Ariens
Ariens engineers used Abaqus/CAE and fe-safe from Dassault Systèmes SIMULIA, along with Wolfstar Technologies’ True-Load, to locate and accurately model strain gauges in all areas of the lawn mower, enabling weld elimination, part-count reduction, fatigue life improvement and other design enhancements.
Now that we use simulation, by the time that we do go to run a physical test of a finished redesign, we are confident that it is going to work.
If you were wealthy enough to afford a lawn in the 17th century, you had scores of scythe-wielding men cut the luxurious green grass of your estate property. Then in 1830, English engineer Edwin Budding invented the first “push” mower - an idea that stemmed from the mechanical challenge of trimming fabric in a cloth mill. Budding designed a series of blades situated around a cylinder that could be moved back and forth with a handle. Lawn care would never be the same.
Around the time when motorization made the automobile possible in the 20th century, the first power-driven lawn mowers roared to life. Mower designs have continued to evolve since then, from ones with improved muffling and lower-emission engines to ride-on and zero-turn versions. The push for ever-better lawn-care equipment continues in this multi-billion dollar industry.
A major American manufacturer of both industrial and personal lawn-care equipment, Ariens Company owns the century-old Gravely® brand that produces a state-of-the-art zero-turn commercial lawn mower. “Zero-turn” allows for 180 degree rotation in a single pass, saving time and providing better maneuverability when cutting.
With the latest upgrade in the Gravely zero-turn due, Ariens engineers were tasked with a list of important challenges. “We needed to make the mower stronger, less expensive to manufacture, and more fuel efficient,” says Mathew Weglarz, lead engineer and structural analyst at the Ariens Company. “Our goal was to design a structure as simply as possible, while maintaining the mower’s ability to perform the task at hand.”
Weglarz, a longtime user of SIMULIA’s Abaqus software, proposed the idea to incorporate the SIMULIA portfolio into Ariens’ design process when he began working there two years ago. Prior to Weglarz joining the engineering team, Ariens had only occasionally used SolidWorks Simulation to analyze certain components. With the help of Weglarz and Ariens’ structural analyst and engineer, Aleysha Kobiske, the engineering team at Ariens used a number of SIMULIA tools to drive innovation in the design of their newest Gravely mower.
The team began by examining the current model and finding areas that could be improved upon - such as geometry, material thickness, or maintenance access. All parts of the mower were simulated - everything from the main chassis, frame tubes, and cross and under-bracing brackets, to engine support mounts and seat platforms. The frame, which was comprised of 22 different pieces of steel that were welded together, was where a majority of design changes were made. “A strong structural design is key for noise and vibration control, durability, and overall manufacturing costs,” says Weglarz.
Designing a Better Frame
Part consolidation of the chassis was vital to a successful redesign. First, a number of welds could be eliminated outright. “Now one piece of steel could perform multiple tasks without the need for three or four brackets to be welded to it,” says Weglarz. Then other welds were designed out of the primary load paths so that the parent metal on either side took over the loading and the role of the welds became secondary. “These design changes increased the overall strength of the frame structure considerably,” said Weglarz.
At the end of the redesign process, the new frame had 50% fewer parts (11 total) and cost less to manufacture than its predecessor.
While lightweighting a frame could be viewed as beneficial towards reducing fuel emissions, it was not a stated design objective in this case: When it comes to industrial lawn-care equipment, there is a perceived correlation between weight and quality. “Even though you can probably make a mower out of aluminum or plastic and have it be just as durable as steel, people wouldn’t buy it because it just wouldn’t feel like a commercial machine,” says Weglarz. “Our customers want that durable, powerful feeling.” So while part-count reduction helped lower manufacturing costs for Ariens, weight itself was maintained with the customer in mind.
Building the Model, Running the Simulations
SIMULIA’s Abaqus/CAE and fe-safe, along with True-Load from Wolfstar Technologies, were the main software tools used in the redesign process. The engineering team was pleased with how well the different programs worked with one another. “True-Load interfaces seamlessly with Abaqus,” says Kobiske. “It takes the data and writes out a macro to fe-safe. Then all we have to do is go into fe-safe and hit the play macro button and it sets up the entire job.”
Using Abaqus/CAE, the engineers examined the stresses around critical frame welds to predict any areas of potential concern. “The read and write capabilities to and from Abaqus are what makes it so easy to use. You can easily pull out whatever data you need in order to get what you’re looking for,” says Kobiske.
Twelve linear-static load cases were run to account for every load direction coming onto the frame through the wheels. The strain simulation results of the unit loads acting on the frame were then sent into True-Load to determine the precise locations in which to place strain gauges on the structure for field testing. A total of 22 gauges were placed on the mower chassis.
Following field tests on an actual mower, the real-world strain-gauge data was incorporated back into the Abaqus model, improving the accuracy of the simulations for a truly realistic representation of the loads that the mower would encounter when cutting a lawn. With high-fidelity Abaqus models of the current frame in hand, the design team could then make upgrades to the frame that would help them achieve the “less expensive, stronger” mandates of the redesign project.
To further strengthen the chassis, engineers tweaked their designs in critical areas to reduce the amount of strain from the attached engine, transaxles, seat, and deck masses. Mounting points for roll-over protective structures (ROPs) had to be built to strict ISO safety standards. “We needed to ensure that we’d designed a strong, reliable frame to support the roll bar,” says Weglarz.
And how to predict the effects of many years of heavy grass work on a lawn mower frame? By using fe-safe to determine fatigue life of the component.
“We normally run fe-safe once for a design iteration,” says Weglarz. “Each time we make further changes to the design we will run fe-safe again to see the difference the design changes make. The life predictions from fe-safe help us determine areas of concern in the structure that we can address with subsequent adjustments.”
After its first round of design changes, the frame showed favorable structural responses and extended fatigue life.
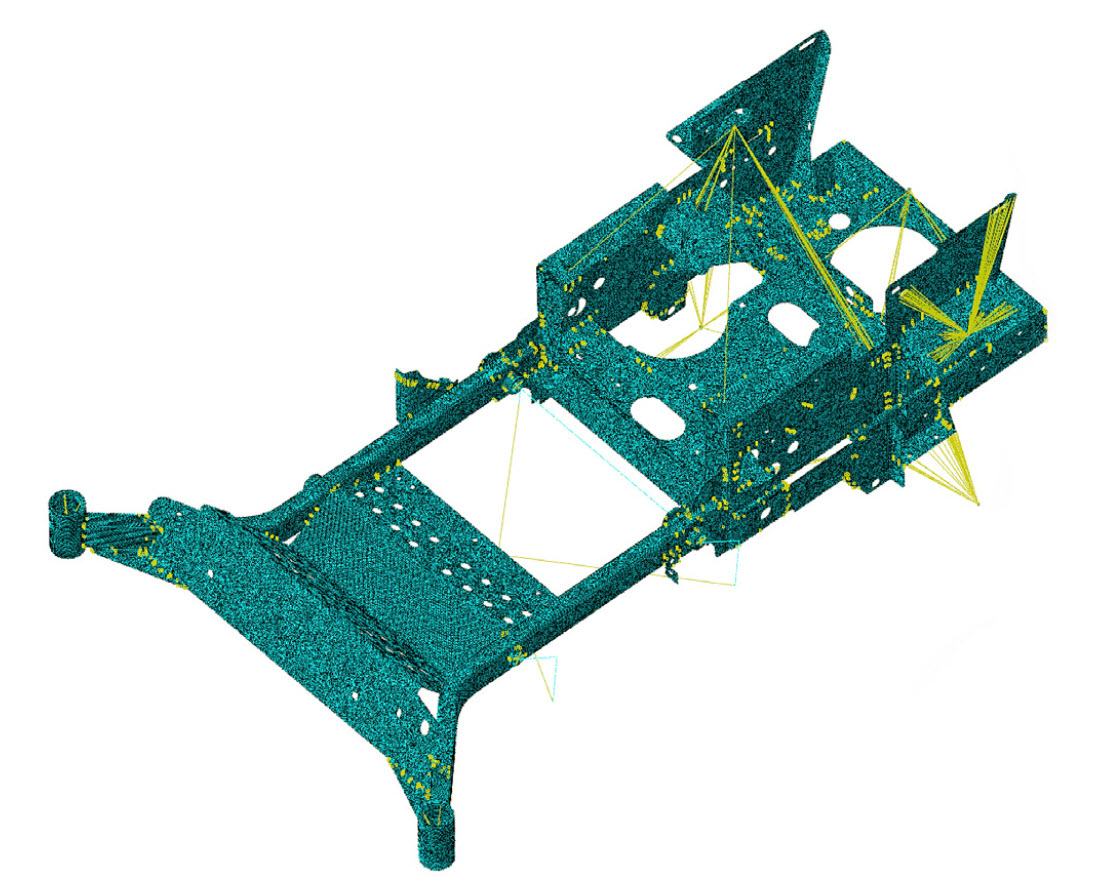
Saving Time with the SIMULIA Portfolio
Prior to using simulation software, Ariens engineers had spent much more time and money on field testing. “We would run a machine until it broke, go build another one, and run that one until it broke,” says Weglarz. “Now that we use simulation, by the time that we do go to run a physical test of a finished redesign, we are confident that it is going to work.”
“We use our time much more effectively and we are extremely efficient,” says Kobiske. “We now can simulate hours and hours of testing in just a fraction of that time.”
The new mower underwent final field testing at the Sebring International Raceway in Florida. As a way of saying “thank you” for using the space for testing, Ariens takes care of all of the grass at the race track and surrounding area.
Helping Upper Management Appreciate Simulation
When Weglarz initially approached upper management with the proposal to integrate SIMULIA tools into the design process at Ariens, he was met with some skepticism. But the visualization that Abaqus delivers helped bridge the gap, explaining why a design may or may not work—as opposed to the pass/fail results of a physical test.
“There’s so much going on inside of the software, that to try and explain everything that’s happening to a non-technical person is extremely difficult,” says Weglarz. “The visual aids that come with simulation are helpful in illustrating everything we’ve done to validate a design prior to actually building it.”
Although images and animations are helpful in demonstrating the power of simulation, the reductions in cost and time are what truly convinced upper management. “At first the investment in the software packages seemed daunting,” says Weglarz. “But after just one year, management was seeing reduced development time and increased efficiency. They’ve already said that the programs are well-worth what we’ve invested in them.”
Adds Kobiske, “The software clearly pays for itself.”
Promoting Collaboration between Designers and Engineers
The use of the SIMULIA portfolio also encourages greater communication between the engineers and the product designers at Ariens. Being able to show the design team areas of concern on-screen helped the engineers easily provide advice on how to redesign components.
“We get a STEP file from our designers, look at it, analyze it, and run it through fe-safe. From there we evaluate the structural concerns that surface and talk to the designers about them. They make the necessary changes and give a better design back to us,” says Weglarz.
“We—the engineers—are the structural guys. We don’t know all that goes into the packaging and other aspects that the design team is responsible for. The visual representation of the analyses we do help us work with them to understand both our structural needs as well as their packaging constraints.”
Exploring other Capabilities in the SIMULIA Portfolio
Ariens plans to continue to learn more about the power of the SIMULIA portfolio and implement new tools and strategies into their design process. They are looking to expand beyond Abaqus and fe-safe to produce the next-generation of lawn-care equipment - and it appears their focus is on topology optimization.
“Tosca, and also Isight, are two programs we are definitely interested in adopting,” says Kobiske. “For future generations of mowers we are going to keep improving our designs—making them more fuel efficient and easier to use. We want to continue down this path of product innovation.”
Although next-gen product ideas are confidential at this point, it is safe to say that simulation will be playing a key role in the development of something truly “cutting edge” at Ariens.