Beyond Aero
Creating the world’s first electric business aircraft designed for hydrogen propulsion, Beyond Aero built a new architecture to optimize the integration of the hydrogen tanks and fuel cell systems using the Reinvent the Sky industry solution experience. Combining design, simulation and model-based systems engineering (MBSE) within the 3DEXPERIENCE platform on the cloud accelerated development, helping to master complexity and maintain full traceability throughout the product lifecycle. Through a simplified virtual twin, Beyond Aero has successfully tested, validated and flown its 85kW scale propulsion system.
One step forward for hydrogen-electric propulsion
One winter’s morning at the Gap-Tallard airfield close to the French Alps, a proof-of-concept plane took to the skies for the very first time. In the cockpit was test pilot Paul Prudent, who successfully completed 10 take-offs including two full flights. The demonstrator, called Blériot, was equipped with an 85-kilowatt hydrogen-electric powertrain prototype developed by Beyond Aero – generating two-thirds of its power from a hydrogen fuel cell, with the remaining third coming from batteries. It was a major milestone for Beyond Aero, a French startup that is on course to launch One, the world’s first electric business aircraft designed for hydrogen propulsion.
“The climate challenge facing us is so huge that we must pursue a fossil-fuel free future, and one of the fastest ways to do that is by using electric propulsion,” said Jacques-Alexis Verrecchia, head of product at Beyond Aero. “However, the weight of batteries remains a barrier, so we looked for other ways to generate electricity and the one that makes sense for aviation is hydrogen. One promises to be cleaner, more cost effective to run and much quieter compared to traditional business aircraft.”
Paving the way for a new flying era, One is expected to be on the market by 2030 and will be capable of carrying up to eight people over 1,500 kilometers; its hydrogen powertrain unlocking a range that is seven times greater than what’s currently possible with lithium-ion batteries alone.
In many ways, Beyond Aero is operating in uncharted waters. Because of the complexities associated with storing hydrogen (particularly in terms of its low volumetric energy density and high pressure requirements), the startup is developing its hybrid energy distribution system from scratch as well as the aircraft architecture to accommodate it. To achieve all of this within its ambitious timeframe, Beyond Aero needed a powerful solution to efficiently handle each phase of the product development cycle, from design and testing to certification and manufacturing. The 3DEXPERIENCE® platform on the cloud proved the ideal solution.
Today, the 3DEXPERIENCE platform serves as our PLM backbone so that we can be sure that everyone is working on the same objects and all our tools talk to each other. And since everything is cloud based, we don’t have to manage an IT infrastructure internally. It’s much more efficient.
PLM backbone on the cloud
One of the biggest appeals of the 3DEXPERIENCE platform for the Beyond Aero team was the ability to centrally handle all its data within a cloud-based product lifecycle management (PLM) environment and securely access it from anywhere at any time. Having all 3D design models and workflows connected within the centralized platform will allow the company to maintain full traceability of the development of One and its innovative hydrogen powertrain from concept to manufacturing and beyond.
“I travel a lot and the fact that I can connect to cloud-based tools that are accessible from everywhere is one of the big reasons we chose the platform,” Verrecchia said. “Today, the 3DEXPERIENCE platform serves as our PLM backbone so that we can be sure that everyone is working on the same objects and all our tools talk to each other. And since everything is cloud based, we don’t have to manage an IT infrastructure internally. It’s much more efficient.”
Beyond Aero values the innate flexibility that comes with the cloud, particularly the ability to scale up and add new functions and features when required. This has proven invaluable when running simulations involving large data sets, consuming vast amounts of computing power.
“Doing all modeling, simulation and analysis on the cloud means we don’t have to manage high-performance computing clusters internally,” Verrecchia said. “We just pay for the computational power we use. It helps us be more agile as our company grows.”
As well as seeking powerful design, simulation and engineering capabilities, Beyond Aero also wanted to work with a technology vendor that was more than just a supplier; it needed a partner that could understand its industry-specific needs and support it with its roadmap.
“Dassault Systèmes and the 3DEXPERIENCE platform are renowned in the industry, so we knew it wasn’t a risk choosing the solution,” Verrecchia said. “However, one thing I liked was that they had a dedicated team for startups. We appreciate the direct contact. This, combined with the startup offer and cloud-based tools, was very appealing.”
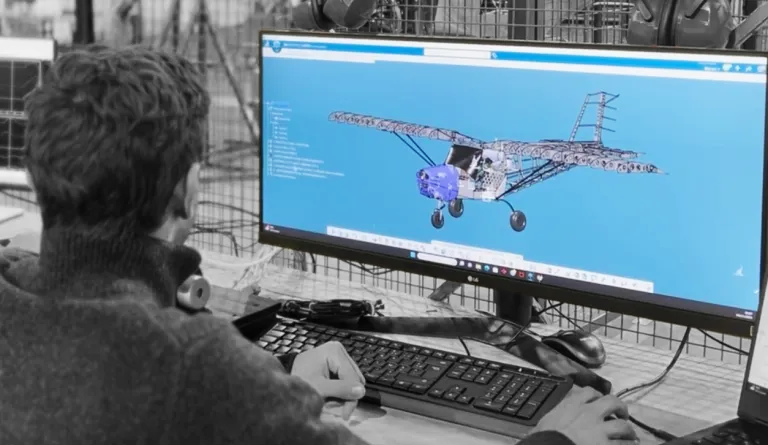
Reimagining the aircraft architecture for a hybrid powertrain
Before Beyond Aero built its hybrid prototype powertrain, it created the entire system virtually in the 3DEXPERIENCE platform on the cloud, using CATIA for 3D mechanical design. Being able to unify design and simulation on a single data model – referred to in the industry as a MODSIM approach – allows Beyond Aero to iterate and validate new designs fast.
“Our plan is to validate everything virtually on the subscale prototype to inform the next stages of development,” Verrecchia said. “With MODSIM, we can draw a 2D diagram of a tank or pipe, for example, connect it to the 3D model, test how it fits and functions, and then any design changes automatically update in the simulation. That seamless integration is saving significant time as we don’t have to go back and forth checking and duplicating changes. This also removes some of the constraints we’d might otherwise face if we tested everything in the real world.”
One’s architecture is being modeled around Beyond Aero’s proprietary propulsion system. Redesigning and optimizing the architecture to accommodate the hydrogen tanks and fuel cells is expected to improve aerodynamic efficiency by up to 30% compared to a retrofitted aircraft.
“With its low wing and sleek design, One looks like a conventional business jet,” Verrecchia said. “However, we’re starting from a clean sheet as the challenges raised by having hydrogen as a fuel are significant; it’s not simply a case of placing these cylindrical tanks in the aircraft. We must also integrate a thermal management system with a minimal effect on drag and we know we can achieve some performance gains by rethinking the design.”
Using the 3DEXPERIENCE platform’s virtual twin capabilities, Beyond Aero can keep track of all part designs and modifications, and validate subsystem integration before building the physical aircraft. Establishing full traceability between virtual and physical testing, and enhancing the use of MODSIM beyond mechanical engineering to electrical design and visual rendering will help to expedite its go-to-market strategy.
“The 3DEXPERIENCE platform will keep all information stored centrally and route the right information and approvals to the right people – everything will be linked to the 3D model,” Verrecchia said. “We are already benefiting from being able to work concurrently on the same parts and see the impact of any changes within the context of the wider assembly.”
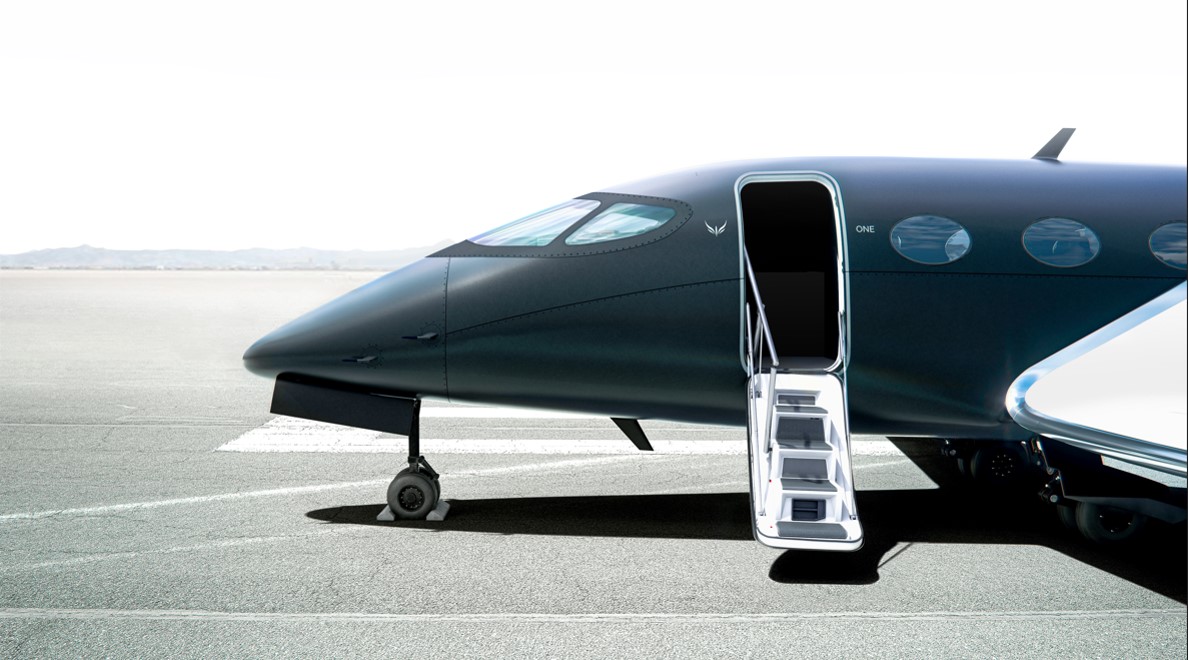
Getting One certified and launched to market
Following the successful test flight of its hydrogen-electric subscale powertrain, Beyond Aero is now moving fast to get One manufactured, certified and launched to market. From there, the company has set its sights on launching a commuter jet and potentially even larger commercial planes – where the carbon emissions challenge really lies.
“As we develop One, we’re building the knowledge required to create a larger hydrogen powered aircraft,” Verrecchia said. “Our focus is on scaling the architecture and capturing all our know-how within the 3DEXPERIENCE platform, which also serves as a reference for the certification process.”
Beyond Aero aims to explore more roles within the 3DEXPERIENCE platform, including Life Cycle Assessment, to track the environmental footprint of One throughout its lifecycle – from raw material sourcing to end-of-life.
“We’re looking forward to using these types of features to accurately quantify carbon emissions across the entire value chain, so that when we build an assembly line, for example, we can ensure it is as sustainable as possible,” Verrecchia said. “We want to be transparent about what we’re doing, and I hope this partnership with Dassault Systèmes will do just that as we help to redefine the future of flight.”
Discover more about the Reinvent The Sky industry solution experience.
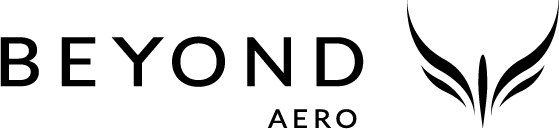
Focus on Beyond Aero
Beyond Aero is building the first electric business aircraft designed for hydrogen propulsion. Founded in December 2020, the French company is redesigning the architecture of a CS23 aircraft around the hydrogen-electric propulsion system, encompassing fuel cells, batteries, hydrogen tanks and a thermal management system. With offices in Toulouse and Los Angeles, the startup boasts a team of highly qualified engineers from leading aerospace companies.
For more information: https://www.beyond-aero.com