ITER
Founded by seven member states, the ITER project brings together 35 nations to build the world’s largest fusion device, and demonstrate the scientific and technical feasibility of fusion power as a large scale energy source. ITER adopted the 3DEXPERIENCE platform to manage the plant's entire lifecycle and gain a single source of truth for every stage of the project.
Putting the sun in a box
Turning fusion power into a new source of energy for humanity: this is the raison d’être of ITER (International Thermonuclear Experimental Reactor), the largest nuclear fusion research project in the world. Its aim is to demonstrate that it is possible to build a thermonuclear power plant capable of producing energy in a safe, sustainable and environmentally friendly manner.
Since 2005, ITER’s members – China, the European Union, India, Japan, Korea, Russia and the United States – have committed to a 35-year collaboration to build and operate the ITER experimental device.
Based in the south of France, ITER involves 35 nations collaborating to build the most advanced and largest tokamak magnetic confinement fusion experiment. When complete, it will be twice the size of the largest machines currently in operation, with ten times the plasma chamber volume, and demonstrate that fusion power can be generated on a commercial scale.
Countries around the world have committed to Net Zero emissions by 2050 as part of the UN Race to Zero campaign and recognize that they must decarbonize their energy sectors if they are to succeed. Global leaders are backing this initiative as nuclear fusion holds the potential of generating colossal amounts of power that is low carbon, safer and produces much smaller amounts of waste. Compared to the chemical reaction from burning coal, oil or gas, nuclear fusion releases nearly four million times more energy, and four times more than nuclear fission.
What we have at ITER with the 3DEXPERIENCE platform is state-of-the-art.
One of the world's greatest engineering feats
Thousands of people are working towards the project’s success, building millions of components, some of which weigh several hundred metric tons. Factories around the world ship them to France to be assembled into the giant reactor. It is one of the most complex engineering endeavors in history.
“Constructing the machine piece by piece will be like assembling a 3D puzzle on an intricate timeline,” said Bernard Bigot, director-general of ITER. “Every aspect of project management, systems engineering, risk management and logistics of the machine assembly must perform together with the precision of a Swiss watch.”
For such a project spanning decades, ITER needed an industry-leading technology platform to help it orchestrate all the global participants; achieve scalable, multi-site, secure collaboration; define common design and engineering processes; effectively manage the technical configuration and ensure compliance with nuclear standards. It found the answer in Dassault Systèmes’ 3DEXPERIENCE® platform.
From the very beginning, ITER has used CATIA to design the tokamak. Since then, as part of its product lifecycle management (PLM) project, it has expanded the scope of applications it uses from Dassault Systèmes within the 3DEXPERIENCE platform to include ENOVIA for collaboration, DELMIA for process analysis and most recently EXALEAD for indexing and intuitively accessing data.
“We are managing a huge amount of data,” said Jean-Pierre Mailharrancin, configuration system coordinator and PLM project manager at ITER. “One of the major issues we faced before was that we were using many tools that weren’t accessible to all. We wanted to reduce their quantity and bring consistency to our organization. To do so, we needed to put in place a central database to bring together all stakeholders within ITER, store and access accurate data, and gain a single version of the truth. With the 3DEXPERIENCE platform, we can now connect everything together, so that all users access, share and gain insights from all the data.”
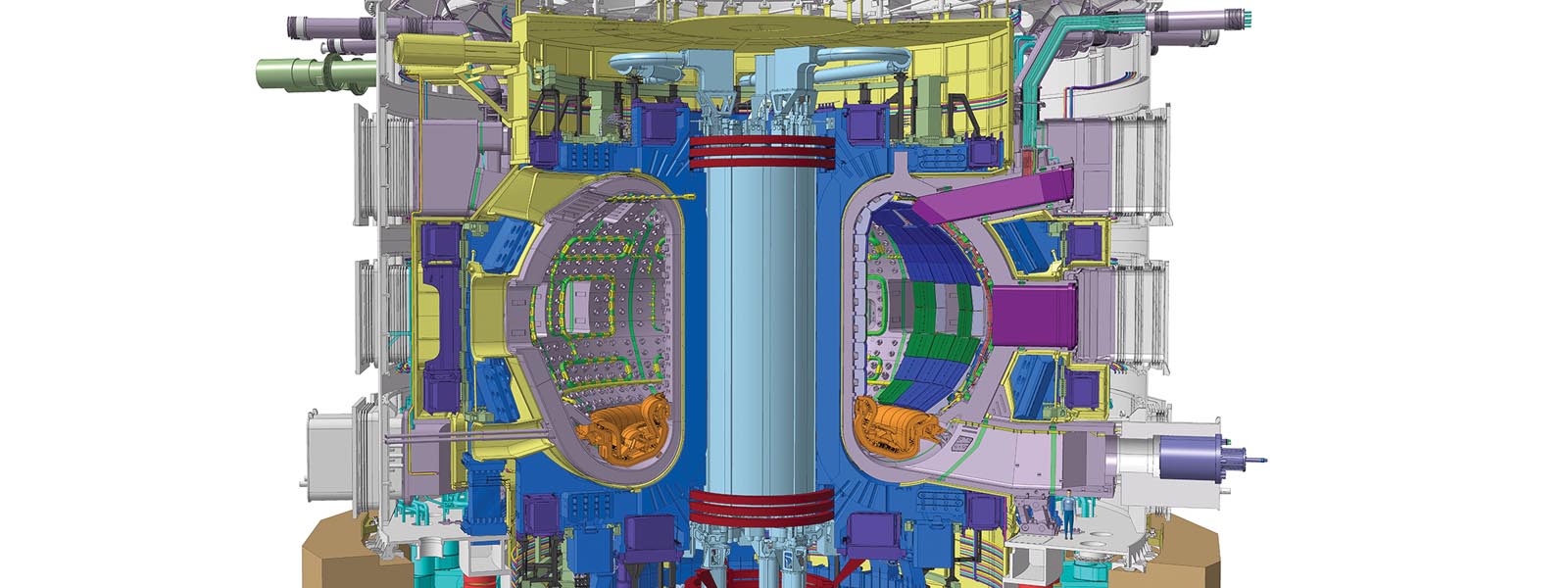
Slicing the elephant
For Hans-Henrich Altfeld, head of the Project Control Office and sponsor of the PLM implementation project at ITER, the 3DEXPERIENCE platform is helping the organization tackle the enormous complexity that comes with an operation of this scope and scale, and gain transparency of each project breakdown. “This project is characterized by two dimensions – enormous complexity and a long duration,” Altfeld said.
“This presents a number of challenges that include the knowhow generated as the project progresses, and allowing people who join the project later to dig into that information. Preserving our knowledge is critical.
“In terms of structural complexity, ITER is comparable to building the international space station, yet it has even more member complexity of this project, contending with the sheer number of people, components and suppliers involved but also the amount of changes that occur. In a first-of-a-kind project like ITER, there’s a lot of learning going on.”
To gain control, ITER is reducing complexity by breaking the project down into smaller parts and connecting them all via a continuous digital thread on the 3DEXPERIENCE platform. By having a complete view of all data surrounding each component, ITER is able to ensure stringent quality control as the machine progresses through the assembly stage of the project.
“The terms ‘complex project’ have the connotation that the project is not under control,” Altfeld said. “Instead, we want to make it complicated, which is still challenging but manageable. That’s why we have to slice the elephant and break the machine down into hundreds of thousands of parts, and manage each individual element. Of course, you need to ensure that the interfaces between each of these breakdown structures integrate seamlessly, and are properly managed. That’s what the 3DEXPERIENCE platform enables.”
All requirements from regulators and authorities are identified in our baseline and managed in the platform.
Meeting global standards
One of the main drivers for implementing the 3DEXPERIENCE platform was to improve ITER’s configuration management processes to bridge the gap between design and engineering.
“We need a system that enables us to implement proper configuration management processes, based on international standards,” Altfeld said.
With hundreds of thousands of documents, all part of the tokamak technical description, it was crucial for ITER to have a robust system running in the background to help manage and keep track of everything.
“The 3DEXPERIENCE platform has allowed us to centrally define the configuration management and implement it so everyone at ITER can benefit from it,” Altfeld explained. “This is not just related to engineering documents, it’s also about ensuring all 3D models are included and fully linked to the engineering data. So, when you’re in the platform and click on a component in 3D, you can see all the relevant engineering data associated with it. “Since all data has been fully approved and authorized, you can be sure that it’s reliable.”
At the same time, the platform helps ITER achieve compliance with global government and environmental regulations, and ensure safer construction.
“All requirements from regulators and authorities are identified in our baseline and managed in the platform,” Mailharrancin said. “Our configuration management system ensures that all global regulations are included and implemented at every stage of the project.”
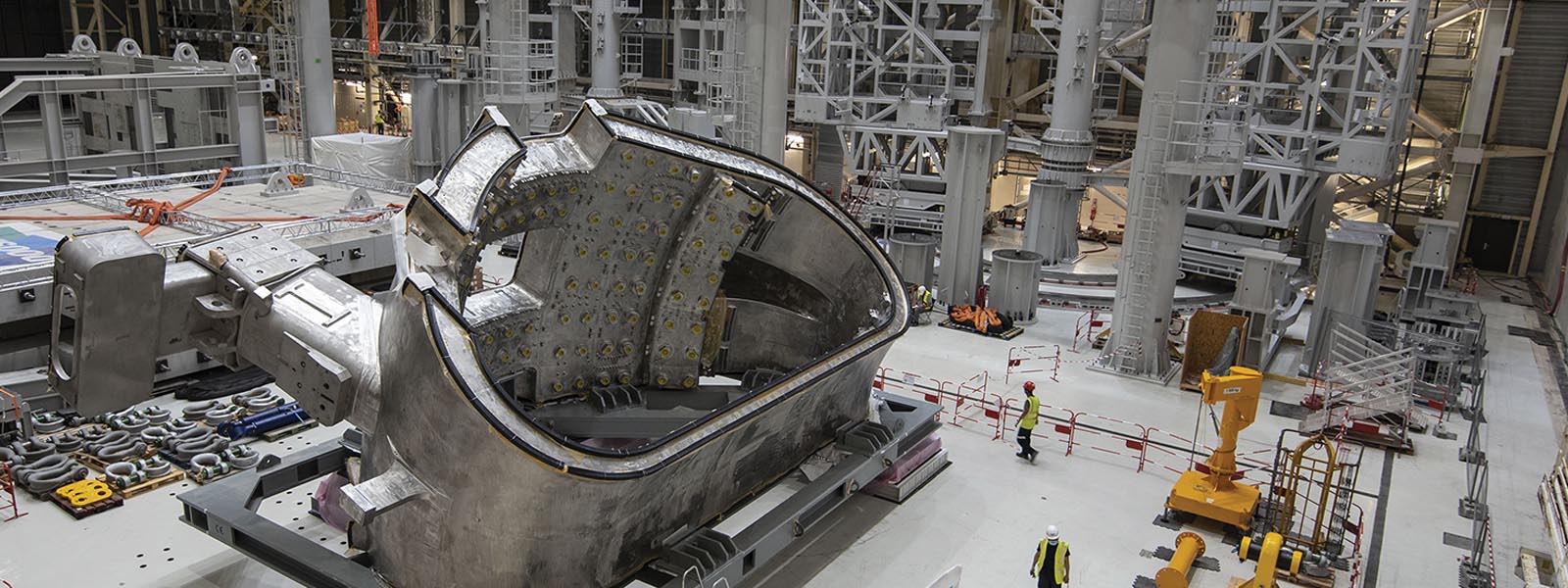
Piecing the 3D puzzle together
ITER uses the 3DEXPERIENCE platform to design all components in the tokamak, bringing together the work from all contributors globally and allowing them to share up-to-date digital mockups.
“We’ve designed in 3D from the beginning of the project,” Mailharrancin said. “All the designers and system engineers – more than 1,000 people – work together at the same time using the same application. We can then share 3D models and digital mockups all over the world for review and change.”
Critically, the platform helps to ensure that technical modifications are correctly implemented and all affected stakeholders are notified at each stage of the project.
“As part of change monitoring, the platform allows me to track all modification decisions and record the impact analysis made by the different domains,” said Vincent Clochard, product change request manager at ITER. “It also links the modifications to each part of the impacted design, whether it’s documents or data, and provides full traceability.”
The 3DEXPERIENCE platform serves as the collaboration environment for the ITER development community. Its program and project management functionalities are used in three main areas: to create a document production plan to implement the list of expected deliverables for the various activities (design, procurement, assembly, commissioning, and operation); to manage project change requests; and to send constructionrelated documents from the platform out to construction.
Then ITER simulates in 4D (3D + time) on the platform its most critical processes, ranging from the validation of the concept of the fusion reactor to construction, operation and maintenance. The solution serves as a process analysis platform and ITER uses its planning feature to optimize all the resources allocated to assembly and maintenance. At the same time, process-licing functions, including kinematics and robotics definition, allow a more in-depth analysis of critical processes and related equipment, using 3D models directly linked to the most recent digital version.
“We’ve done lots of assembly simulations,” Mailharrancin said. “The 3DEXPERIENCE platform has been invaluable for confirming that the components can be put together and that there is no physical clashing.”
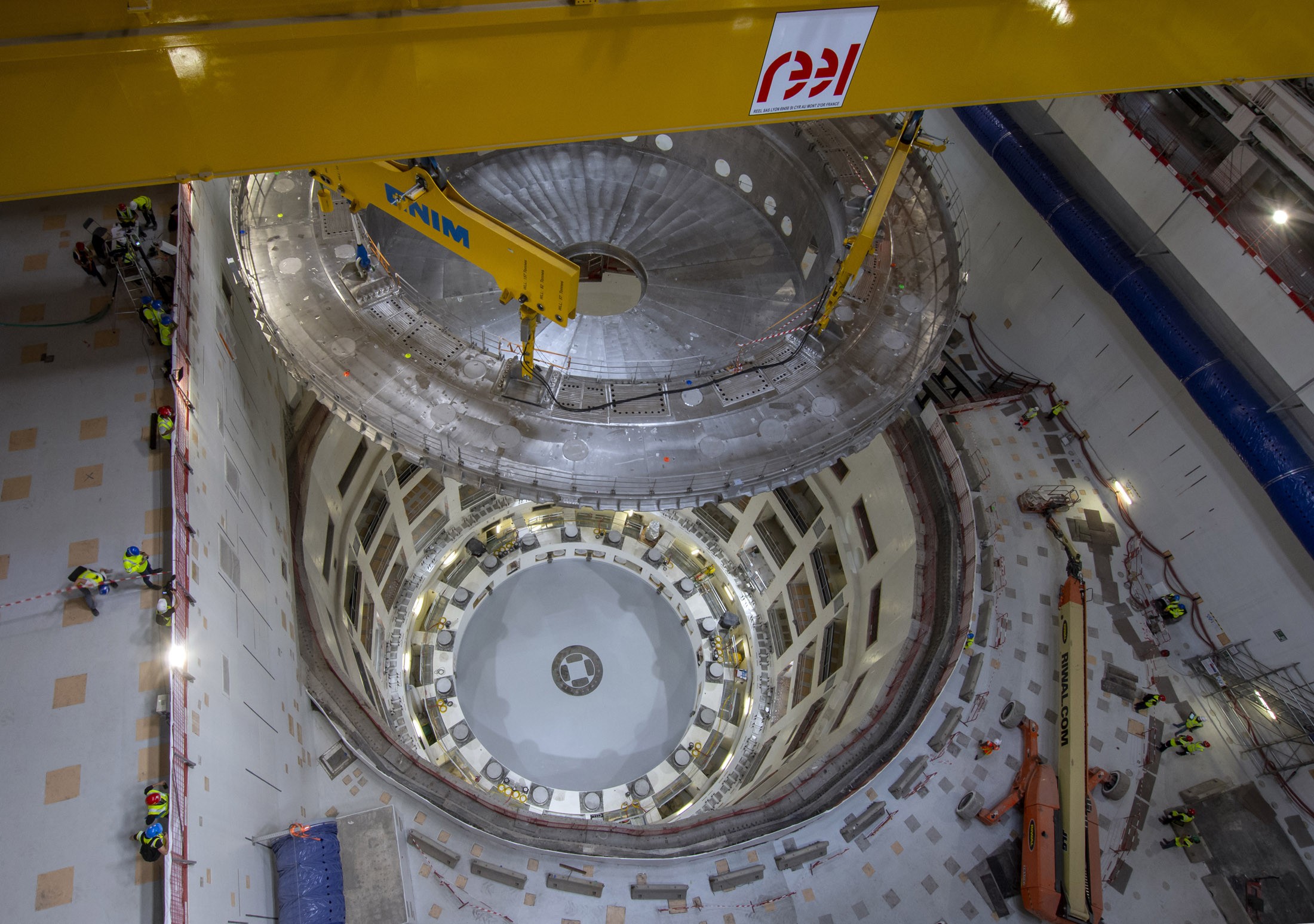
Assembly and beyond
ITER plans for all the core parts of the reactor to be installed, fully integrated and ready to produce first plasma by 2025. As the project progresses through the assembly stage and beyond, ITER needs controlled engineering information and reliable data to successfully complete each stage and hand over from one discipline to the next.
“With our current system, we have a fantastic basis to serve our clients [construction contractors, domestic agencies, operational clients, etc.] with robust engineering information,” Altfeld said. “Once the machine is built, we’ll have clients in commissioning doing the validation and testing. Then clients operating the machine will need maintenance manuals. And once all the research is done, the next client will carry out deactivation and safely dismantle the machine and bring the site back to nature. All these clients will need the technical information we’re currently generating. And they need to be sure in years to come that all this data is accurate and can support them in their role.”
“For me, the most important feature within the platform is the traceability it delivers,” added Adriana Rossi, technical document controller for ITER’s cooling water system. “With the way we’re storing information on the platform, you can easily get hold of any documentation and retrieve the information you need related to a specific engineering work package.”
Critically, the 3DEXPERIENCE platform allows ITER to take control of the entire lifecycle of the tokamak experiment and master the complexity of one of the greatest engineering feats to date.
“What we have at ITER with the 3DEXPERIENCE platform is state-of-the-art,” Altfeld said. “Some people believe that machines of this complexity can only be managed by specialists. However, they vastly underestimate the complexity created by the interdependence of all these thousands of experts and components that must come together. This is something the human brain cannot capture. We had to support a project like this with a powerful solution like the 3DEXPERIENCE platform.”
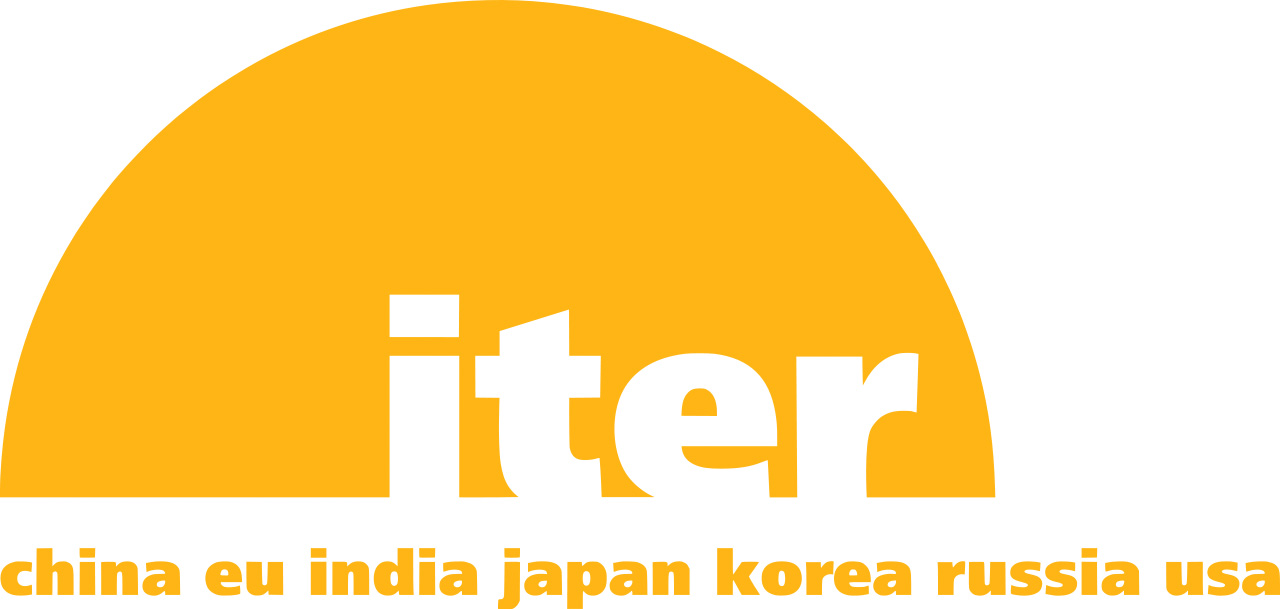
Focus on ITER
ITER is an international, large-scale scientific research project intended to prove the viability of nuclear fusion as an energy source, and to collect the data necessary for the design and subsequent operation of the first electricity-producing fusion power plant. Thirty-five nations have joined forces to build the ITER tokamak, the world’s largest fusion device, and share in every aspect of the project: science, procurement, financing, staffing and intellectual property.
The ITER project is based in Saint-Paul Lez Durance, in the south of France, where the fusion plant is under construction.
For more information: www.iter.org