National Institute for Aviation Research
Supported by the Keep Them Operating industry solution experience on the 3DEXPERIENCE platform, NIAR will take the B-1 Lancer aircraft completely apart, scan every single structural element and digitally reassemble the aircraft to create virtual twins for future sustainment activities. The platform serves as the hub for visualizing, analyzing and predicting the aircrafts’ performance.
Virtual twins keep aircraft mission ready
The B-1 Lancer has been a strategic military aircraft for the US since the 1980s. But after years of heavy use in combat, much of the fleet is retired and the remainder in service face issues around structural fatigue and part obsolescence. In 2017, the B-1’s mission readiness was less than 53%, which spurred a call to action by former US Secretary of Defense James Mattis to be 80% mission ready. Now under tight restrictions in terms of how and how often they can fly during training and live operations, it has become a matter of national security to get more of the aircraft mission ready.
That’s why the US Air Force has given NIAR the mammoth task of dismantling, cataloging and scanning every single part of the strategic aircraft to create a full-scale, operational virtual twin. The program will provide the US Air Force with unprecedented information on the B-1 and promises to revolutionize the way the government procures replacement parts and keeps aircraft mission ready.
A retired B1 Lancer is now in a hangar at the National Institute for Aviation Research (NIAR) at Wichita State University (WSU). This particular B-1 airframe will never fly again, but a full-scale, 3D virtual twin of it will, within the virtual environment of Dassault Systèmes' 3DEXPERIENCE® platform.
More than 250 engineers and students at the university are already working on the project, carefully taking the airframe apart piece by piece. Eventually, NIAR plans to have more than 350 people involved in the virtual 3D reconstruction: scanning each piece, creating detailed CAD models of every part and digitally reassembling the full aircraft, all managed using the 3DEXPERIENCE platform.
Virtual twin technology is still pretty young, but the 3DEXPERIENCE platform provides all the capabilities we need to bring this virtual aircraft to life.
“NIAR was selected as we have a unique set up here and we have the ability to handle every stage of the virtual twin program,” said Melinda Laubach-Hock, director of sustainment at NIAR and NIAR B-1 program manager. “Other facilities may have modelers, scanners and tear down personnel, but we have all of that under one roof. The scale at which we can do this is what differentiates us; we have industrialized the virtual twin process. We have a history of doing military sustainment aircraft and virtual twin work so the US Air Force felt comfortable that we would be capable of handling a project of this scale.”
These types of programs are central to NIAR’s commitment to enhance education with hands-on learning and advance the nation’s aviation industry.
“We’re proud of the applied learning the students are getting from working on this project,” Laubach-Hock said. “They leave us with two to four years of real-world experience and are immediately productive in the 3DEXPERIENCE platform when they join the workforce.”
Extending the lifespan of the B-1
The B-1 is an ideal candidate for virtual twin technology. As an airframe designed before the digital age, there is no living record of the complete design. By developing a 3D virtual twin, engineers will inspect the B1 for structural damage, incorporate any known maintenance data or fleet inspection results, and develop predictive analytical tools to identify issues before they arise in the fleet to manage effectively the aircraft for the rest of its lifecycle. A virtual twin also allows for testing prototypes of new parts and repairs, and even supports a change in mission by understanding the impact the new mission may have on the life of the particular B1.
“One of the reasons the B-1 emerged as a candidate for this technology to make the most impact is when it first went into service, it didn’t have a full-scale structural test, which meant that the program officers managed it reactively,” Laubach-Hock said. “They don’t have a good predictor of where the damage is going to occur on the airframe and what impact it could have on the airworthiness of the fleet. They’re also looking to use the B-1 to perform different missions. So, we’re taking an airframe that was supposed to last a certain number of years, we’re extending its lifespan further and we’re increasing its mission readiness and capabilities. This is the perfect time for us take advantage of new technology to give them the data they need to make all these things happen.”
NIAR is an expert in virtual twin technology and a user of the 3DEXPERIENCE platform since 2016 and CATIA for design since the 1990’s. In April of 2017, NIAR and Dassault Systèmes opened the 3DEXPERIENCE Center on the WSU Innovation Campus.
“Virtual twin technology is still pretty young, but the 3DEXPERIENCE platform provides all the capabilities we need to bring this virtual aircraft to life,” Laubach-Hock said. “I think we’re hitting the apex for its adoption as we have the technology available and the need is clearly defined—that’s why we’re at the point where we are now.”
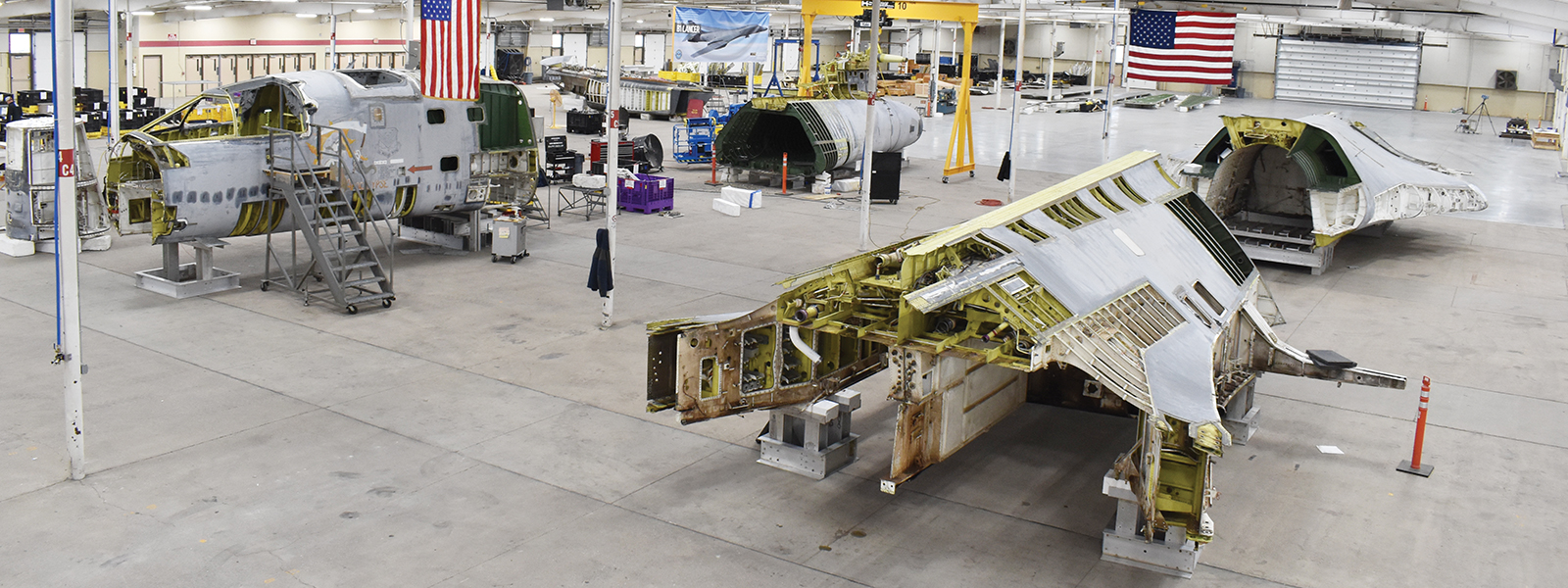
Keeping track of all parts
Before NIAR develops the virtual twin of the B-1, it must first disassemble the entire aircraft and track every piece along the way.
“To the extent of what we have to scan, when we have to scan it and how we coordinate that with the tear-down and reverse engineering group, we’ve learned a lot from previous programs we’ve managed about how to do this most effectively and be successful on a large-scale program like this,” said Shawn Ehrstein, director of Emerging Technologies and CAD/CAM at WSU-NIAR. “The tear-down group has to track everything that comes off the airplane as part of the reverse engineering process. For this particular program, we’ve reformulated what we do and we’re constantly enhancing our approach.”
Additionally, NIAR is taking steps to familiarize itself with the airframe structure before taking it apart, and developing the B-1’s virtual product structure in advance to ensure nothing gets missed.
As we build the virtual model, we’ll take advantage of most aspects of the Keep Them Operating solution to ensure that the structure and function we’re building aligns with modern design principles.
“We will use the 3DEXPERIENCE platform to establish the entire product structure ahead of time, so we know how everything fits together in the system,” Ehrstein said. “It will allow us to track all the parts and see their status. We’ll have different dashboards to see what’s in work, in check and released, and use the routing capabilities of the platform to control our release process. All of these modeling, product structure and data management processes will be managed through ENOVIA on the 3DEXPERIENCE platform.”
Even if a part does go missing or was never there in the first place, NIAR will use the virtual model to build a complete picture.
“We’re talking about tens of thousands of individual parts that need to be tracked at all points in time,” Laubach-Hock said. “If something is lost along the way, we can compare against what should be there. And sometimes with these legacy platforms we just don’t get a certain part in the first place. It allows us to identify and fill holes in the airframe data.”
“As the project progresses, the platform will also help with design revision control,” Ehrstein said.
Data-driven smart sustainment
Being able to manage the form, fit and function of the B-1 and correlate the physical condition of the aircraft with the virtual experience will transform the way the US Air Force manages its fleet going forward. This high-fidelity engineering model will validate stress and strain data against the real aircraft, which can be used to determine the mission impact on each operational B-1 from a corrosion, fatigue and fracture perspective. Using this feedback, it will be possible to determine mission life degradation as well as which parts may need to be proactively investigated and replaced.
“The pool of aircraft we can pull from to perform a mission today is small, but through this virtual twin project we hope to improve the B-1’s mission readiness,” Ehrstein said. “These aircraft are very old and must survive longer than they’re intended to. There are issues with getting replacement parts because there’s not a lot of existing inventory out there. This is compounded by the fact that all these parts were initially developed in a 2D format. If you need one part and you send it out for a bid, finding someone to take a 2D drawing and make a 3D model for it is challenging. It would require too much effort.”
The virtual twin allows access to a full 3D representation of all parts, which makes it easier for the government to replace a part themselves or more easily find a manufacturer to produce it for them.
“For small tweaks that are low risk, the government can do their own engineering analysis and part sourcing work without going back to the original equipment manufacturer,” Laubach-Hock said. “The real advantage of the 3DEXPERIENCE platform is not just the 3D modeling; we’re going to create a single repository for all of the analysis being done on the B1 program. Right now, the government has different systems all over the place and keeping track of the latest version and who has it has been hugely challenging. The platform will change that.”
Additionally, the US Air Force has proposed specific repairs for the B-1, but it relies on legacy drawings, which are not the most legible and can lead to costly mistakes.
“There are some parts on the aircraft that you can’t get anymore, so the B-1 office also wants to explore advanced and additive manufacturing to find new ways of replacing those parts,” Laubach-Hock said. “To do this, it will need all the engineering data from the virtual twin. It can also begin to explore how to take advantage of new technology, such as laser paint removal and additive manufacturing, to enhance sustainment. At the moment, the data to assess the risks and understand how this technology can be used doesn’t exist.”
“The government will have the data and 3D models to work off and determine if the airframe can handle the types of changes it wants to do,” Ehrstein said. “It can test it out virtually instead of potentially damaging the small amount of existing inventory left, making sure that any changes will be successful. To take advantage of smart sustainment, you need digital data. You can’t do this type of thing with legacy drawings. You need 3D models to manage inspections, modifications, enhancements, stress levels, new manufacturing methods, new training methods and work instructions. We are building the core package that allows you to take those next steps.”
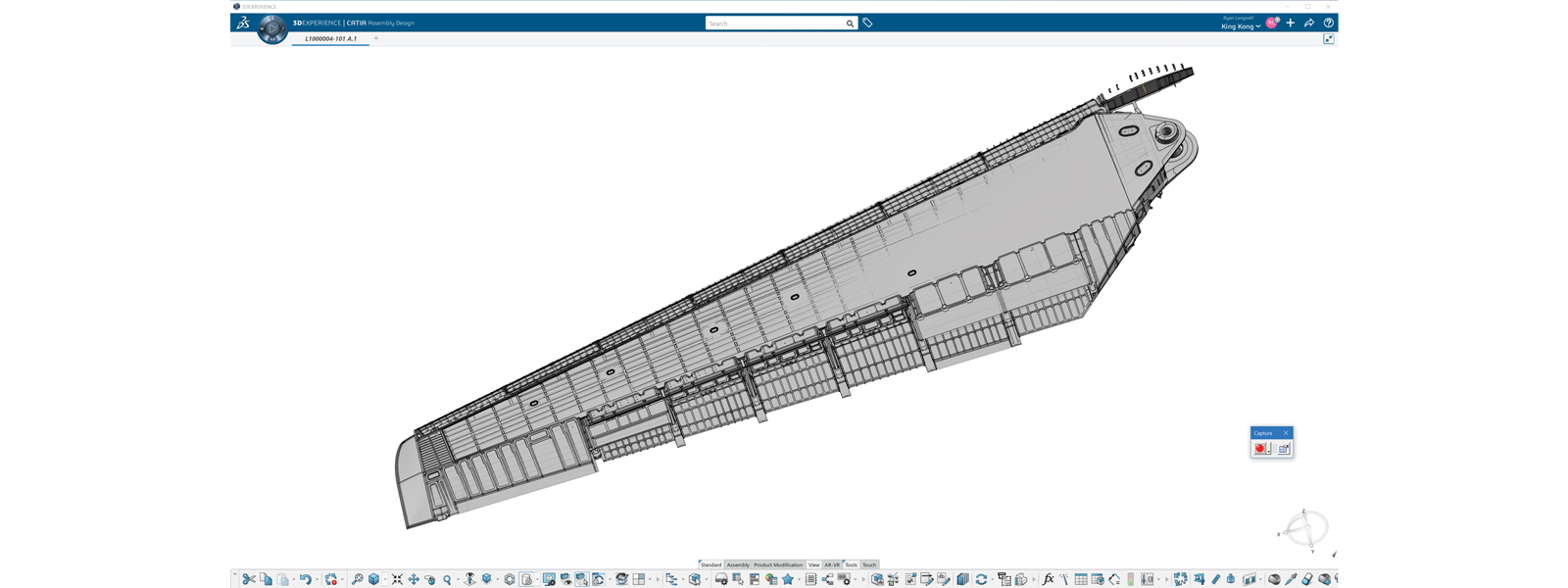
Embracing a modern, 3D approach
“As we build the virtual model, we’ll take advantage of most aspects of the Keep Them Operating solution to ensure that the structure and function we’re building aligns with modern design principles,” Ehrstein said. “Within the platform, we’ll be able to take the master digital build and begin to track all the maintenance activities of every part, track flight hours within the system—all those capabilities are there to help keep the aircraft running sustainably.”
In the future, the US government will be able to use the virtual twin to manage full digital engineering.
“It could do system work, look at additive manufacturing processes, build work-based instructions for new maintenance activities—there are all kinds of avenues the government can explore from the virtual twin on the 3DEXPERIENCE platform,” Ehrstein said. “We’re going to show them how they can use all of this data.”
While this project specifically involves the B-1 Lancer, it will serve as a pilot for the development and validation of a wider virtual twin strategy to support similar legacy aircraft and modern fleets, too.
“If the government wants to implement a change on a newly manufactured airframe, there’s a lot of lessons learned that we’re gaining from this project that we won’t have to relearn,” Laubach-Hock said. “This program is preparing the government to handle new data and embrace a new way of doing things digitally.”

Focus on NIAR
Wichita State University (WSU) is a US public state university dedicated to the applied learning and research model. As the university-based aviation research center at WSU, NIAR’s mission is to conduct research, transfer technology and enhance education for the purpose of advancing the nation’s aviation industry.
For more information
www.wichita.edu/research/NIAR