Smart Manufacturing: A Unified Ecosystem for the Next Normal
Mitigate disruptions and adapt to changing demands in the post-pandemic future with the industrial internet of things (IIoT) powered by the 3DEXPERIENCE® platform.
Recent disruptions that affected the global economy, such as shortages of raw materials and parts, have made manufacturers realize the cost of deferring the adoption of digital transformation and smart manufacturing.
We spoke with Prashanth Mysore, Strategic Business Development Director at Dassault Systèmes, to get the answers to how digital transformation prepares manufacturers for disruptions and enables them to thrive in a post-pandemic future.
Manufacturers can achieve this [agility] by making data actionable. We know that data insights are crucial for flexible and resilient supply chains that can move rapidly to meet shifts in market demands and customer requirements. But aggregating and making sense of the data requires the right digital solution.
Smart Manufacturing for Disruptive Times
Synchronize your operations across design, engineering production and supply chains using a unified collaborative environment. Our white paper reveals the importance of an integrated business platform to meet strategic business and production goals.
Overcome Disruptions and Global Trade Tensions
Leverage the Right Digital Support
Below are some specific steps on how manufacturers can utilize digital solutions on the 3DEXPERIENCE platform to make use of data insights and perform better:
Be resilient
First, manufacturers can model a virtual twin of the factory on the 3DEXPERIENCE platform to design the production shop floor for resilience and model scenarios, and test out potential responses to disruptions.
Be efficient
Second, manufacturers can optimize planning and scheduling as well as adopt lean manufacturing, automation and robotics to raise efficiency and create leaner, more resilient operations.
Be flexible
Third, stakeholders can collaborate on the platform to build a flexible ecosystem of suppliers and partners. Flexible networks can help companies foresee disruptions (e.g., shortfalls in raw materials and parts), respond rapidly to changing market demands and expand output capacity by 15 to 20%.
Map Future Success Digitally
The IIoT is central to factories of the future – and more manufacturers will utilize virtual twins, IIoT sensors and devices as well as artificial intelligence (AI).
With these technology tools, manufacturers can analyze internal and external data, optimize existing processes, model risk scenarios, deploy early warning technologies and develop pre-programmed responses. The virtual twin experience will become even more valuable in increasing operational efficiency and flexibility.
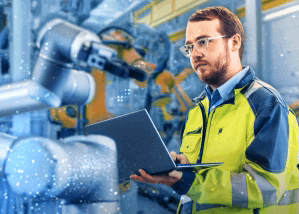
Meanwhile, digital collaboration and real-time visibility are important for achieving flexibility. Cloud-based digital collaboration enhances information sharing as well as the quality and speed of decision-making within the organization and across the supply chain network. With the 3DEXPERIENCE platform, manufacturers can leverage the integral cloud-based capabilities to thrive against disruptions today and beyond.
Read more articles on Connected Industry
Explore our Industry Solution Experiences
Learn more about how our industry solutions can help you to achieve your professional ambition and business objectives