Autoliv
Driving Lean Manufacturing with DELMIA Apriso.
The quality advantage (with ACE) is we have better access to traceability data and batch tracing at the line. A big advantage of this ACE project for the plant is we have integrated, real-time information flow. Reaction time has been cut short very much. Data transference is much better than we had before.
The challenge
Autoliv sought to better manage quality and material flows, achieve greater traceability and drive consistent, lean continuous improvement across all of its manufacturing plants.
The solution
The company is deploying DELMIA Apriso with an ERP rollout – a solution internally known as “ACE” to improve and harmonize operational and commercial business processes into one integrated system.
The result
Better visibility into materials, workflows and processes has been achieved, helping the company to improve productivity, enhance global traceability and standardize global process improvement.
Innovation and an intense focus on saving lives have been the hallmarks of Autoliv from its inception half a century ago.
Now its products save 30,000 lives every year and prevent ten times as many severe injuries.
Delivering quality products is important in all industries, but it is especially critical where consumer health and safety are affected. Automotive is one of those industries.
That’s why Autoliv, a Fortune 500 Tier 1 supplier of airbags and safety systems to all of the global automotive OEM’s, wanted to better manage quality and material flows, achieve greater traceability, and drive continuous improvement across its manufacturing plants. “We needed to improve and harmonize our operational and commercial business processes into one integrated system,” explained Gilles Bridon, Senior AEU IT Director, Autoliv.
To achieve this goal, Autoliv made a decision to deploy their Enterprise Resource Planning (ERP) and Manufacturing Execution System (MES) together in a system the company calls ACE, or Autoliv Consolidated ERP deployment. From Autoliv’s perspective, MES is seen (and referred to) as a Lean Execution System to implement and continuously improve Lean manufacturing initiatives, which can then help Autoliv standardize and share best practices across multiple plants.
The company chose SAP as their ERP solution, and DELMIA Apriso as their manufacturing execution platform. Now Autoliv has an enterprise solution to streamline production operations from planning, to inventory and material flow management, to traceability and continuous improvement.
“ACE is a business transformation program that will take us to the next level of performance. It is a business driven program to harmonize processes to bring everything into the same master data and into one ERP and MES system,” said Jan-Henning Krumme, ACE Program Director, Autoliv. “In short, one process, one system, one data” he said.
Lean Material Management
The ACE system provides lean materials handling across Autoliv’s manufacturing operations, thanks to DELMIA Apriso’s wide footprint that extends beyond the four walls of production, including inbound material receiving and put-away, quality control, maintenance, shipping, and outbound to their supply chain. Logistics and production planning is prepared in the ERP system, and then moves to DELMIA Apriso for execution. Daily schedules are communicated to the suppliers to ensure timely arrival that is synchronized against customer demand.
“We have chosen DELMIA Apriso as a proven automotive MES solution to support Lean manufacturing principals and the Autoliv production system to increase quality of our product, product data and the safety of our products. We save lives. Zero defects is a given in our market,” said Jan-Henning Krumme, ACE Program Director, Autoliv.
ACE directs all material movements inside the plant, with activities captured by scanner to ensure efficient and secure material flow. Automated triggers notify warehouse operators to replenish the line when materials are needed. During production, sampling rules predefined in SAP are executed through the DELMIA Apriso application, which alerts and guides operators to perform and execute the proper quality steps. Post production, ACE ensures accurate and timely delivery by automatically creating advanced shipping notification.
Paperless processes streamline operations
The ACE system automates and standardizes financial and control processes. Self-billing is now integrated into the system, resulting in a paperless billing process that has streamlined processes, improved accuracy and increased efficiency in their Finance department.
ACE has also brought paperless operations to many other activities that were previously manual. For example, physical Kanban cards have been replaced with production sequences displayed directly on the monitor of each production line, with production order labels printed automatically. Supervisors use the graphically-driven DELMIA Apriso Dispatching Board to enable efficient planning and execution of daily production and sequence of orders.
The Dispatching Board provides real-time visibility and control of plant floor activities. Supervisors and plant managers use it to monitor production progress status, planned maintenance activities and unplanned events at a single glance. This allows Autoliv to quickly address issues as they arise, such as rearranging production orders to meet customer demands and plant efficiency targets.
Global traceability
With physical flows managed by DELMIA Apriso throughout the plant, from receiving to shipping, Autoliv can achieve a far more comprehensive set of traceability intelligence, which is then readily available as future needs arise. DELMIA Apriso supports batch and end-to-end flow of product and process traceability, and can help quickly identify, isolate and contain suspect materials or errant processes should a potential issue be detected.
Just as importantly, the standardized execution platform means that when problems are traced to process or material issues, corrective actions can be readily implemented and rapidly deployed to all plants, thanks to the ACE system.
Global deployment
Based on the initial success of pilot deployments, Autoliv is now rolling out their ACE solution to 30 manufacturing plants across Romania, Hungary, Turkey, France, Sweden, Spain, UK, Germany, and Russia. DELMIA Apriso can help ensure the company centrally monitors quality and production processes while gaining insight and visibility into operations as Autoliv focuses on taking their business performance to the next level of success.
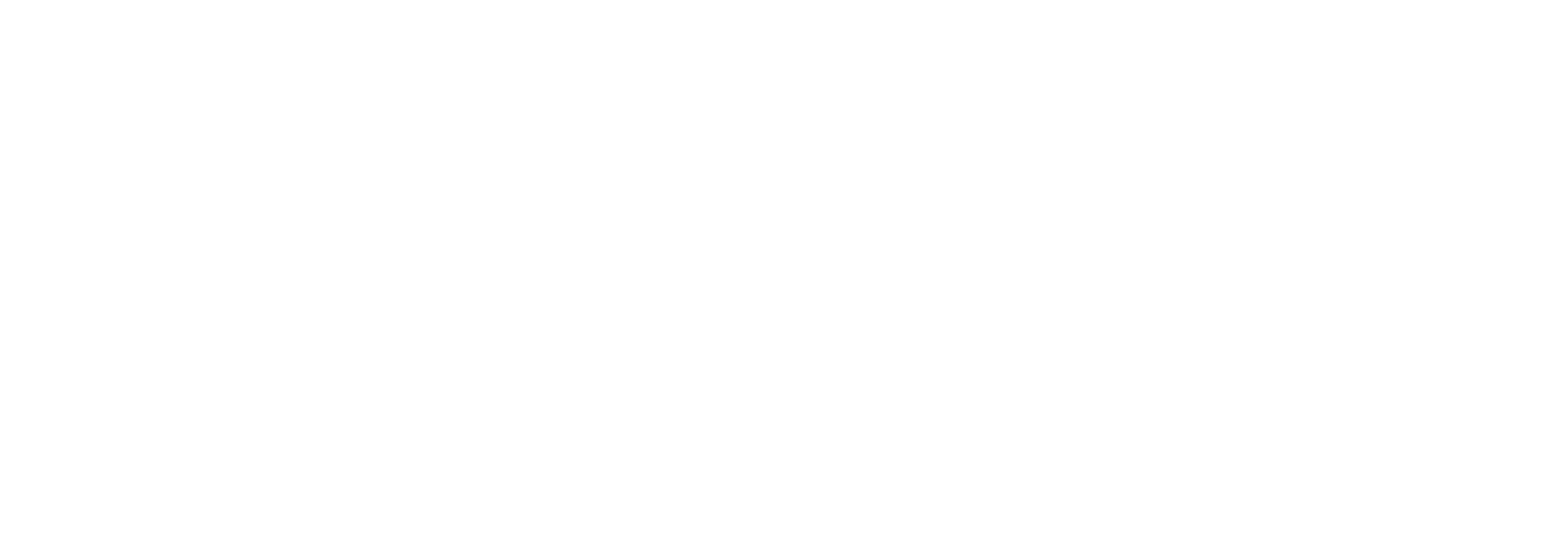
Focus on Autoliv
Products: Active and passive safety systems that save lives
Headquarters: Stockholm, Sweden
Revenue: € 3,84 billion in 2017
Employees: 60,000
For more information: www.autoliv.com