Do More With Less: The Additive Manufacturing Edge in Lean Manufacturing
Secure a competitive advantage in lean manufacturing by leveraging additive manufacturing technology.
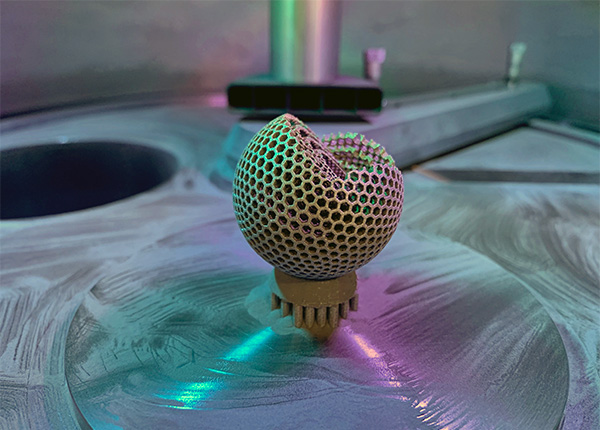
Ever since Japan's Toyota Motor Company introduced lean manufacturing to the world, lean principles have revolutionized factories worldwide with its emphasis on minimizing all forms of waste and maximizing operational efficiency. Fast-forward to today's landscape of fierce global competition and rapid technological advancements, where optimal implementation of lean principles rides on the rise of additive manufacturing, and in particular 3D printing capabilities.
Though it can be challenging to plan and implement these initiatives from the ground up, getting support from an integrated platform with end-to-end digital solutions can help manufacturers enjoy lean manufacturing benefits while staying competitive, agile and resource-efficient.
Get Started on Successful Additive Manufacturing Implementation
Adopting additive manufacturing is the best way forward to expand lean manufacturing targets. Download this white paper for a complete guide on planning and executing your additive manufacturing strategy successfully with Dassault Systèmes’ 3DEXPERIENCE® platform.
Is Additive Manufacturing the Same as 3D Printing?
"3D printing is one of the forms of additive manufacturing that uses computer-aided design (CAD) to build objects layer-by-layer," explained Adrian Wood, DELMIA Strategic Business Development and Marketing Director at Dassault Systèmes.
He added, "The term 3D printing is typically associated with consumer-grade applications while additive manufacturing is a big-picture term that often involves product design and the development of innovative technologies to create greater manufacturing efficiency. It's one of the capabilities that manufacturers can put in place to support their lean manufacturing operations and goals."
Change the Game With Additive Manufacturing
According to EY's report, 65 percent of the companies surveyed have used additive manufacturing technology to take their lean manufacturing operations to the next level. The advantages of executing lean principles include:
- Producing value-added products
- Cutting operation costs
- Improving strategic flexibility
- Driving long-term growths
Will additive manufacturing play a role in the future of lean manufacturing?
To me, the future is already here and we can leverage the technology to eliminate non-value added steps, wring inefficiencies out of every process and fully optimize waste reduction.
From just-in-time production to Six Sigma, the primary goal of lean principles has always been to optimize all forms of waste reduction:
- Overproduction
- Waiting times
- Unnecessary logistics
- Over-processing
- Excess inventory
- Motion
- Defects
How Additive Manufacturing Drives Lean Operations
Reduced Material Consumption
Unlike subtractive manufacturing such as conventional machining, casting, and forging processes, additive manufacturing constructs products through layering material rather than removing, cutting or filing pieces. This unique capability enables manufacturers to increase the production of more near net shape components and reduce material consumption and waste.
Ability to Create Complex Components
Additive manufacturing supports lean principles better than subtractive manufacturing, which requires different product components to be produced separately and assembled. Creating complex parts (of varying shape, material and functionality) within a single piece of material helps trim processes, save time and reduce operational costs.
Lower Logistics and Inventory Costs
Additive manufacturing processes enable on-demand manufacturing of components and replacement parts, removing the need to keep warehouses filled with an idle inventory of forgings. Substituting a homogenous feedstock for multi-material 3D printing also helps eliminate waste material from the production process.
Shorter Lead Time and Improved Consistency
By using agile 3D design and printing capabilities, manufacturers can produce small batches and optimize design dimensions to reduce waste and energy consumption. This allows manufacturers to manage processes better and create bespoke parts to meet market demands, minimize wasteful large-batch production and remain agile despite supply disruptions.
Reduced Need for Multiple Machines
Since 3D printers can print infinite design options in theory, additive manufacturing enables manufacturers to offer more product variations without investing in additional machines or infrastructure. This agility allows manufacturers to occupy much smaller facilities and further optimize lean manufacturing.
Digital Designs and Rapid Prototyping
Additive manufacturing's product development stage relies on virtual simulation technology, eliminating the need for machining and minimal finishing. Simulation cuts product development time and costs, making it possible to develop designs that couldn't be fabricated using standard machine tools. Different product designs are easily converted into cost-effective prototypes that take on new forms with sufficient input data and software support.
Unleash the Power of Additive Manufacturing
Optimize your additive manufacturing strategy on the 3DEXPERIENCE platform.
Dassault Systèmes' in-house expert, Adrian Wood, shares how you can get the most out of additive manufacturing in a closed-loop environment.
Read our top articles on Operational Optimization
Explore our Industry Solution Experiences
Learn more about how our industry solutions can help you to achieve your professional ambition and business objectives