V-ZUG
V-ZUG chose Dassault Systèmes’ 3DEXPERIENCE platform to manage its product development process in one single environment and to ensure data consistency from specifications through to production.
FIRST-CLASS DESIGN AND PREMIUM “SWISSMADE” QUALITY
Swiss household appliance manufacturer V-ZUG is known for its innovative products. The family-owned company continues to set new standards in the industry since it was founded more than 100 years ago. Swiss art of engineering combined with passion give rise to high-quality household appliances combining design, function and aesthetics. “More than 4.5 million household appliances in Switzerland come from V-ZUG,” Ernst Dober, Head of Development and Services at V-ZUG, said. “This means that every other Swiss household uses one or more appliances from us, and that’s something that every employee at V-ZUG takes prides in.”
The company’s kitchen and laundry appliances are famous for their energy efficiency, reliability, longevity and userfriendliness. V-ZUG is an industry trailblazer with innovative inventions like its Vibration Absorbing System®, an active unbalanced load compensation system, which ensures that the washing machine does not vibrate during the spin cycle. This and other world exclusives and pioneering achievements have forged V-ZUG’s reputation as a leader in its domain.
V-ZUG believes that its household appliances should make life easier – whether you’re cooking dinner or washing dishes or clothes. “We provide our customers with more functionality than what is usually found in the industry,” Dober said. “At the same time, it is our priority to make our appliances easy to use. This is why we invented the ‘press and go’ feature, which automatically starts the desired program at the touch of a single button. We also provide recipes with our ovens and steam cookers in digital format, which can be used by anyone, even those without much cooking experience, to prepare delicious meals right the first time.”
QUALITY BREEDS TRUST
As a medium-sized company, V-ZUG is very flexible and close to its customers. “We cover the entire product lifecycle, from customer needs to product development and production all the way to after-sales services,” Dober said. “Our proximity to the customer enables us to receive, process and implement their requirements quickly.” The company, however, distinguishes between functions with real added value versus what it considers gimmicks. “Quality and reliability are more important to us than gimmicks. We focus on high-class and consistent design of our complete product range, for example a retractable handle that “magically” appears when the appliance is turned on. In the premium segment it is important to achieve the right balance between innovation, quality and cost,” Dober explained. This year, Swiss consumers have again nominated V-ZUG as the most trusted provider of household appliances because they value the company’s consistent and demanding pursuit of quality. “Trust is an important factor when people are buying domestic appliances and our customers value our high manufacturing quality,” Dober said.
A UNIFIED PLATFORM TO MANAGE COMPLEXITY
V-ZUG is increasingly expanding its activities abroad, for example in China and Australia. As customer and regulatory requirements increase, so do its product variants. V-ZUG has been a Dassault Systèmes’ customer for over 25 years, and transitioning to a robust unified platform like the 3DEXPERIENCE® platform to manage these growing product variants was a logical move.
“We replaced two legacy systems with the 3DEXPERIENCE platform because we were impressed by the fact that we could group PDM and CAD information in one environment and progressively add new functionality as our needs evolved, thanks to the flexibility of the platform,” Dober said. “The 3DEXPERIENCE platform is robust enough to manage all our product data in a sustained manner with project stakeholders simultaneously accessing information in real time. Moreover, we can track requirements from the earliest stages of development through to production, which helps to minimize development errors and to improve the quality of our products.”
With the 3DEXPERIENCE platform, we have created a foundation that prepares us for the future. The platform gives us the ability to map the requirements from the start of development to series production, and to manage the development of the appropriate specifications and models.
BUSINESS PARTNER RELATIONSHIP BASED ON TRUST
Dassault Systèmes partner Helbling IT Solutions conducted a business value assessment of V-ZUG’s principle processes, which illustrated the potential benefits of a unified IT environment. Helbling IT Solutions provided consulting services to V-ZUG to define the solution based on standard out-of-thebox (OOTB) processes and concluded the implementation of the system. “The standard features of the 3DEXPERIENCE platform are well-aligned with our needs. As a result, we have been able to limit customization to a minimum. This will help us minimize maintenance and future software update costs. Approximately 440 employees in construction, production and in management use the platform,” Dober said.
“Rolling out a PLM platform is a complex process and it’s important to have a good implementation partner and a relationship of mutual trust,” Blaise Metzker, Head of CAD/ CAM at V-ZUG added. “We have a long-standing partnership with Helbling IT Solutions. They are familiar with our development process and the way they’ve implemented the system is in line with how we work.
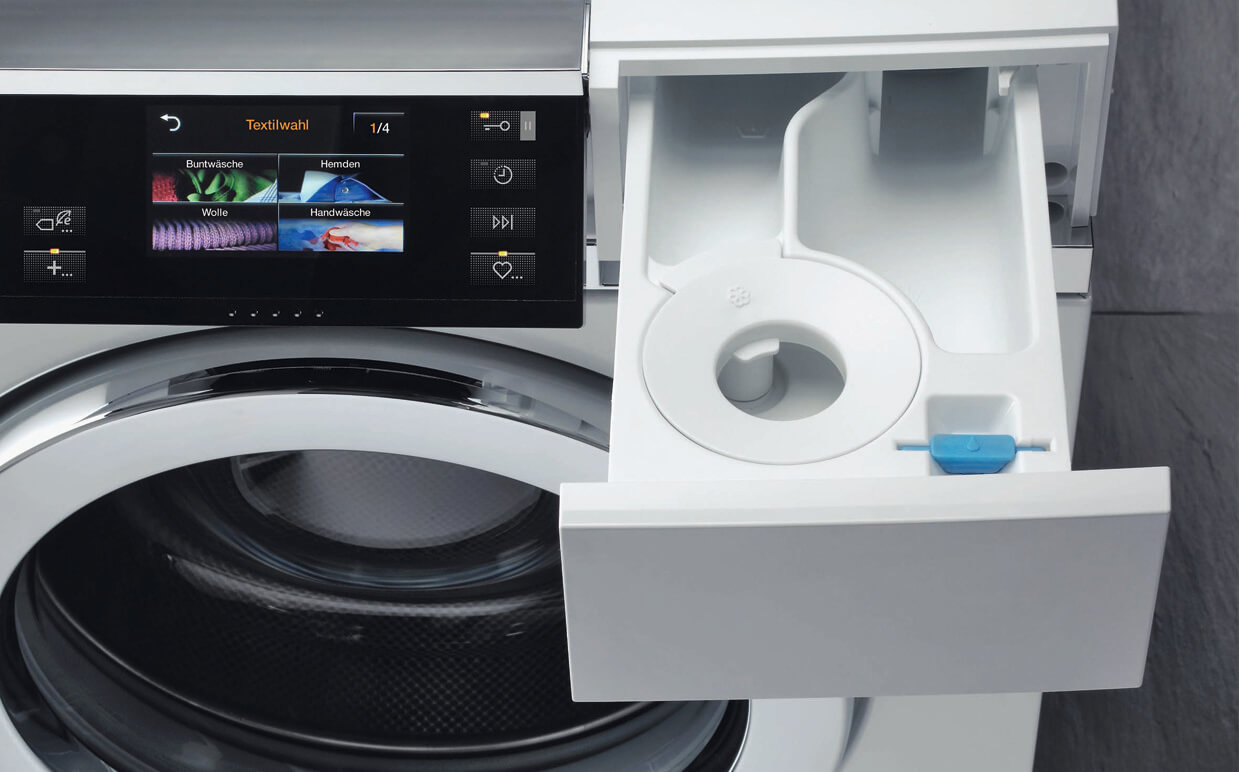
SMOOTH COLLABORATION AND DIGITAL CONTINUITY
“One of the 3DEXPERIENCE platform’s biggest advantages is that it provides an integrated solution for the different disciplines involved in product development,” Petra Peter, Mechanical Engineering Technician at V-ZUG said. “All product stakeholders - mechanical, electrical, software development - can collaborate on the most up-to-date version of a product’s data, which promotes a fluid exchange of ideas. This transparency also increases product quality,” Metzker added. “As a result, zero-defect design is definitely within our reach,” Peter continued. “The supplier integration is important for us. With the 3DEXPERIENCE platform we can provide suppliers that create parts for us with access via a secured Internet connection,” Metzker explained.
Peter explains that “designers begin by designing components and assemblies using the 3DEXPERIENCE platform’s authoring application CATIA. They then create the BOMs (bill of materials) of the different components that they manage with ENOVIA’s Engineering Central function. Data continuity in the 3DEXPERIENCE platform enables engineers to create a part in CATIA and to then synchronize it with ENOVIA’s Engineering Central. Once it’s in ENOVIA’s Engineering Central, we don’t have to re-create the part the next time. All product knowledge and its history is centrally located on the 3DEXPERIENCE platform and always available for re-use.“
Construction and design changes are also managed in the 3DEXPERIENCE platform using engineering change orders (ECOs). “As customers demand more diversity and our products become increasingly complex it is important to have powerful change-management capabilities to help us save time when implementing a change,” Metzker said. “All our components are available in the 3DEXPERIENCE platform. If we need to make a design change, like making the lock on an operating panel sturdier, we create the change request in ENOVIA and the design change is automatically passed on to all downstream processes within the company using ENOVIA’s change order feature,” Peter said. “In particular, we were able to reduce change management by reengineering our processes and the digital workflow by 50%,” Metzker added.
“We used 3DS Companion, Dassault Systemes’ e-learning platform, to support the training of our employees during the transition from CATIA V5 to CATIA V6,” Metzker explained. ”The 3DEXPERIENCE platform is user-friendly,” Peter said. “Even employees with no particular CAD training can use the 3DEXPERIENCE platform’s 3DLive application to consult the latest 3D designs. Navigating a product’s structure is easy and intuitive thanks to its tree-like display,” Peter added.
Even though product development and production are on the same site, proximity does not eliminate the need for clear production instructions. “We use CATIA Composer to create work instructions from the latest 3D model,” Metzker said. “By eliminating 2D assembly drawings, we save time and costs and end up with fewer assembly errors at the production stage.”
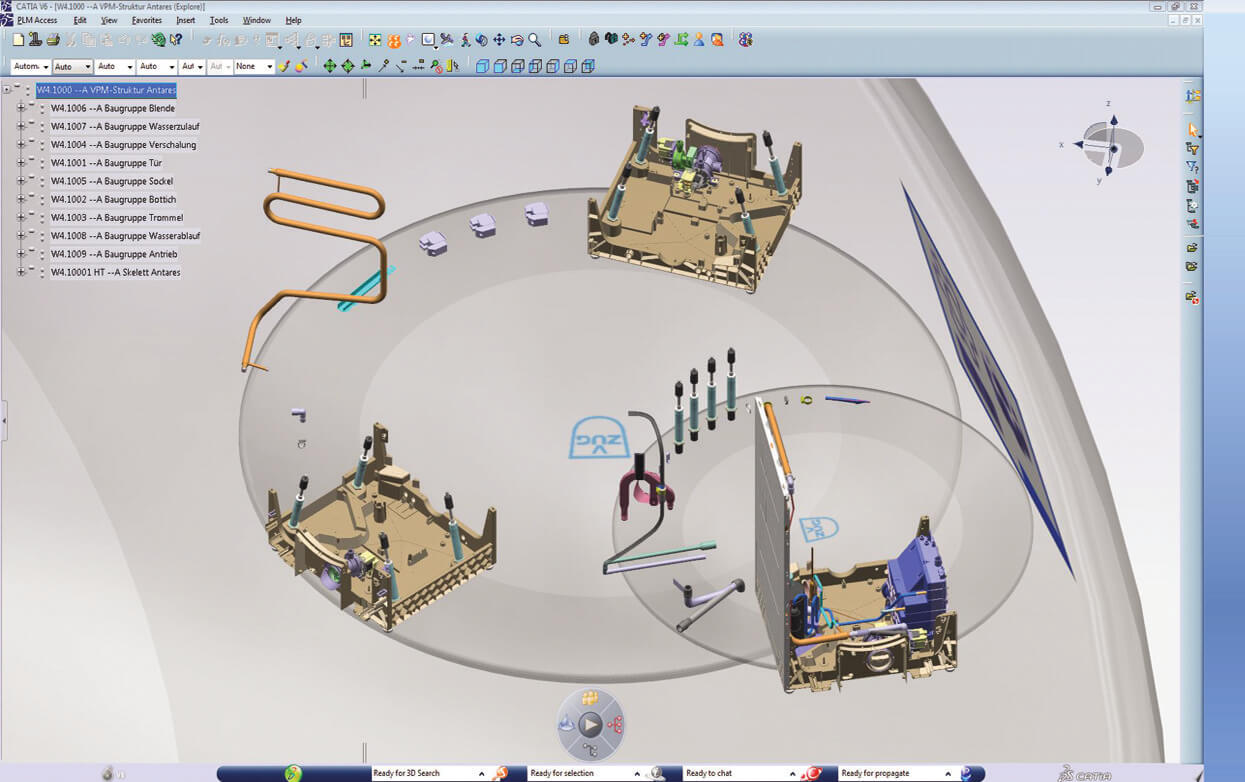
CONFIGURATION MANAGEMENT AND VIRTUAL SIMULATION IN THE FUTURE
V-ZUG plans to expand its use of the 3DEXPERIENCE platform’s virtual simulation capabilities to cut development costs and cycle time even more. “We would like to define the product as accurately as possible with early product simulation, thus cutting costs related to changes. And by optimizing the digital product, we are able to reduce the number of prototypes,“ Metzker said. “Moreover, as our customers demand more, we need to respond by offering a wider range of products,” Dober said. “A more consistent approach to development and better configuration management will improve our efficiency as well as the diversity and quality of our products. ‘Swiss-made’ will take on a whole new meaning,” he concluded.

Focus on V-ZUG
A Swiss company which develops, produces, markets and distributes high-quality, premium-segment kitchen and laundry appliances.
Products: ovens, steam cookers, cookers, hobs, coffeecenter, drawers, control units, range hoods, microwaves, dishwashers, refrigerators, washing machines, tumble dryers, fabric care systems.
Employees: 1,850
Headquarters: Zug, Switzerland
For more information www.vzug.com

Focus on Helbling IT Solutions
Helbling IT Solutions promotes creativity and innovation by creating PLM (Product Lifecycle Management) environments that are geared towards the needs of the client. Based on its staff’s wideranging and in-depth knowledge, Helbling IT Solutions focuses on the business-relevant elements of the value creation chain, which gives the client a competitive advantage. The company delivers PLM-related consulting, implementation and integration services.
For more information www.helbling.ch/