Flow Robotics
Flow Robotics leverages the 3DEXPERIENCE platform on cloud to scale up production of flowbot™ ONE, its liquid handling robots functioning as medical devices, and accelerate product development.
We couldn’t continue to grow the way we have without the support of the 3DEXPERIENCE platform.
Liquid handling robots relieve pressure on labs
In life-science laboratories and hospitals across Europe, a team of robots is helping to alleviate the strain on bioanalysts as they process thousands upon thousands of COVID-19 tests per day. Collecting, preparing and analyzing the virus samples is usually very manual and repetitive – a physically demanding, intensive task that involves mixing specific quantities of reagents and liquids using pipettes. Thanks to flowbot™ ONE pipetting robots, developed by Danish manufacturer Flow Robotics, laboratories can now easily automate part of the testing process, speeding up the time it takes to produce results and reducing pressure on their staff. However, PCR analyses are only one area of the applications of flowbot™ ONE.
High workloads and physically challenging conditions have long been an issue for laboratory professionals. Flow Robotics estimates that around half of medical lab technicians carry out the same arm movements for at least a quarter of their working day. Meanwhile, the American Society for Clinical Pathology reported that 85% of laboratory professionals feel burnt out; 36% struggle with inadequate staffing; and 32% face a heavy workload and pressure to complete all testing on time.
The flowbot™ ONE pipetting robots have been designed specifically to reduce physically demanding pipetting tasks for laboratory personnel and minimize the risk of human error and contagion in the process. The robots are paving the way for a more sustainable lab setup, where humans and robots work in parallel to avoid work-related injuries and operate more efficiently. In the COVID labs, the robots pipette the live virus, handling several samples simultaneously, all working from a predefined pipetting pattern.
“Our aim when we started was to disrupt the way that liquid handling is performed in life sciences companies around the world,” said Steen Vester, chief technology officer at Flow Robotics. “Laboratories tend to have lots of manual, repetitive tasks and are looking for ways to become more efficient. Our robots work alongside people, so they don’t get overburdened and develop strain injuries or become exposed to live virus samples. The robots deliver in terms of accuracy too. When you’re manually handling pipettes for hours, it can become difficult to dispense the exact amount of liquid every time. But this isn’t the case for a robot. It doesn’t get tired and make those kinds of mistakes. The psychological and physical savings we deliver are far from insignificant.”
Versatile and affordable, Flow Robotics robots can be used for numerous laboratory applications. Unilabs in Copenhagen, for example, uses the robots to dilute blood samples and dispense them onto microtiter plates as it screens sclerosis patients all over the world for diagnostic analysis.
“We’ve made it possible for lab technicians without any programming experience to learn how to set up the robots within an hour,” Vester said. “Often, these labs have a protocol and you can set that up on one of our robots in a couple of minutes.”
Orders for the affordable, user-friendly liquid-handling robots are growing fast as more laboratories become aware of the potential to speed up their processes and better support their staff.
“We want to put our pipetting robots into the hands of people in the labs to support them and avoid strenuous tasks,” Vester said. “Existing machines on the market are more focused on full automation, whereas we want to help create workplaces where robots and people work alongside each other. For that, the robots need to be adaptable, affordable, easy to program and very user friendly.”
As Flow Robotics scales up production, it realized it needed a powerful technology platform to bring order and visibility to its product development processes and, very much like its own robots, help make workflows more efficient. The company opted for the 3DEXPERIENCE® platform on cloud and is already achieving noticeable benefits.
“We couldn’t continue to grow the way we have without the support of the 3DEXPERIENCE platform,” said Per-Arne Jönsson, senior mechanical engineer at Flow Robotics. “As we’ve brought more engineers on board and expanded across the company, we needed a centralized communication platform to establish a common understanding, ensure everyone is working from the same data and help multiple disciplines work together. In terms of communication, we need a straight line instead of going around in circles. Our processes should follow a formal flow and the platform helps us to do that.”
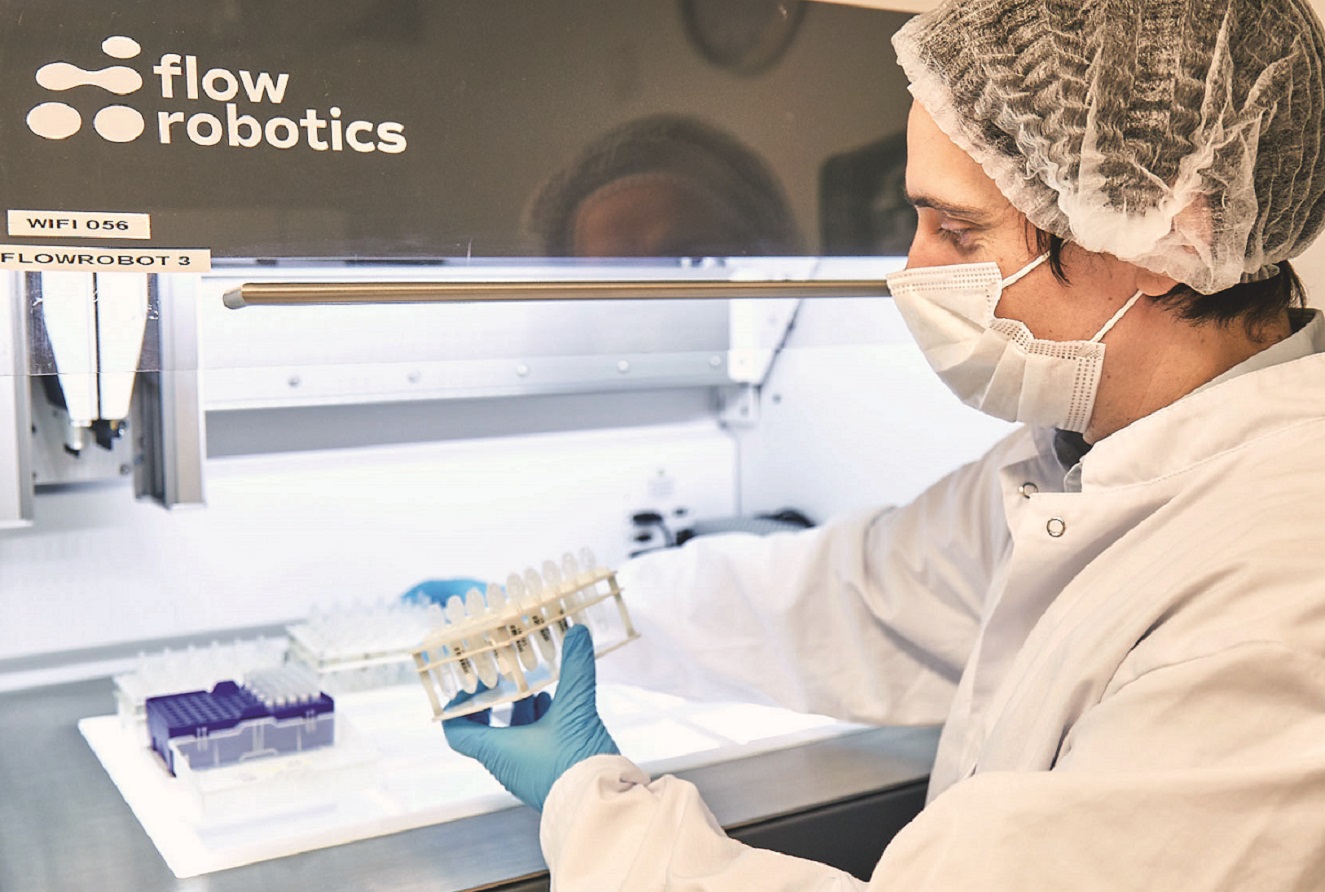
Supporting a fast-growing business
Flow Robotics’ team has expanded rapidly as demand for its robots accelerates. What used to be a case of a couple of engineers working alongside each other has turned into an increasingly complex operation as more people join the production, purchasing and R&D departments. It’s meant that the company has had to define new processes and workflows to achieve effective multidisciplinary collaboration.
“Within 20 weeks we were running our first projects directly in the platform, using it for automatic bill of materials (BOM) generation, drawing templates and sorting standard components within a material database,” Jönsson said. “We’ve balanced our processes and ways of working to use as much of the native 3DEXPERIENCE functionality as possible.”
Key to the success of the rollout was Flow Robotics’ partnership with Dassault Systèmes value added reseller X10D Solutions, which worked closely with the manufacturer to define its processes and implement the PLM platform.
“The first meeting we had with X10D really set the bar for what was to come,” Jönsson said. “There was no doubt that the partner was genuinely interested in helping us out. They spent a lot of time being there for questions. It felt like a joint venture with strong commitment and a can-do attitude, and they have been there for us throughout. It has made a huge difference to the end result and speed of implementation.”
Critically, X10D challenged Flow Robotics to rethink its way of working.
“X10D helped us develop a more balanced view and changed our mind about our processes in minor and major ways,” Jönsson added. “We didn’t know the platform before, so we trusted them to help us. Now, when we go into new projects, our users access, consume and share data in a very different way to before. It’s much easier.”
Opting for a cloud deployment also allowed Flow Robotics to get up and running quickly.
“It made sense for our business on so many levels,” Jönsson said. “There are numerous requirements for these on-site installations; I have yet to see a company succeed in that without interruption. For us, it was really important that we could hand over some of that IT management to the professionals with a lot more resources and skills. It’s great that we don’t have to worry about data security; we can trust Dassault Systèmes to handle that.”
I know that the possibilities in the platform are basically endless, but it brings a smile to your face when you can very quickly leverage the data you have painstakingly created in such a way that a colleague’s work tasks become easier and more efficient.
Freeing minds up for innovation
Now that Flow Robotics has transferred all its legacy data into the 3DEXPERIENCE platform, it has begun handling new projects natively in the platform.
“Our goal has been to maximize the use of documentation and minimize administration, and we’re already seeing a benefit,” Jönsson said. “We can have discussions on a different level; people can see what we’ve discussed in meetings; and everyone can access the same data. It’s an ongoing journey for us. We were cross functional before, but now we have more people and we can give them an opportunity to go and look at stuff independently or brainstorm within small teams.”
Through this greater level of transparency and ease of access to information, Flow Robotics’ growing team is empowered to be more innovative.
“We have a lot of innovative people here,” Jönsson said. “When you have an efficient tool that allows you to focus on your work and not on documenting it, it makes your task easier and more fun. My aim is to have my engineers spending 98.5% of their time doing development and 1.5% doing documentation.”
“I wanted us to have a pure database setup from the very beginning and that’s what the 3DEXPERIENCE platform gives us,” Jönsson added. “Now, for example, the search and find feature is very easy to use; you can pull up the result you need without losing loads of time. The bottom line is we want to help our people focus on developing great customer-oriented products.”
Using customized dashboards and widgets, engineers can choose what information they want to see that’s relevant to them, allowing them to work smarter and faster.
“The flexibility of the web interface is really starting to pay off,” Jönsson said. “It’s brilliant to have the opportunity to build dashboards for specific use cases. I made one of our service engineers giggle with pleasure when I was able to create a dashboard with widgets catered to his needs within just ten minutes. I know that the possibilities in the platform are basically endless, but it brings a smile to your face when you can very quickly leverage the data you have painstakingly created in such a way that a colleague’s work tasks become easier and more efficient.”
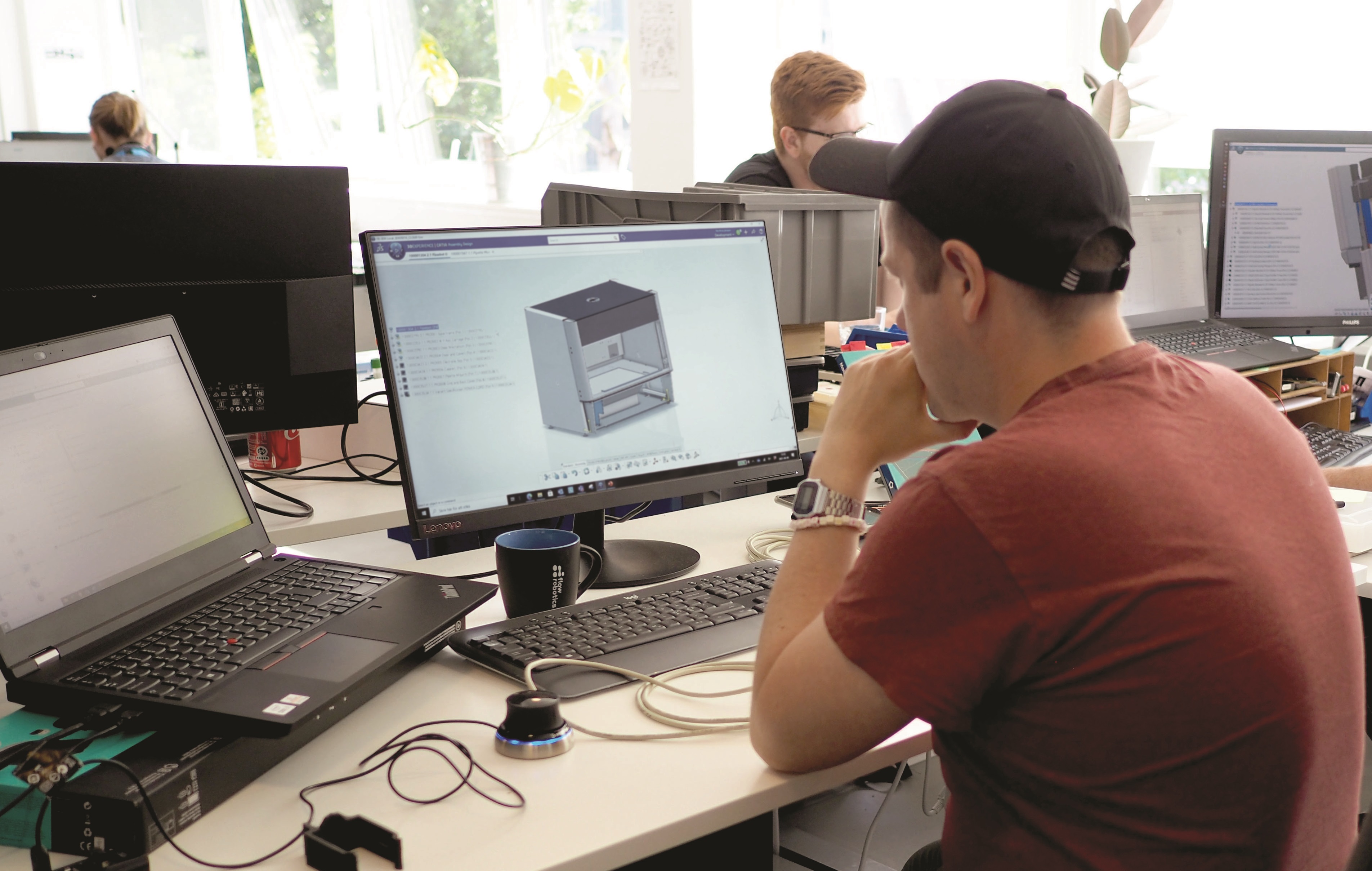
Handling growing complexity
Flow Robotics’ previous design tool didn’t offer the functionality it needed beyond simple CAD, which made it difficult to extract the information it needed for defining the engineering BOM. Now, it is using CATIA for part, assembly and drawing creation, all managed on the 3DEXPERIENCE platform to provide the flexibility to extract BOMs or run simulations all from a single engineering definition.
“We’ve moved rapidly from something simple to a more complex situation where we’re producing many robots a week and working to keep up with orders and customers’ specific requests,” Jönsson said. “With the 3DEXPERIENCE platform, we have a very efficient setup that allows us immense flexibility to easily define what goes in the BOM. We don’t have to manage separate structures to cater for motion simulation and BOM definition. It’s very well suited to the stage we are at currently.”
Although Flow Robotics already had a standard parts library, it is now also using the platform to better understand how it can optimize part reuse and save costs in the long run.
“When you have these tools, you can automatically increase the specifics of everything,” Jönsson said. “Suddenly everything becomes much clearer to see. We can now access and filter our data in so many different ways, and it gives us a much better understanding across the board of how many parts we’re using. It will give us the opportunity to consolidate and reduce the amount of parts we use.”
Advancing design capabilities
As Flow Robotics’ team of engineers gets up to speed with the 3DEXPERIENCE platform’s rich functionality, it plans to extend the use of CATIA’s powerful modelling capabilities in the design of new robots.
“CATIA has a whole new visual interface that is fast working,” Jönsson said. “The setup we have is fun to use and it’s easy to document something in the right way as it requires so little effort. It means we can continuously mature our data in the product development process. We’re still learning how to use CATIA and will gradually move towards parametric modelling.”
The future is looking bright for Flow Robotics. And now, with PLM on the cloud, there are no limits to its growth or its ability to innovate.
“Our people can serve themselves with customized information and it frees them up to think about new ideas and solutions,” Jönsson said. “We’re already becoming more efficient both in terms of cost and time. With the platform, we will develop better designs and solutions, and make fewer mistakes. Communication is constantly improving and we now have a better understanding of each project status at any given point in time.”
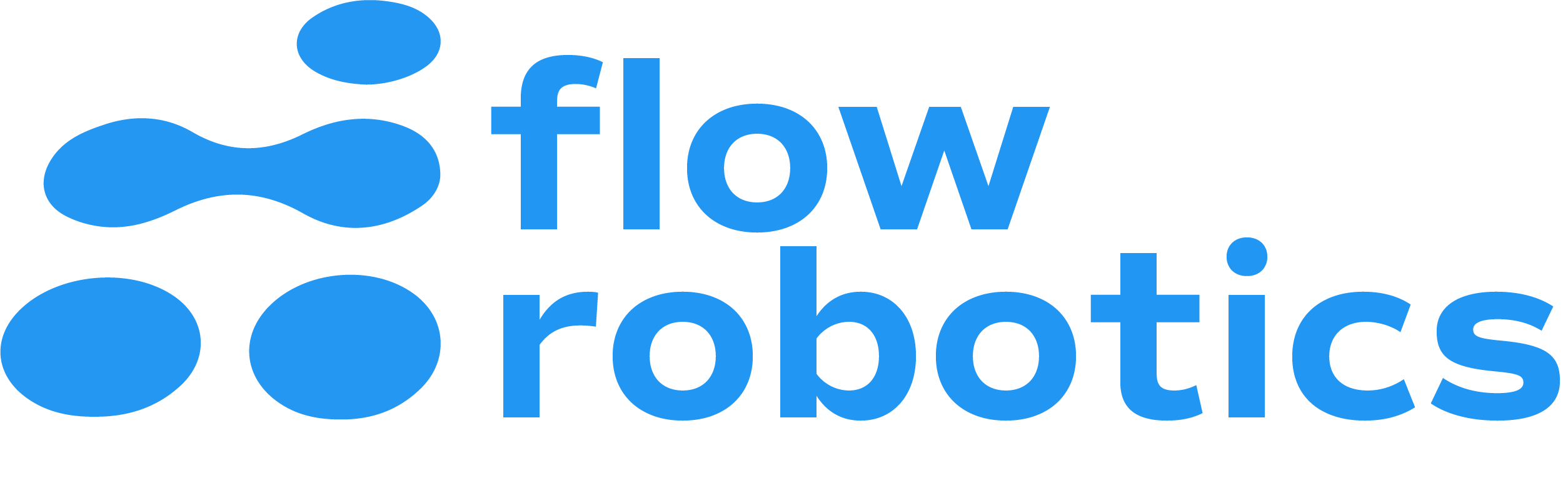
Focus on Flow Robotics
Flow Robotics aims to help labs speed up their liquid handling processes and experience a new level of flexibility. The company’s pipetting robot, flowbot™ ONE, is a new technological innovation designed to assist lab workflows and adapt to their processes. Intuitive and user friendly, the robot allows scientists and technicians to set up tailored protocols in a simple and reliable manner. Anybody can learn how to use the robot within an hour and setup is completed within minutes. Through increased efficiency, flowbot™ ONE delivers a rapid return on investment and is proving a sound choice for labs.
For more information: www.flow-robotics.com
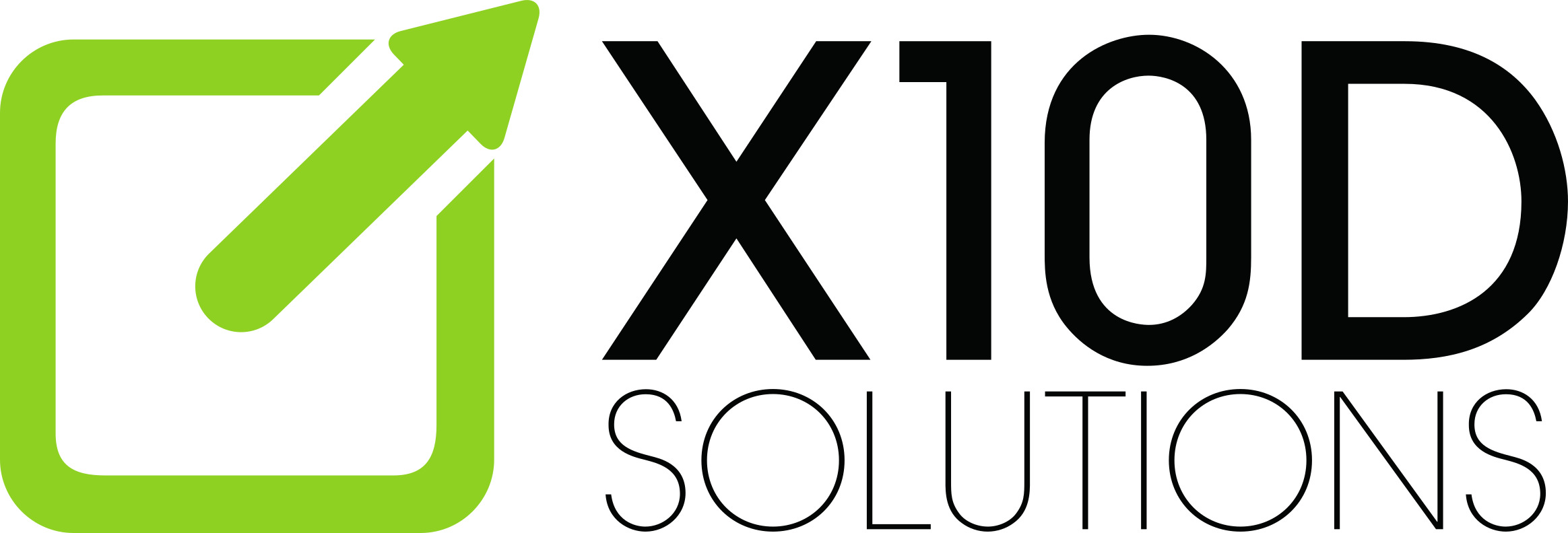
Focus on X10D Solutions
X10D Solutions is a company with extensive experience of PLM. It works with world-leading software from Dassault Systèmes, delivering high-quality support and cost-effective implementations. X10D specializes in working with small and medium-sized companies, helping them to get the most value from their investments.