physical testing of the final design is still a key step in the process. But increasingly, this is becoming more of a validation step rather than a learning step, where potentially unwanted or unforeseen risks might be realized. Simulation brings information and a level of understanding and confidence that is simply not achievable without it and ultimately helps companies to develop packaging innovations using new sustainable materials faster than ever before.
Remi Dornier: I think the first approach is to leverage biomass. I often hear about the project to capture carbon. I know very interesting features today that capture carbon: These are trees, and trees capture carbon when they are growing. And then, we can make very good use of that in construction. And today, we see more and more initiatives done in order to replace concrete with materials.
And I wanted to emphasize one of the examples of our customers called Piveteau Bois. Piveteau Bois, it has a very interesting model: It owns a forest. And it has responsibly used this forest, in fact, for 50 years, and it takes some trees of the forest and what it does is make maximum use of those trees. So, it uses all the scraps for heating. The low-quality wood material is used to make, in fact, some bardage – what we call facade – and so on, and the high-quality materials are used to make construction materials. And we have been helping it to make the next generation of materials called cross-laminated timber. So, this material is able to replace concrete slabs inside the factory and inside the buildings, and we help it to reduce and improve the productivity of the line by 15% by using, in fact, the virtual twin experience inside the factories.
Another example we could share is that we can think about the functions of materials. If you take a facade element of a building, this is aesthetic; this contributes to the shape of the buildings and it's to view the outside, of course.
Today, we have an example from China, where customers such as CNBM and CSADI – one of the biggest architecture and engineering institutes in China – are designing net-zero towers that are, in fact, energy-positive and that have some facades that generate energy. How did they do that? They engineer a new material, which is a photovoltaic glass panel that's able to generate power. So here, we doubled the functions of the material, and this is very interesting since we are able to move toward more energy-positive towers.
Last but not least, we cannot focus only on the building itself — we can focus on the sub-components of the building. So sub-pieces, and for that, we have many SOLIDWORKS customers today, such as Assa Abloy, which is working, in fact, on all locking systems and improving their subsystems. So, it tries to reduce the quantity of materials used to decarbonate and find the best alternatives. And today, it’s also very important to work, in fact, on the sub-assembly's level.
Sriyani: Next up, we have Yann Pithon. He is the Business Value Consultant Expert, of the Business Services Industry at Dassault Systèmes. Hi, Yann. It's good to have you here. We've just been chatting about sustainable materials, so can you tell us how companies can become more circular? Perhaps through their packaging strategy?
Yann Pithon: When it comes to circular economy or sustainability, one of the first things that pops up in my mind is the packaging strategy. It should be because we're all confronted with that in our real life. We all have the same feeling sometimes when we receive an order that's delivered with the wrong parcel, because it's empty, or because it's a big box for a small product. So, it easily comes to mind for anybody.
If we think about what can be different, let's say the first thing we are thinking about is that parcels are built with recycled products — not only recycled products but also products coming from bio-based materials, for instance, wool and algae. These are examples that are already coming to the market.
We may also use parcels with a manual height adjustment that will allow the packer or the operator to get the parcel at the level of each content and avoid using additional filling materials. The use of technology is also to optimize the packaging strategy and support the operator in the parcel selection to have the best parcel fitting the order, depending on the product characteristics that the order contains, but also to avoid putting filling materials inside.
We can have some technology that will help the operator split an order into several parcels in order to optimize the saturation rate of the parcel and also to optimize the pellet building and the truck loading. And if we go to the extreme, we can also have industry-setting automated packaging equipment or semi-automated packaging equipment. And the carton will be built around the content of the order and the packer; we don't have to select anything.
Sriyani: Absolutely. It's great to learn that technology can help companies improve their strategy, and avoid unnecessary filling materials. Now, I like that you also made a point about what could be different, not just packages built with recycled products, but also using bio-based materials like wool and algae. That was very interesting. Thanks, Yann, those were some good insights.
Narrator: Disruptors Unleashed is produced by Dassault Systèmes. For more episodes, follow us on Apple Podcasts, Spotify, Deezer, or your nearest streaming platforms. To learn more about Dassault Systèmes, visit us at 3ds.com.
Discover the Pillars of the Circular Economy
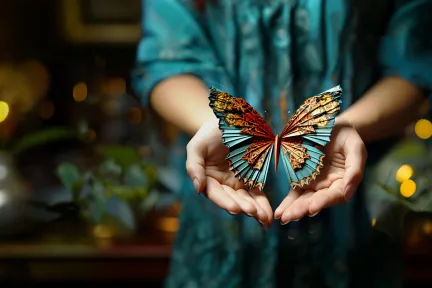
It’s time for concerted action. Here’s how to make the circular economy achievable, scalable and profitable.
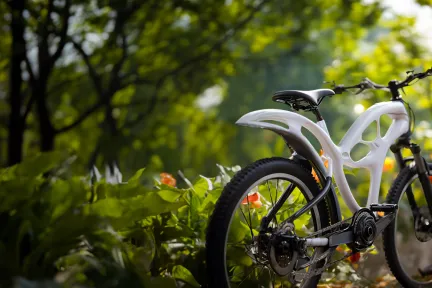
Products designed for circularity are pivotal in shaping the environmental impact for generations to come.
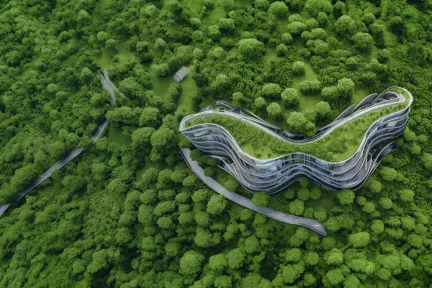
Transform how you do business through circular supply chains to achieve profitability and lasting success.
Learn more
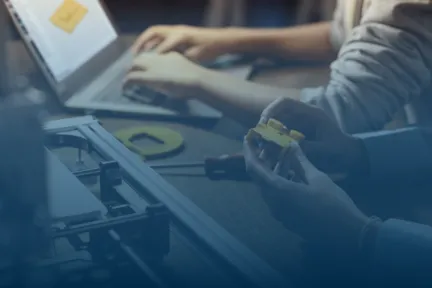
From biodegradable plastics to nanoscale structures, new materials will transform the way we live – if we can develop and produce them at scale.
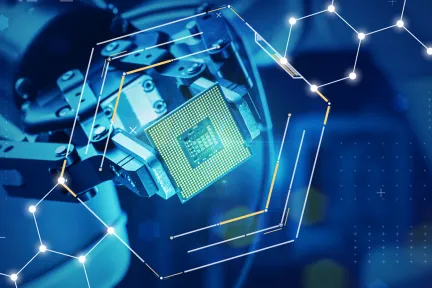
Modular supply chains make it easier for manufacturers to master complexity and strengthen their supply chain resilience against volatility.
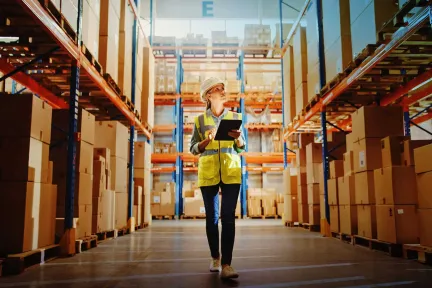
Proactively anticipate risks and mitigate disruptions in your automotive supply chain network.
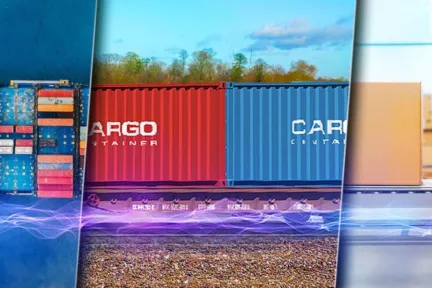
Recent global disruptions necessitate a reset for supply chain and logistics services to deliver more efficiently. Integrated logistics on the right digital platform holds the answer.
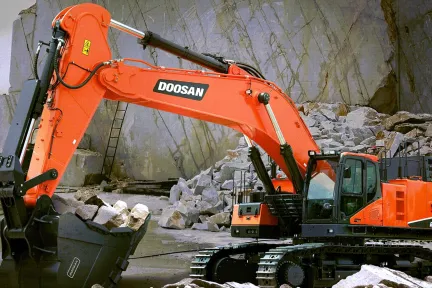
Hyundai Doosan Infracore succeeded in synchronizing manufacturing best practices across multiple global plants with DELMIA Apriso, as part of their journey to build the Factory of the Future.
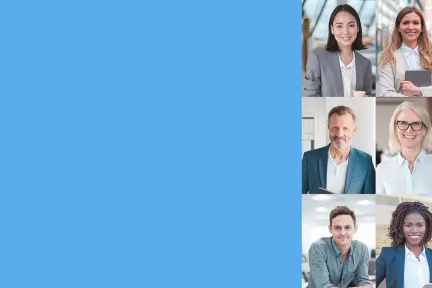
Manufacturers make the world. But the world is rapidly changing. Understanding how best to embrace these changes is crucial to driving innovation and growth over the next decade.