Assystem
The company chose Dassault Systèmes’ 3DEXPERIENCE platform and the Capital Facilities Information Excellence industry solution experience to increase the value of its solutions through digitalization.
Complexity breeds risk
While many countries question their use of nuclear power for safety or environmental reasons, Assystem, an international independent engineering group with 2,500 experts in the nuclear field, has made the maintenance of highest level of safety in the nuclear industry a priority. “Building and operating a nuclear plant entails satisfying more and more requirements imposed by safety authorities and public opinion as well as integrating increasingly sophisticated technologies,” said Christian Jeanneau, senior vice president Nuclear at Assystem. “This introduces a high level of complexity during the engineering and construction project phases. Because of their massive size and cost, plants have to be built right the first time. Physical prototypes are simply not an option.”
Challenging Complexity with the 3DEXPERIENCE Platform
Improving performance, safety and cost
Digitalization is, therefore, an objective Assystem is pursuing for itself and when interacting with its clients. “There will be tremendous opportunities for improvement when we complete our digital transformation,” Jeanneau said. “We chose Dassault Systèmes’ 3DEXPERIENCE® platform to accelerate our digitalization. We decided to implement these technologies after considerable benchmarking and analysis, and believe they will help us manage our projects in a way that will bring the most value to our clients. Our strengths are in managing large and complex physical power plant projects with special emphasis on performance, safety and cost.”
Large energy projects are complex to manage – managing the configuration, managing terabytes of data, managing requirements, all while meeting cost and scheduling targets. “We believe digitalization and modern tools give us a huge advantage in terms of cost and efficiency because they will allow us to manage complex information much more easily and efficiently and with greater accuracy,” added John Clark, chief technical officer, Assystem UK. “For example, instead of using expensive physical prototypes, we rely on digital modeling and simulation to test the movement of a robot with many degrees of freedom when maneuvering a large piece of equipment in a reactor vessel, to make sure it can be pulled in and out of a very tightly constrained space.”
Large and complex projects also require that all project stakeholders collaborate like a well-tuned orchestra. “Everyone must have access to large amounts of accurate and up-to-date data,” Jeanneau said. “The 3DEXPERIENCE platform offers a common language and methodologies that can be shared inside a company and with external partners and contractors. It improves our efficiency because sharing ideas and expertise in real time allows us to reduce the number of hours we spend on a project.”
Another challenge is to manage information continuity from early requirements to design, construction, commissioning, handover and operations. “For example, to prove that a plant’s life can be extended after 40 or 50 years in operation, we have to be able to demonstrate that the equipment and facility itself have been operated in compliance with the initial design and construction specifications,” Jeanneau explained. “Therefore, we need to record the data. We need traceability. Using a digital model to record the operating data during commissioning and during operations is the best way to capitalize information to present to certification agencies, and to implement a predictive maintenance strategy that improves our clients’ competitiveness.”
Working with the 3DEXPERIENCE platform will influence the types of projects Assystem accepts. “The platform delivers key capabilities for us, which include requirements, bill of materials, and change management,” John Clark said. “Increasing complexity generates more risk and this solution enables us to manage this complexity and, hence, risk. For example, through better change management, we have a more current, unified view of the plant’s status and performance. This single source of the truth helps us make more accurate risk assessments. Other benefits include less scrap and rework because our designs are more precise and of better quality. We are able to spot deviations earlier and make adjustments before releasing the design for construction when corrections would be too expensive to implement.”
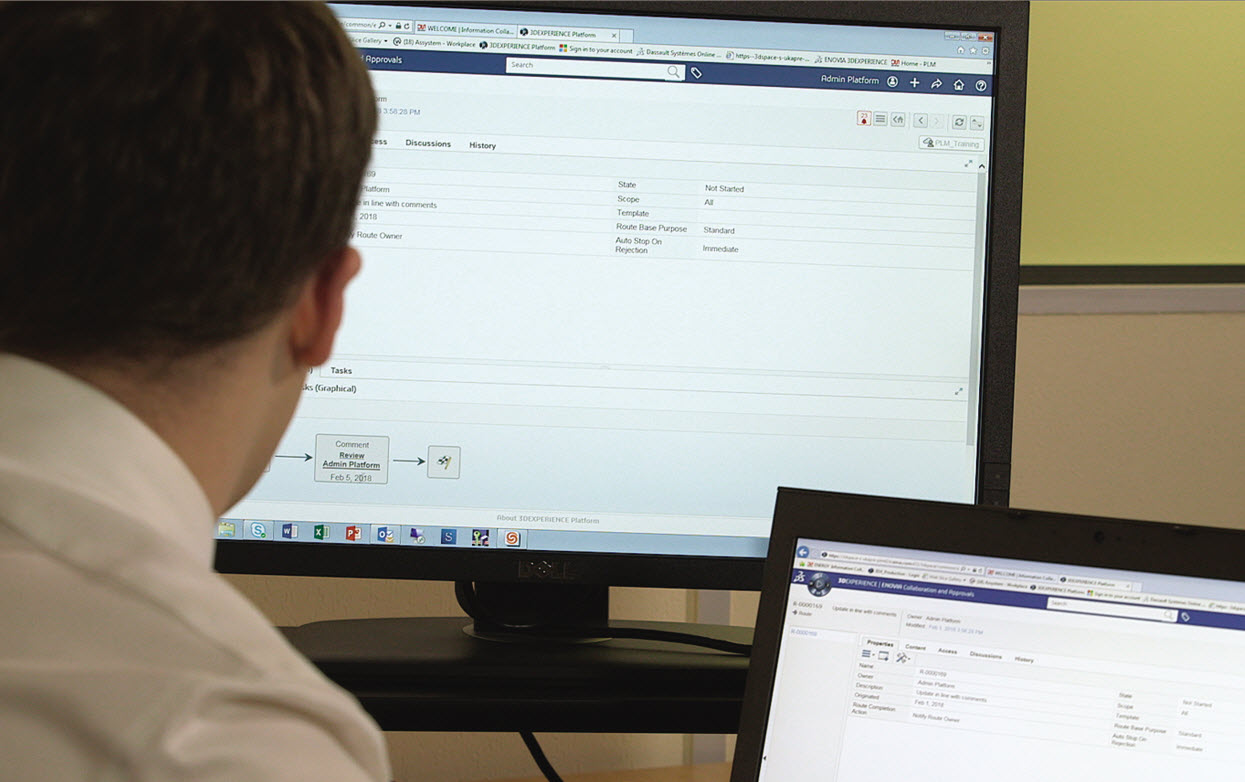
From pilot project to wide-scale deployment
Assystem began by deploying the 3DEXPERIENCE platform on a few small projects involving ten people in a production setting in 2016. In their pre- and post-assessment, they noticed people spent 20% less time performing certain tasks. The successful outcome of these projects encouraged management to roll out the platform to the rest of its business and to begin managing projects that are more ambitious. “We’re looking to capitalize on these good experiences and extend implementation of the 3DEXPERIENCE platform to all our mechanical and systems engineers,” Clark said.
Implementation services and support are managed by Majenta Solutions. “The system was tailored to fit our company methods and procedures such as managing standard part libraries and auto numbering documents according to Assystem’s quality control processes,” Clark said. Majenta engineers reviewed Assystem’s existing processes such as Documentation Control, Inquiry, Contract Start-up, Contract Variation, Design, and Purchasing, performed offsite analysis and mapped these processes to the latest version of the 3DEXPERIENCE platform, built test environments, sifted through end-user experience and feedback, all the way through to full deployment of the solution. They also provided first-level training to Assystem ‘subject matter experts’ who formalized and deployed company best practices to additional users. “Majenta did a fantastic job representing us to Dassault Systèmes and managing the dayto-day operations, making sure we got answers in a timely manner,” Clark said. “I look forward to working with Majenta to continue building our experience with the system and to bring more people up to speed so they can become happy users. It is one of our goals.”
One of these users is Tom Goulding, a mechanical engineer who uses the 3DEXPERIENCE platform to manage customer changes. “My job is to make sure that changes are reflected in all necessary documents and that project information such as designs, methods statements, and calculations are updated accordingly,” Goulding said. “The 3DEXPERIENCE platform helps me manage this aspect of my work more efficiently because when I am assigned a task, I can see all my tasks, which are displayed on my dashboard with all the documents that need updating. Once I promote my task to ‘complete’, this status and the task’s history are recorded in the platform for future reference.”
Goulding also developed internal methods and processes that comply with the company’s quality assurance charter. “We assigned rules in the platform to define the tasks to be completed when documents are submitted for review or approval,” he said. “We also schedule our technical design meetings through the system and attach all the documents that need to be reviewed. The system allows us to close the meeting once all actions have been completed. It’s a great way of making sure nothing is missed.”
Data traceability is another advantage. When someone uploads a document to the system, everyone knows who submitted it, when it was last updated, and when and to whom documents were sent for review or validation. “The problem with hard copies is they get lost or are locked in someone’s drawer, so information is not being communicated to the right people,” Goulding said. “With the 3DEXPERIENCE platform, everything is online and in one place; we don’t risk losing any information. We also link each deliverable to a specific requirement making it easier for managers to track how many requirements have been met or how many are still outstanding and where we need to focus our resources.”
Christian Jeanneau believes technology will help the nuclear industry successfully negotiate its competitiveness revolution. “In mega capital projects, construction often runs over budget and overtime. Our clients need to be more competitive. Our role is to help them run their projects within their cost and scheduling parameters, and to allow them to demonstrate that they can build and operate their plants safely and efficiently. There is a good level of competitiveness if we are able to use digital media during the life of a nuclear plant to demonstrate regulatory compliance, perform simulations, engage in predictive maintenance and improve safety. With the 3DEXPERIENCE platform, we have a unique tool and methodology accessible to our entire ecosystem, giving stakeholders a horizontal view of a project that enables them to better collaborate and to improve their performance. It helps ensure the competitiveness and quality of the services we deliver to our clients,” he concluded.
The 3DEXPERIENCE platform helps ensure the competitiveness and quality of the services we deliver to our clients.
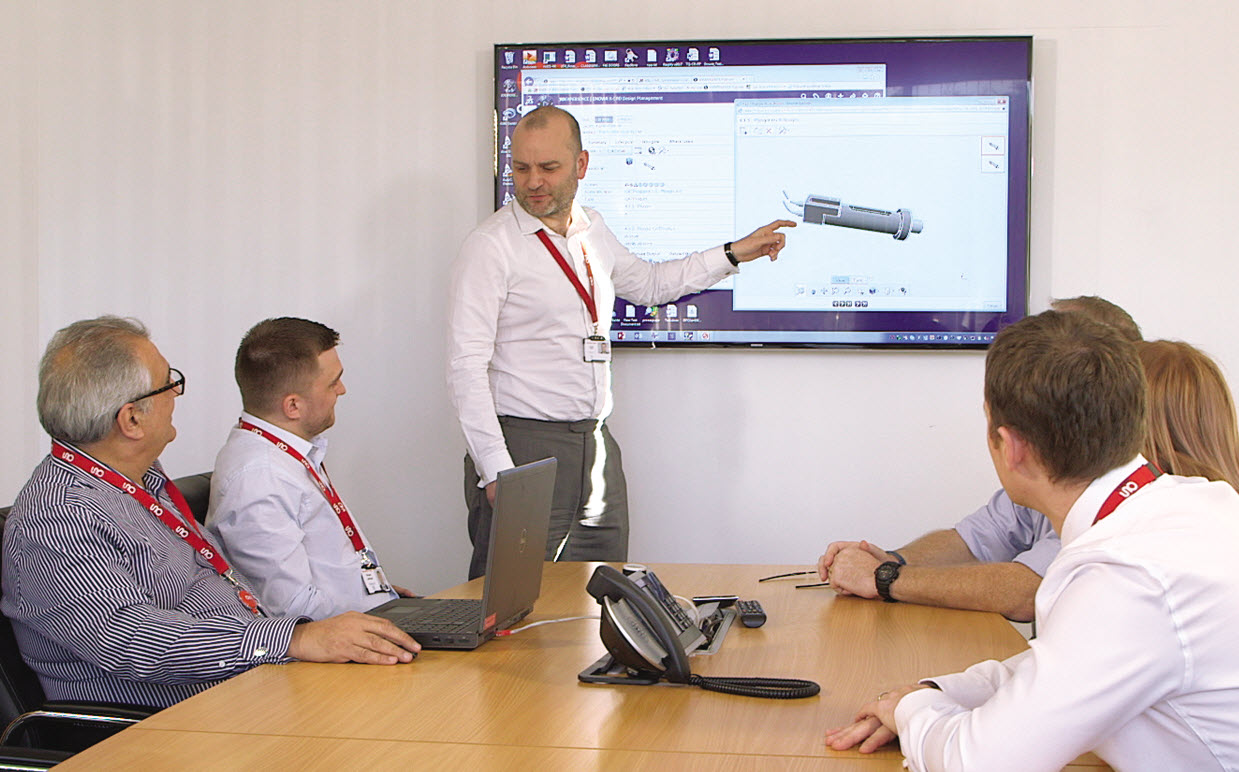
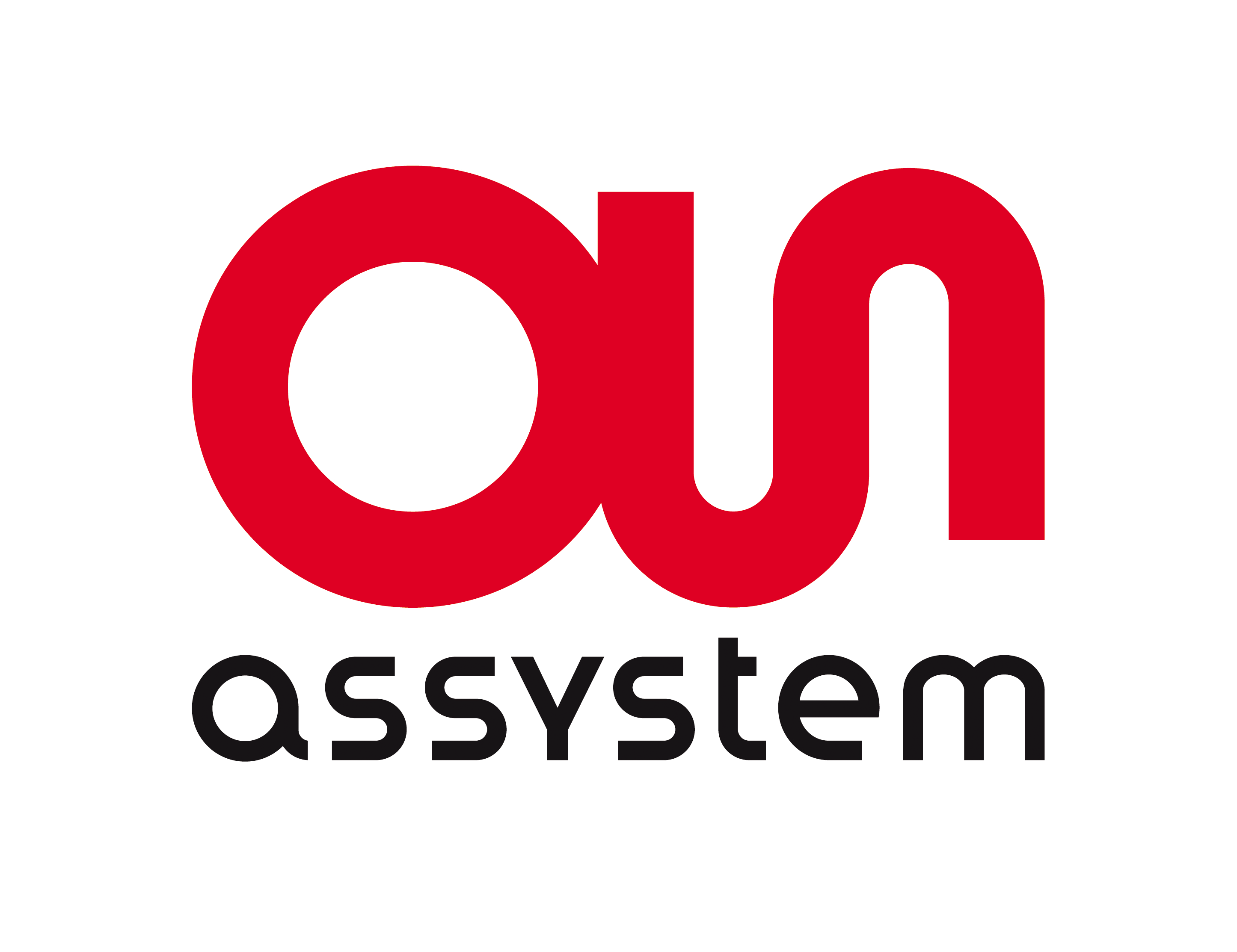
Focus on Assystem
International and independent engineering company helping their clients to manage, design, build and improve the performance of their infrastructure used for electricity production, transport systems and healthcare facilities Three lines of services: Project Management & Engineering, Digital & Performance, Security & Safety
Employees: 5,000 worldwide
Revenue: €400 million consolidated
Headquarters: Paris, France, with offices in 13 countries
For more information: www.assystem.com
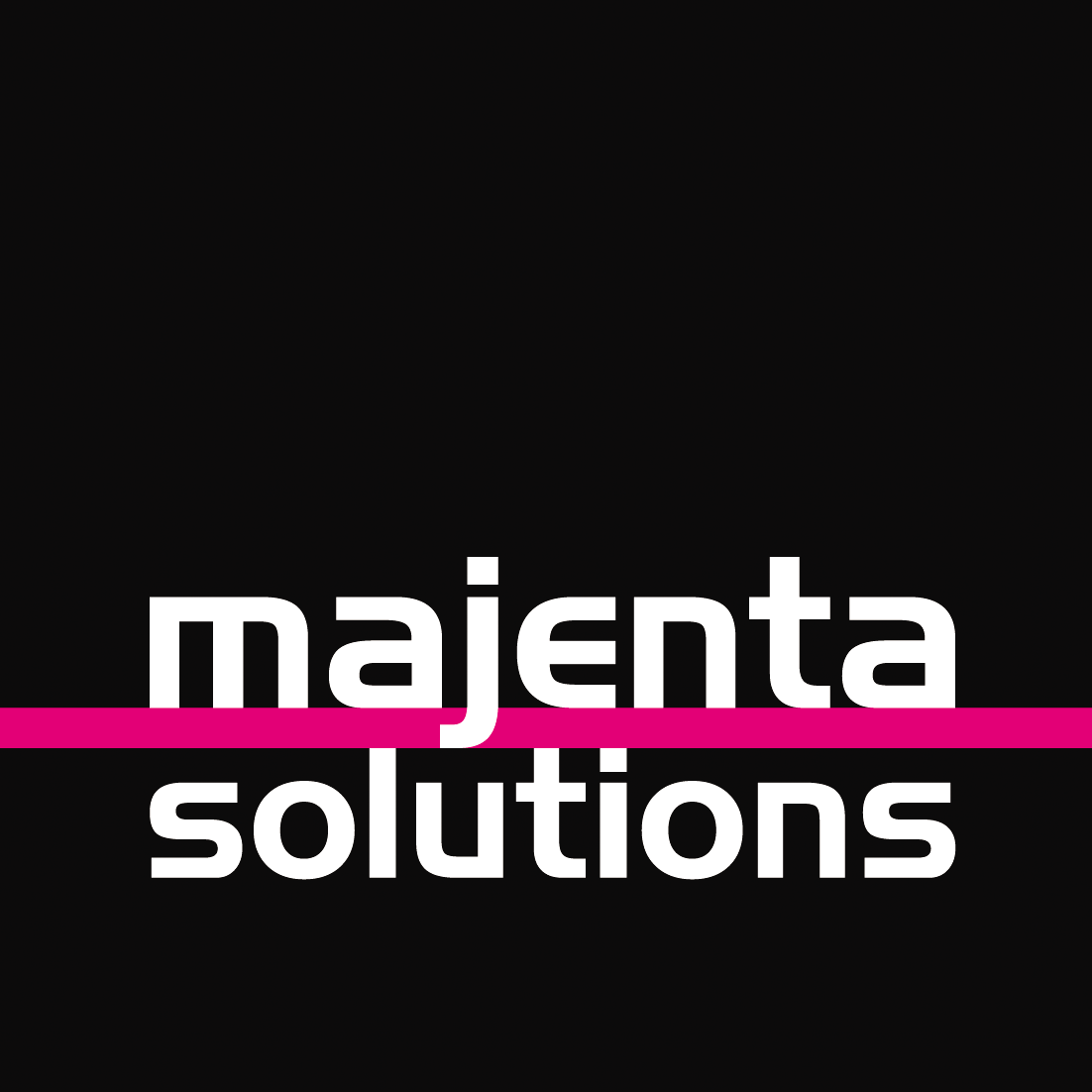
Focus on Majenta Solutions
Majenta Solutions are a UK-based leading technology solutions provider, supporting design, engineering and manufacturing businesses with the provision of appropriate and relevant products, services and support. Main industries covered among others are automotive, aerospace, general manufacturing and construction. Majenta Solutions have extended expertise in the specialized fields of product lifecycle management, supply chain integration and data exchange solutions, including working with more than 5,000 globally dispersed suppliers for major UK OEMs.
For more information: www.majentasolutions.com