Unbrick
Turning the traditional process of home construction on its head, Unbrick implemented 3DEXPERIENCE on cloud to build houses faster, smarter and more sustainably. Digitizing its processes from end-to-end enabled the company to develop collaborative design, improve efficiency and create complex assembly instructions.
A new generation of sustainable housing experience
As a result of its commitment to sustainability, Netherlands-based Unbrick is one of very few construction firms permitted to build in a Natura 2000 area – a network of protected areas covering Europe’s most valuable and threatened species and habitats. It is the largest coordinated network of protected areas in the world, extending across all 28 European countries, both on land and at sea.
“Building in these areas is highly regulated,” said Theodore Tonino, Unbrick’s director of engineering and technology. “So much so that we cannot emit any nitrogen at all during the manufacturing and construction process."
Unbrick has also achieved a A++++ energy label. "This is the highest accolade for energy efficiency you can achieve in our region,” said Krijn Smits, Unbrick’s director of brand and customer experience.
How is Unbrick able to build so sustainably? By turning every part of the traditional process of building a home on its head.
Within the building world, if you want to start a company like ours, it would take around 5 to 8 years using traditional methods. Thanks to our innovative approach, teamed with the 3DEXPERIENCE platform, we did it within 2 years.
Unbrick’s new approach to building houses is revolutionizing the Dutch market. The company is using sustainable materials such as FSC-certified wood, and is assembling different modules in their own purpose-built facility, before delivering them to site. Unbrick’s homes include solar panels that produce twice as much energy as they need. To make sure the buildings have an independent water supply and sewage system, the company is using certified sustainable materials as well as Helophyte Filter systems, which are natural but very effective.
“We are trying to build houses faster, smarter and more sustainably by questioning every step of the construction process,” Smits said. “We can take this approach because we don't have the legacy that holds traditional firms back.”
A company this progressive requires a technology platform to match. “With the traditional way of working, the construction firms end up with a lot of redundancy and are used to do a lot of rework since they have to exchange files between point solutions,” said Theodore Tonino, Unbrick’s director of engineering and technology. “They also struggle with scalability – there’s not enough detailed design information to sustain simulation, which makes it difficult to improve performance. We wanted a different approach. We sought an integrated solution that could give us traceability and accountability, as well as scalability and collaborative design features.”
Unbrick set about looking for a solution that could meet its exacting needs. “We looked at many solutions, but they failed to deliver the performance and scalability we were after,” Tonino said. “Then, one day, I saw a video of one of Dassault Systèmes’ Belgian customers who was explaining how his company manufactured parts of a truck. He described how he could access all of the data he needed from a single solution and that the platform was able to scale with his company as it grew. This was a lightbulb moment for me – I decided we needed to investigate the 3DEXPERIENCE® platform further.”
This was the perfect starting point from which Unbrick could realize its vision.
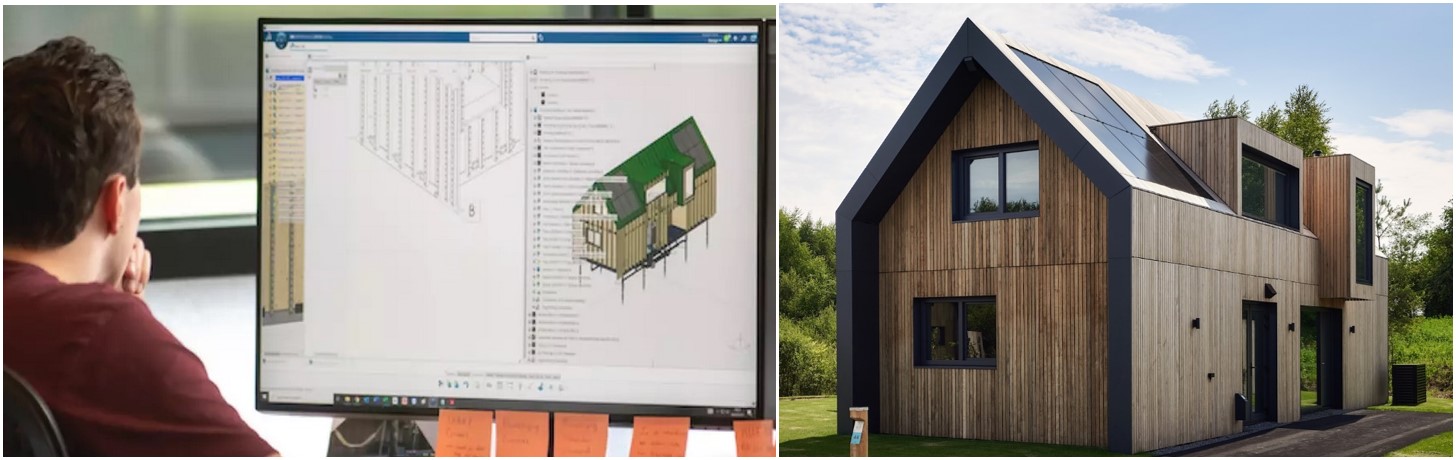
Virtual twins prove their worth
Unbrick sought advice from local partner Keonys to help it quickly and easily implement the 3DEXPERIENCE platform on cloud, as well as to support its team with training, and spotting design and manufacturing new opportunities. Thanks to KEONYS' expertise, Unbrick’s engineers deployed an optimal collaborative design approach and reduced the time spent on design changes. On the manufacturing site, the experts’ guidance helped the company to take full advantage of DELMIA capabilities on the platform, including manufacturing bill of material structure and process plans.
“We trusted KEONYS to support us with the platform’s rollout and to adapt it to the construction industry specificities,” Tonino said.
By adopting the 3DEXPERIENCE platform on cloud, the Unbrick team has been able to create an integrated, data-driven environment that facilitates effective collaboration and can scale as the company grows. Unbrick was able to digitize its entire end-to-end processes, from the initial idea to the finished building.
“Because we are a new company, with no need for data migration, the implementation was very smooth,” Tonino added. “Also the cloud is safer. The risks of corrupted or missing data are very limited. Crucially, you can access your data from anywhere.”
Leveraging unified modeling and simulation – known as MODSIM – on a single platform, design and analysis engineers took advantage of the platform with the critical advantage of creative, collaborative design with enhanced product insights. This approach also helps minimize risk and maximize performance, all while accelerating sustainable innovation.
Unbrick’s first project using the design capabilities of the 3DEXPERIENCE platform was to engineer a series of premium holiday homes.
“Traditional systems and workflows tend to be quite primitive – it’s not unusual for files to be shared via e-mail, or even for printed plans to be sent by post, which makes it difficult for stakeholders to know whether they are working with the most up to date design files,” Tonino said. “Using CATIA on 3DEXPERIENCE, we were able to produce incredibly detailed virtual twins of our homes. We could create high-resolution plans from these virtual twins that could easily be shared with external stakeholders who can actually log into our platform and work with us there. They can view the live data and get a complete bill of materials, so the process isn’t open to interpretation – which means there’s less chance of errors. Mistakes are very costly in this business, so that’s a huge selling point for us.”
These external stakeholders include the FSC-certified wood supplier, who is able to access the designs it needs to pre-fabricate parts directly on the platform. The wood is cut using CNC machines, following very detailed plans that optimize how the roll stock should be cut to minimize waste. The various pre-cut components of the homes – like the floors, walls and ceilings – then arrive at Unbrick’s factory ready to be assembled.
“Following the step-by-step work instructions that we have created using DELMIA, our engineers then assemble the homes in the same way they would do with a LEGO® model,” Tonino said.
“You can even see the threads on a screw,” Smits added. “It means the assembly team can tell exactly how deep they need to screw. There’s no room for guesswork on anything. And, because the plans are so detailed and easy to follow, it also makes it easier for us to recruit and train production staff.”
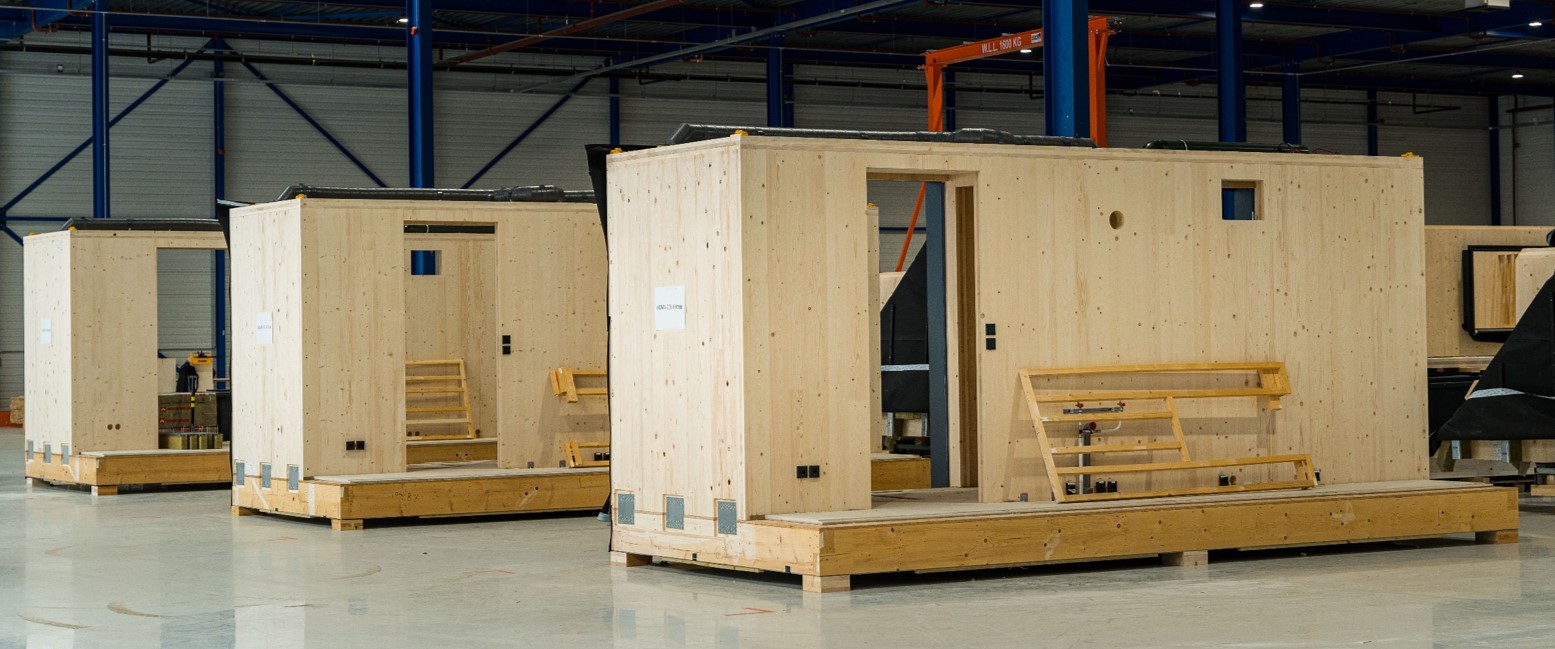
Better beats best
By doing everything from a single location, Unbrick has streamlined the way it works. The shell modules are developed in one production hall. Once complete, these modules are then moved into another production hall, where they are made up into rooms – this might be a kitchen, a bathroom, a living room or a bedroom, for example.
“Once we’ve finished one house, which takes two to three days, we can move straight onto the next,” Tonino said. “Not only is this a much more efficient way of working, but it also makes it easier to spot any problems.”
The completed modules are then transported to site for assembly – a process that takes just five hours.
“Even the way the modules are transported to site has been carefully thought out to optimize efficiency and lessen our impact on the environment,” Smits said. “The first times, we found we needed four trucks to move a house from our factory to the construction site. However, by using the 3DEXPERIENCE platform to simulate the various loads, we have been able to reduce this down to three trucks.”
While the Unbrick team is already working efficiently, they are not resting on their laurels. The company adopts the principle of ‘better beats best’.
“This means we’re always looking for ways to innovate,” Smits said. “We aim to make our homes better every day, always seeking to improve our efficiency, our sustainability and our production techniques. This is only possible with a solution like 3DEXPERIENCE. It allows us to test new ideas quickly and easily, and make tweaks where necessary. It makes continuous improvement possible.”
Using SIMULIA’s parametric design functionality on 3DEXPERIENCE, for example, the engineering team is able to seamlessly evaluate a number of design variants and pick the design that best satisfies their requirements in attributes such as function, sustainability, costs and labor involved.
“It influences practically every decision we make,” Smits said. “But it also gives us the freedom to make as many iterations as we need to. We might try something, and if we see it doesn’t work, we can do an iteration. There are small differences from the first up to the fifth house we built. By the sixth, we had eliminated most of issues and mistakes. The iterative design functionality means we don’t have to keep repeating the mistakes.”
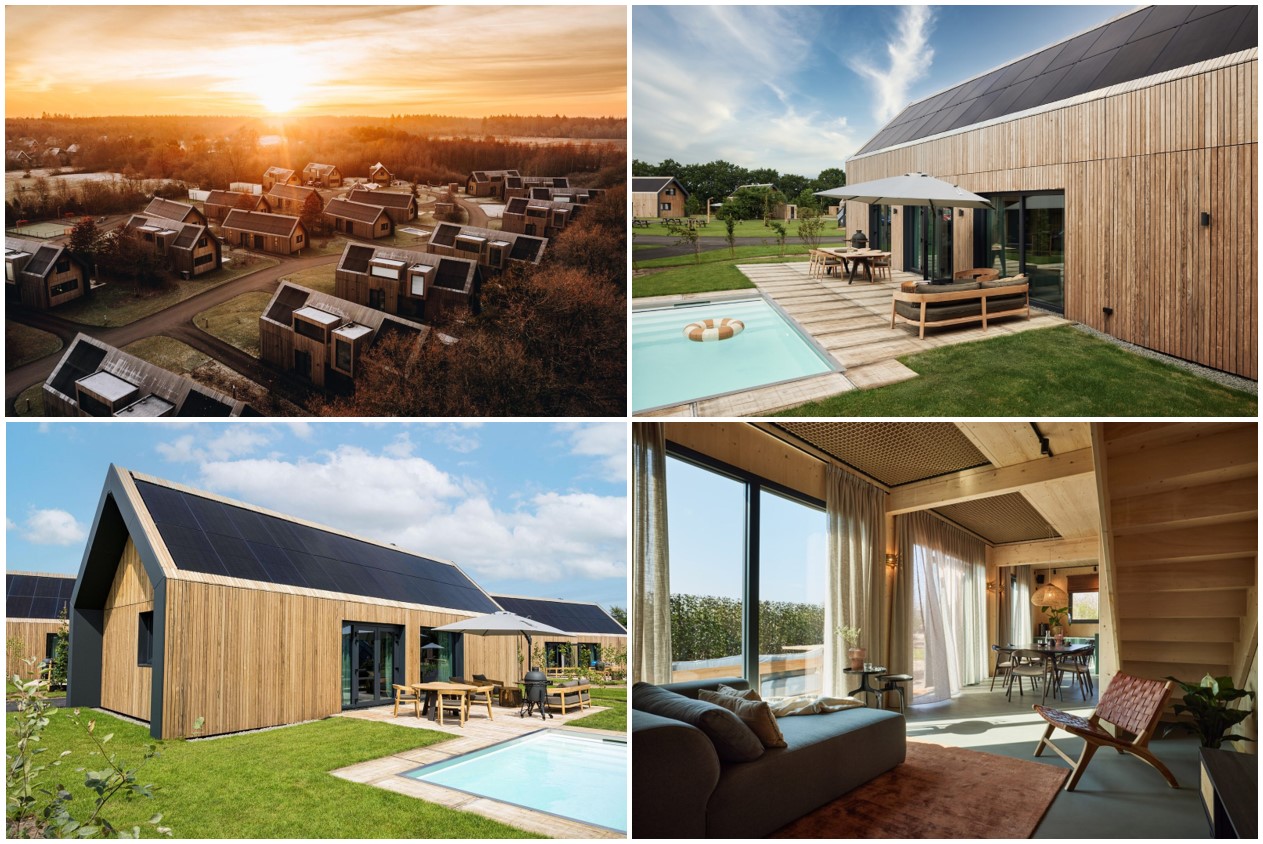
Scaling for success
Following the roaring success of Unbrick’s first holiday park, the company has begun developing two new parks.
“We are trying to turn the construction world upside down,” Smits said. “To achieve that, we need to expand beyond holiday homes. In the near future, we want to develop more factories offering different products. That will be a very important step for us.”
Smits is confident the 3DEXPERIENCE platform can support Unbrick’s future vision.
“We’ve already achieved something big,” he said. “Within the building world, if you want to start a company like ours, it would take around five to eight years using traditional methods. Thanks to our innovative approach, combined with the 3DEXPERIENCE platform, we did it within two years.”
The company is looking to expand its use of the 3DEXPERIENCE platform so that it can realize even more efficiencies.
“We’re particularly interested in adopting the Plant Layout Designer functionality, which will enable us to create accurate digital representations of the floor plans of our facility and simulate our entire production lines so that we can optimize our factory resources even further,” Tonino said. “We also hope to adopt ENOVIA’s project management capabilities so that we can improve visibility across every part of the process.”
As the company grows, the platform will scale with it. It has already supported Unbrick’s growth from 10 to 80 employees.
“Dassault Systèmes is as forward thinking as we are," Tonino said. "We see how the platform is developing every day – new features are being introduced all the time. Ultimately, there’s just so much value in having all of your data in one place. It means everyone can look at the data in a way that’s relevant to them. And, because of that, you can reduce process steps, time and waste too – three things that are crucial to running a sustainable business.”
Discover more about the Building Design for Fabrication industry solution experience.
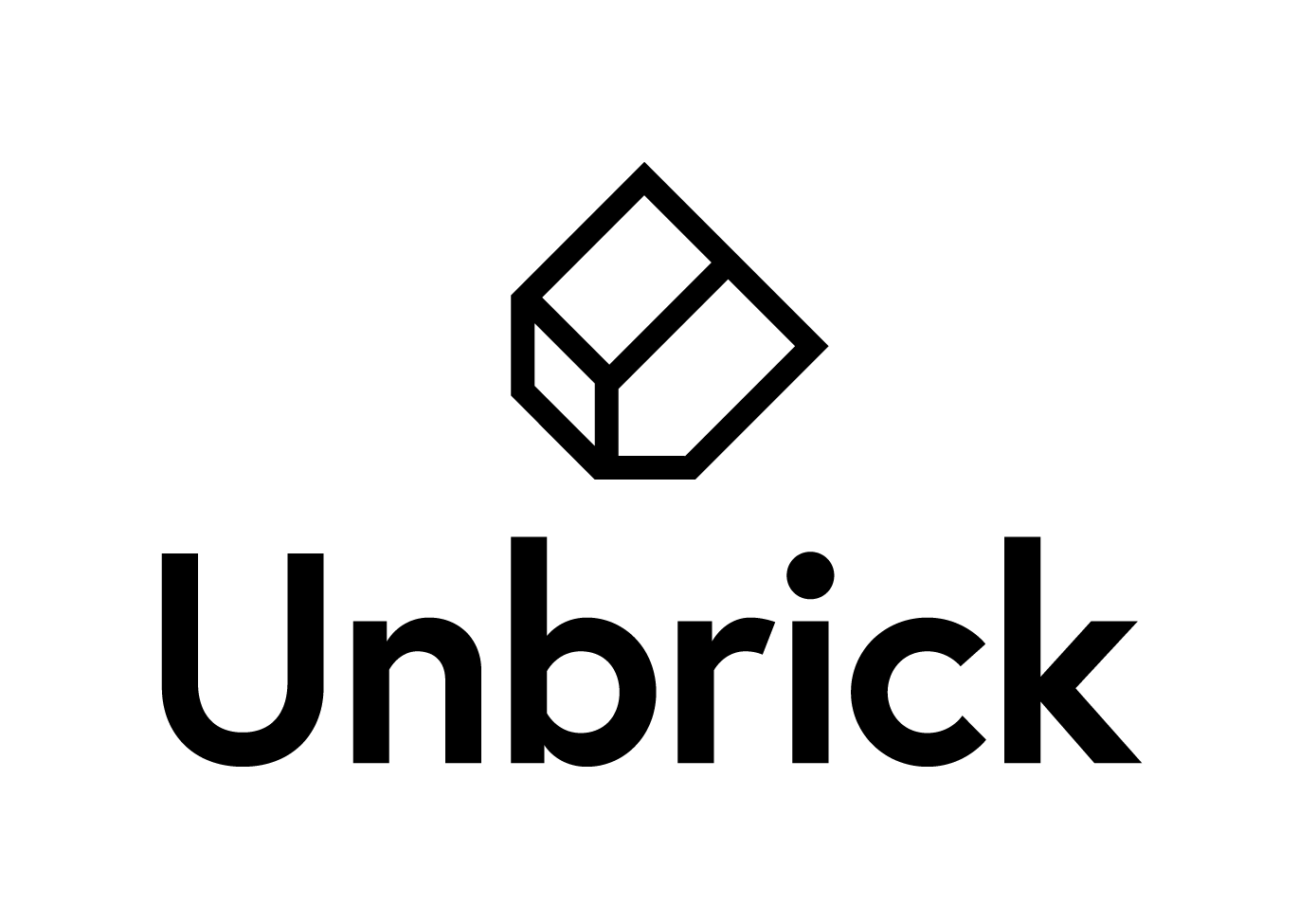
Focus on Unbrick
Netherlands-based company Unbrick is revolutionizing the Dutch housing market by challenging the traditional materials, processes and culture that have historically been adopted by construction firms. Its modular approach enables the company to create the various components of its highly sustainable homes that are manufactured at its production facilities in just three days. The modules are then assembled on site in as little as five hours.
For more information: https://www.unbrick.nl
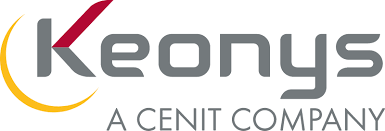
Focus on KEONYS NL BV
Headquartered in Paris, and with local offices in multiple locations including the Netherlands, KEONYS is a value-added reseller of Dassault Systèmes solutions including CATIA, DELMIA, ENOVIA, SIMULIA, 3DVIA and the 3DEXPERIENCE platform. Committed to supporting the implementation of solutions that best meet its customers’ needs, KEONYS provides comprehensive consultancy services and can assist with all training requirements.