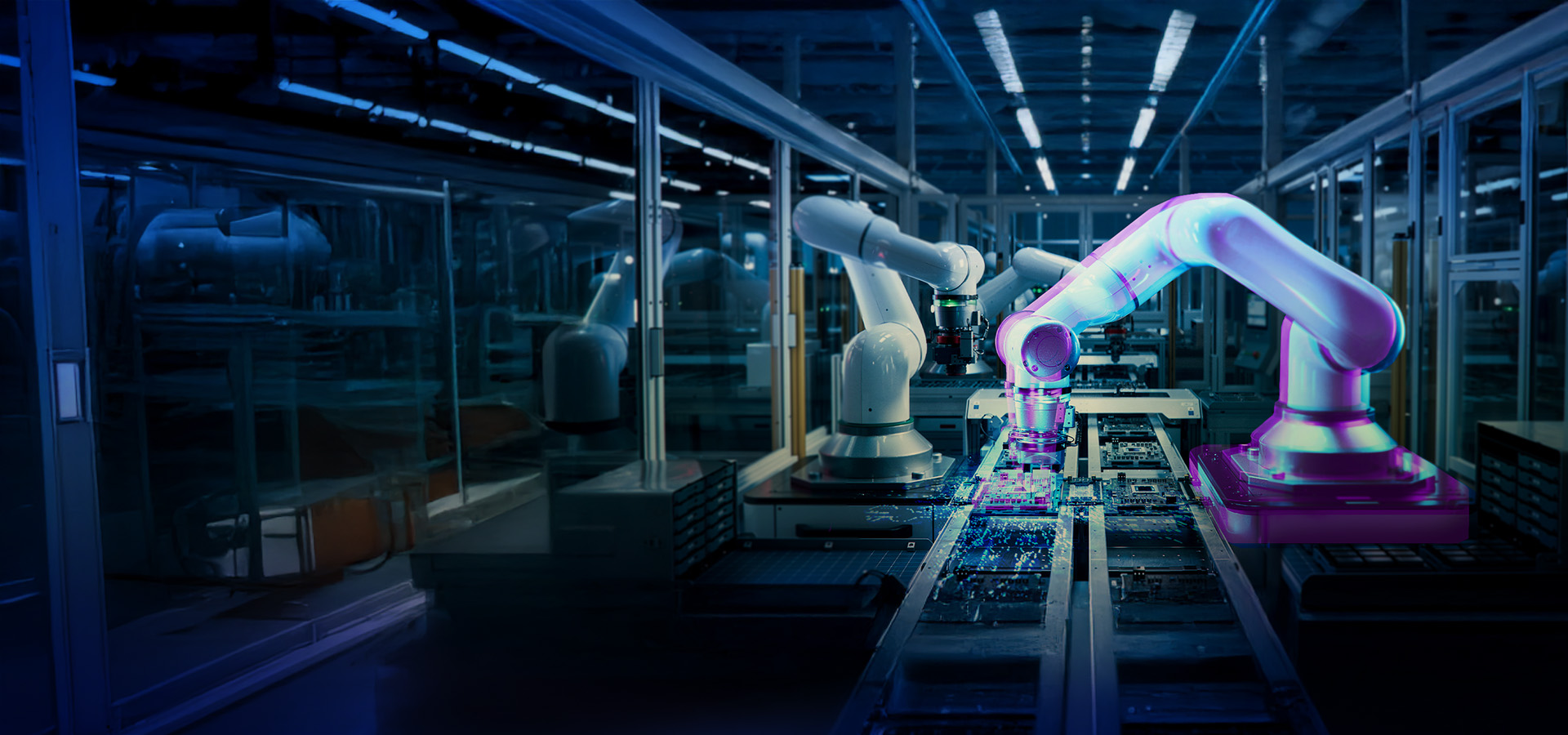
#26 : How To Empower Engineering Teams for Speed, Efficiency and Performance?
Discover how the virtual twin fosters end-to-end collaboration across product engineering, manufacturing planning, scheduling and operations.
#26: How To Empower Engineering Teams for Speed, Efficiency and Performance?
Join us on this episode as we explore a transformative strategy that revolutionizes the manufacturing of connected objects, from factory planning to production. We’ll dive into the power of the virtual twin and a closed-loop infrastructure that fuels agility and continuous improvement. Learn how data intelligence, machine learning and advanced process simulation empower high-tech companies to optimize manufacturing planning and operations to train new workers faster to maintain competitiveness in delivering cutting-edge devices.
Click here to learn more about how the virtual twin synchronizes manufacturing and engineering for optimized throughput.

Meet our speakers
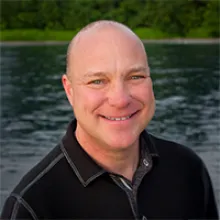
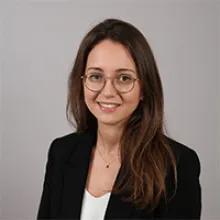
The creation of the virtual twin is the key. It’s not only the twin of the product but also of the process and all the resources required to manufacture it. Essentially, it’s built before you build it, allowing you to simulate everything about the manufacturing process and reduce ramp-up time while improving quality and efficiency."
Liliane Sadler
Read the transcript
Narrator: Welcome back to Disruptors Unleashed, where we explore disruptive technologies and chat with the trailblazers who are redefining industries as we know them. In our last episode, we explored the future of engineering education with Prof. Dr. Rainer Stark from TU Berlin, as well as Olivier Sappin and Valerie Ferret from Dassault Systèmes.
Today, we are diving into the real-life value of agile manufacturing to deliver innovative high-tech products and systems, which are enabled by the virtual twin technology. The 3DEXPERIENCE platform enables faster collaboration with the best tools, leveraging knowledge and know-how across functional and geographical boundaries. Tune in as our experts, Liliane Sadler and Ron Watkins share insights from next-gen engineering teams in action.
Adrian Wood: Hello, and welcome to our conversation about the very important symbiotic value network in play at high-tech manufacturers. I'm your host for today, Adrian Wood. I'm the high-tech strategic business development and marketing director at Dassault Systèmes. Today, we're going to dive into how leveraging the digital model-based synchronization of manufacturing engineering will lead to long-term success in delivering competitive connected systems.
Adrian: In the next 15 minutes, we’re going to show you how leading innovators were able to build a sustainable success strategy by effectively integrating their teams across high-tech product design, planning and manufacturing. With me today to help with the conversation, we have Liliane Sadler and Ron Watkins, two of our senior experts for high-tech innovation. Hello, Liliane and Ron.
So, let's start with you, Ron. You've been in the high-tech industry for many years, focused on business transformation in the areas of planning, manufacturing quality, warehouse and maintenance – everything to do with the shop floor, just to name a few. Any comments on the importance of this symbiotic relationship throughout the value network?
Ron Watkins: Absolutely. The high-tech manufacturers that we work with have enormous pressure on themselves to innovate faster, have flexible and efficient operations and consistently deliver high-quality products to their customers that add value. In this environment, it's imperative that there is digital continuity throughout engineering and manufacturing value networks so that our customers can position themselves as market leaders.
To establish this continuity and collaboration platform, it's essential that these companies utilize a virtual twin and leverage it throughout the engineering and manufacturing operations lifecycle.
Adrian: Okay, thanks, Ron. What a cool topic! There are some buzz words, virtual twin. I know we'll have a lot more to say on that topic in a minute. But hold those thoughts later until we get more into a deep dive. Let me just switch to you, Liliane, because you're technically responsible for our high-tech manufacturing solutions as well as engaging with our customers just to ensure that these solutions we offer add value. So, from your perspective, how have we helped our customers achieve this symbiotic value network and digital continuity collaboration that Ron was just mentioning?
Liliane Sadler: Thank you for asking Adrian. There are many solution experiences that we offer to facilitate this business transformation, and also to leverage the design and manufacturing assets. First, we can improve the speed and efficiency of new product introductions by challenging companies to rethink the way they currently do their ramp up. Second, once the products are transitioned into high-speed production heights, we shift the focus to flawless manufacturing execution. And last, we focus on automation, acceleration and optimization by leveraging data intelligence, AI and feedback loops for more manufacturing efficiency and profitability.
Adrian: Okay great, thanks very much, Liliane. I can see the value in all three of those areas to establish this symbiotic value network. Let's talk a little bit more about the first level, which is rethinking your ramp-up as you said. So, the transition from engineering to manufacturing is especially critical in high-tech because of the pace of innovation and frequency of new product releases and changes. So how does Dassault Systèmes’ solution expedite the precision and speed that is needed in that early manufacturing phase?
Liliane: The creation of the virtual twin is really the key. It's not only the twin of the product but also of the process and all of the resources that are required to manufacture it. High-tech companies will either create the engineering design or engineering bill-of-material (E-BOM) within the 3DEXPERIENCE platform, or it may also come from another third-party design tool. And then the first step is to create, from this E-BOM, the virtual twin M-BOM to reflect accurately how the product will then be made. As I just mentioned, it is not only about the material structure or what you will build but also the structure of how it will be built. It is created in the 3D virtual twin, which is visualized throughout the creation.
It means that for each step of the manufacturing process, the parts, tools, fixtures, resources, skill levels and additional information about the process are defined so that you will have a complete manufacturing virtual twin.
Adrian: Okay, that makes sense. So, we have this virtual twin but how can the virtual twin be utilized for the smoother transition and to enable that faster ramp-up for manufacturing that we're talking about.
Liliane: This is where the true value of the virtual team is realized. Because you can virtually build the product, you can simulate everything about the manufacturing process before you ever have to actually build something in the factory. Essentially, it's built before you build it. All of these simulations can be done during the manufacturing process, on the assembly sequence and equipment operations to identify potential manufacturing issues like collisions, bottlenecks, performance and build rates. All this helps to reduce ramp-up time and improve quality, resulting in higher efficiency.
Adrian: Those are definitely significant benefits associated with the virtual twin. How else can the virtual twin be leveraged to improve the ramp-up and full-scale manufacturing operations execution?
Liliane: We only discussed the definition of the manufacturing process plan and routings so far. But another key manufacturing element is the creation of digital work instructions. At each operation step, the virtual twin automatically creates the initial build sequential 3D views, complete with the proper build stage of the product, tools, and resources. This will allow the manufacturing process planner to use it as a starting point. If needed, he can also add additional textual work instructions, quality notes, safety warnings, callouts or some graphics. In the end, the result is detailed 3D work instructions that clearly illustrate to the manufacturing operator how he will perform the tasks efficiently and right the first time.
Adrian: That's fantastic. With the virtual twin in the virtual world, we were able to solve all these problems and address all these challenges. Now, when we transition to actual manufacturing, Ron, we should expect flawless execution as well. Is that right?
Ron: Absolutely, yes. This is really the major reason and justification for investing the upfront effort in the virtual twin and maintaining it throughout the product lifecycle. For example, we have a customer, Panasonic Connect, and they've leveraged DELMIA to manage all of their unorganized data and analog information from their equipment. Their goal was to improve the manufacturing process. Now, this enabled them to track their overall factory line operation in real time and significantly reduce their overall workload, as well as remove several of their bottlenecks and increase throughput. They also reported to us that they were able to reduce the time taken to recognize issues in production and resolve them quickly.
Adrian: Okay, great. So, we're getting benefits on the virtual side from the virtual twin in pre-production, manufacturing process, engineering and virtual build. We're also getting the benefit on the execution side. But we could dive a little bit deeper into some of those value drivers that you mentioned. How are they getting some of those savings?
Ron: We'll start off with quality, which is one of my favorite areas. One of the outputs of the virtual twin is the process, failure, modes and effects analysis, or commonly referred to as the PFMEA. It's used to identify your potential failures that may result in any quality issues, scrap rework, losses in productivity or even safety events.
Adrian: Okay, so we can reduce some of the defects and increase quality in the virtual world. But obviously when we get to execution, there are obviously some things we can't plan for, so it sounds like that's a great way to prevent a lot of defects from happening in the first place. Even if we didn't catch them in the virtual world and then if they occur, we can ensure they are caught and resolved efficiently. There's a lot of automation that Panasonic Connect and other companies are doing. But of course, there's a lot of people involved as well. So, in high-tech, one of the biggest challenges for companies is finding and keeping a talented workforce. They end up having to bring in new employees sometimes who may not be as skilled. Is that addressed at all by leveraging the virtual twin in manufacturing?
Ron: It actually is. The training and ramp-up of the new employees as well as, like you mentioned, upscaling the existing workforce. It is improved by the utilization of the virtual twin in a couple of ways. First, the virtual twin can be used for virtual reality-based training before they start working in the factory in the first place. Then, once they start working in the factory as they come up to speed, augmented reality experiences can be used to step the operator through a specific task during the manufacturing process.
Now, the way this works is by utilizing the 3D model-based work instructions and content then superimposing or projecting it over the actual product that they're building. So, you can think of this as a virtual assistant that takes the guesswork out of the process and really makes the operator or the quality inspector more efficient.
Adrian: Who wouldn't want a virtual assistant in all their applications! That's a great application of leveraging the connection between the virtual and the real world, where the use of presumably handheld tablets, smart glasses and projection systems can bring that to fruition. Any other ways to leverage the virtual twin to help with flawless execution? Can we still improve beyond that?
Ron: Yes. As you know, the factory floor is a great source of process improvements, and it's critical that there's feedback to the appropriate team members in the manufacturing or the quality engineering group, whoever it may be. The DELMIA manufacturing operations management system allows the operators to take screenshots, mark them up or even go to the actual 3D model and make callouts on that model. All of this shop feedback can then be routed back to the appropriate group, where the progress is tracked throughout the complete process for transparency. The result is a robust, continuous improvement platform that ensures best practices are incorporated and used in the future. This really provides a closed-loop feedback process. It's not only within the companies’ four walls but can be extended to their suppliers, contractors and even OEMs.
Adrian: This goes straight to the heart of what we're talking about here – the symbiotic or what should be a symbiotic relationship and collaboration throughout the value chain between engineering and manufacturing for efficient operations and continuous improvement.
Adrian: So, now that we have manufacturing executing flawlessly, of course, life happens every day and nothing is ever what we expect, with a lot of disruptions. Let's shift a little bit on how to automate, accelerate and optimize our operations for improved efficiency and profitability. How do we do that? And why is there a need to do that?
Ron: Over time, there's a tremendous amount of data being gathered and captured in the manufacturing operations management system. This is valuable data, and it's a historical record of the product, process, equipment, people involved and environment itself. This data can not only be used for the as-built and traceability records, but it can also provide insights into the future. All of these actuals can be brought back into the virtual twin to make the model even closer to reality for better planning, simulation and ultimately execution.
Adrian: Okay, that's great. But as we execute, of course we all have a plan or we start with a plan, and that plan sometimes doesn't last very long, as real-life changes occur. A lot of companies talk about planning and scheduling the heartbeat of a digital factory. How does it also benefit from the synchronization with the actual production, with material and maintenance data that you said we can collect?
Ron: We still see a lot of customers relying on siloed scheduling systems or even manual offline spreadsheets to do their production scheduling, which is incredibly inefficient and suboptimal. But with Dassault Systèmes’ solution, the manufacturing operations execution, the production, planning, and the scheduling are all synchronized.
This allows your process planners to make faster and better decisions with more precision. And they're based on demand volatility, planned maintenance activities, material shortages, shop floor and even workforce issues as well as supply chain disruptions. All of this is achieved with world-class optimization based on real-time KPIs, consideration of multiple constraints and superior simulation capabilities for “what-if” analyses.
Adrian: And we've spoken about the benefits of the other areas. What kind of benefits have customers realized from the synchronization of planning and scheduling?
Liliane: I can answer this one, Adrian. We work with one of the world's leading manufacturers of thermal transfer ribbons that implemented DELMIA’s planning and scheduling solution to control customer lead times and maximize equipment uptime while reducing waste and stockouts. With our solutions, this customer succeeded in absorbing the increased workload without compromising customer service levels. They could also reduce lead times by over 60%. Their stock-out was reduced by 50% and they also reduced the time required for planning by 80% – that's amazing! And as more and more AI and machine learning is being utilized within our planning and scheduling solutions, these improvements are only going to get better.
Adrian: That's great to hear. Clearly, we've seen value in each of the different areas we've looked at. But we've also seen the ability across these values, the collaboration and symbiosis of these different solutions working together, and the closed loop and continuous improvement process, Ron that you mentioned. So, leveraging the virtual twin for the synchronization between manufacturing and engineering for long-term success is really how companies are going to drive competition in connected systems.
We have covered a lot of great information and savings and benefits from Dassault Systèmes’ high-tech solutions. Unfortunately, we’re out of time. I know we could speak for a lot longer. If any of you listening would like to learn more about our solutions or deep dive into any of these areas we've spoken about, the value that we deliver to our customers or how to start your journey of business transformation, please check out our website. Thank you very much for listening, and we look forward to talking to you again soon.
Learn more
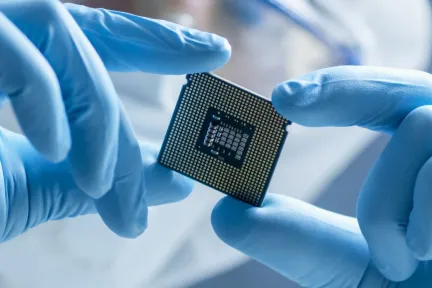
Deliver Innovative Market-Leading Electronic Experiences
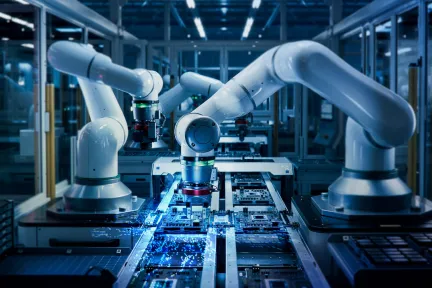
Leveraging Virtual Twins to Synchronize Manufacturing and Engineering to Accelerate Delivering Competitive Connected Devices and Systems.