MG McGrath
MG McGrath chose Dassault Systèmes’ 3DEXPERIENCE platform and Design for Fabrication industry solution experience on cloud to streamline its concept to fabrication process.
A culture of excellence
An award-winning leader in the architectural surfaces industry, MG McGrath designs, fabricates and installs innovative architectural glass, metal and composite surfaces and systems for industrial and commercial buildings. MG McGrath’s most precious asset is its people and their commitment to excellence and innovation on every project. Through their skill, knowledge and experience, they make the impossible a reality every day.
“Our clients select us because of our attention to detail and our ability to find solutions to any issues that might come up,” Mike McGrath, president at MG McGrath, said. “We work together with our clients as partners throughout the entire process. It’s this can-do attitude and partnership mentality that differentiates us from our competition.”
Complex problems, simple solution
New building projects involve an aesthetic aspect that push architects to propose increasingly audacious designs, built in unprecedented time, to win new business. MG McGrath is familiar with this trend to increase quality and scope but still save on cost and time.
“Structures are becoming more complex,” McGrath said. “As a result, our clients, who may be construction managers, general contractors or building owners, challenge us to do things that are unique and that have never been done before. At the same time, however, they want the finished product faster and at the lowest possible cost. What is expected of us has evolved compared to 10 to 15 years ago
“Today, quality and scope must be greater than cost and time,” McGrath continued. “It’s a more difficult challenge. The only constant is our desire to maintain our reputation for quality and not lose sight of our values, which is placing our faith in our employees’ ability to get the job done successfully no matter how complex.”
Due to the evolution in architectural challenges, MG McGrath decided to digitally transform its design to fabrication process to enhance the experience of its clients and employees alike by engaging in 3D modeling to enable greater precision and control. With a model-based process, the 3D model can feed not only the design and engineering phases but also installation, coordination and procurement throughout the entire project.
As a successful user of Dassault Systèmes’ CATIA application for over a decade, MG McGrath decided to go one step further by adopting the 3DEXPERIENCE® platform on cloud and Design for Fabrication industry solution experience to streamline development from concept to fabrication.
“We chose the Dassault Systèmes’ solutions after vetting several different types of software and platforms and believe that there isn’t any other software out there today that can do what the 3DEXPERIENCE applications can do,” McGrath said. “We have a more user-friendly and robust solution, and one we are excited to use to push our creative limits further. Moreover, with the cloud, we have less IT infrastructure costs. And since we travel nationally and have workers in craft all over the United States, they can access data on the cloud from wherever they are located.”
Unique iconic structure
One of MG McGrath’s recent projects is in the foothills of Pike’s Peak in Colorado Springs – a 60,000-square-foot structure that will house the United States Olympic Museum (USOM), including the United States Olympic Hall of Fame, a highly interactive exhibit space, a state-of-the-art theater, café, gift shop and broadcast studio.
“What makes the U.S. Olympic Museum unique is its purpose,” Lee Pepin, director of virtual design and construction at MG McGrath, said. “Each Olympic athlete is unique. The architect, general contractor and MG McGrath want this building to stand out as much as each one of those one-of-a-kind athletes. You’ll see these beautiful triangulated surfaces and diamonds on the surface with a breathtaking landscape and mountainous ranges behind it. We want to make sure that the total effect, when you walk up to that building, is one of ‘wow, this is amazing.’”
When MG McGrath was chosen as the façade surface fabricator for the USOM, it knew that the 3DEXPERIENCE platform was the right solution for the project.
“Anytime we can be part of an iconic structure like this, something that’s going to be around for years to come, is significant and impactful,” McGrath said. “There’s not a single panel on the entire project that has the same size or the same geometry. For instance, there are more than 9,000 shingles on the building with different constraints and we just can’t see another way that we could execute the project without the 3DEXPERIENCE platform.”
“The building is very unique – the structural steel in and of itself, the curvature, the geometry of the building,” said John McCorkle, construction manager at GE Johnson Construction Company, who is working with MG McGrath on the USOM. “We faced a lot of challenges on the coordination, so using the software to mitigate and achieve our one-sixteenth-inch tolerance on the metal panels that we ultimately have was absolutely critical.”
Simplifying decision-making
MG McGrath leverages the power and flexibility of Design for Fabrication to design and fabricate the metal panel and facade system as well as the curtain wall and storefronts for the USOM.
“Through the pre-construction phase, we’re able to quickly run through various design iterations as to how the facade will look and then work through the selected design to come to a finished product that we’re seeing virtually first and then implementing in the field,” Pepin said. “We use the platform to give the architect and general contractor something tangible to look at in the model space so that they can go through, zoom around and see what they do and do not like. It’s a smooth back and forth process that simplifies decision-making.
“Moreover, because data is updated live as designs are modified, we don’t need to worry about working on outdated information,” Pepin continued. “With ENOVIA, every stakeholder from design to project management to fabrication to field installation can access the model, collect points and pull dimensions, all from a single source of information. It’s a seamless chain all the way through.”
“Prior to using the 3DEXPERIENCE platform, we spent a lot of time dealing with files and making sure everyone had the same information and working off the most current project data,” Neil Meredith, virtual design and construction at MG McGrath, said. “With ENOVIA, that’s gone away and we can largely focus on what’s going on within the project in terms of content and not have to worry about if stakeholders have the most up-to-date files.”
New capabilities, clearer understanding
Adding to the increase of virtual visualization, the MG McGrath engineers used the sheet metal tools available on the 3DEXPERIENCE platform for the first time on the USOM project, and they are already experiencing the benefits.
“The sheet metal applications are a huge differentiator compared to what we were able to do in the past,” Meredith said. “For example, seeing a corner in 3D and the way all the conditions and corners come together is something we’ve never been able to visualize at scale across an entire building. We only really get down to that level of detail if we build a physical mockup, so that’s been a big advantage. Moreover, using the sheet metal tools to rapidly detail and define the geometry and obtain a coordinated unfolded pattern for production has been really great.”
“Virtually being able to build the panels and having very tight control over all the geometry for the entire project cuts out a whole loop or loops of creating, testing, physically fabricating, and then, unfortunately throwing out material every time,” McGrath said. “Additionally, visualizing the skin with a high degree of definition in 3D has given the owner a more handson approach to the skin’s design, which not only helped us resolve several conflicts early, but also calmed a lot of his concerns because it gave him confidence in the end result.”
“We’ve been working with McGrath since the beginning of the [USOM] project,” said GE Johnson’s McCorkle. “Without McGrath and without CATIA, the project schedule would have been significantly extended while working through all the coordination issues.”
The communication has not only improved with the external stakeholders, but also on the shop floor where MG McGrath is realizing time-saving results. For the users who do not know how to use CATIA, they can still open and review models, take sections and analyze digital mockups with ENOVIA Design Reviewer on the platform.
“We’ve also been able to shorten the amount of time spent during fabrication by providing the shop floor with 3D models that are clearer and easier to understand than text-based documents,” Meredith said. “A lot of time and effort goes into making very clear documentation. However, providing the actual models to the shop floor allows those fabricating and assembling components to easily understand how they’re put together.”
Meredith shares, “Historically, we’ve used CATIA because it’s the strongest 3D engine able to handle these complex designs, but now there’s all this other information that we’re able to access. ENOVIA has really opened up some new ways of using existing information that’s already there within a project.”
For instance, when designing, detailing and working through the specifics of a building, a wealth of information is stored on the 3DEXPERIENCE platform and accessible through a web browser to different user profiles who didn’t have access to that information before.
“Project stakeholders use dashboards to obtain essential project information such as how much raw material might be needed or how many pieces were fabricated,” Meredith said. “Each user can customize their dashboard to focus only on the information that is important to them. It gives them a clear visual description of the status of things within the project, which is a very powerful communication tool.”
Recycling knowledge
Another way to save time and share knowledge through the CATIA application is by MG McGrath designers creating generic component templates to be reused and adapted in future projects.
“It’s not just one template for a specific challenge but a solution for several challenges that we might encounter in years to come,” McGrath said. “The 3DEXPERIENCE platform, hence, has allowed us to offer more custom solutions at a much more affordable price. Yet another advantage to using the platform is the ability to automate our processes, which strips out a lot of the repetitive work.”
For example, instead of modeling 10,000 pieces by hand, MG McGrath uses CATIA Template Designer and the Enterprise Knowledge Language, to perform repetitive tasks for them. “Furthermore, once a process or a workflow is automated, we can make changes quickly because we’re not worried about throwing out or losing that work,” Meredith said. “We are confident that we can get the same results we need for fabrication and construction thanks to the automated process.”
Accomplishing more
“I think the biggest business impact of the 3DEXPERIENCE platform has been to allow us to do things that we probably would have never been able to accomplish before,” McGrath said. “Without it, our work would be so labor-intensive that we would never be competitive today. For example, 15 to 20 years ago, we spent hundreds of hours manually laying out complex pieces or components on the shop floor. Today, in a matter of hours, we can do the same thing. We can quickly provide feedback as it relates to constructability of different sorts of geometries and surfaces because the software allows us to analyze the geometry to a more granular level. 3DEXPERIENCE has really reshaped the way we interface with our various stakeholders.”
It is a delicate balance but MG McGrath has complemented it most precious asset – its people – with a very capable solution to further expand its possibilities.
“In the future, we hope to really push technology further to maximize it to its greatest extent possible,” McGrath said. “Hopefully we will continue to grow our capabilities by utilizing the 3DEXPERIENCE technology to make our processes even more efficient.”
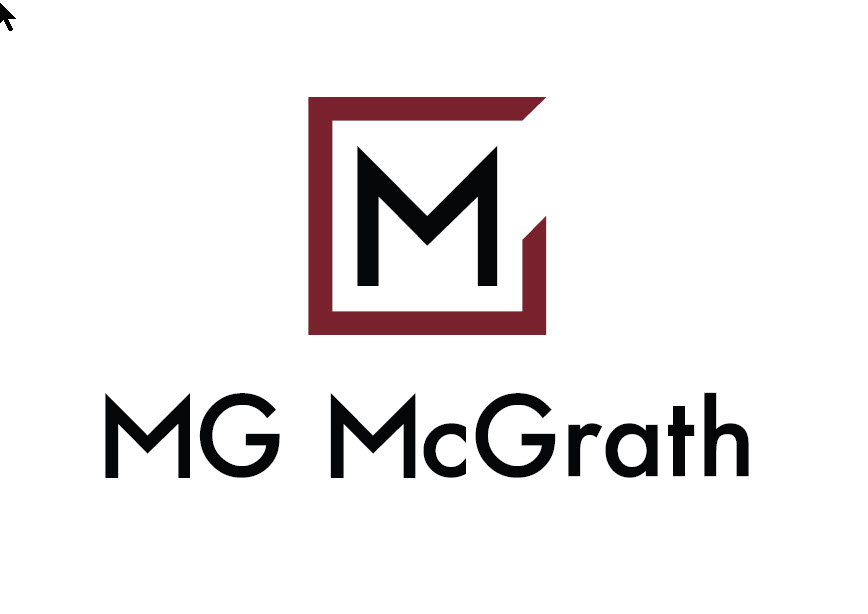
Focus on MG McGrath
MG McGrath is an award-winner and leader in the industry;providing creative solutions in design, fabrication, and installation of architectural surfaces.
Product: Glass and metal panels, classic glazing, curtain wall, high-end art sculptures, patina fi nishes.
Employees: 250
Headquarters: Maplewood, Minnesota, USA
For more information: www.mgmcgrath.com