AutoForm-QuickLink for CATIA V5
The AutoForm-CATIA5 module directly integrates AutoForm software and AutoForm parameters into CATIA V5, making two programs associatively linked. User...
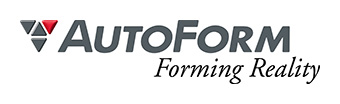
A solution by: AUTOFORM ENGINEERING
Application domain: Simulation
Solution Overview
The AutoForm-CATIA5 module directly integrates AutoForm software and AutoForm parameters into CATIA V5, making two programs associatively linked. User control of AutoForm and the management of simulation files are partially transferred to CATIA. This integration not only greatly improves the speed and efficiency of design and engineering cycles, but also improves the consistency of part data in CATIA and the consistency of process data in AutoForm. Surfaces, curves and tipping information are transferred from AutoForm to CATIA V5, and the corresponding process layout is stored in the CATIA V5 part document. Similarly, surfaces, curves and tipping information are transferred from CATIA V5 to AutoForm to update and store the part geometry and to provide process information.
The main features of AutoForm-CATIA5 include:
*Rapid development of die faces can be done in CATIA V5 starting from an AutoForm 4D-Process-Layout. Completed die face designs as well as wireframes are automatically transferred from AutoForm to CATIA V5.
*Process layout is intuitively and quickly defined and provided in the CATIA V5 structure tree. Thus, active surfaces and other geometric process data, designed with CATIA V5 can be linked with this CATIA V5 process layout. And a forming simulation could be started at any time.
*Automatic updating of the entire data chain - from CATIA part geometry through die faces to AutoForm simulations - greatly reduces die development time. Due to this associative link, several alternative tooling concepts can be validated in just one day.
The main features of AutoForm-CATIA5 include:
*Rapid development of die faces can be done in CATIA V5 starting from an AutoForm 4D-Process-Layout. Completed die face designs as well as wireframes are automatically transferred from AutoForm to CATIA V5.
*Process layout is intuitively and quickly defined and provided in the CATIA V5 structure tree. Thus, active surfaces and other geometric process data, designed with CATIA V5 can be linked with this CATIA V5 process layout. And a forming simulation could be started at any time.
*Automatic updating of the entire data chain - from CATIA part geometry through die faces to AutoForm simulations - greatly reduces die development time. Due to this associative link, several alternative tooling concepts can be validated in just one day.
Benefits
- Increase productivity for CATIA users by direct access to AutoForm results
- Improve accuracy of product and process data by automatic and instant updates
- Increase speed and efficiency of the product development cycle
- Minimize data source errors with one shared CAD data file