Sustainable manufacturing Hackathon
20 students from various academic disciplines came together for the first-ever Dassault Systèmes Hackathon focused on sustainable manufacturing solutions.
Inventing new ways of producing and consuming is vitally important. Currently, manufacturers focus on efficiency, but their attention is shifting towards sustainability. Producers that fail to align themselves with sustainability objectives will find that their products and services fall below their customers’ expectations, and they will struggle to find a market for them.
By testing ideas, products and experiences virtually before offering them in the real world, producers can find new, respectful ways of operating. In this way, virtual universes are catalysts for change, connecting and contextualizing the exponentially growing volume of data. Only the digital world provides a suitable platform for the observations and decisions needed to devise new methods of production. Therefore, using virtual technology increases efficiency in the real world.
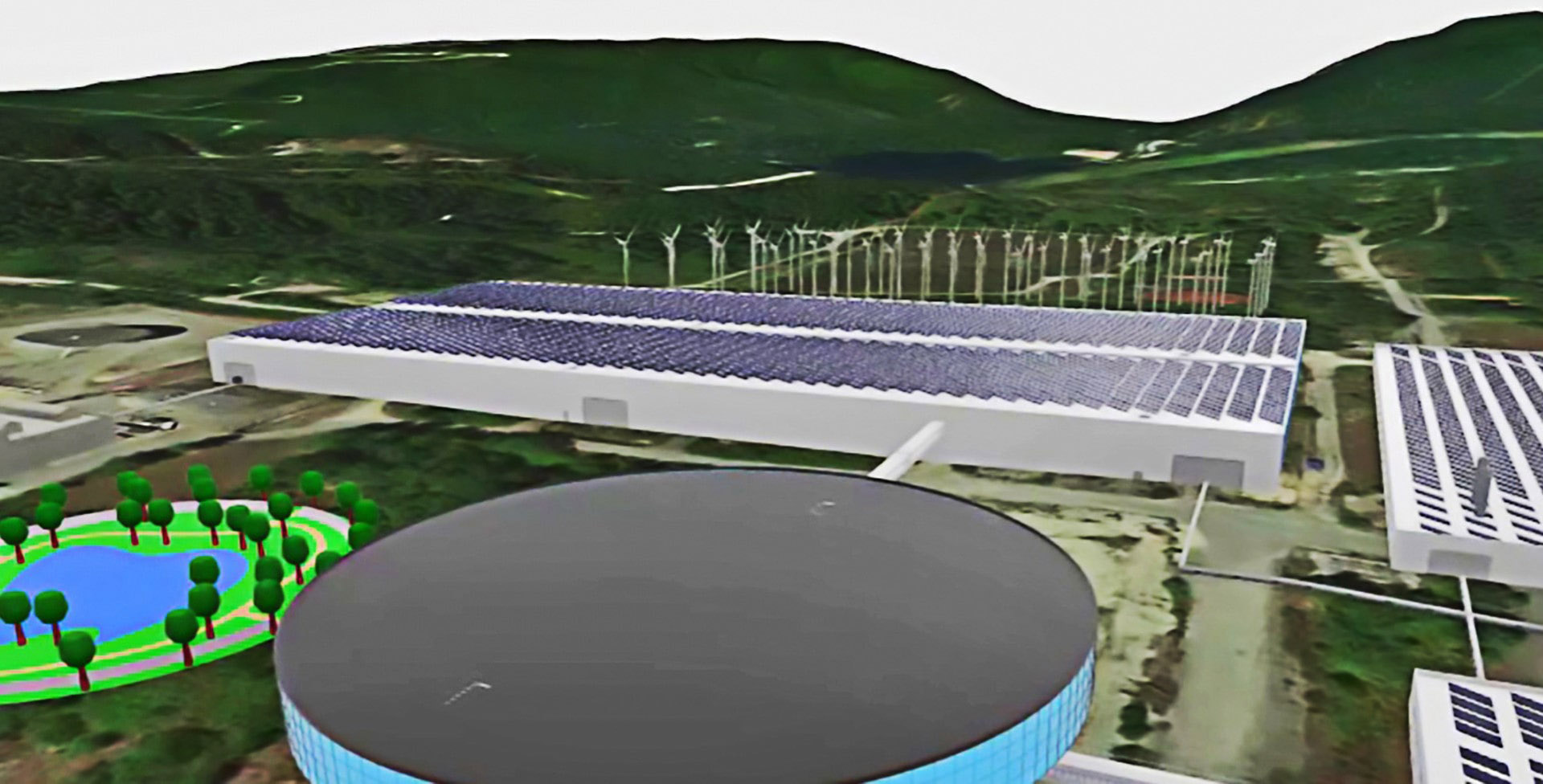
To demonstrate the power of virtual worlds to make manufacturing more sustainable, 20 students from around the world and from various academic disciplines came together for the first-ever Dassault Systèmes Hackathon focused on sustainable manufacturing solutions.
Four teams with five students each used the 3DEXPERIENCE platform; they worked, innovated and collaborated intensively over 48 hours before presenting and discussing the fruits of their labor. The yellow team focused on recycling plastic waste found in ocean gyres. Their concept was for autonomous boats to collect the plastic, which would be recycled to build houses using additive manufacturing. The recovered plastic also would be used to make water collection systems: plastic nets resembling spider webs would be used to condense morning mists into water droplets. The green team designed a “sunflower-factory” in which nature and technology would work in synergy.
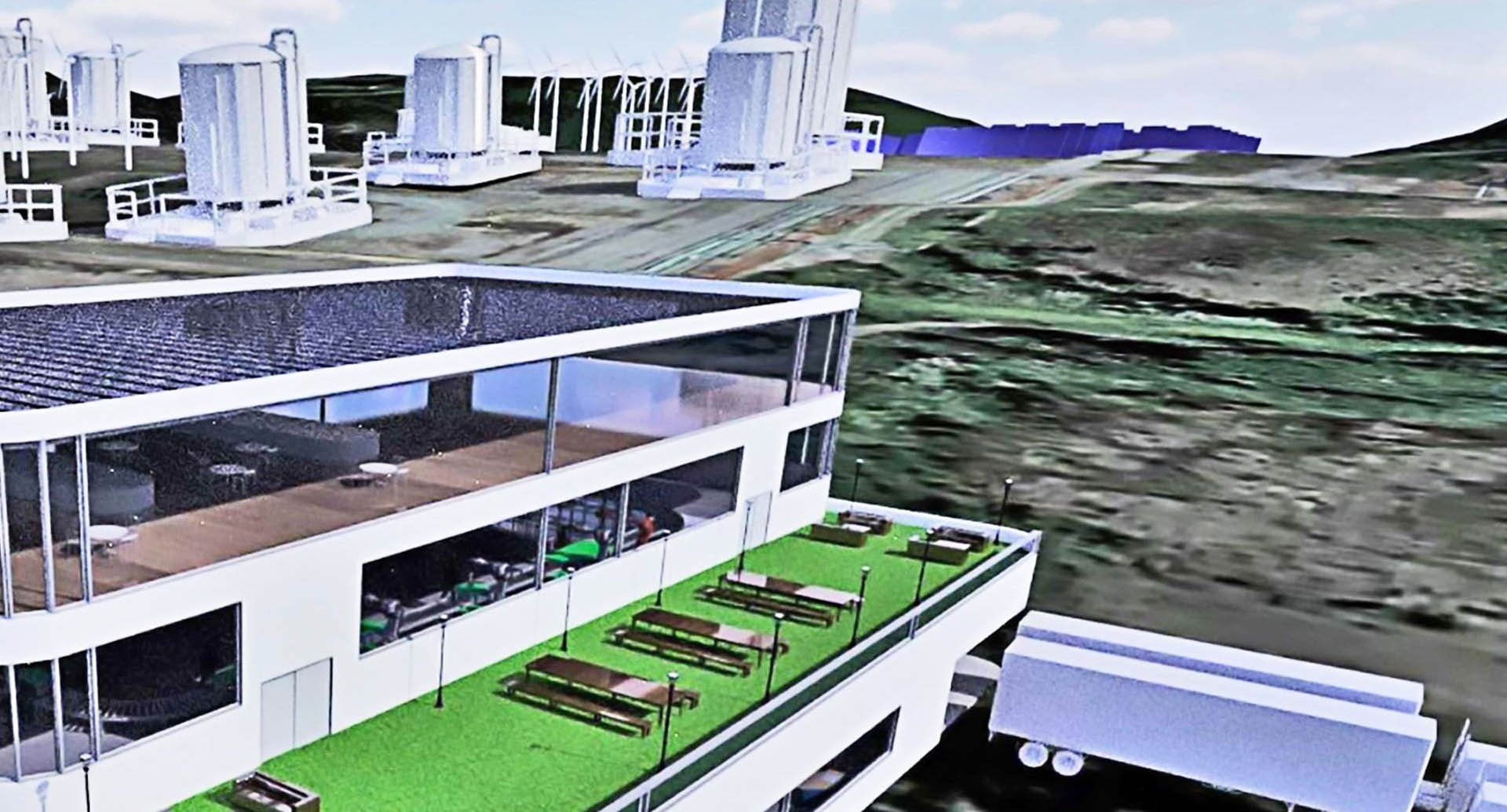
This factory of the future would use biomimetics – using elements of nature to solve complex human problems – to adapt to its environment. Like a sunflower, the factory would absorb sunlight and blend in with nature, a self-sufficient ecosystem powered by its environment. The blue team’s main goal was to create a healthy environment within a factory. With large windows and solar panels on the rooftop, the factory would contain green spaces in which employees could relax. Its second aim was intelligent resource synchronization: process sequencing, self-guided vehicles, automatic storage and retrieval systems, and robots that collaborate with humans.
The red team, which won the Hackathon, proposed a way in which various companies in the same area could collaborate and share resources. Employee well-being would be improved through access to a nursery and fitness center, as part of a post-modern industrial complex. The approach would also enhance the manufacturing process itself through the sharing of skills and the pooling of certain technical services. By integrating the supply chain, carrying out joint operations, and sharing logistics facilities, storage costs could be reduced and production capacity increased.