Humans: powering the heart of sustainable, digital factories of the future
What is the role of the worker as manufacturing becomes increasingly digital?
This article was produced by Financial Times for Dassault Systèmes
Digital technology has transformed manufacturing, and today plays a greater function in shaping the industry than ever before. It has advanced and improved processes at great pace and acted as a key driver in the shift towards a greener future. Advanced technology such as digital simulation is helping companies to lower emissions and waste when there is limited time to mitigate the catastrophic effects of climate change..
Inevitably, the increasing introduction of automation has changed the traditional human roles integral to production. However, as the symbiosis of man and machine in the factory of the future develops, it has become clear that the universal adoption of digital technology will ultimately produce more jobs for humans than it will take away. Critical thinking will be fundamental in this journey.
Growth Industry
Despite misplaced concern that technology is replacing workers, it is in fact increasing the potential for human input – even if this interaction will look different in the future. Jobs in the manufacturing industry have actually been growing at double-digit rates since mid-2017, but a study by Deloitte and The Manufacturing Institute revealed a growing disparity between the roles that need to be filled and the talent pool available to step into them. As digital technology continues to shape the industry, businesses must adopt a systemic approach to reskilling for the jobs of the future in order to answer to the growing call for more technological and cognitive skills. “Tech is not taking away the role of the human, it’s improving it,” says Dassault Systèmes’ Executive Vice President Florence Verzelen. “Technicians can become engineers, and engineers can become business innovators. It improves and extends the capabilities of human beings.
While there is no doubt that technology has improved efficiency, research has shown that a fully automated factory is not as productive or cost-effective as when humans and robots work together. A recent MIT study revealed that idle time is reduced by 85 per cent when people work collaboratively with a human-aware robot compared with a solely human team, while Veo Robotics found that cycle time for an assembly job can be halved using human-robot collaboration. To optimise results, a combination of the accuracy and speed of automation coupled with the critical thinking of humans is increasingly being embraced by manufacturers in the transition towards the blending of workers and robots.
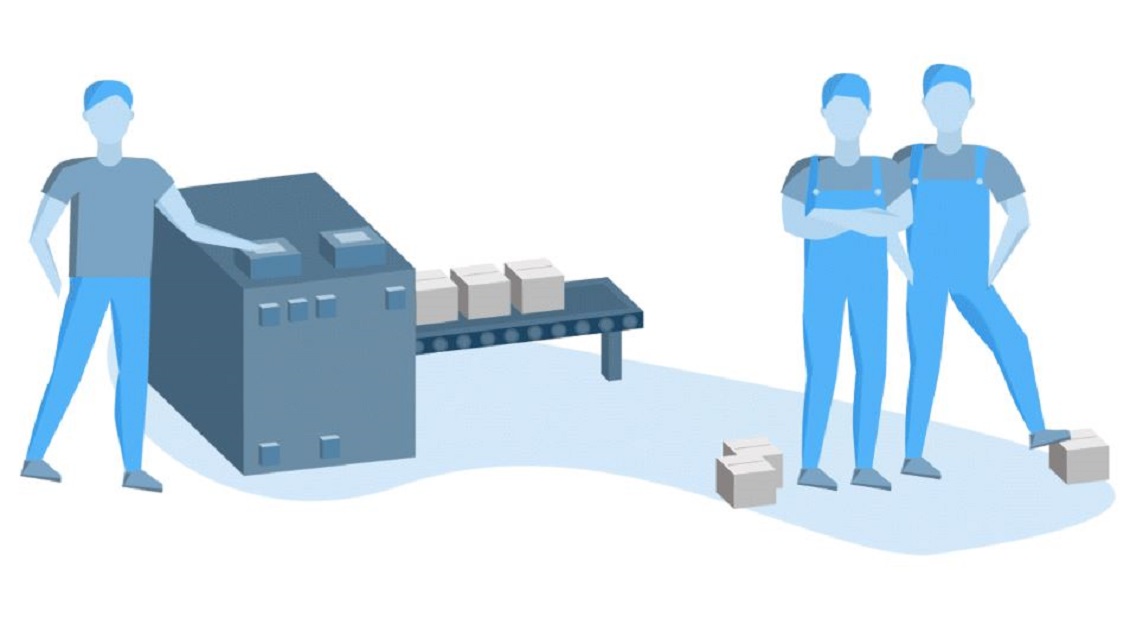
Idle time reduced by 85% when people work collaboratively with a human-aware robot compared to a solely human team.
- Massachusetts Institute of Technology
Putting the impetus on collaboration while maintaining the role of humans at the centre of a business can be achieved by educating and empowering workers to program and manage smart factories. This ultimately results in less waste of resources and time. Research by the World Economic Forum (WEF) has revealed that 48 per cent of time was spent on repetitive labour in 2019, but this is predicted to drop to 35 per cent in 2030 through the integration of tech. The sheer speed of change, however, will be so fast that technologies such as virtual simulation will be vital in the transformation of the workplace, allowing workers to adapt safely, effectively and risk-free. Given that 85 per cent of the jobs that will exist in 2030 haven't even been invented yet, reskilling workers to be able to “think critically, work in a team, be able to analyse big data and to understand how we improve the world though automation,” are crucial according to Florence Verzelen.
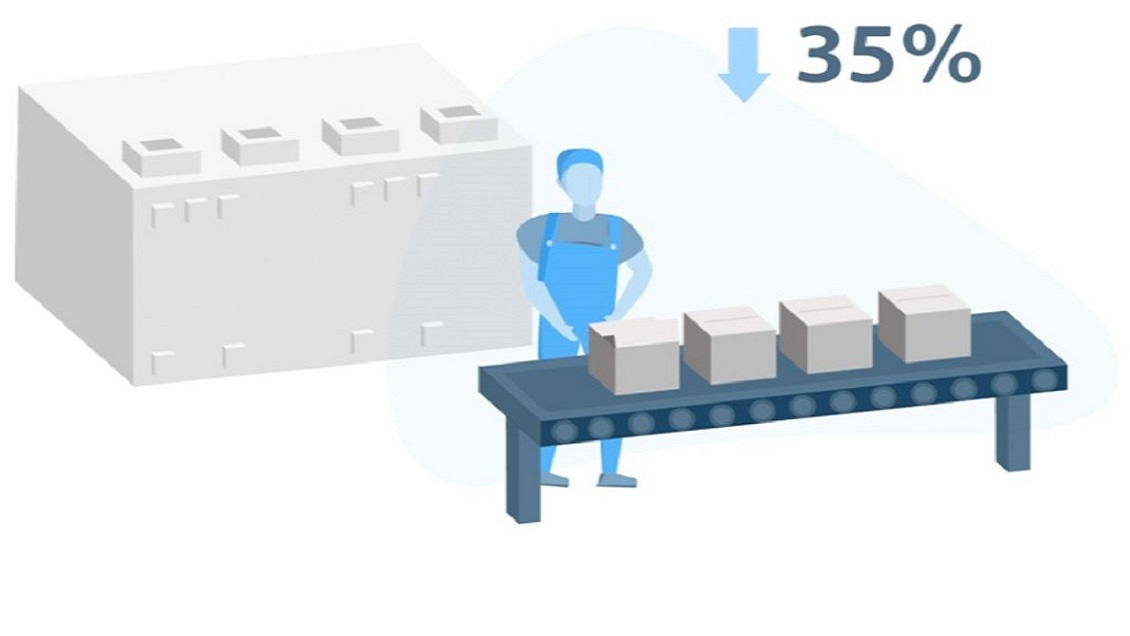
Time spent on repetitive labour is predicted to drop from the current 48% to 35% by 2030 through the integration of tech.
-World Economic Forum
Value chain reactions
French luxury porcelain manufacturer Bernadaud has been producing its wares in Limoges for more than 150 years. The family-owned company recently proved that even the most traditional manufactur can introduce cutting-edge technology into their production and combine it successfully with long-serving human workers. The company implemented Dassault Systèmes’ 3D virtual modelling to blend its historic designs with more complex shapes that were previously impossible to achieve. This combination of human and digital design allows the business to produce prototypes much faster and present them to clients before production.
While the products are still hand crafted by artisans, the increased speed and waste-reduction has been facilitated by digital technology. “The constant search for new and more complex shapes as well as new manufacturing processes has led us to combine our know-how with new technologies,” says Bernadaud Director of Development Charles Bernadaud. “Each generation has brought different expertise to each stage of the company’s evolution. I am glad to play my part in opening up new perspectives while accompanying society’s move towards sustainability.”
The potential for the manufacturing sector to provide roles for workers is huge. According to the WEF, 4.6 million manufacturing jobs will open up in the next decade in the US alone. However, 2.4 million of these are predicted to go unfilled. These figures reveal that while the demand for jobs for humans in the face of increasing automation is clearly there, leaders must implement change across value chains and production to fully thrive in this era of transformation. If we are to work towards a more efficient, sustainable future in manufacturing, we must challenge the notion that as digitalisation and technology increasingly integrate into industry, humans are losing their role in the factory. In reality, they are a vital part of this crucial transformation process. As Florence Verzelen concludes “without humans, there is no factory.”
Read our latest Manufacturing articles
Explore our Industry Solution Experiences
Learn more about how our industry solutions can help you to achieve your professional ambition and business objectives