Georgia Institute of Technology
As the backbone for its virtual prototyping environment, the lab used the Dassault Systèmes’ Winning Program Industry Solution Experience, part of the 3DEXPERIENCE® platform, including the CATIA, ENOVIA, SIMULIA and 3DVIA applications.
Harsh environmental conditions and unknown territory often put the safety of soldiers at risk during warfare or peacekeeping missions. Whether gathering pertinent intelligence during a reconnaissance mission or escorting soldiers through an unfamiliar building, drones or unmanned aerial systems (UASs) have proven to be useful and lifesaving due to their size, stealth and ability to fly with a human pilot safely navigating by remote control on the ground.
“Systems, such as UASs, have become more complex because they are required to do more and to operate under increasingly changing and challenging conditions,” said Simon Briceno, research engineer at the Aerospace Systems Design Lab (ASDL) at the Georgia Institute of Technology. “The environments in which drones evolve – from flying inside buildings or out in the open in enemy territory – require systems with a high degree of adaptability, which has increased risk and development time to unacceptable levels over the past 50 years.”
As a complex system, a UAS consists of many components with numerous interactions between these components that dictate the behavior of the system as a whole. Since thousands of situations exist for which thousands of drone configurations can respond, Briceno and his students at ASDL wanted to bring more information, more knowledge and more detailed aspects of those conditions into the concept phase prior to physical prototyping to save time and cost.
“Past methods of building and testing physical prototypes for each design are just too expensive and time consuming,” said Briceno. “We needed to reduce the design, integration and testing time of UASs. The way we do this is by creating, analyzing and testing our design and behavior in a virtual environment.”
Sponsored by the U.S. Army Research Laboratory, ASDL aimed to develop a UAS to relay real-time intelligence at a squad level. Working with other academic and industrial research organizations, ASDL created a virtual prototyping framework to integrate a series of multi-disciplinary tools for designing, simulating, analyzing and predicting behavior for one or more UASs in a very large concept space and for a variety of missions. However, the team’s challenge was to execute the framework in an efficient manner and establish traceability of requirements.
As systems make up the products, it’s very important that we don’t just think about shape but we also consider the complexity of the systems and how they fit into the overall design.
Winning with the 3DEXPERIENCE business platform
The ASDL team required a platform to bring together the disparate framework. They used Dassault Systèmes’ 3DEXPERIENCE® platform and the Winning Program Industry Solution Experience for aerospace and defense that is comprised of applications from ENOVIA, CATIA, SIMULIA and 3DVIA. The Winning Program solution provides a platform to optimize conceptual design studies and allows knowledge capture of the end-to-end proposal process allowing repeatability and reusability on future concepts.
The Winning Program provided the backbone of the virtual prototyping framework and methodology because it had integrated design, manufacturing, analysis and verification features providing the capability to virtually identify, plan, design and configure the right concept that meets customer requirements and in a short amount of time.
ASDL focuses its research on conceptual design bringing more information earlier into the design to ensure there are no downstream manufacturing or certification surprises in the real world. “As systems make up the products, it’s very important that we don’t just think about shape but we also consider the complexity of the systems – the components and relationships between them – and how they fit into the overall design,” Briceno said. “Virtual prototyping is a more cost effective way to see the total picture.”
The Winning Program gave the students a chance to work in an integrated environment with many applications, and not with disparate solutions. The students learned very quickly, and even had fun with the system during their free time in the evenings. They were eager to showcase their creativity and to try new things using all the different features.
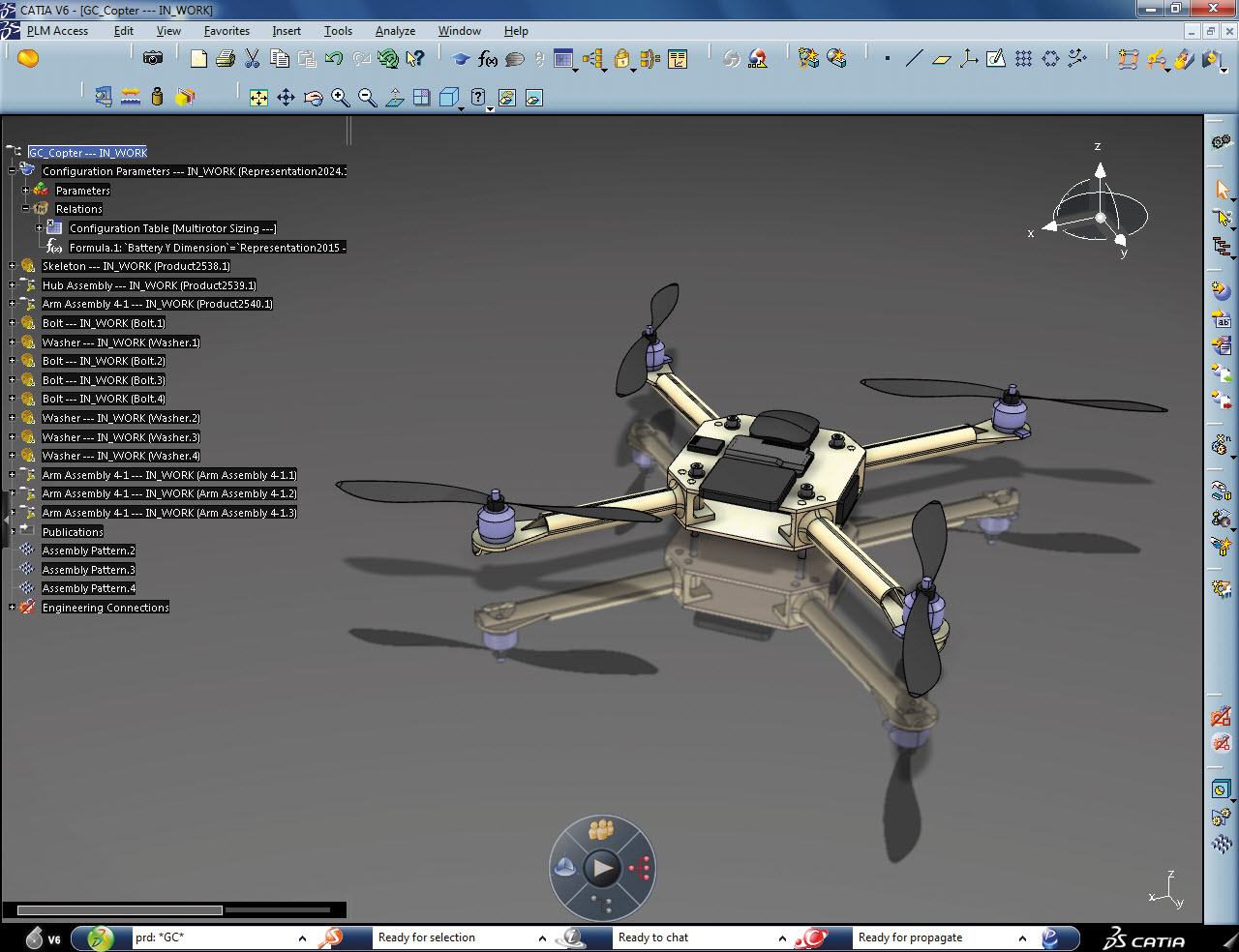
Benefits of an integrated framework
A high priority for ASDL was the ability to not only track requirements but also understand the configuration that responds to those requirements. Powered by the ENOVIA application, Winning Program flags when requirements are altered through the design process, so designers can trace how those changes will impact the system and identify if simulations need to be re-run for requirement compliance.
The traceability feature comes in handy for managing engineering changes and product evolutions allowing users to see and understand how changes in requirements affect the components selected or what a concept would look like if certain changes were made.
In order to help explore all possible UAS designs, the SIMULIA application automatically proposes an iterative number of configurations that best respond to the requirements based on the library of smart components stored in ENOVIA.
The systems trade study feature allowed the lab to limit exploration from an astronomical number of combinations to a manageable quantity. “At this point, we don’t necessarily know exactly what the concept will physically look like but we know it has to function a certain way and that there’s a certain logic to this functionality,” said Briceno.
The virtual world also allows ASDL to have confidence in their designs. Programming intelligence into components, virtually building the system and testing it with SIMULIA gives them confidence early on in the process that the concept could actually be built and perform as expected once they got to the physical prototyping stage, making them confident to commit to what could be done.
Briceno’s team uses Winning Program’s component-based approach to design UAS’s smart cyber-physical components with features from the CATIA application. These components include more than just geometrical CAD information; they can include behavioral characteristics or whether they are manufactured on the market or produced in house. By storing these components in ENOVIA, ASDL can also reuse them for future projects, which reduces design time and ensures the component’s intellectual property remains available for future students.
Once Briceno and his students are ready to construct a 3D environment to test the adaptability of the UAS, they use the 3DVIA application to create a test mission for the drone. 3DVIA enables the students to visualize the virtual environment and gather the physics and other associated data into CATIA to analyze. “All applications are completely integrated and fully compatible, which helps harmonize teamwork and streamline data exchange,” Briceno said.
Building on teamwork, ENOVIA ensures the most up-to-date data is available so that project teams can collaborate together and work simultaneously on the same model in real time. “Moreover, we can allocate different tasks over time to the team and define what everyone’s role is, what the project milestones are and the deliverables that are expected of each team member,” Briceno added.
Once a concept is finalized, the Winning Program can help assure the customer that all the requirements have been met and it will function as promised in the real world. “Designers can address many aspects concerning the design from the conceptual side of requirements all the way through the preliminary detailed analysis. We can walk our customers through our concept visually to show them that we have addressed their requirements. We also know from the earliest stages that we can deliver the customer’s solution on budget and time,” said Briceno.
Looking ahead to certification
The lab is also working with Dassault Systèmes to introduce certification into the early design decision-making stages. “We have a team that engages in certification-driven design,” Briceno said, “because we consider certification a critical component to the overall cost of any complex system. We thought that it was important to not only look at performance and economics, but to also look at what aspects of certification or means of compliance will play a role in the system and the components that are selected for a particular concept.”
Demand for UASs continues to grow for both consumer, commercial and military purposes. As the next 50 years will prove, the technology and methodology will continue to refi ne. “Now, with the ability to move decisions to the concept phase, our virtual prototyping framework is integrated on one platform,” Briceno concluded.

Focus on Aerospace Systems Design Lab at Georgia Institute of Technology
Research laboratory belonging to the school of Aerospace Engineering. ASDL works on civil, military and space projects that include aerospace vehicle design, gas turbines, naval and missile systems.
Areas of Research: Civil aviation research, propulsion & energy, advanced concepts, advanced system engineering and defense & space
Staff: 200 MS and PhD students, 50 undergrads, 40 research staff members
Headquarters: Atlanta, Georgia, USA
For more information: www.asdl.gatech.edu