Claas
CLAAS adopted Dassault Systèmes’ 3DEXPERIENCE platform and its Single Source for Speed industry solution experience. Engineers and designers at CLAAS sites around the world have access to a unique source of product information that enables collaboration, design reuse, digital simulation before manufacture and consequently less waste and production corrections.
Food for thought
Sustainable production is one of the key trends of the 4th Industrial Revolution*. With the world’s population expected to balloon from 7 billion today to 11 billion by the end of the century, sustainable food production is a growing priority among governments, scientists and business. “We need to double our food production by 2050 if we are to satisfy requirements on a global scale,” said Thomas Böck, executive board technology & systems at CLAAS group, a world leading agricultural equipment manufacturer whose combines, forage harvesters, balers and tractors are renowned for their technology and quality. (*1 Like its predecessors, the 4th Industrial Revolution is a transition to new manufacturing processes. It is characterized by social, “smart” and flexible production methods, including the use of new technologies to create goods that better match customer and consumer expectations.
“When you look at the last 20 to 30 years, technological advances in machinery were linked to size and horsepower,” Böck said. “Today the focus is more on intelligent, energy efficient machines that accomplish more while keeping operational costs to a minimum. It is these machines that have the preference of farmers who speak less about machine power or productivity and more about resource efficiency. They need to effectively harvest farmland and use water and energy resources as well as technology wisely to achieve more output - a greater harvest,” he said. “At CLAAS, we know that agricultural equipment is increasingly equipped with smart technology to be IOT-ready and manage working processes automatically increasing the efficiency throughout the whole production process.”
Know your customers and innovate
The 4th Industrial Revolution will significantly enhance the consumer experience and at CLAAS, innovation and technology go hand in hand with a perfect understanding of a customer’s needs. “That understanding along with our attention to service is why our customers turn to us,” Böck said. The company has a global staff of creative design teams whose objective is to bring new and more efficiency-related ideas into the design process. And to know at all times what customers want.
“One very important core activity at CLAAS is research and development,” Böck said. “We are not the largest manufacturer in the world so we must differentiate ourselves from our competitors through innovation and customer service. And to satisfy our customers, we must first know their needs. By involving customers we’ll receive instant feedback on new ideas and, more importantly, if they are relevant. This accelerates our development, which gives us the competitive advantage.”
The 3DEXPERIENCE platform not only helps us to master the data complexity but also supports the global collaboration massively.
Data complexity and interdisciplinary collaboration
CLAAS has development sites all over the world, that need to work together across borders. Additionally, the extensive CLAAS product offering means the company creates and manages significant amounts of complex data. To facilitate global collaboration and manage the increasing data complexity, CLAAS relies on Dassault Systèmes’ 3DEXPERIENCE® platform. “We’d like to bring new technologies and new business models to the market faster. And digital transformation is the enabler for that,” Böck said. “In addition, the digital transformation, embedded into our corporate strategy, is a key success factor for interdisciplinary collaboration and data management.”
“The 3DEXPERIENCE platform plays a key role for the digital transformation. It’s our strategic platform for everything we do in engineering and digitalization – starting from ideation to production and service,” said Nico Michels, head of digital product engineering at CLAAS. “As part of the digital transformation, all employees affected and involved in the process are included.”
“The 3DEXPERIENCE platform not only helps us to master the complexity but also supports the collaboration. We can collaborate on the same product or on the same object from any CLAAS site at the same time. And it’s not only in the engineering departments, but all downstream departments that are able to access a product or specific object simultaneously, if required,” Böck explained.
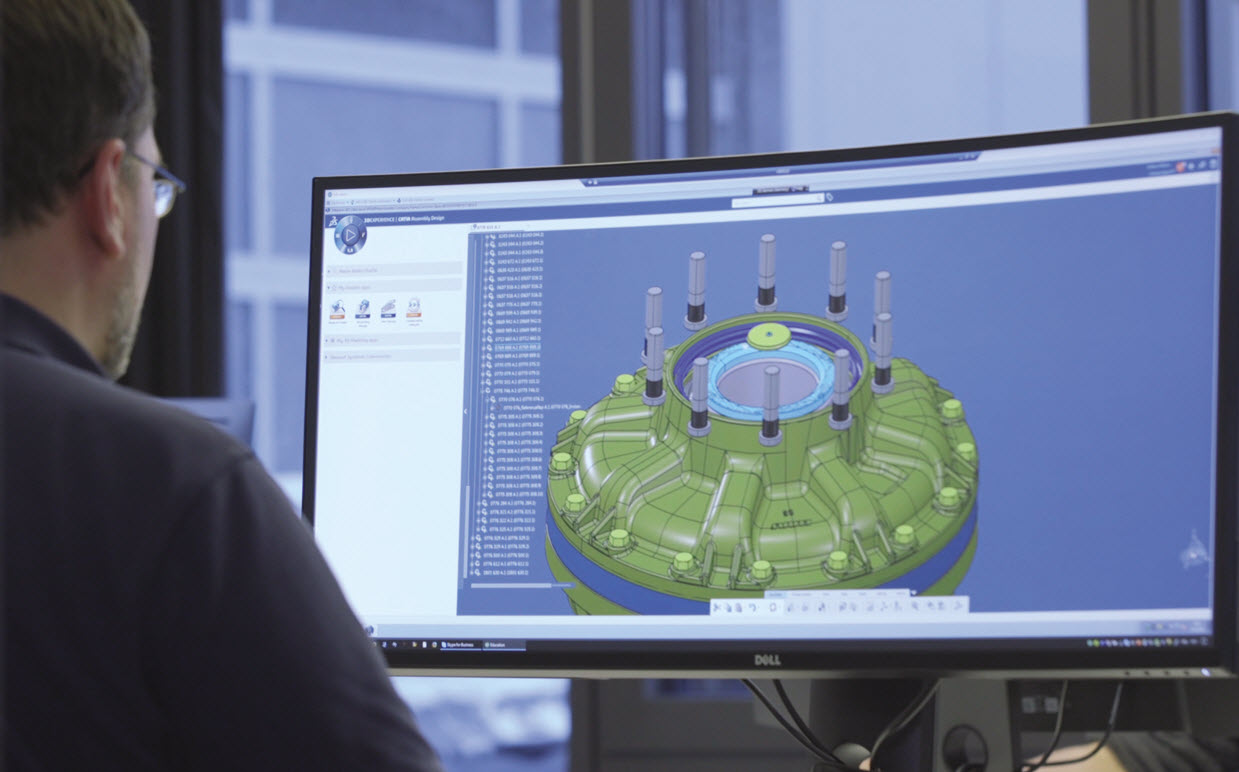
Design anywhere, produce anywhere
The leaders of the 4th Industrial Revolution think globally and act locally. CLAAS’ development and production sites around the world must develop machines according to company standards and practices. This requires consistent processes, sharing the same data, and exchanging ideas and expertise across borders in a secure manner.
“Global competition requires that manufacturers have the ability to design anywhere and produce anywhere. At CLAAS, we must prepare for the day when we will have different design and production locations around the world that manufacture our machines in a uniform manner. We adopted Dassault Systèmes’ 3DEXPERIENCE platform as a way to help with our international expansion by streamlining global collaboration between all our sites,” Bernhard Schuchert, CIO at CLAAS said.
“Designers worldwide have access to a unique data management system. They are authorized in the 3DEXPERIENCE platform according to the ‘need-to-know’ principle which protects our data against unauthorized access,” Michels said. “Product information is the same for everyone, which avoids errors that occur when the wrong design is used. Everyone has access to the integrated solution with the most recent designs that we only need to maintain once since there is no more duplication of information.” Bernhard Schuchert continued, “Designers in India and Germany can work on the same component because they all access a unique database.”
Tools for building intelligent machines
With the 3DEXPERIENCE platform, CLAAS has an environment in which designers can digitally store and test their designs before creating a prototype. “Building more intelligent machines is a collective effort of multiple disciplines that must work together and the sooner the better,” Böck said. “In the past, systems engineers would start installing their equipment after the mechanical design was completed,” Kai Wallasch, advanced PLM development said. “If problems arose, the redesign effort would sometimes escalate to prohibitive proportions in terms of planning and costs. With the 3DEXPERIENCE platform, mechanical, electrical, and hydraulics engineers have simultaneous access to the design and can work concurrently instead of in a sequential manner,” he said.
“Now, they voice their requirements early so that they are taken into account before the mechanical design is finalized. Adjustments are made on the fly in a digital environment. As a result, we have less waste and fewer errors during production since electronic and hydraulic systems are positioned early during structural design. With the 3DEXPERIENCE platform, space requirements are simulated and detected early; we know what the results will be before manufacture, which accelerates the final physical assembly. Moreover, by playing out operator movements or servicing scenarios we introduce ergonomics considerations in our designs, which are important for the machine operator and for maintenance personnel,” Wallasch said.
Machine lifecycles are long so it is important to upgrade equipment with new technology as it becomes available so that they continue to deliver the best value to farmers. “Electronics, software, processors, memory media – technologies generally have shorter lifecycles than our machines,” Böck said. “To make our machines future-proof we need to add new or upgrade current technology in existing machines, which will enable them to provide owners with sustainable added value for years to come. Since the design data for every machine we develop is stored and managed in the 3DEXPERIENCE platform, it is easy to access this information to add additional features over the machine’s lifecycle and to provide this to the customer without having to develop a new machine every time a new technology comes along. Our response is faster and our customers are happy because our solution is more cost-effective.”
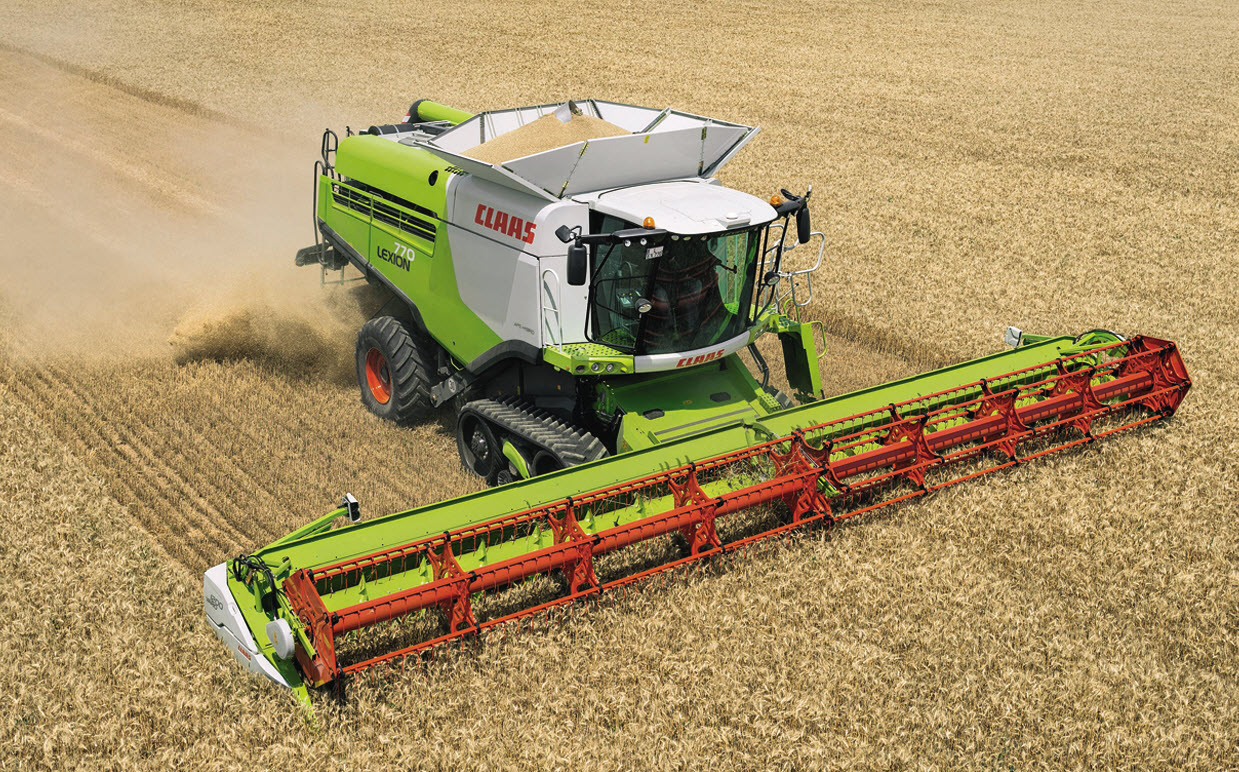
Future-ready
Digital transformation also means acquiring new knowledge, changing, re-defining, or even breaking up organizational structures. “As for our processes, we achieved major improvements because we had an opportunity to break old habits and rethink and reengineer old ways of working. With the 3DEXPERIENCE platform, we are set for the future”, said Michels.
According to Böck, being recognized for innovative products is good, but not enough for CLAAS. “We also have to be innovative in how we develop and manufacture our machines; innovative in our processes, systems and tools so that our response is up to par with the global challenges facing the agricultural industry. Agricultural technology is changing at fast pace. The digital transformation at CLAAS covers every step from development to sales and it links us as a manufacturer with development partners, software suppliers, research institutes and customers. It all begins with a common environment, a unique data reference and global access to this unique information source by all project stakeholders wherever they are in the world. 3DEXPERIENCE increases our productivity in research and development and helps us unite global talents on one unique platform to enable them to exchange knowhow and ideas. This helps us to release innovative products to market faster, which is important for our customers and for the development of our activity on an international scale.”
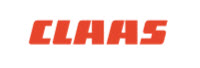
Focus on CLAAS
Leading agricultural equipment manufacturer.
Products: Combines, forage harvesters, balers and tractors, and field harvesting machinery.
Employees: 11,000
Revenue: € 3,84 billion in 2017
Headquarters: Harsewinkel, Germany
For more information www.claas-group.com