ROBOT AT WORK
Using virtual experience twins on the 3DEXPERIENCE platform on cloud, Robot at Work was able to improve its production lines’ setups and accurately estimate production capacity.
Optimizing robots in a virtual world
Imagine if you could set up your production line in such a way that it required fewer resources while still achieving maximum output. Also imagine you could test everything in a virtual plant, running limitless scenarios to check the design before committing to building or reconfiguring the physical production line or cell. Since embracing virtual twin experience technology, that’s exactly what Robot at Work now enables its industrial customers to do.
The Italian production line solutions specialist, which has been in business since 2017, started out selling and integrating Cobots – the robot arm that works alongside people in a production setting carrying out tasks such as circuit board assembly, metal processing, packaging, and loading and unloading. Robot at Work’s customers soon began asking the company to solve more complex production solutions with standard robots. Seeing how major manufacturers in the automotive industry were embracing virtual commissioning, Robot at Work wanted to do the same.
“We saw in the last few years that the main automotive manufacturers had gone in the direction of virtual commissioning for welding lines and so on,” said Alessandro Tecchia, commercial manager at Robot at Work. “We knew that if we could test robots’ capabilities, evaluate their functionality and identify issues and improvements based on virtual models, we could meet all our customers’ automation needs. Eventually, we think all integrators will be forced by the market to move in this direction.”
Robot at Work’s new virtual commissioning approach is powered by DELMIA on the 3DEXPERIENCE platform. Before, the company used to determine its customers’ production requirements and design and validate a robotic solution in a 2D layout. It was only when the entire cell was built in real life that it could test the solution and identify any issues.
“We knew there was a better way,” Tecchia said. “We explored the possibility of solving these kinds of problems in the virtual world and found that the 3DEXPERIENCE platform and its application DELMIA delivered all the functionality we needed. Now, we are bringing solutions to the customer much faster as we can fully define the robotic cell before it’s built.”
Today, virtual commissioning allows Robot at Work to meet its customers’ increasingly complex requirements more easily and help them run their manufacturing operations more efficiently.
“We recently had the opportunity to simulate a plant with more than 12 cells,” Tecchia said. “The customer wanted to introduce automated guided vehicles for logistics, and we showed them that they only needed three-quarters of the space on the shop floor that they had planned for. They can now create their parts in a more compact space and run far more efficiently.”
The company is winning more new business too.
“Because we have completely changed our way of making offers to customers, we now stand out from other standard integrators on the market,” said Lorenzo Codini, administrator at Robot at Work. “Our customers can now see a complete simulation of their production line upfront before they commit to the full investment of setting it up physically. In Italy, there aren’t many companies that work in this way. It’s revolutionized how we handle new projects.”
Our customers can now see a complete simulation of their production line upfront and know exactly how their investment will pay off. It’s bringing us much closer to our customers.
Complete solution on the cloud
The Robot at Work team evaluated several virtual commissioning solutions before choosing the 3DEXPERIENCE platform, including DELMIA.
“We were searching for one piece of software that covered all of our virtual commissioning requirements,” Codini said. “We were already users of Dassault Systemes’ SOLIDWORKS software in our design office, so when our IT partner Nuovamacut presented DELMIA on the platform to us, it made perfect sense.”
Robot at Work was impressed by DELMIA’s sophisticated robotics features, which enable it to program robots in the context of a specific production line and simulate in depth the behavior of all the robotics. It was also keen to use a cloud-based solution.
“We appreciated the fact that the solution could be deployed in the cloud,” Tecchia said. “We are not a large company, so we don’t have a huge IT infrastructure. For us, then, the cloud was a real benefit. It meant we’d be able to get up and running on the solution without a significant upfront investment. We also liked the fact we’d get updates automatically, so would always be working with the latest version of the software. When we visit a customer site, we simply take a laptop with us and easily access the 3DEXPERIENCE platform from wherever we are. There’s no need to carry hard disks around with us anymore.”
With assistance from the Nuovamacut team, Robot at Work was up and running on DELMIA in a matter of a couple of months.
“The Nuovamacut team worked closely with us to make the rollout a success,” Codini said. “It was a really fast process, and the support was great. Nuovamacut set up a training program that would get us up to speed and it’s enabled us to use DELMIA independently. We always know they’re there to support us. So, when we get a new request from customers for simulations that are different from our standard, we know they have the expertise to help us out.”
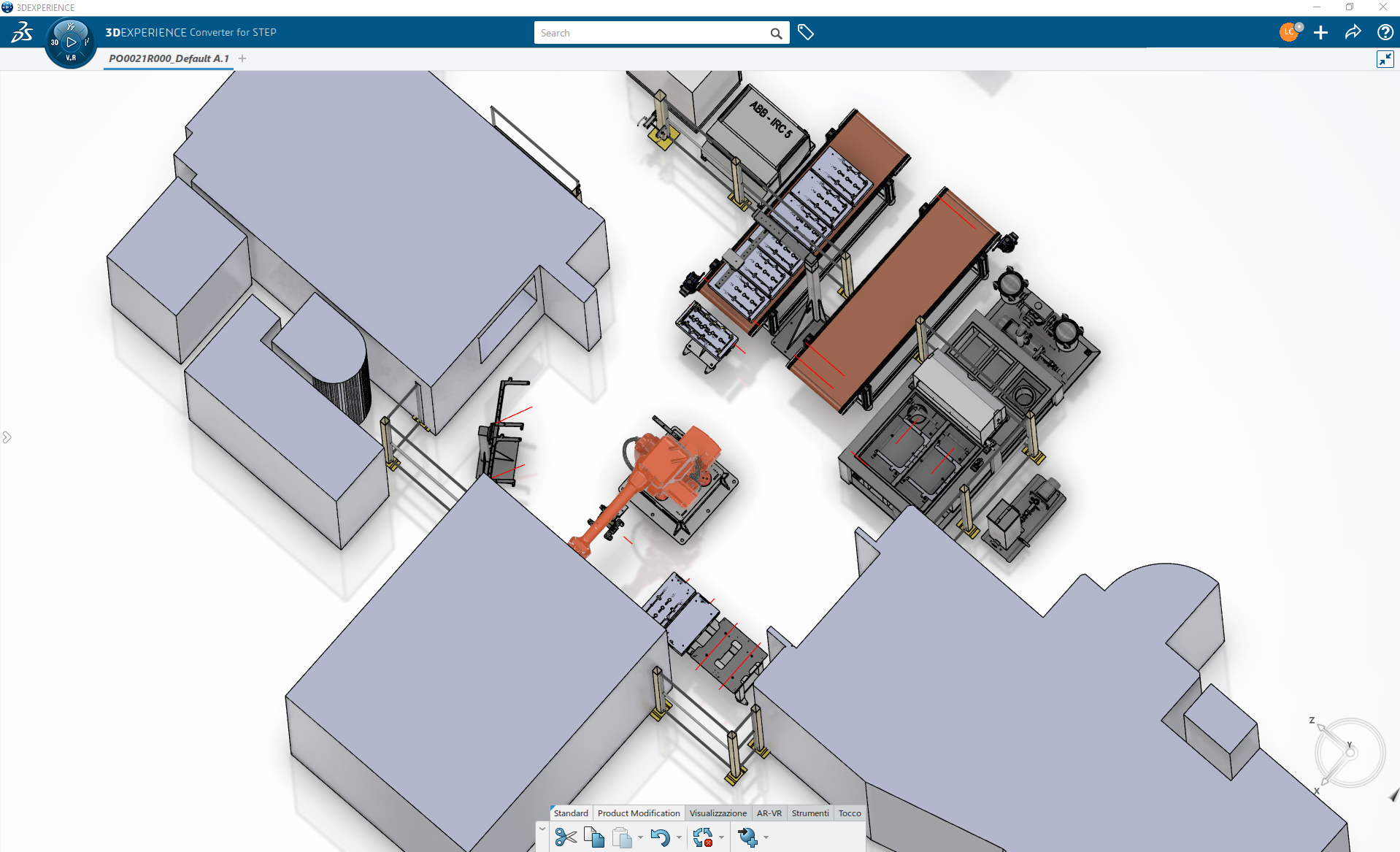
Solving complexity through simulation
In the time since it has been in business, Robot at Work has seen its manufacturing customers’ demands grow as they come under increasing pressure themselves to be more flexible, create products at lower cost, accelerate time to market and maintain the highest levels of quality.
“It was becoming harder for us to meet all their requirements,” Tecchia said. “The customer would come to us with a specific request, but there was not always an obvious solution. They also wanted to see how a robotic cell would operate within the context of the complete shop floor operation. Simulation has answered those issues. Already, we’ve used our virtual commissioning approach with many of our automotive customers and it’s helped to solve their production line requests.”
One area where this has made a big difference is in the way Robot at Work now programs robot application and PLC, written code that controls certain machinery in the manufacturing process.
“We do a lot of robots and PLC for our automotive customers,” Codini added. “Now, we can evaluate the automated solution through simulation and demonstrate exactly how the robots and PLC process will dictate the movement of factory tools and machinery ahead of building it. This wasn’t possible before.”
We are now selling complete logistics solutions on DELMIA, and we’ve seen revenue in our robotics business line double in the last year alone.
Choosing the right robots
Because Robot at Work has the capabilities to define each production line solution at the greatest level of detail, it is able to determine which robots are best suited for which tasks and combine several different functions into one cell. At the same, its customers avoid the costs, delays and mistakes that come from a traditional approach of physically installing a new line and trying to debug and optimize it on the shop floor.
“Using DELMIA, we can simulate in depth the behavior of all the robotics,” Codini said. “The advantage is that we can use all the leading robot brands, program them, move and change the mechanical parts and then swap robots all within the same application. It allows us to easily integrate many brands of robot and compare them all to check which will be the best ones for the customer’s needs. We then see exactly how they will fit in the customer’s setting. We can also use DELMIA to test existing robots on which we’re going to make modifications.”
With this approach, Robot at Work can come up with the optimal solution for each of its customers’ requirements and help them save costs.
“One example is an automotive customer,” Tecchia said. “They have an assembly unit with a vision control system for checking quality. Before, they needed five cameras to monitor the line. We virtually designed a new robotic set up which meant that the same part could be monitored just as well using one camera. In our simulation, we could show the robot assembling the part, and the single camera tracking all the activity, all without impacting quality. They have taken this setup into other production lines and it has saved them a lot of money.”
Maximizing output
One of the main requests Robot at Work must deal with is helping its customers to maximize output.
“Output is the first piece of data that the customer wants to see,” Tecchia said. “In the past, we could only estimate cycle times based on our calculations and experience. Sometimes this led to errors in the final output as we couldn’t plan for every scenario. With simulation, we’re far more accurate. We can show the customer how the robots will perform in the virtual world and the results end up being very close to the reality of physical production. There are no more surprises.”
The virtual experience twin also can simulate a system while it is operational. This allows Robot at Work and its manufacturing customers to monitor the system, create models for adjustments and automatically make changes to the system to ensure it’s running at maximum efficiency.
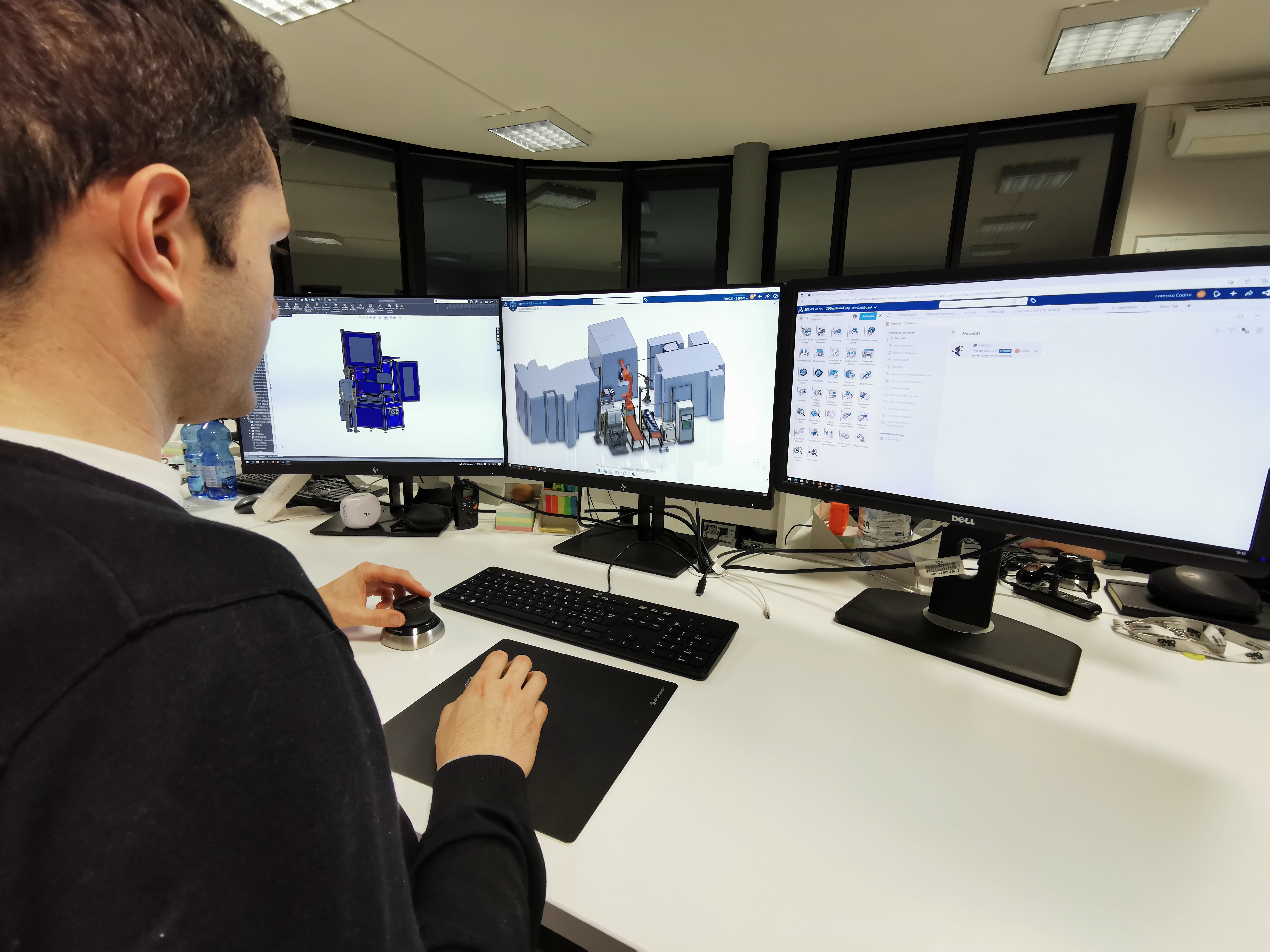
A new service business model
For Robot at Work, its transition to virtual commissioning has been nothing short of transformational, both for how it meets its customers initial requirements and then continues to serve them once a production solution is fully up and running.
“One of the biggest impacts has been in our aftersales offering,” Codini said. “Many of customers change production two to three times a month, and they need help from us to modify programs. The platform and DELMIA helps by speeding up how quickly we can get a new cell up and running. If a customer wants to change production or a robot cycle, we can simulate it ahead of time, show them it works and then make the switch with the minimal amount of downtime. We can get a new production cycle up and running within a day.”
Robot at Work’s business has really taken off since it embraced the 3DEXPERIENCE platform.
“We are now selling complete logistics solutions on DELMIA, and we’ve seen revenue in our robotics business line double in the last year alone,” Tecchia said. “Looking ahead, we’re expecting even bigger growth and the platform is really driving this.”
It’s given us a completely different way of working,” Codini added. “Our customers rely on us and trust in our know-how. They can now see that we’re delivering the best solution before they have to commit to building it. They know exactly how their investment will pay off. It’s bringing us much closer to our customers.”
Discover more about the Digital Equipment Continuity industry solution experience.
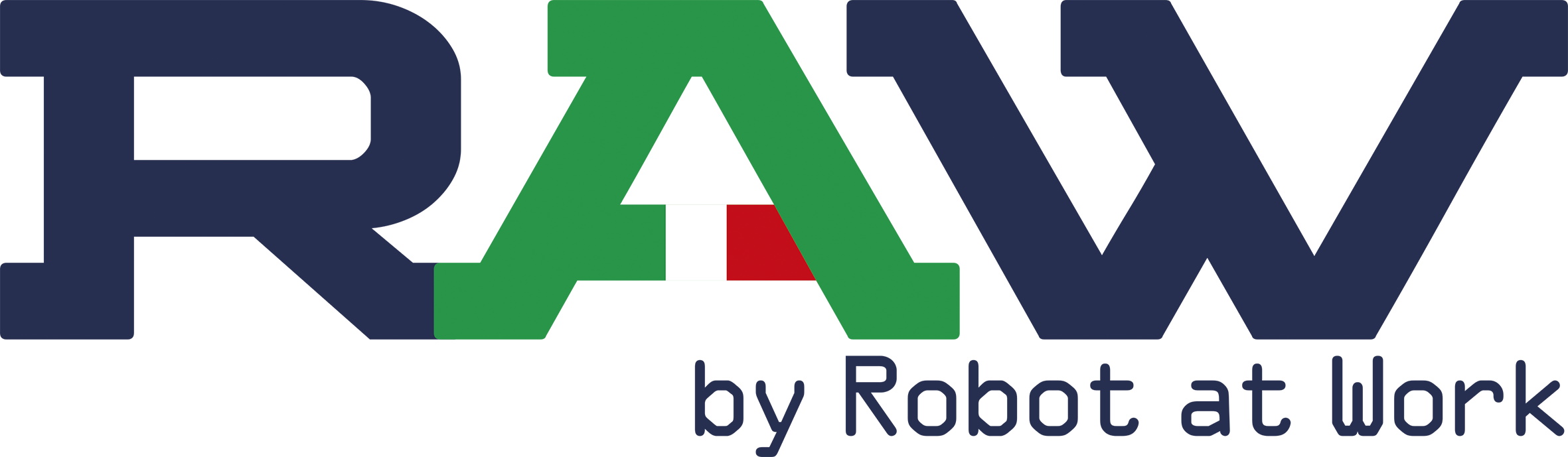
Focus on Robot at Work
Robot at Work was born in Rovato as an innovative startup, starting from the distribution of collaborative robotics. Its aim was to provide these innovative cobots to integrators, end users, research and development centers, and educational institutions.
The company has continued to evolve by adding traditional industrial robotics to its business and today invests in skills and resources to use both virtual twin and virtual commissioning as main internal design tools.
For more information: www.robotatwork.it
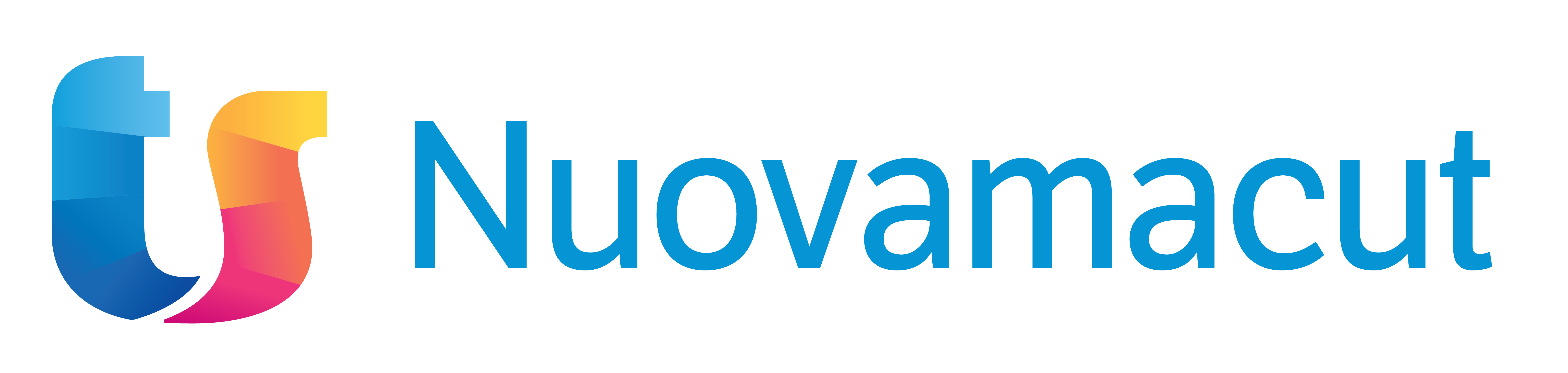
Focus on Nuovamacut
Nuovamacut is an Italian company and Dassault Systèmes partner with strong expertise in CAD, CAM, CAE and PLM. The company is active across Italy, supporting customers of all sizes and complexities, operating in different sectors ranging from the mechanical industry, design, and construction of molds, consumer goods, and technological equipment to aerospace, transport, planning, and design services.