Big Data Analytics: A Catalyst for Smart Manufacturing
Transforming big data into actionable analytics requires a data-driven, model-based approach. Find out why the 3DEXPERIENCE® platform is the right fit.
The manufacturing sector is a significant part of the global economy, accounting for nearly 16% of global GDP in 2018. In today’s interconnected world, manufacturing disruptions can easily and quickly propagate across borders. Manufacturers need a powerful solution to mitigate this risk.
One such solution can be found in big data, which are exceptionally large data sets collected at every stage of production from devices and operators. Its growth in recent years, becoming more integral in manufacturing operations, presents both challenges and opportunities to make manufacturing smarter.
When implemented correctly, big data can empower manufacturers to make more agile and sustainable business decisions. In today’s data-driven economy, the best way to boost efficiency, quality and productivity is by turning big data into actionable analytics. This is where the Industrial Internet of Things (IIoT) comes in.
Drive Flexibility and Agility Into Manufacturing and Operations
Unlock the potential of the IIoT in an exclusive interview with Prashanth Mysore, Dassault Systèmes.
What is the IIoT?
The IIoT is a network of intelligent devices connected to form systems that monitor, collect, exchange and analyze data. Embedded sensors and connected production equipment, such as conveyors, fastening tools and robots, can provide manufacturing engineers and plant managers with reams of data.
As a result, manufacturers can improve the performance of their assets, speed up job assignments on the shop floor and even improve their ability to achieve remote and autonomous operations. That information enables better and faster decision-making within factories, making continuous improvements more quantified and disciplined.
The IIoT gives manufacturers a new look into their processes and products down to a granular level of detail. However, this also creates an unintended side effect:
What happens to data that is extracted and stored?
Data sets typically remain siloed off in disconnected databases without being incorporated into the day-to-day manufacturing processes, making its interpretation, accessibility and use difficult.
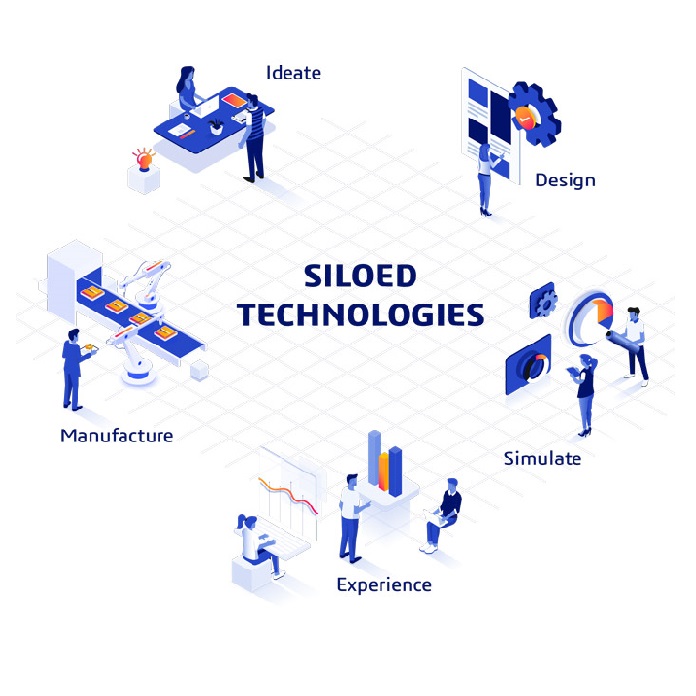
Big data by itself does not create value until it is employed to solve business challenges. What’s needed is access to different kinds of data spread out across organizational silos, as well as robust analytics capabilities that include the right digital business platform and the right skill sets to use them.
As manufacturers adopt more IIoT systems, they’ll need to manage, enrich and cleanse more real-time data. This is where artificial intelligence and machine learning shines, as it can be used to manage massive volumes of data, discover patterns and generate insights and solutions. With these capabilities, manufacturers can greatly increase their responsiveness and quickly identify new business opportunities.
Data may be the crude oil of the 21st century, but without the ability to analyze and action based on tangible, accurate insights, it is simply taking up space.
2019 Manufacturing Trends Report, Microsoft
The Smart Manufacturing Experience
To ensure the right information is used for collaboration across all functions and all departments within a company, big data needs to be contextualized and related. This is possible with the 3DEXPERIENCE platform, which offers manufacturers a broad smart manufacturing experience.
Here’s how the 3DEXPERIENCE platform makes your manufacturing smart:
Single source of truth
Integrate multiple data streams into a single source of truth, where all teams and collaborators can work off the same data sets and utilize the same learnings.
Precise simulation
Accurately simulate supply chain locations, machine placements and factory layouts that can then be configured to include interrelated rules.
Testing environment
Virtually test and validate R&D choices long before hitting the shop floor, enabling faster design and iteration before going into production.
Dedicated libraries
Simplify, organize, classify and optimize all necessary parts and components. Identify master parts for reuse and easily find all design-related documentation.
“The core of the 3DEXPERIENCE platform is a model-based, data-driven approach to help define business processes, workflows, data management and performance,” explains Prashanth. “This is what we call the virtual twin experience, an IIoT-based approach that allows business teams to frame data in the right context.”
Read more articles on Connected Industry
Explore our Industry Solution Experiences
Learn more about how our industry solutions can help you to achieve your professional ambition and business objectives