Imperial College of London
Researchers at London Imperial College’s department of aeronautics were seeking ways to improve the strength, fracture response and damage tolerance of composite materials and graphene through the use of engineered microstructures.
The Nobel Prize in physics was awarded to Andre Geim and Konstantin Novoselov in 2010 for their work in the isolation and understanding of graphene, a two-dimensional honeycomb-like structure of carbon just one atom thick. Although the material was first theorized nearly one century ago, the term “graphene” was only coined in 1987 to describe the structure of recently discovered carbon nanotubes, as well as Buckminsterfullerene, a.k.a. buckyballs. But it wasn’t until 2004 that Geim and Novoselov were first able to isolate individual crystals of graphene, using a micro-mechanical cleavage process now known as the “Scotch tape” technique.
Graphene is an amazing material. Found in everything from pencil leads to human DNA, it is 100 times as strong as steel by weight but far more elastic. According to Geim and Novoselov, a theoretical one-meter square hammock made of graphene would be strong enough to support a napping house cat, yet would weigh less than one of the cat’s whiskers and be nearly invisible. Graphene is more electrically conductive than copper, dissipates heat ten times faster, and is virtually impermeable to gases, giving it broad potential for use in semiconductors, fuel cells and batteries, gas sensing equipment, solar panels—and especially composite materials.
It’s this last possibility that brings Silvestre Pinho to work every day.
Studies in simulation
Professor Silvestre Pinho is a member of the engineering faculty at London’s Imperial College department of aeronautics. He and his team of postdoctoral researchers and Ph.D. students use Abaqus finite element analysis (FEA) tools from SIMULIA to study the structural design and simulation of graphene, carbon fiber reinforced plastic (CFRP), and similar materials. Their goal? To improve the strength, fracture response, and damage tolerance of composite materials through the use of engineered microstructures. Their work could be described as building a stronger house by engineering the internal structure of each brick, or making cars safer by designing chassis and body parts from the molecular level up.
In fact, this last application is one likely outcome of the team’s studies. Some current real-world examples of where these new materials could be used include aircraft fuselage, race-car bodies, and the blades of wind turbines or helicopters. And once the manufacturing processes for these microstructurereinforced composites become commonplace and production costs come down, Pinho envisions them being used in a wide variety of everyday products.
“Carbon fiber is already used today in electric vehicles, but one limitation is fracture toughness,” he says. “Anywhere you have a large structural component, there are geometric discontinuities—the intersection of an aircraft fuselage with an engine cowling, for instance, or the window frame in a passenger vehicle—that present areas prone to failure in the event of a crash or overload.”
An early Abaqus user
Pinho studied at the University of Porto in Portugal, earning his undergraduate degree in mechanical engineering. It was there that he first began using Abaqus finite element analysis (FEA) in his work. Two years later, he moved to Imperial College in London to pursue a Ph.D. on the simulation of mechanical response in composite materials. Just before completing his doctorate, however, he received an offer to stay on at the college as an academic, and has been there ever since. “I used a different FEA software while doing my doctorate on composite crash behaviors, but went back to Abaqus once my first research project was funded,” he says. “I’ve been using it exclusively for the past five years.”

Pinho says he became an engineer because he was good at math and physics, and felt that path offered him a nice balance between theoretical science and the real world. But when news of Geim and Novoselov’s discovery came out, he got to thinking about some practical uses for the new graphene material. “I thought that within the next decade or so, people should be able to manufacture interesting things with it,” he says. “That in turn created an immediate need for simulation and analysis of its properties, something I knew Abaqus could help me with. Based on that, we spent the next several years developing the molecular-dynamics code needed to simulate graphene and other carbon-based structures within the Abaqus finite element framework.”
Plugging into the right level of simulation
His project involves far more than simulation of a few carbon atoms. Pinho is studying the mechanical response of “very large sandwich structures subject to a very localized load that could lead to failure in that very localized place.” This would mean events such as bird strike in a carbon-fiber aircraft wing, or hail damage in a solar array. He says representing threedimensional structures such as these requires a coarse model at the macro level, inside of which sits a concentration of microsized detail at the place where the damage will occur.
“There are many different numerical formulations that help with these types of problems, and Abaqus has several of them implemented by default,” Pinho explains. “One of the more useful ones is the ability to have different length and time scales in your analysis. For instance you can, in-effect, zoom in on the crash zone with Abaqus/Explicit, which provides a very high level of discernment, and then as you move farther away you would use Abaqus/Standard, employing much larger three-dimensional constructs but at lower resolution.”
Because the user interface in Abaqus is very “plug-in friendly,” Pinho and his team have been able to develop their own subroutines that complement and expand the software’s native capabilities. “The interfaces in Abaqus that support user subroutines are particularly well-organized, well-structured, and offer quite a lot of freedom,” he says. “It’s very powerful, and is a key feature for us.”
“Shaking hands” between meshes
Another challenge is accurate representation of the “handshake regions” between the different meshes used to simulate the microstructures within carbon composite materials, which in effect links small-scale models with larger ones. For this reason, Pinho and his students have experimented with different mesh superposition techniques in Abaqus, allowing them to develop schemes that have greatly reduced the computational time needed to perform such complex analyses, while still maintaining excellent accuracy in their models.
“The ability to create handshake regions between meshes was quite important to our work,” Pinho says. “Without it, it would be far more difficult to perform simulation of large structures simultaneously with the underlying material’s microstructure.”
Helping develop new capabilities in Abaqus
Pinho has collaborated with SIMULIA throughout this complex work, and has even influenced the Abaqus software development path to some extent. “There was one case where SIMULIA had just released a new phantom-node method, but I along with other researchers wanted to implement our own criteria for failure initiation inside the new method,” he says. “SIMULIA invited me to submit my own interface design, which was subsequently approved and released to me in beta version within a very short time frame. This allowed me to explore different failure possibilities much more quickly than would otherwise have been possible.”
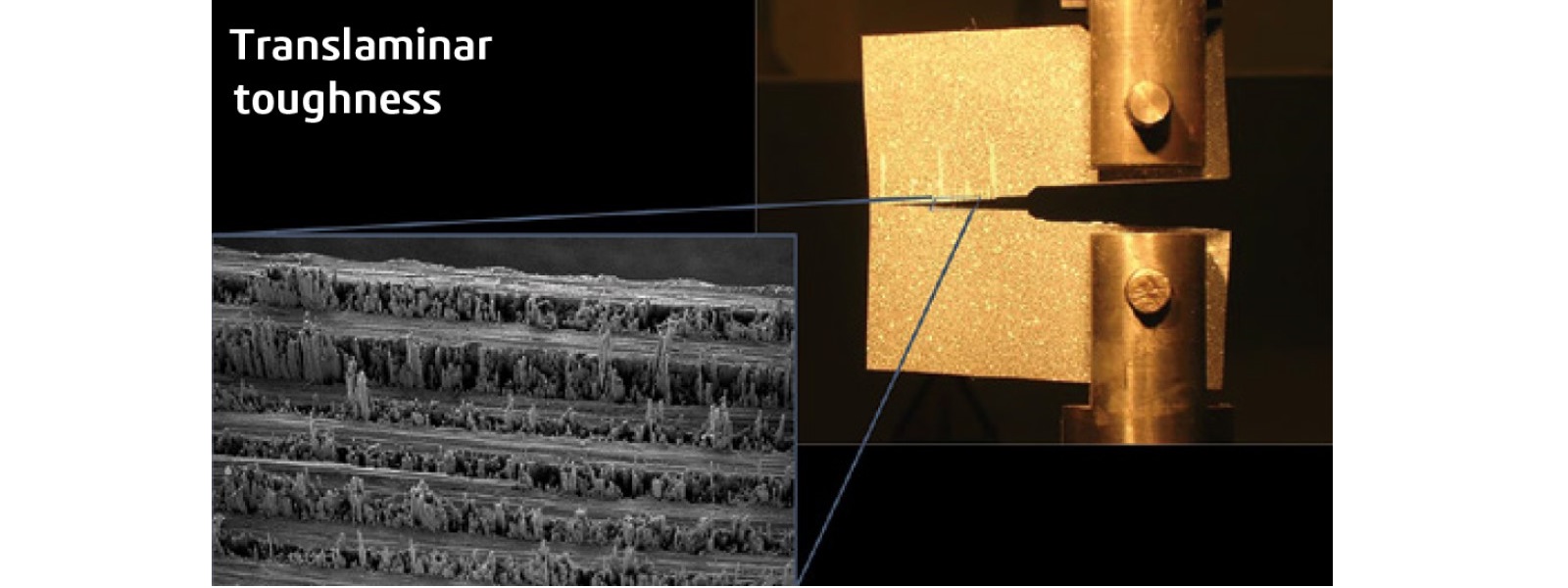
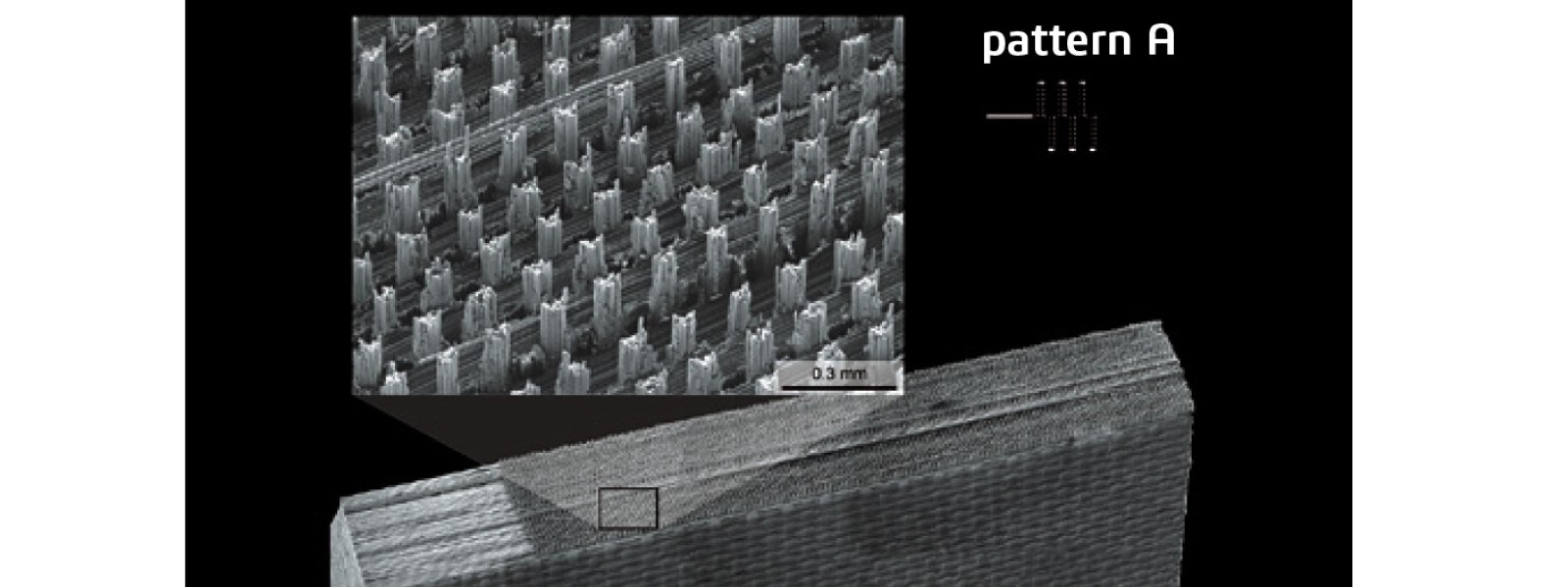
While the majority of Pinho’s current work with Abaqus is devoted to micro-structural modifications of carbon-fiberreinforced composites, this work has led to several valuable lessons which are useful for nano-structural design using graphene. The physics and mechanical interactions at graphene’s molecular level are admittedly quite different from those of a carbon-fiber aircraft component, but Pinho says a fundamental understanding of each is critical to increasing fracture toughness in carbon-based materials.
“Everything we’ve learned about numerical methods within Abaqus, and the knowledge of how the different features of the finite elements code are organized, allows us to understand how we could express the equations that come from the interaction of individual atoms in a way that can be formally equivalent to the equations Abaqus expects to solve,” he says. “Knowing that we could do all these things within the finite element framework of Abaqus itself has been quite important to our work. It’s a very powerful tool.”
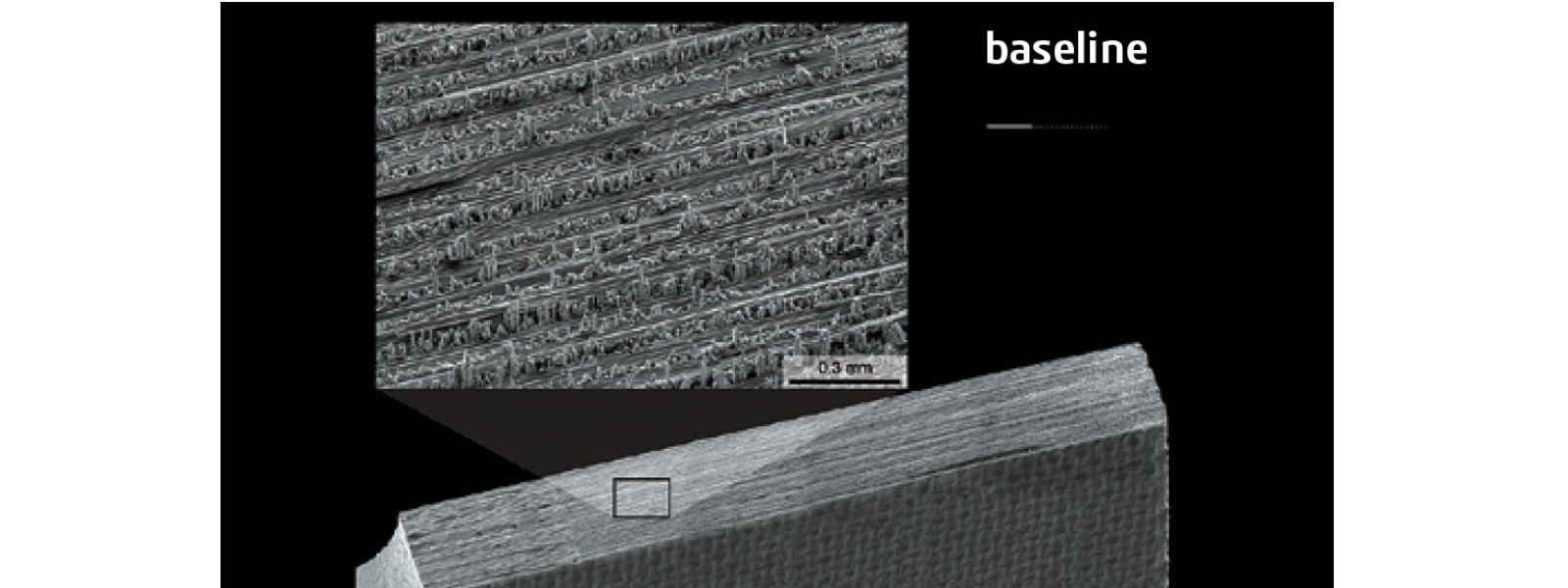
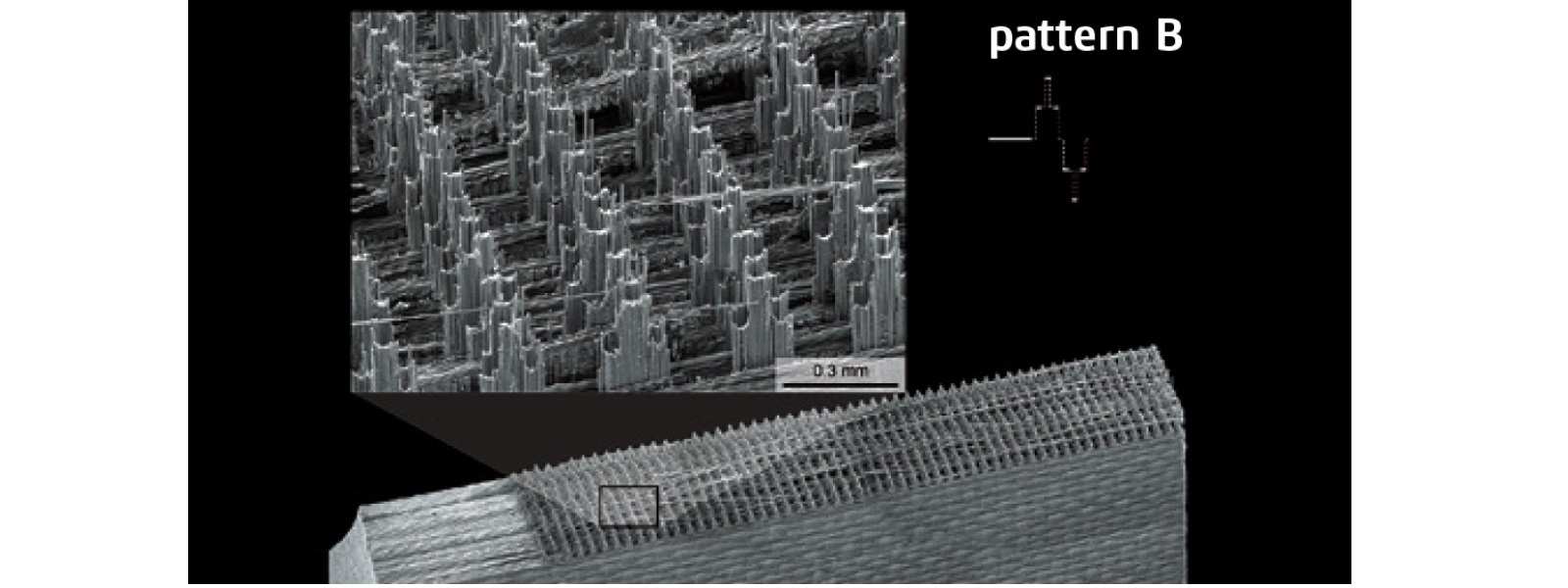
Toughening up microstructures
With a material ten times stronger than steel, crash-proofing would seem to be unnecessary, but graphene and to a lesser extent carbon fiber have an Achilles heel: they’re brittle. For two-dimensional graphene, breaking the van der Waals bonds between the graphene crystals is fairly easy to do, the atomic equivalent of poking your finger through a pile of paper. And carbon fiber composites are known for their propensity towards delamination and impact cracking.
In both cases, Pinho seeks to manipulate the structures of those materials at the micro or even nano level. He cites one theoretical possibility where two graphene sheets might be connected by a series of carbon nanotubes, greatly increasing its crack resistance. A more real-world example is one where Pinho and his colleagues were able to construct polymeric microstructures in carbon fiber composite material, increasing its energy dissipation capability.
“Basically, we modify the microstructure of each individual ply before the material is cured and the end result is a material with 560% percent the fracture toughness of the baseline carbon-fiber material. We’ve demonstrated it can be done; the next step is how to do so on an industrial scale. I imagine that within the next few decades, we will hopefully have the ability to design nanoscale structures, and tailor them to produce whatever mechanical properties we want them to have.”