airinspace
During the COVID-19 pandemic, airinspace® required a solution that would help them simulate the performance of their air decontamination technologies in a variety of different use cases and high-risk environments. Using Dassault Systèmes’ SIMULIA technology, airinspace was able to demonstrate that adding their machines on top of existing air treatment systems in hospitals could significantly increase air decontamination.
FROM SPACE STATIONS TO HOSPITALS: AIR DECONTAMINATION IN HIGH-RISK ENVIRONMENTS
Established in France in 2002, airinspace is a pioneer in air and surface decontamination technologies, and develops professional solutions for hospitals, critical environments, and public access buildings.
“Our solutions are based on the innovative air decontamination technologies that were first created by Russians for the MIRir space station, and then developed further for the International Space Station,” says Stéphane Chatenet, the company’s CEO. “This scientific legacy is the foundation of our company.”
Starting as a collaboration between the European Space Agency and the Russian Space Agency, airinspace began by leveraging a technological patent for air treatment technology. The company then broadened its offering by developing products that could be used in medical environments such as hospitals.
“Of course, hospital needs are different to those of space stations, but ultimately the need is the elimination of contamination on a microbiological level,” Chatenet says. “As a result, the basic principle of our technology remains the same as it was in the early days.”
Today the firm operates in 50 countries and has installed over 6,300 indoor air quality and environmental contamination control machines, all of which have been designed and assembled at airinspace’s purpose-built production sites at Lisieux and Pruniers, in the Sologne and Normandie regions of France. All of airinspace’s machines are low energy consumption and have a long service life. The company uses materials that have a low environmental impact and favors the use of natural resources.
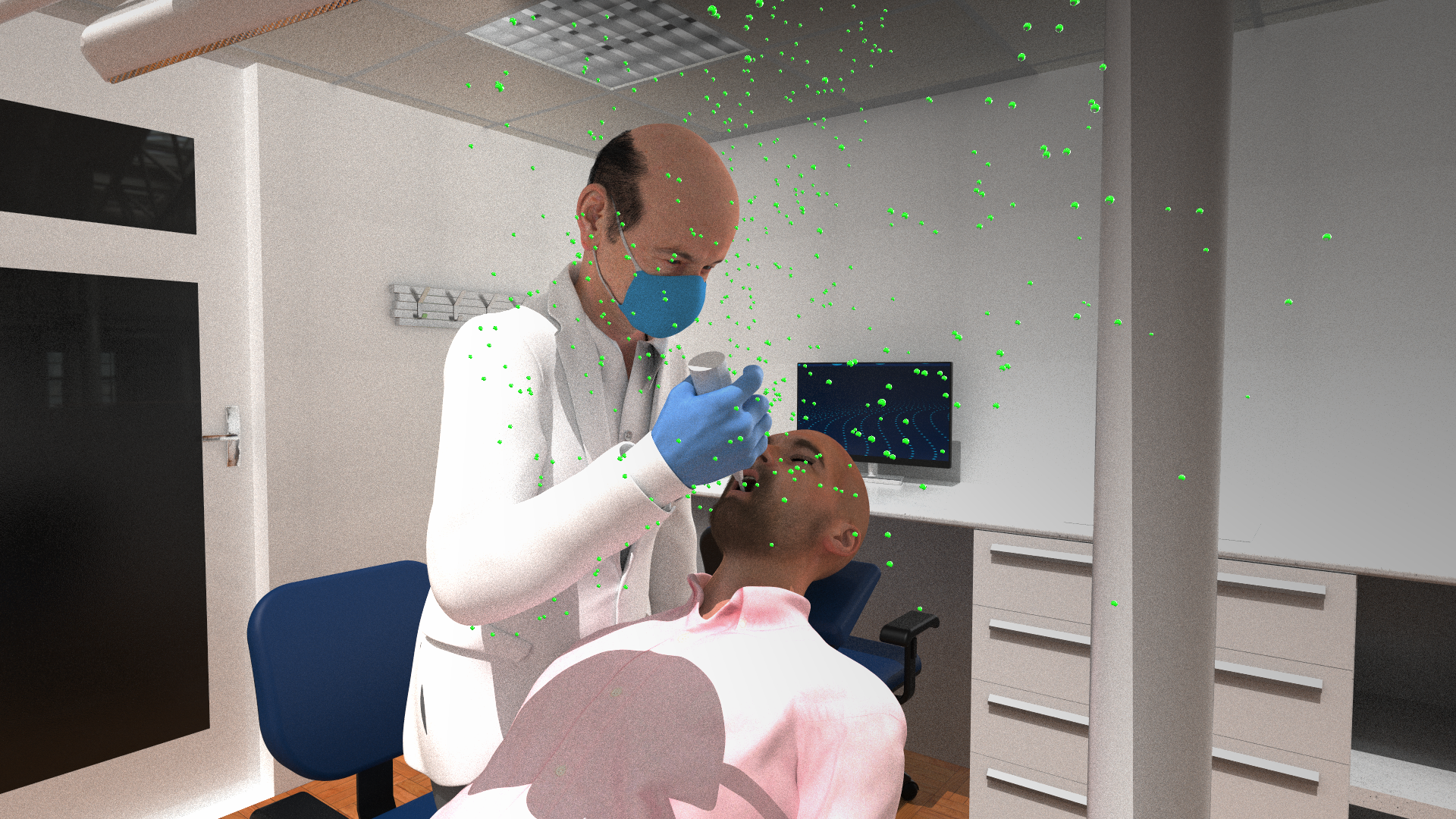
COVID-19: THE CLEAN AIR IMPERATIVE
While having clean air has always been vitally important for hospitals, it became exponentially more so during the recent COVID-19 pandemic. As a result, the team at airinspace realized they wanted to be able to better understand the impact their machines could have in high-risk environments.
“As well as advancing our solutions for hospitals during COVID–19, we developed a lot of products for new markets such as schools, canteens, and dental surgeries,” says Chatenet. “We wanted to demonstrate their effectiveness during this vital time.”
Having seen research by Dassault Systèmes about the Assistance Publique des Hôpitaux de Paris, which used simulation technologies to demonstrate that the air treatment systems in many hospital buildings weren’t equipped to filter out COVID-19 particles, Chatenet and his team were curious to see what difference could be made if airinspace machines were used.
“These studies seemed very relevant,” Chatenet said. “We were surprised by the power of the simulation technologies, and we knew we had to be a part of that research. We immediately got in touch with the Dassault Systèmes team and told them that we’d like to work with them.”
By using Dassault Systèmes’ SIMULIA technology, the team at airinspace was able to use simulation to demonstrate that adding their machines on top of existing air treatment systems significantly increased their performance. “It was fascinating,” Chatenet said. “We could simulate a wide variety of use cases to determine which products were best suited to which environments.”
For example, the airinspace team was able to simulate the impact of a corridor’s microbiological contamination on a side room in a hospital. In another scenario, it could simulate the dangers facing dentists when working inside a patient’s mouth.
“Usually customers can’t see how microorganisms behave because they are not only microscopically small, but they are invisible,” Chatenet says. “However, with simulation, we can make them visible—we can color them so that customers can see the contaminants. They can see the way particles spread across the room, and they can see how our machines treat them. As a result, customers quickly come to terms with the level of risk they face, and better understand the value of our products.”
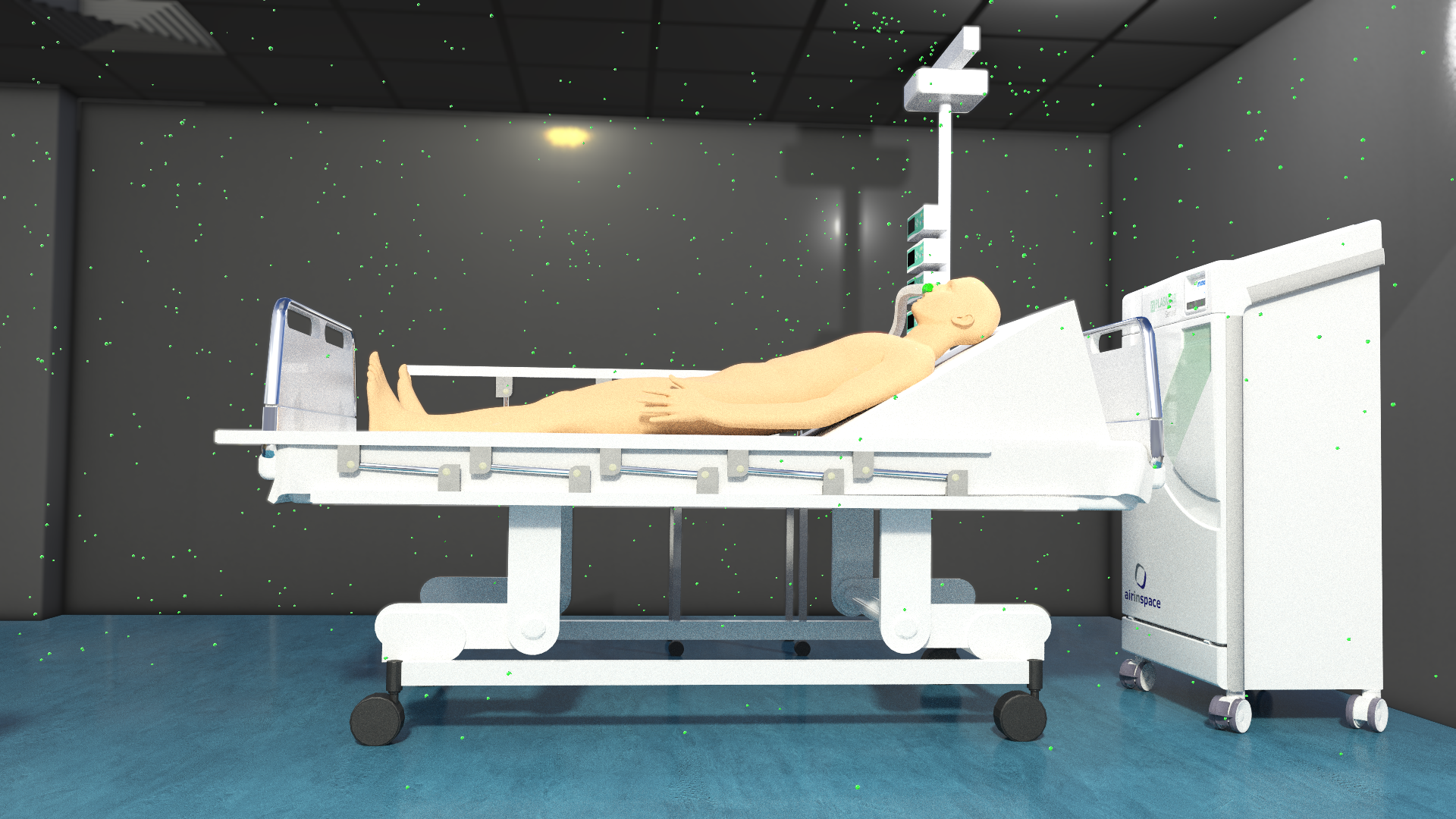
The simulation results were fascinating. We could simulate a wide variety of use cases to determine which products were best suited to which environments.
SIMULATING A SUCCESSFUL FUTURE
Following this success, Chatenet and his team decided they wanted to use SIMULIA solutions to simulate the performance of all of airinspace’s products. “It’s a continuous process,” Chatenet says. “The technology has become essential for us and our future development.”
Chatenet says that SIMULIA technology will allow his company to work much faster in the months and years to come. “Not only does it help customers understand the performance of our solutions more quickly than in the past, but it also allows us to avoid having to go through physical testing phases,” he says. “These phases are traditionally very time- and labor-intensive. Historically, they have prevented us from rapidly taking our products to market. Now I believe we can shorten the R&D phase by as much as four months.”
airinspace also plans to use SIMULIA solutions to simulate the operation of its new machines, even before they are built. “This will help with investment,” Chatenet said. “We can demonstrate the machines way ahead of the actual launch and even project ourselves into new market sectors. This is a very exciting proposition.”
Not only does simulation help customers understand the performance of our solutions more quickly than in the past, but it also allows us to avoid having to go through physical testing phases. Now I believe we can shorten the R&D phase by as much as four months.