Technology Suppliers
Meeting the "Smaller, Better, Faster" challenge
What are the challenges faced by the Technology suppliers
Technological and environmental leaps are reshaping the industry, what are they and how will they affect your business?
- Bidding
- Requirements
- Project Management
- Usability
- Cyber Systems
- Complexity
- Simulation
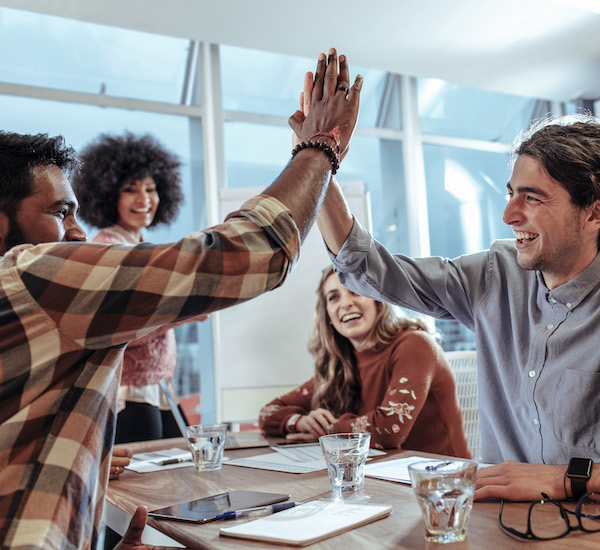
Bidding
Manual bid processes can lead to slower and less accurate opportunity assessment and higher risk bids. To ensure complex requirements can be met profitably while maximizing win ratios, bid processes should be standardized, automated and fully integrated with technical and business systems.
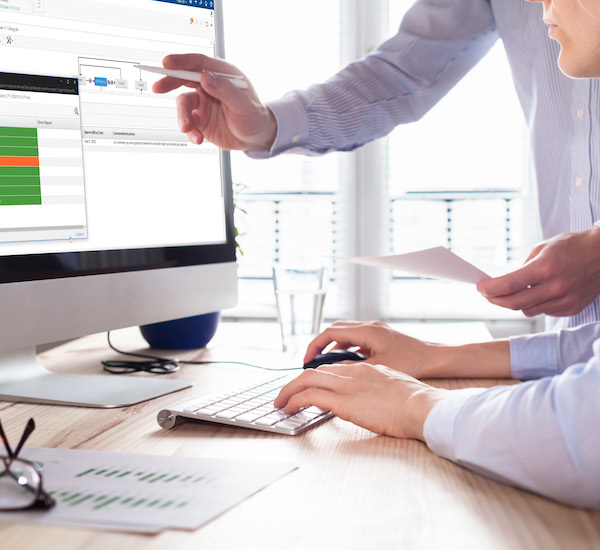
Requirements
Implementing a strong requirements management (RM) strategy can help make product complexity more manageable while minimizing time to market. Integrated RM systems can help you capture customer-centered requirements and distribute and enforce them across all design, engineering, testing and order fulfillment cycles. This reduces the number of potential issues and change orders, boosting quality while accelerating cycle times.
Only about half of an engineer’s time is being spent on value-added activities, on really focusing on, for example, innovation, engineering design.
Project Management
An automated project management process boosts quality and efficiency. Dynamic dashboards provide automated, real-time reporting on key schedule, milestone, resource and cost metrics to keep projects on schedule. Non-intrusive governance helps workers better adhere to schedules and enables managers to optimize resources and detect and address potential bottlenecks before they impact operations.
You don't want to paint yourself in the corner by putting in a system in the beginning that won't help you grow.
Usability
PLM has long been used by OEMs to improve essential product lifecycle processes. With latest technology advancements and best practices, now suppliers can leverage next generation PLM to better manage increased product and market complexity.
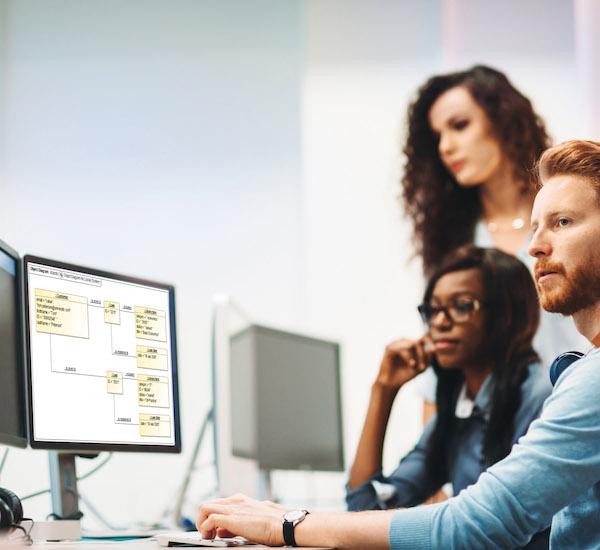
Cyber Systems
The increasing demand for electronics and software-driven functions are making tight collaboration between mechanical engineers, essential to market success. A common platform for all engineering disciplines helps overcome this challenge. The integration of mechanical and electronic design and validation workflows can boost part and design reuse and accelerate creating variants to serve complex and dynamic demands.
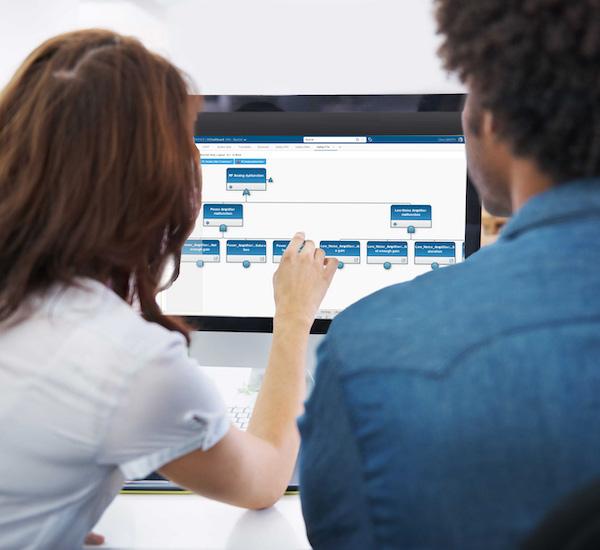
Complexity
Systems engineering helps develop complex systems with an optimal balance of performance, functionality and price. Model-based systems engineering fosters collaboration across disciplines. This collaboration increasingly extends beyond the boundaries of an organization. As OEM products grow in complexity, suppliers need to attend closely to the interfaces between their components and the larger systems in which they will be incorporated.
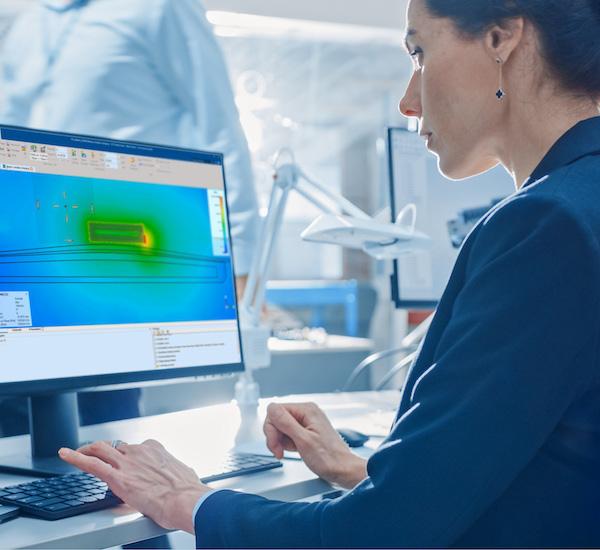
Simulation
Realistic simulation is essential for developing complex systems. It improves the ability of designers to understand and anticipate the behavior of their product in standalone form and as part of a larger system, helping them better manage trade-offs. When simulation is integrated throughout the entire development cycle, it can reduce costs and accelerate time to market as well - by minimizing the need for physical prototyping and testing.
Master the Future of High-Tech Manufacturing with Symbiotic Value Networks
Leveraging Virtual Twins to Synchronize Manufacturing and Engineering to Accelerate Delivering Competitive Connected Devices and Systems.
Discover our Customer Stories
Explore 3DEXPERIENCE
Learn more about how our Industry Solutions can help you achieve your professional ambition and business objectives