Circular thinking: how manufacturing can lead us to a greener, more sustainable future
In a crucial bid to lowering emissions and reducing waste, digital technology is propelling the manufacturing industry into a sustainable future
This article was produced by Financial Times for Dassault Systèmes
In the battle against climate change, companies in the manufacturing industry have a major role to play. A huge corrective leap is needed if the Paris Agreement’s carbon-neutral target is to be met. With evidence that 45 per cent of the global economy’s emissions can be eliminated by rethinking manufacturing, distribution and production, sustainability in this sector is of key importance.
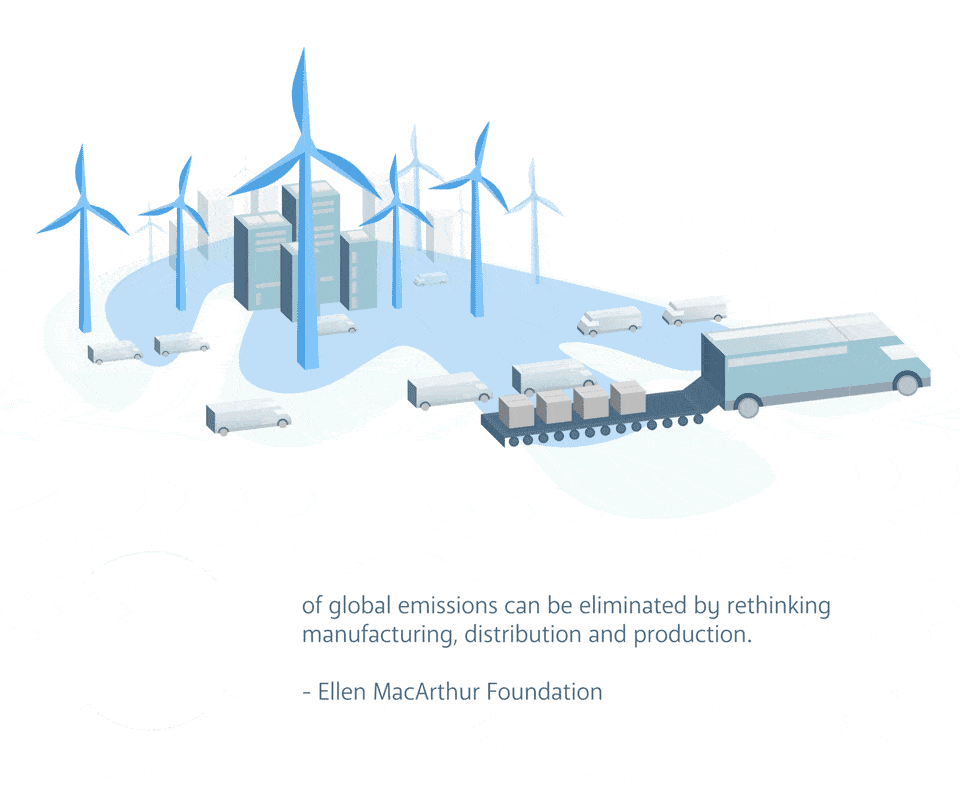
Applying circular economy strategies in five cornerstone areas of manufacturing – cement, aluminium, steel, plastics and food – will represent major progress, equivalent to cutting current emissions from all transport to zero. This massive shift is progressively being achieved by increasing efficiency and reducing waste in manufacturing processes, a transformation underpinned by significant developments in digital technology.
There is no doubt that sustainability in manufacturing cannot be attained without it. “There is no contradiction between industrial excellence and sustainability,” says Guillaume Vendroux, Dassault Systèmes’ DELMIA CEO. “In fact, if this is achieved through lean processes it is the very path to sustainability. It is the robust, scientific way to achieve your goals.”
Valuable Resources
Building sustainability into the very foundations of a company not only reduces the negative impact on the environment but can provide very real advantages to the business. Responsible waste management reduces costs, introducing green techniques driven by new innovation, while regulatory requirements are met early and the image of the company in the market is strengthened.
This journey to transformation has been accelerated by the increasing digitalisation of the industry with efficiency being improved in factories that have embraced technologies such as artificial intelligence (AI) and the Internet of Things (IoT).
Platforms which allow end-to-end visibility, for example, can significantly cut valueless by-products. Digital techniques such as virtual twin technology have revolutionised the industry in this respect and speak to the very heart of the circular economy. This technology can optimise waste management, lengthen the life of materials and reduce the reliance on precious non-renewable resources.
Improved waste management is critical in the sustainable factory of the future, and a closed-loop system which converts waste products into resources that are put back into the manufacturing cycle is the goal. Achieving this is not without its challenges, and it is an area in which virtual simulation has proved invaluable. The path to waste management best practices for manufacturers begins with the introduction of three main principles: end-to-end visibility, which eliminates damaging information silos across a business; life cycle assessment, which gives deep insight into a product while it is being developed; and digital intelligence platforms in the product design phase which enhance yield and quality.
New Dimensions
Digitalisation, including virtual simulation technology from a solution provider such as Dassault Systèmes and its 3DEXPERIENCE ® platform, can have a radical effect on the production cycle of a product, from design to final creation, by putting sustainability front and centre in the process. This technology, allowing companies to create a virtual 3D model, which collects physical operations together into an all-encompassing digital copy and gives manufacturers the chance to comprehensively visualise the end product and how to produce it efficiently, sustainably and cost-effectively. In doing so, they can assess impacts and test the viability of any necessary solutions before dedicating materials and money which could be potentially wasted on physical resources.
For global agricultural machinery manufacturer Claas, implementing this technology created an environment in which its designers could digitally store and trial their designs before producing an expensive and resource-heavy prototype, rather than installing equipment only after a mechanical design had been completed. With their previous system, a redesign could “escalate to prohibitive proportions in terms of planning and costs,” explains Kai Wallasch, Advanced PLM Development at Claas. However, using Dassault Systèmes’ 3DEXPERIENCE solutions, Claas’ engineers across the board had synchronous access to the design. “Now, they voice their requirements early so these are taken into account before the mechanical design is finalised. Adjustments are made on the fly in a digital environment. As a result, we have less waste and fewer errors during production,” says Wallasch.
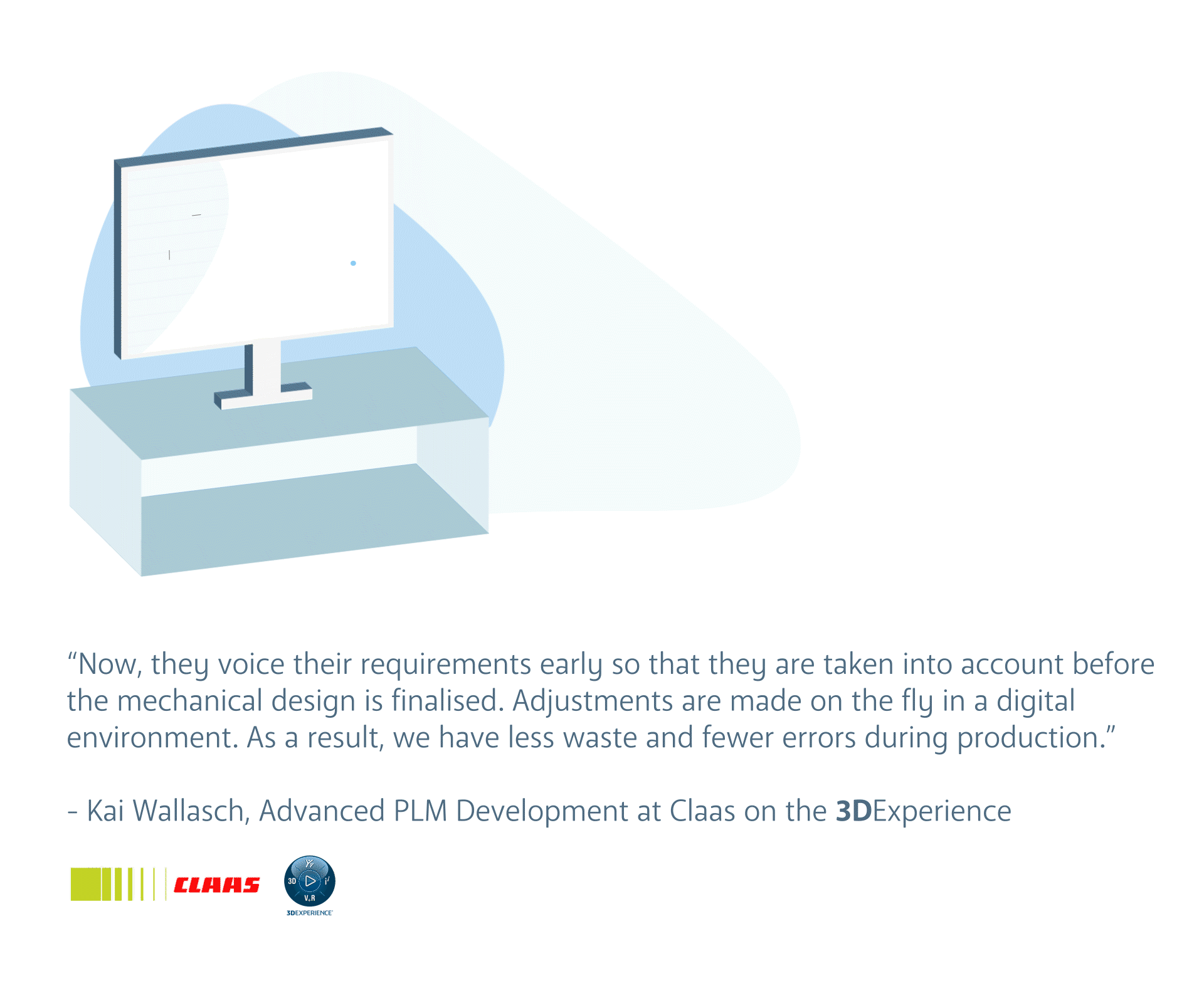
These kinds of digital technologies are proving instrumental in creating a resource-efficient industrial sector which can help decrease costs, develop a sustainable foundation, promote company growth and reduce the harmful effects of emissions and waste. Manufacturing represents 54 per cent of the world’s energy consumption and is responsible for 20 per cent of global emissions, so the time for change is now.
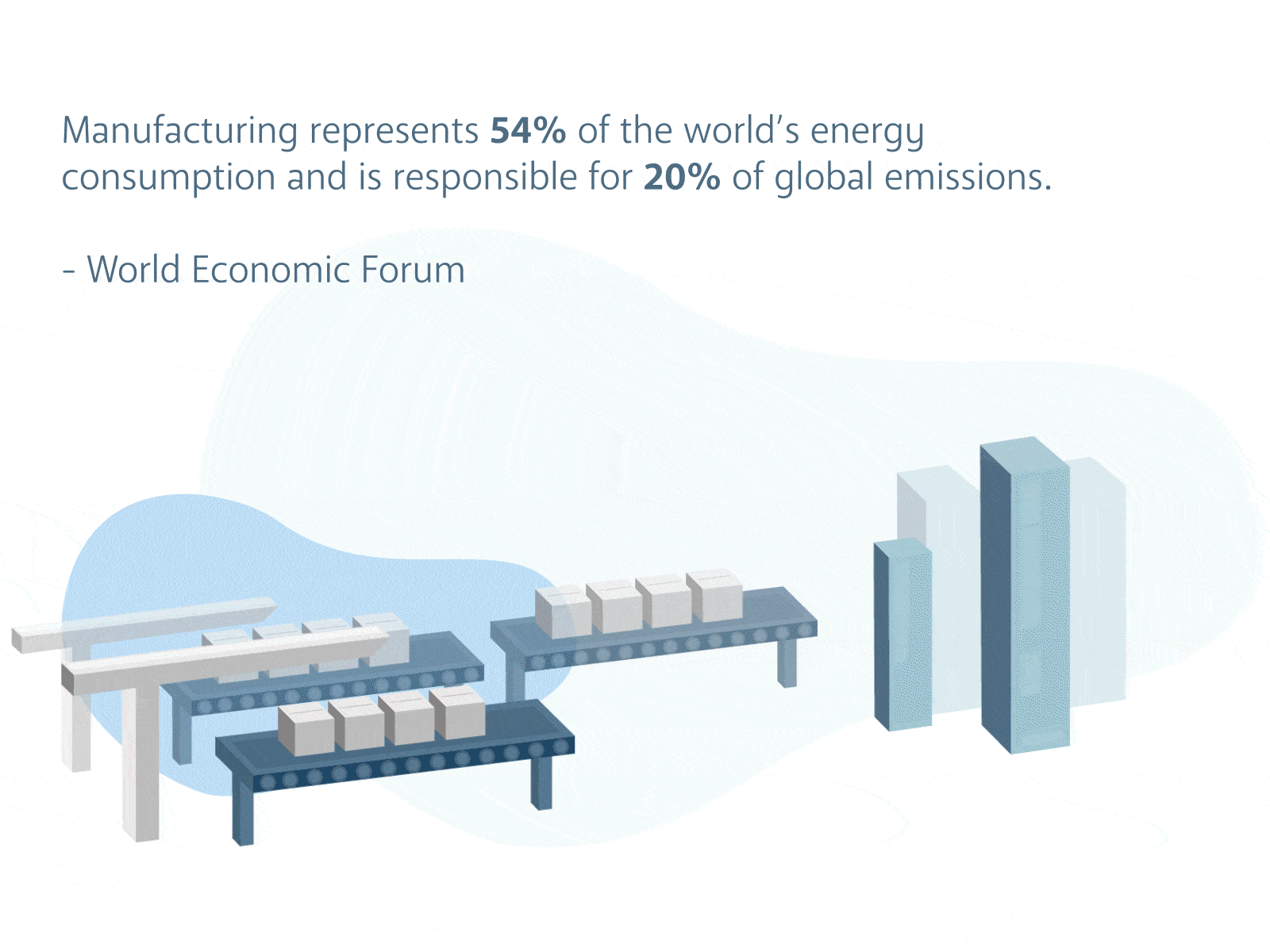
According to the Ellen MacArthur Foundation, if the manufacturing industry adopts a circular economy it could save up to US$630bn a year on raw materials in the EU alone.
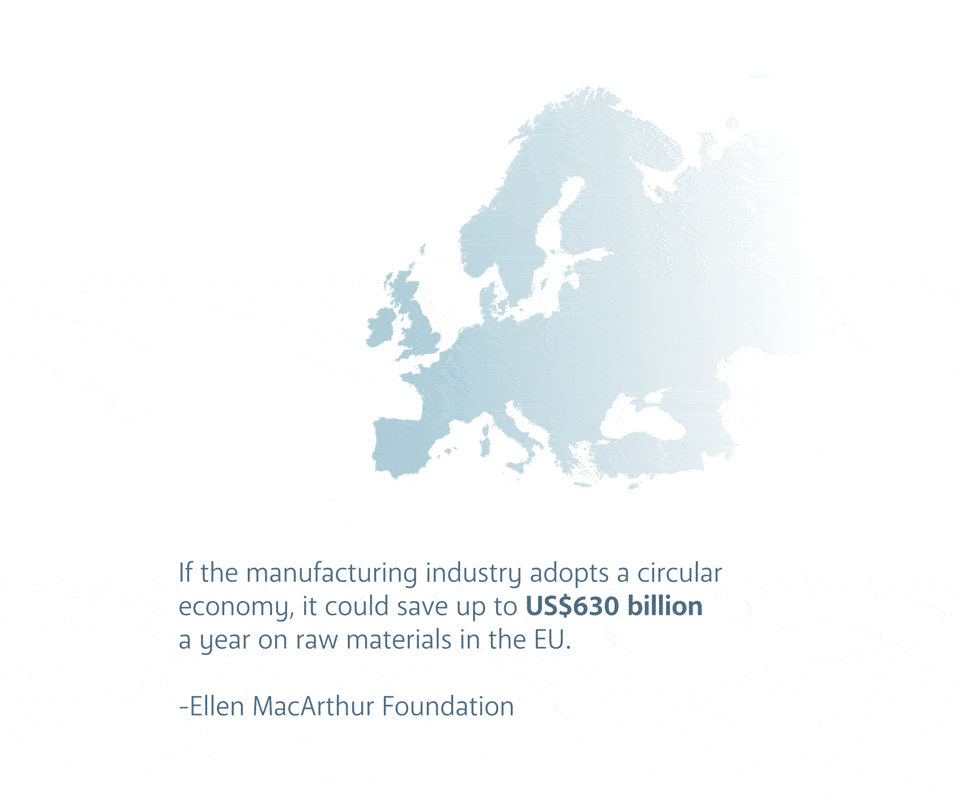
Advanced technology digital platforms such as 3DEXPERIENCE are significantly accelerating the move towards sustainable manufacturing by improving manufacturing process efficiency, reducing the use of non-renewable resources and extending the life of by-products that would otherwise be wasted.
As Vendroux succinctly puts it: “Be lean and you will be green.”
Read our latest Manufacturing articles
Explore our Industry Solution Experiences
Learn more about how our industry solutions can help you to achieve your professional ambition and business objectives