SABCA
SABCA connects engineering and manufacturing with Engineered to Fly solution to master complex product assemblies, and streamline product data and workflows.
Actuation systems at the heart of aerospace performance
In the complex field of aerospace engineering, actuation systems are the vital muscles, joints and nerves that allow aircraft to fly. These sophisticated systems are found in nearly every moving part of an airplane, controlling essential components such as rudders, flaps, landing gear, brakes and doors, making them indispensable to an aircraft’s function and safety.
SABCA (Société Anonyme Belge de Constructions Aéronautiques) is at the forefront of this actuation technology. The Belgian company specializes in the development of hydraulic, electrohydraulic and electromechanical actuators for a wide range of aerospace applications serving companies like Airbus, Arianespace, the European Space Agency and Lockheed Martin. Its cutting-edge components and systems are found in everything from rockets to civil and defense aircrafts – contributing to their exceptional maneuverability and performance.
“Our mission is to design highly complex assemblies and structures, and to place them in any flying system,” said Miguel Laduron, CIO of Orizio Group, SABCA’s parent company.
Today, SABCA securely stores all the engineering and manufacturing data related to some of its major aircraft projects in Dassault Systèmes’ 3DEXPERIENCE® platform, both on premise and in the cloud. Part of a company-wide digital transformation, this move allows SABCA to manage all engineering bill of materials (eBOM) and manufacturing bill of materials (mBOM) within a centralized repository. This is reducing the time spent searching for data and fostering enhanced collaboration between engineering and manufacturing. In the longer term, the integration is expected to yield substantial improvements in productivity and innovation.
“One of our strengths is managing parallel processes, such as design, manufacturing engineering and production,” said Marten Venmans, director of engineering at SABCA. “By better connecting our processes in the 3DEXPERIENCE platform, we can speed up how we work and engage suppliers even before finalizing designs.”
It was essential to choose a state-of-the-art solution as it will be something we rely on for the next 10 years, or even longer. Dassault Systèmes’ platform was the most scalable and would give us the most scope for the future.
Overcoming inefficiencies with a connected PLM system
SABCA has relied on Dassault Systèmes solutions for over 20 years for all design and product lifecycle management (PLM). These solutions have been vital for its collaborations with aerospace industry leaders. Until recently, though, the company was hampered by communication barriers between design, engineering and manufacturing as each team used its own separate systems. When modifications were made, engineering teams struggled to pinpoint specific changes, and manufacturing found it increasingly challenging to identify impacted components. This disconnect led to inefficiencies and increased the chance of costly errors.
“The main challenge was linked to the fact that individuals didn’t have the same reference point,” Laduron said. “It became extremely complex when we made modifications; we spent a lot of time figuring out what needed to be changed and which elements were affected.”
To address these issues, SABCA sought a holistic approach and decided to upgrade from its CATIA V5 and ENOVIA VPM solutions to the 3DEXPERIENCE platform. The company feels confident that Dassault Systèmes offers the most advanced, sustainable solution suitable for its long-term needs.
“It was essential to choose a state-of-the-art solution as it will be something we rely on for the next 10 years, or even longer,” Laduron said. “Dassault Systèmes’ platform was the most scalable and would give us the most scope for the future.”
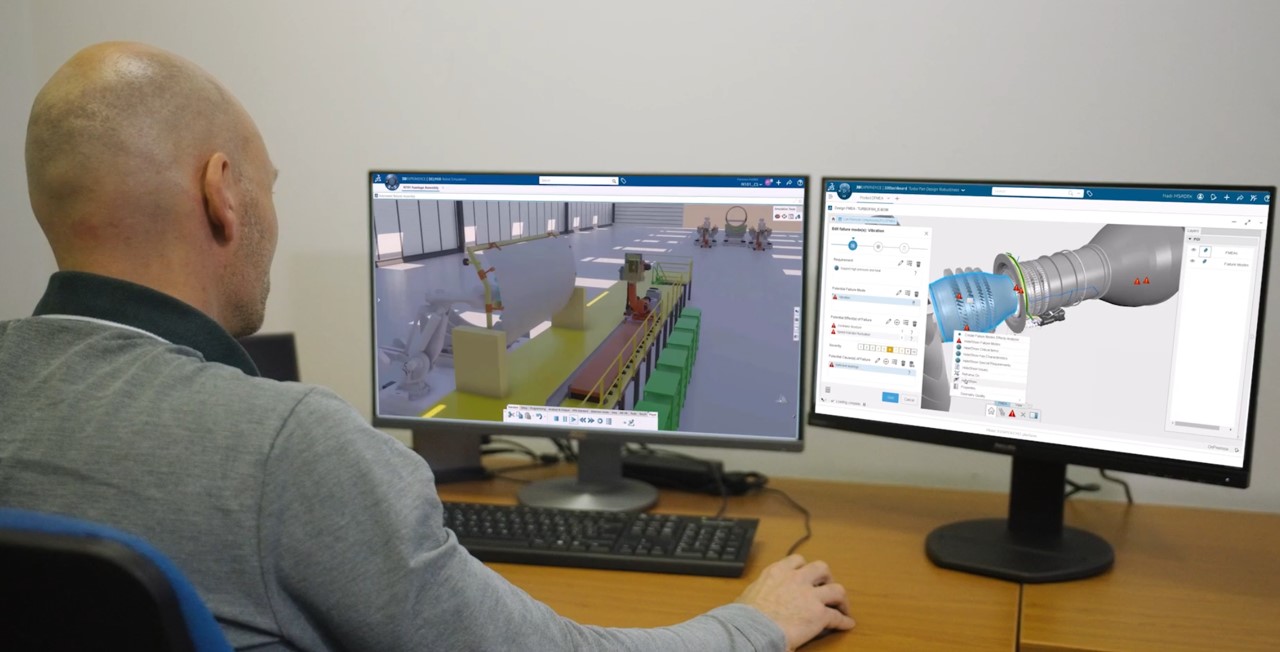
Integrating engineering and manufacturing
By adopting Dassault Systèmes’ platform, SABCA has made it easier for its engineering and manufacturing teams to work together, centralizing workflows and simplifying access to critical information. Now, engineers can focus on core tasks – developing highly complex assemblies that meet customers’ unique requirements.
“The 3DEXPERIENCE platform is a next-generation PLM system that enables us to take on a more comprehensive approach than our legacy system,” Venmans said. “One of its significant advantages is integration, particularly with our major design tools. It allows us to interface with our customers’ databases as well as our manufacturing plants, and facilitates a continuous digital thread, especially between manufacturing engineering and production.”
With 3D at the heart of its operations, SABCA is better equipped to streamline its development processes. It is also positioned to attract – and retain – talent drawn to the platform’s sophisticated yet intuitive and versatile features.
“We hope that using the 3DEXPERIENCE will support us to attract young talent because it is an attractive platform that has all the qualities found in the latest mobile app interfaces.”
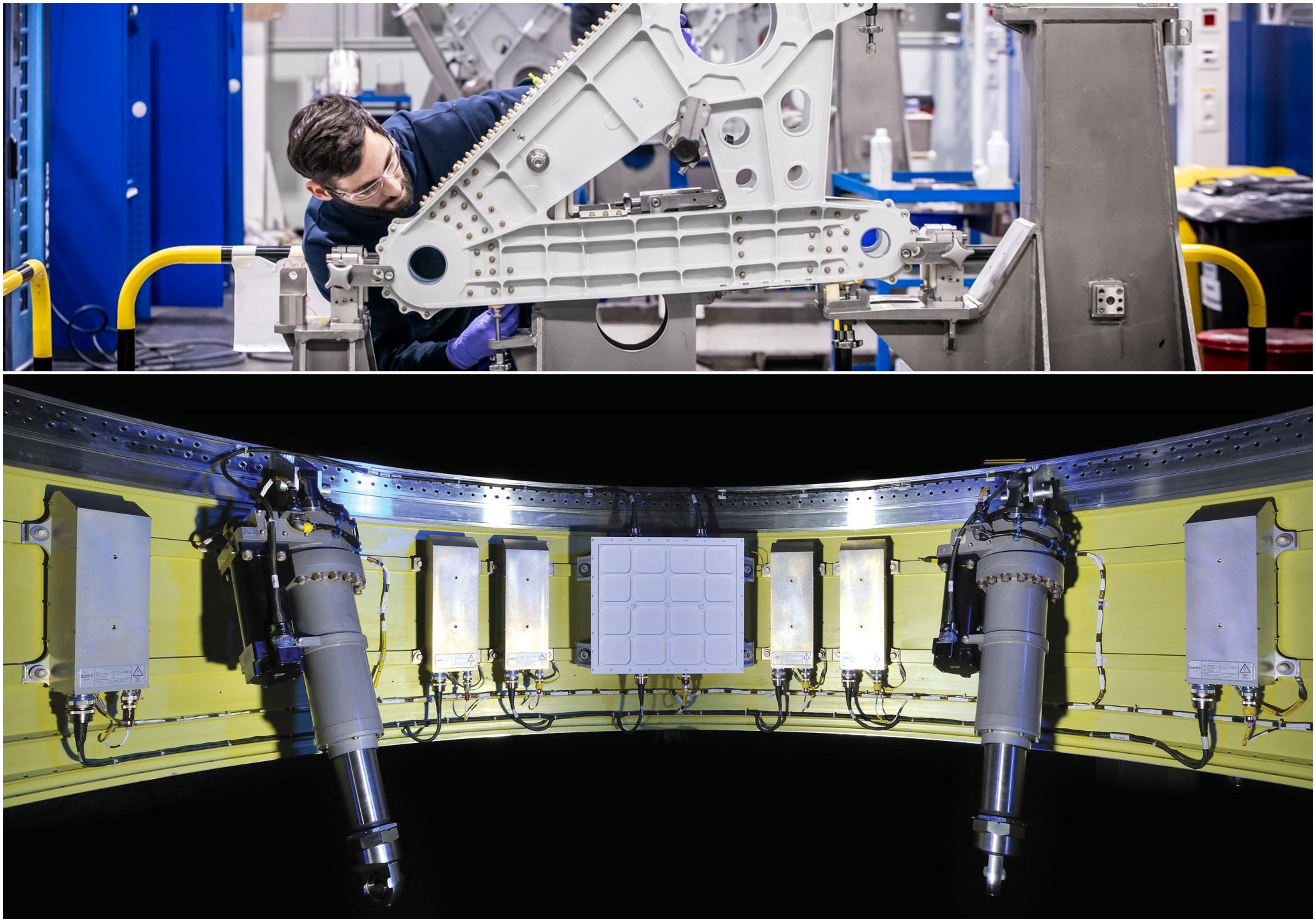
Exploring the virtual twin capabilities
Looking ahead, SABCA plans to use more of Dassault Systèmes’ virtual twin capabilities to model and optimize its plants and all manufacturing operations. With the virtual twin, the company will be able to simulate different scenarios, incorporate live data from the shop floor and effectively plan its workflows to boost production capacity.
“Virtual twins are a powerful tool, particularly for testing manufacturing processes and avoiding errors before transitioning to the physical world,” Venmans said. “We already use virtual twins in some processes to improve our first-time-right ratio.”
“As we continue to explore the potential of the virtual twin, it will allow us to prepare our factory for new assemblies, while also capturing feedback from the shop floor to compare real-world results with what the virtual twin predicted,” Laduron added. “It will be a cornerstone of how we operate.”
Sustainable aerospace ambitions
As the aerospace industry moves toward sustainable aircraft powered by carbon-free, renewable energy, SABCA is pioneering a new generation of electric actuators that are lighter and consume less energy than traditional hydraulic systems. This cutting-edge technology not only improves performance but also enhances reliability and is expected to play a critical role in the next era of aviation.
“The technology originates from our work in the space sector, where we developed electromechanical actuators for the Ariane 5, Ariane 6, and Vega rockets,” Laduron said. “Now, we’re collaborating with Airbus to integrate these advanced actuators into aircraft, and we handle all product development with the 3DEXPERIENCE platform.”
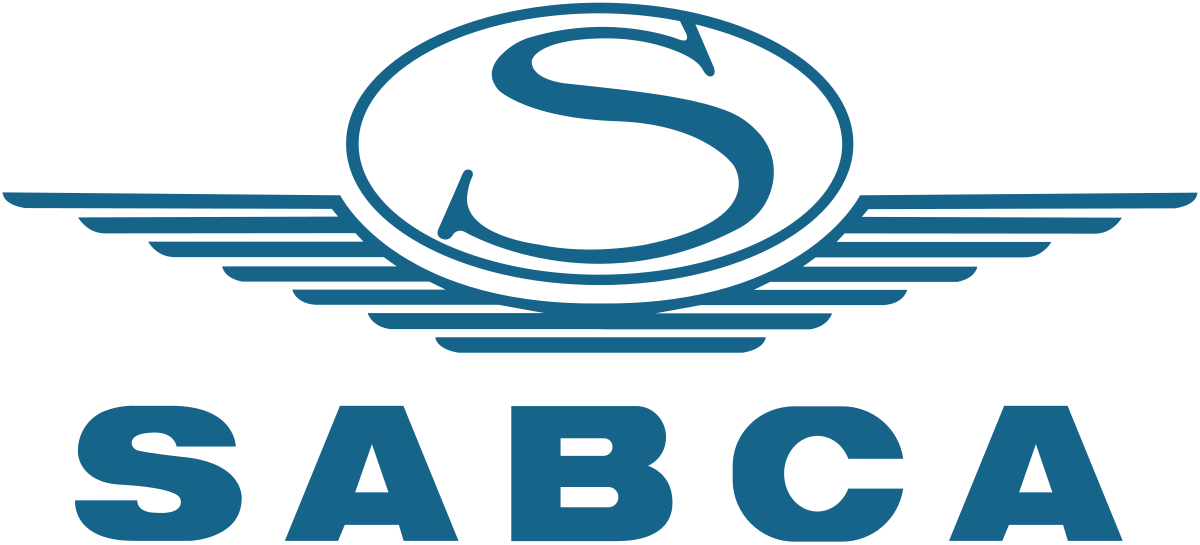
Focus on SABCA
The SABCA Group has operations in three Belgian regions (Brussels-Capital Region, Louvain la Neuve – SABCA Technologies – in Wallonia and Lummen in Flanders) and Casablanca, Morocco. With over 100 years of experience, the company has developed a wide range of expertise in the design, manufacture and maintenance of large structural components for aircraft and space launchers as well as actuation systems. Its customers and partners are among the elite of the aerospace industry. SABCA offers a full range of services to the civil, space and military aviation markets, and has recently expanded into the commercial autonomous unmanned systems market as an integrator of aerospace solutions for industry.
For more information: http://www.sabca.be/

Focus on Visiativ Benelux
A subsidiary of Visiativ Group with 25 years of customer experience, Visiativ Benelux enables industrial companies to drive innovation, increase efficiency, reduce costs and improve quality through the integration and resourceful use of innovative technology solutions. It delivers tailor-made support to businesses, helping to facilitate their digital transformation and build new experiences for their entire ecosystem.
For more information: https://www.visiativ.nl or https://www.visiativ.be
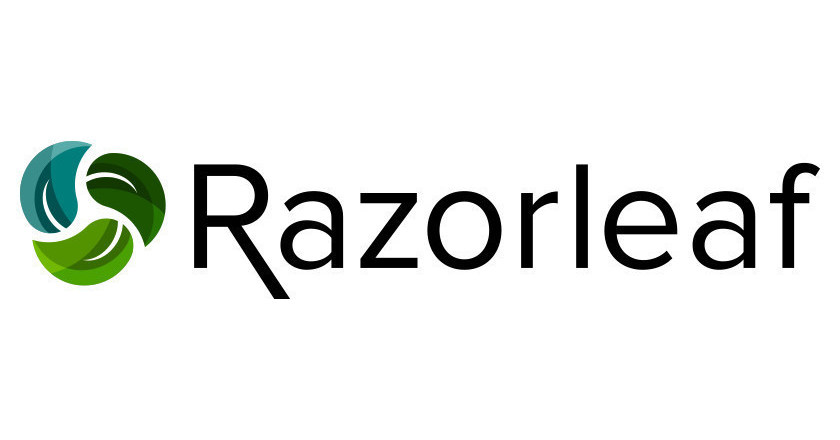
Focus on Razorleaf
Razorleaf is a consulting and systems integration firm specializing in digital technologies designed to help the world’s most innovative manufacturing organizations bring new products to market. The company partners with clients to connect products and processes across the enterprise, driving greater business value. Razorleaf is recognized for its highly skilled and experienced team of consultants, now located across the globe.
For more information: https://www.razorleaf.com/