Port Kembla Coal Terminal
Port Kembla Coal Terminal (PKCT) is a coal-exporting facility that services two of Australia's richest coal reserves, the southern and western coalfields of New South Wales
DELMIA Quintiq allows us to provide feedback to customers on a real-time basis as well as optimize throughput throughout PKCT.
Customer
Port Kembla Coal Terminal (PKCT) exports high-quality coking and steaming coal to customers around the world, primarily to China, India and other Asian countries.
The challenges of handling receipt, storage and dispatch of such large volumes of coal, including coordinating train and truck unloading, devising optimal ship loading and managing onsite storage, created a complex planning challenge. Adding to the complexity are fluctuations in demand and resource capacity limitations.
“We are currently running at a throughput rate of about 14 million metric tons per year,” said Mark Beale, planning manager at PKCT. With customer orders projected to increase in volume, PKCT forecasts a significant increase in throughput.
Challenge
“The planning solutions we had in place before DELMIA Quintiq were predominantly paper-based – individual spreadsheet models that were not integrated,” Beale said.
Often, Beale added, when there was no vessel at port, loading facilities were idle. The existing planning solution did not provide visibility into the future effects of planning decisions over any significant period.
Additionally, planning was heavily reliant on a small pool of experts with the most senior and most experienced planner nearing retirement.
With plans for expansion that could eventually double throughput at PKCT, it was clear that a better planning system was needed.
Requirements
The solution had to be capable of handling the multilayered planning tasks associated with train and truck unloading, ship loading and managing onsite storage.
“We were looking for an advanced planning system that could handle our complex work environment while also being extremely flexible,” said Peter Green, general manager at PKCT. The solution had to take into consideration the numerous business rules associated with stockyard usage, machinery and other critical port assets.
Of equal importance in the selection process, was “the transparency and visibility of decisions on either inbound constraints or outbound constraints,” Beale said.
The choice
PKCT chose DELMIA Quintiq because of its proven track record in the industry. “DELMIA Quintiq is recognized as highly successful in the field," said Green. "We could get exactly what we needed: a solid solution with flexibility.”
One of the key features of the integrated operations planning system is that it enables real-time feedback on inbound and outbound logistics constraints as well as on their stockyards. “The model allows us to provide feedback to customers on a real-time basis as well as optimize throughput throughout PKCT," Beale said.
This real-time visibility across PKCT’s operations covers ship loading resources and stockpile planning. It is possible to optimize stockpile planning based on scheduled incoming stock and scheduled vessel arrivals. Loading resources are planned with respect to hatch plans, tidal conditions and scheduled equipment maintenance. DELMIA Quintiq covers operational planning to maximize throughput on a daily basis, tactical planning to resolve port scheduling and stock pile issues on a rolling weekly basis. What-if scenario capabilities enable full understanding of the consequences of planning decisions on port operations.
The integrated solution enables stakeholders to make informed decisions on the parts of the supply chain they control. In addition, the software supports PKCT in increasing efficiencies and visibility across the supply chain.
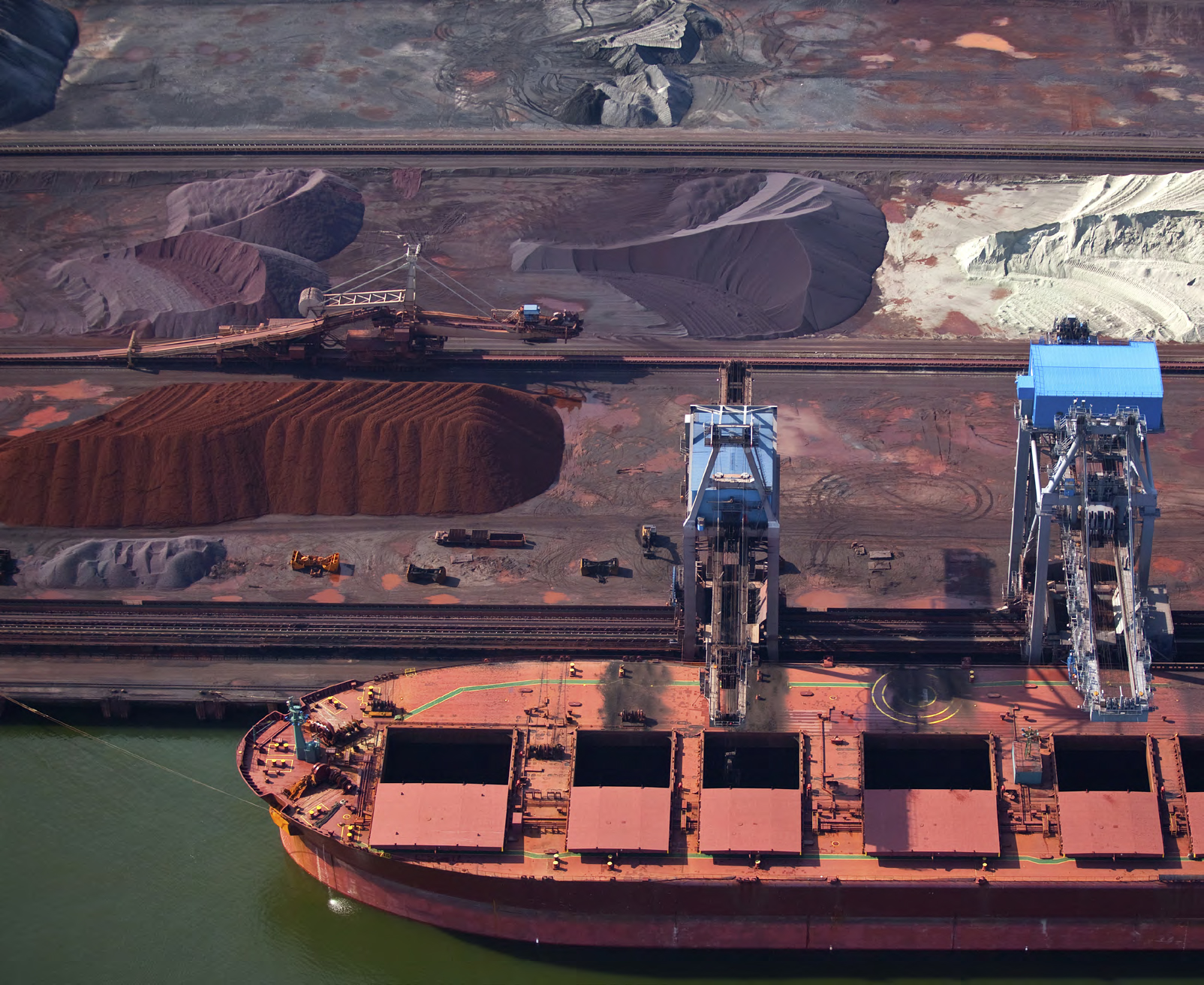
Implementation
"The challenges for the implementation were predominantly cost and schedule,” said Beale. “There was a tight time frame and a tight budget; both were met without issue. The data system integration was the third element or challenge, and that required both companies to come together to use their intellectual horsepower to deliver the outcome – it was a very successful marriage of both companies.”
The contract was signed in July 2009. In February 2010, the project went live. “From start to finish it was about six months. Both organizations worked very closely together and held to schedule," noted Beale. "The implementation went off without a hitch.”
The results
Within six months of going live, the company reported improved port terminal throughput, maximized use of the stockyard, and enhanced visibility of scheduled maintenance and its impact on capacity, resulting in shorter coal ship queues.
According to Beale, the benefits that the DELMIA Quintiq solution brought to PKCT could be seen primarily in areas which had constraints, such as the stockyard. “We believe we’ve got about 10 percent greater usage of the stockyard, reducing bottlenecks on the inbound and outbound constraints, and increasing throughput as a result.”
Automating the planning functions, incorporating the embedded shared knowledge and providing expert decision support have all helped to optimize the planning process. Having visibility and foresight means that planners are better equipped to handle outages and deal with large forecast demands. All in all, planners are now more independent and they work under less stress, lowering fatigue. In addition, the DELMIA Quintiq solution enables PKCT to do performance-based planning. Managers can develop data-driven targets and goals and make informed decisions on the parts of the supply chain that they control and influence.
“The most interesting thing that we found was the visual capability of depicting constraints. That was really important because there were several ‘Aha!’ moments when we went: ‘Okay, we’ve got a constraint. How do we fix that?’ The answer is: we address these issues through the scenario planning – the ‘what-if’ planning – which is a very powerful tool.”
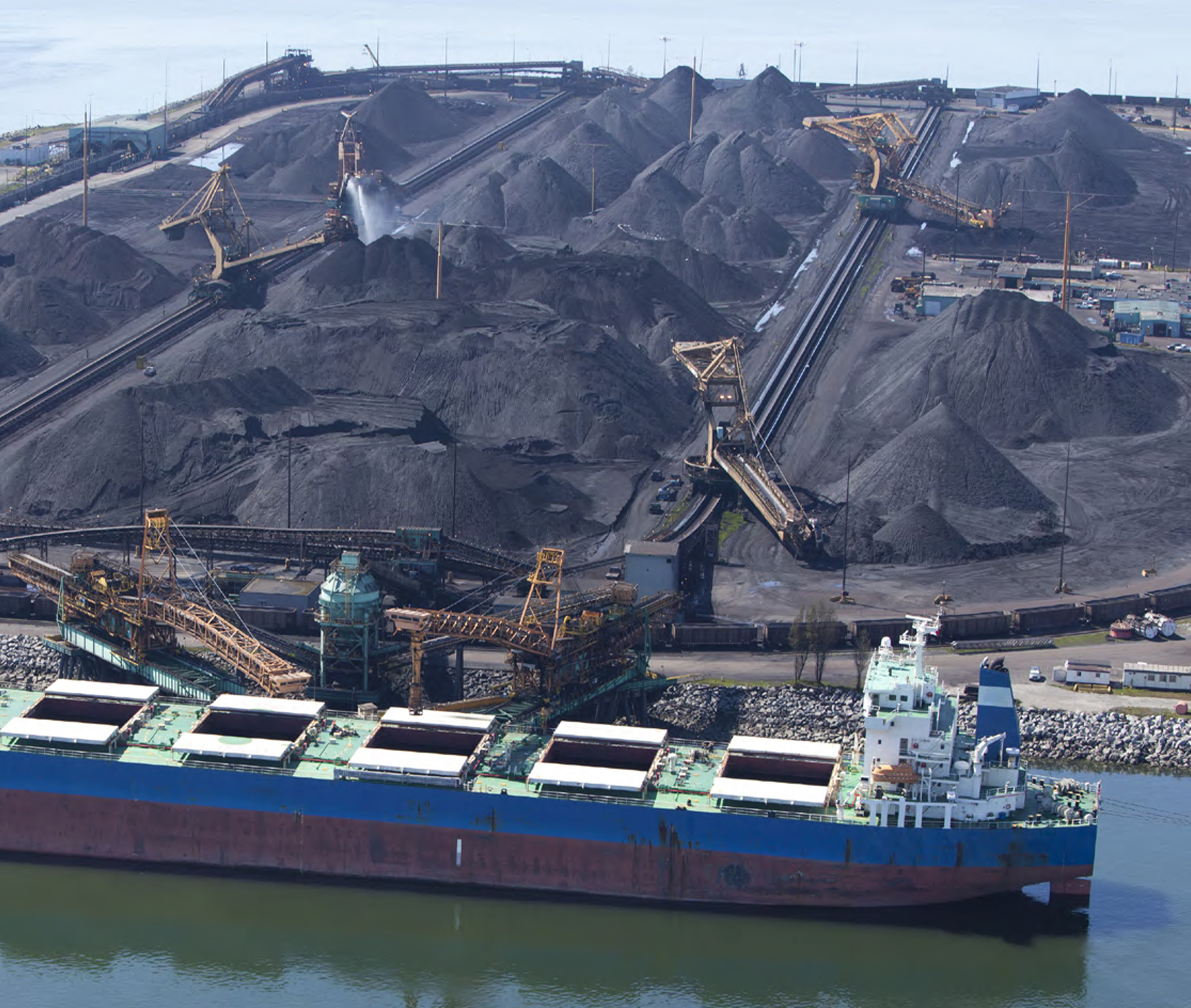
The future
PKCT is aiming for a throughput in the range of 23-28 million metric tons annually. With the current solution, DELMIA Quintiq has already helped to advance this goal.
The next challenge is to optimize the plan for tipping trucks and trains at the port. It has become evident that this is the next bottleneck in operations. PKCT also has a bulk products berth that is currently planned manually.
"PKCT and DELMIA Quintiq are working together to evaluate the use of the existing model and the expansion of that model to incorporate a second berth and a second stockyard," Beale concluded.
PKCT Fast Facts
Location: Australia’s east coast, 45 miles south of Sydney
Exports: Over 14 million metric tons of coal annually
Top Markets: China, India and other countries in Asia
Coal Delivery to PKCT: Seven trains per day at 3,300 metric tons per train / Approximately 420 truck deliveries per day at 40 metric tons per trip
Stockyard Capacity: 850,000 metric tons