ANYWAVES
Founded in 2017, ANYWAVES develops high-performance miniature antennas for satellite constellations in arduous space environments. SIMULIA's CST Studio Suite helps engineers to test, validate, and accurately optimize each component. Comprehensive electromagnetic (EM) simulations ensure precision and reliable performance during space travel.
ANTENNAS PERFORM A CRITICAL ROLE
Satellites travel over 17,000 miles per hour at low-Earth orbit and use less gas than a Toyota Prius. More than half of the over 4,000 satellites orbiting Earth are used for communications purposes. That number will continue to increase as technology companies race to bring high-speed internet access to every corner of Earth. This increasing demand is spurring innovative approaches to satellite system design. Traditional satellite systems typically rely upon one large satellite high above Earth, which means data must travel a long distance, potentially causing latency. Another issue with traditional satellite systems is the potential disruption of connection that can be caused by a singular satellite going over the horizon and losing contact as Earth blocks its signal. These problems can be addressed by deploying multiple, smaller satellites in a constellation or swarm in low-Earth orbit. A lower orbit means data must travel a shorter distance, therefore less latency, and overlapping satellite coverage ensures constant contact with the signal. Smaller satellites are also typically cheaper to build, launch, and operate than traditional satellite systems. Whatever a satellite’s mission—telecommunications, navigation, Earth observation, etc.—antennas perform a critical role throughout its lifetime.
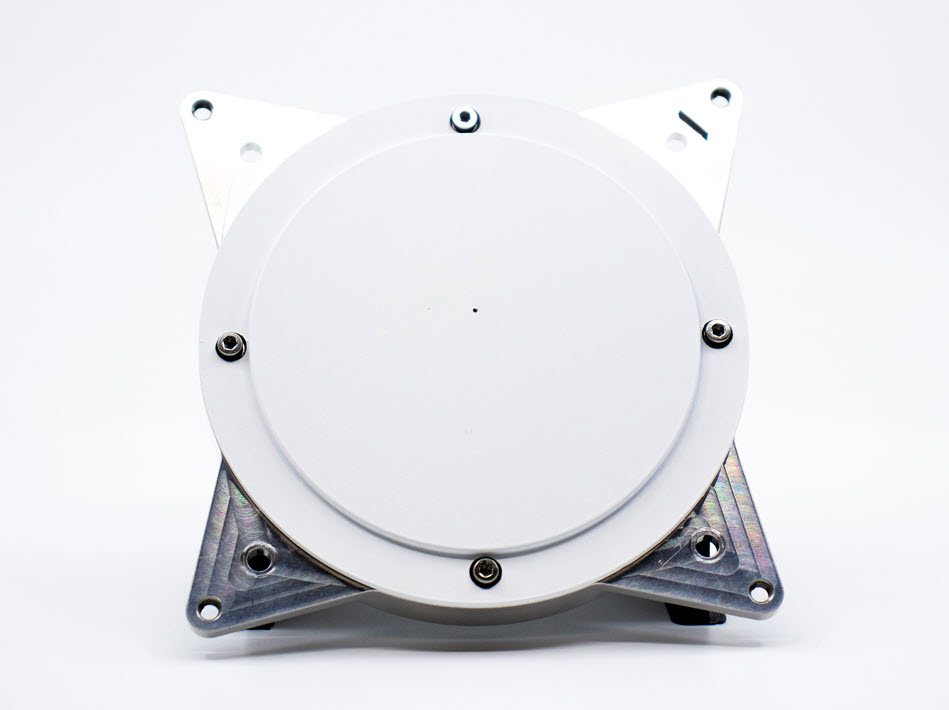
PERFECTING SATELLITE PERFORMANCE
ANYWAVES CEO Nicolas Capet holds a doctorate in electromagnetism and microwaves. He started his career at the French Space Agency (CNES) as an antenna engineer, overseeing antenna innovation for future applications. Capet has contributed to more than 65 scientific publications and 25 patents. Among them is a true technology breakthrough based on 3D printed substrates. In 2017 he created ANYWAVES, a CNES spinoff that develops innovative antennas for satellite constellations. Space antennas are crucial pieces of equipment that have a direct impact on satellite performance. A failure or malfunction could heavily impact the performance of a satellite or even cause a total shutdown. These factors, along with numerous physical and electromagnetic forces, make testing antennas mission-critical for product development success.
“Depending on the type of equipment, there can be between 3 and 20 antennas on a single satellite,” notes Capet. “Physical testing is extremely complicated and expensive. The design of antennas requires the integration of a multitude of physical criteria to verify that the components function correctly in all situations.” Once in orbit, satellite components cannot be repaired. Therefore, frequent testing becomes essential to building reliable equipment. “Failure is not an option,” states Capet. “Simulation is our day-to-day tool for optimizing new antenna concepts and refining the form and shape of our equipment.” With simulation, expensive and time-consuming physical testing can be minimized.
TRUSTING SIMULIA CST STUDIO SUITE FOR ELECTROMAGNETIC SIMULATION
Space equipment is meticulously designed and engineered down to the smallest details. Testing must be comprehensive and precise and produce reliable results. The complexity of satellites themselves demands rigorous processes, requirements, and testing. Because space is an unforgiving business, every single aspect of a satellite must be reviewed with a fine-tooth comb to ensure everything is right the first time to guarantee 100 percent mission success every time. What’s more, multiple types of physics, both on Earth and in space, need to be carefully tested to prevent any surprises after launch. Therefore, simulation at ANYWAVES is a tightly integrated part of the product development process. Mechanical, electromagnetic, thermal, shock, and more are continually tested from the earliest design stages until final delivery.
For example, radiated electromagnetic compatibility is one of the many tests performed to check how much interference radio frequencies introduce from satellite to satellite. This testing ensures signals do not interfere amongst themselves within a constellation, thereby preventing problems when operating and controlling individual satellites—critical testing for mission success. ANYWAVES chose SIMULIA CST Studio Suite®, a high-performance 3D electromagnetic analysis software package for designing, analyzing, and optimizing EM components and systems to simulate the entire range of potential EM interferences for its satellite equipment. The company needed software that was easy to use that would produce exact results every time. “SIMULIA CST Studio Suite is precise, and the simulation run times are extremely good,” reports Capet. “The choice, in the end, was obvious. CST Studio is a powerful, comprehensive, fast, and agile solution.”
SIMULIA CST Studio Suite is precise, and the simulation run times are extremely good. The choice, in the end, was obvious. CST is a powerful, comprehensive, fast, and agile solution.
CHANGING THE PRODUCT DEVELOPMENT GAME WITH 3D PRINTING
Capet recalls that when he first started working for space agencies, it took 10 years or more to launch a product from an entirely new technology to an object that could go into space. The enormous risks and costs involved necessitated an extremely long product development cycle. “Now, with simulation and other technologies, we can deliver our products 5 times faster than we used to,” says Capet. “We can demonstrate that our products are well-suited for space applications in two years [for a simple antenna] with this new ceramic 3D printed technology.” Capet discovered early in his career that 3D-printed ceramic antennas offer a reliable and flexible solution. Ceramic antennas can withstand huge temperature variations because ceramic is exceptionally stiff and resistant to radiation, therefore ideally suited to the harsh space environment. “Ceramic is remarkably difficult to model and fabricate using traditional methods,” says Capet. “3D printing allows us to design and manufacture complex shapes that are extremely thin and precise, which enables us to optimize the design and get the maximum performance from our equipment.”

TAKING LEAPS AND BOUNDS INTO THE FUTURE
Developing a quality antenna is just one challenge. Mass-producing antennas for the space domain with quick turnaround times and extremely high quality and reliability at competitive prices is quite another challenge. “Once you have demonstrated your technology is ready for space travel, there is still a lot of work to perform in order to equip all of the satellites and then to mass produce antennas,” says Capet. “Definitely our future challenge is two-fold: Continue to improve our competitiveness to deliver cost-effective and reliable equipment for our customers. And, to start developing more complex antennas because that type of antenna is key for our customers [going forward].” By leveraging SIMULIA CST Studio’s simulation and other technologies, ANYWAVES continues to impress its customers with its space equipment by designing and manufacturing a new generation of miniature, high-performance antennas for space applications. Thanks to this unique expertise, the Toulouse-based SME can produce custom-made miniature antennas for all types of satellites. With customers across the globe, ANYWAVES aims to become the world leader in innovative antennas for the satellite constellation market.
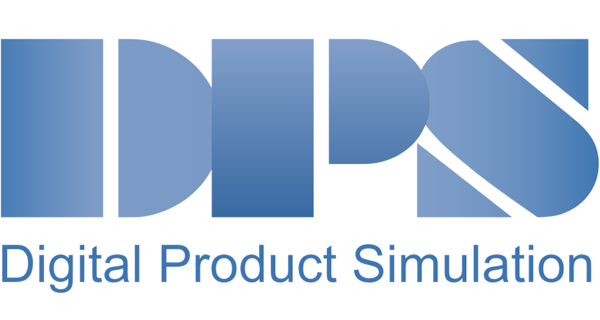
About DPS
DIGITAL PRODUCT SIMULATION (DPS) Digital Product Simulation, recognized for its expertise in digital engineering, offers high value-added services in this field and distributes Dassault Systèmes software. Specialized in the fields of computer-aided design, digital simulation and digital transformation of companies, the company employs more than 130 engineers dedicated to its customers such as Airbus, Devialet and Exotec. Although DPS markets CATIA, SolidWorks, Abaqus, CST and 3DEXPERIENCE software, the company’s strength lies in its mastery of the software it sells and its business expertise. Indeed, its engineers use the solutions sold by DPS on a daily basis in industrial projects. Thanks to this know-how, the company has opened a Qualiopi certified training center in order to better support its customers’ employees.
For more information: www.dps-fr.com