Symetal
Symetal solves three complex planning puzzles with DELMIA Quintiq.
Produced in Greece for global use
Symetal S.A. is a highly export-oriented producer of aluminum foil and flexi-packaging materials. It provides diverse options to numerous companies, primarily in the food, tobacco and pharmaceutical sectors. Over 90% of its sales is to more than 60 countries in Europe, the Middle East, Africa, the Far East, America and Australia.
Symetal owns two production facilities outside Athens — a rolling plant in Oinofyta, Viotia and a converting plant in Mandra, Attica. The rolling plant produces plain aluminum foil in a wide range of thicknesses and alloys for various uses such as flexible packaging, pharmaceutical and semi-rigid containers. The annual capacity of the rolling plant is 52,000 tons and of the converting plant, 26,000 tons.
The converting plant receives foil produced by the rolling plant and puts it through paper laminating and lacquer coating. The processed foil is used in the food production and pharmaceutical industries. It is also used to make the inner lining of cigarettes.
In such a diverse production environment, maximizing plant performance is the key to Symetal meeting its profit goals as its operations grew. To safeguard its leading position in the market, it sought a world-class planning and scheduling solution.
DELMIA Quintiq’s implementation methodology was one of the critical success factors for our strategic initiative to re-engineer our production process. Our partnership with DELMIA Quintiq has brought Symetal and Elval great operational and business improvements, as well as industry recognition.
Delay to market caused by manufacturing bottlenecks
The processing of rolled aluminum products requires planning of various production flows such as casting, hot-rolling, cold-rolling and finishing to be both flexible and transparent. At the beginning of the project, Elval and Symetal were operating the entire supply chain for foil products, starting from slab production.
Planning was done manually using spreadsheets — time-consuming work that made creating what-if scenarios almost impossible. As a result, order planning and S&OP supply planning were not optimized and bottlenecks were formed. Slitting patterns were created manually and the ability to frequently review this complex puzzle was limited, which led to sub-optimal results.
The complex processes were giving planners multiple challenges, which impacted the quality of plans and affected production delivery to customers. Manufacturing lead time, inclusive of foil stock production, was too long. The market was increasingly demanding for swift deliveries and higher accuracy in order delivery performance.
To improve its business, Symetal outlined a few key objectives: Reduce manufacturing lead time, improve delivery performance, maximize production volume and reduce inventory. A more optimal product mix was also on the list as that would help increase the company’s profitability.
The critical search to increase competitiveness
DELMIA Quintiq was chosen to help Symetal achieve those goals based on a few factors:
- Deep knowledge of the aluminum industry. DELMIA Quintiq was set up 20 years ago to solve the planning puzzle of an aluminum hot mill operator. Planning for the aluminum industry remains one of DELMIA Quintiq’s core expertise
- Full coverage of planning processes, from scheduling and order planning, to slitting optimization and S&OP
- DELMIA Quintiq integrates seamlessly into Symetal’s existing IT environment with no complications or loss of data
At the top of the list in Symetal’s search for a solution was lead time reduction, which would help it increase on-time, in-full deliveries to customers. The goals to achieve were:
Scheduling, production planning and S&OP
- Reduce inventory and work in progress (WIP)
- Increase resource utilization (supply chain)
- Improve order fulfillment (company planning)
- Improve the bottom line and financial results (macro planning)
Slitting optimization
- Reduce scrap by finding better patterns and assigning new orders to existing patterns
- Increase flexibility by quickly assigning new orders to existing or new patterns
- Improve production efficiency by reducing knife settings
The routing puzzle
Processing rolled aluminum products requires planning of various production flows such as casting, hot-rolling, cold-rolling and finishing to be both flexible and transparent. It includes the various specifications, delivery due dates, constraints and shifting bottlenecks.
The DELMIA Quintiq solution maps each planning action. Different weights are assigned to different KPIs depending on what Symetal wants to focus on. Job orders are created by the routing generator. Visibility over different strategies lets planners compare the consequences of each strategy to decide on the most optimal plan.
Symetal is now able to provide the added value of flexibility to its customers. This covers time, alloys and quantities. The solution’s interface is built with the flexibility to accept multiple inputs of orders of various requirements. Using historical data in the routing library, the system creates pre-defined unique routes that can be used to produce final products with similar characteristics.
Symetal uses a make-to-order strategy, rather than a traditional make-to-stock strategy. However, the DELMIA Quintiq solution’s flexibility allows it to incorporate even last-minute orders into the production schedule by calculating when and where the order can best be inserted without affecting KPIs and the other orders already scheduled.
The DELMIA Quintiq optimizer comes up with a feasible production plan by taking material that can be spared from other orders in the workflow. Orders are mixed and matched according to alloy, temper, surface, thickness, width, due date, spool type, outer diameter, final length, and lubrication levels.
Manufacturing lead time took too long, including for foil stock, making it challenging to satisfy the market’s increasing demand for swift deliveries. By introducing intermediate stock, as well as taking advantage of the just-in-time algorithm offered by DELMIA Quintiq, Symetal was able to reduce manufacturing lead time to a few weeks and be competitive in the market.
The S&OP puzzle
Manual planning tools such as spreadsheets that Symetal relied on for its sales and operations were insufficient as business growth had increased the complexity of its operations. Its planning process now involves more input information and needs to consider more business constraints and goals. Symetal’s planning tools did not take into account multiple requirements such as price, capacity and sales forecasts.
Using DELMIA Quintiq, Symetal is able to create supply plans across multiple levels, from short-term quarterly forecasts for the continuous monitoring of market trends and best capacity utilization, to annual budgeting and strategic five-year analysis. DELMIA Quintiq gives Symetal full visibility so that the company can easily compare strategic business options by creating S&OP supply planning scenarios.
In 2015, Symetal won a Gold ranking in the BITE (Business IT Excellence) Awards for the macro planning implementation.
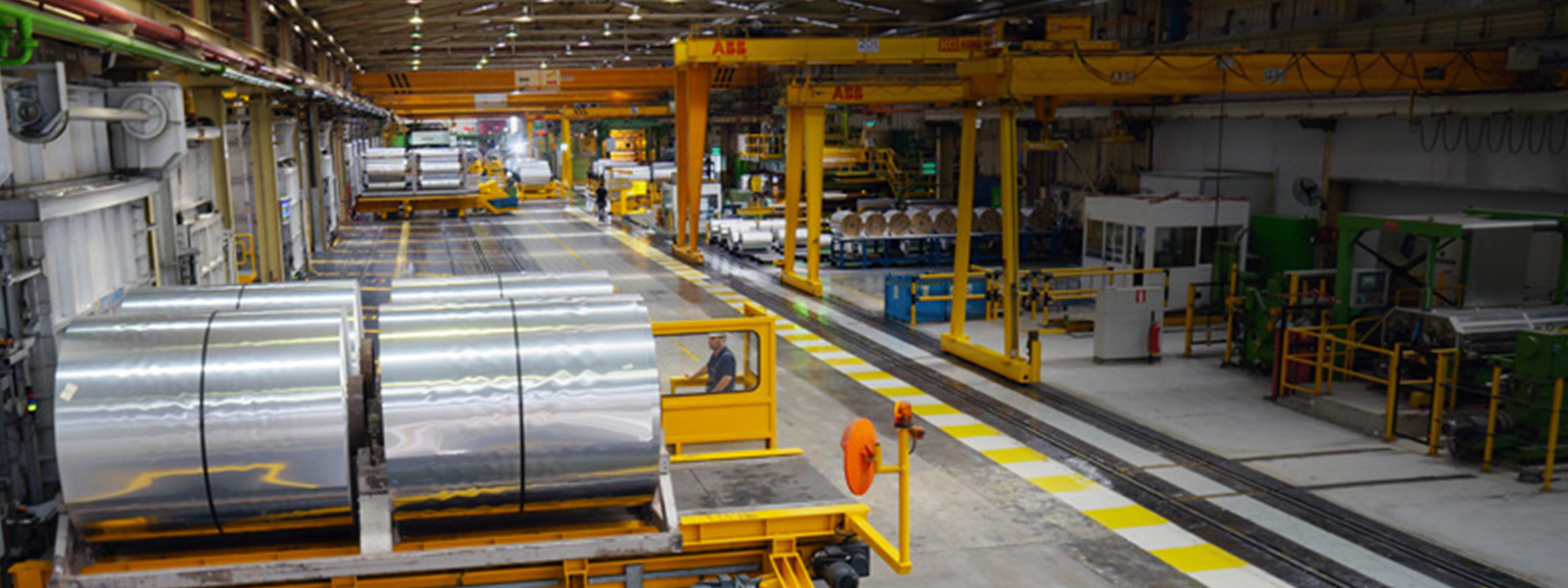
The slitting puzzle
Symetal’s challenge was how to maximize yield without losing flexibility. One cold rolled coil measuring 1 millimeter thick and 2 meters wide can produce more than 1,000 different final products. The complexity lies in different customers requiring different widths, thicknesses, alloys, tempering and other constraints.
The slitting optimizer finds the sweet spot where cost is balanced against what the customer wants and when. Symetal gains an understanding of the relationship between different KPIs, allowing it to select the best set of KPIs to execute. Various scenarios are compared to choose the most optimal plan that satisfies the company’s KPIs and customer’s expectations. This enables the company to give more reliable answers to customer requests.
Solving the slitting puzzle brings another business gain to Symetal — greater flexibility in processing customer orders that reduces scrap. Producing a customer’s order can result in different yields depending on when it is executed. For example, producing it next month could cost 100kg of scrap, whereas producing it two months later could cost only 20kg, depending on the scrap reduction that comes from making better combinations of orders on a coil.
The slitting optimizer reduced scrap returns significantly, making it possible for Symetal to have return on investment in less than one year. The Symetal Slitting Optimizer Project was awarded the Gold Prize in the 2017 BITE (Business IT Excellence) Awards.

Stakeholder background
Symetal is an Elval subsidiary, the major constituent of Viohalco’s aluminum manufacturing, processing and marketing segment. Viohalco S.A. is a Belgium based holding company of leading metal processing companies across Europe.
Symetal uses foil stock manufactured by Elval to produce aluminum foil and aluminum flexible-packaging materials. Both companies share a company planning and routing generation system.