Jakob Müller
Optimiert weltweite Produktentwicklungsprozesse mit CATIA und ENOVIA
„Es ist schon schwierig genug, an einem Standort eine Zeichnung zu finden. Sind die Zeichnungen an zwei oder mehr Standorten verteilt, wäre die Fehlerrate ohne PLM-System einfach zu hoch. Das hätten wir ohne ENOVIA nicht geschafft.“
Weltmarktführer in der Etikettenherstellung
Fast jeder Mensch besitzt irgendeine Art von Kleidungsstück, das auf den Maschinen der Jakob Müller AG gefertigt wurde: Kleideretiketten, Reißverschlussbänder, Gurte oder Wirkspitze. Die Textilmaschinen des Schweizer Maschinenbauers liefern hochleistungsfähige Lösungen zur Herstellung von Schmaltextilien und Bändern in erstaunlicher Detailgenauigkeit und Geschwindigkeit. Mit 120 Jahren Erfahrung und einem Marktanteil von mindestens 50 % ist die Jakob Müller AG der Weltmarktführer bei Etiketten.
Das Unternehmen hat 1.200 Mitarbeiter an sechs Produktionsstandorten in der Schweiz, Deutschland, Italien, Indien, China und der Tschechischen Republik sowie fünf weitere Verkaufsniederlassungen. Über die Hälfte der Mitarbeiter sind am Schweizer Standort Frick für die Entwicklung, die Konstruktion und den Bau der Maschinen und Systeme zuständig.
CATIA für Konstruktion und NC-Programmierung
Seit Mitte der 1980er-Jahre setzt die Jakob Müller AG CAD-Technologie ein. CATIA und ENOVIA wurden im Januar 2005 eingeführt. 2006 implementierte Jakob Müller eine NC-Lösung auf der Basis von CATIA-CAM Modulen, verbunden über ein Tool-Managementsystem und eine direkte, digitale Steuerungslösung.
CATIA wird für die Konstruktion und Prüfung komplexer Teile der Textilmaschinen von Jakob Müller eingesetzt, beispielsweise bei der Simulation von Kinematik oder bei der Festigkeits- und Dynamikanalyse. Bei der Herstellung von Teilen wird die NCProgrammierung eingesetzt. Die CATIA-Lösung für die NC-Programmierung bietet Optimierungskapazitäten, um Stillstandszeiten in den zunehmend komplexen Produktionszentren zu reduzieren.
„Wir haben immer weniger Bearbeitungszentren, diese werden aber immer größer und komplexer“, so Adrian Brogle, Leiter der Abteilung Computer Science bei Jakob Müller. „Da kann man sich keinen Stillstand leisten, die Anlagen müssen laufen. Früher konnte man Programme viel schneller ändern, weil man es direkt an der Maschine machte, aber inzwischen sind zwei Stunden NC-Programmierung billiger als eine Viertelstunde Stillstand – die neue NC-Lösung macht sich also schnell bezahlt.“
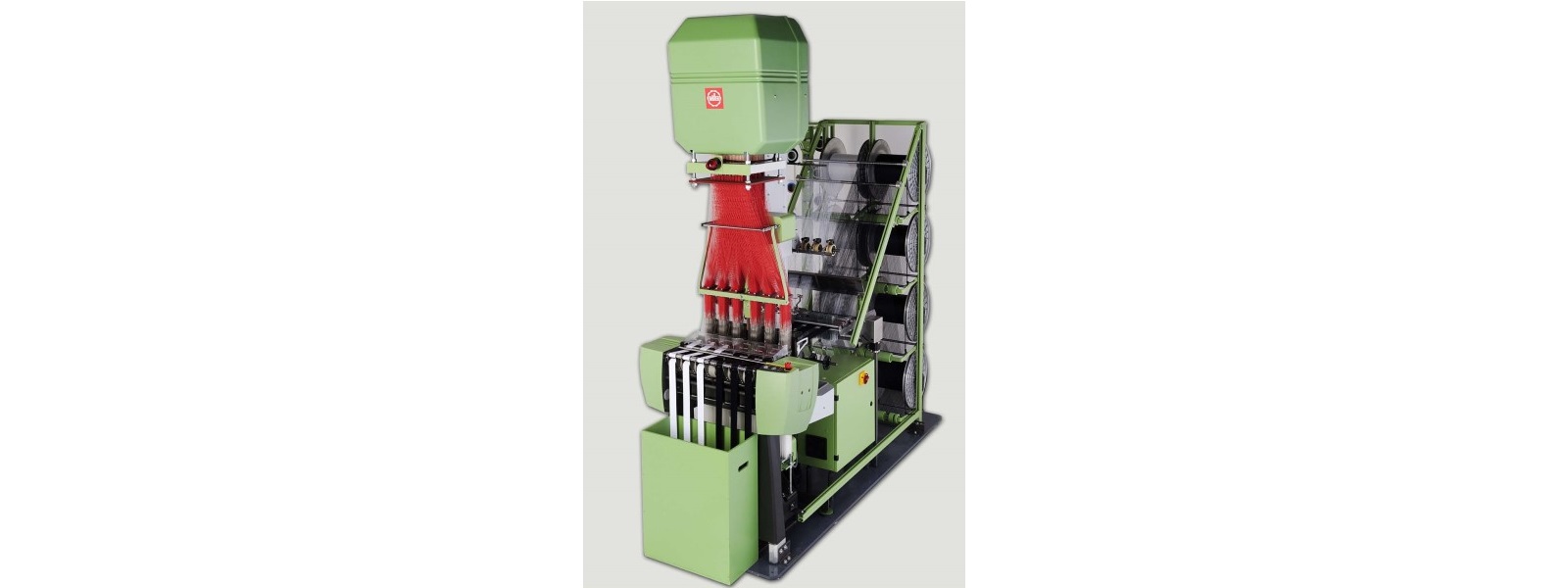
ENOVIA erhöht die Transparenz bei der Verwaltung von Engineering Change Orders
Die Entscheidung von Jakob Müller für ENOVIA, einschließlich Engineering Central und Program Central, basierte auf der Fähigkeit der Lösung, flexible Workflows und standortübergreifende Installationen zu unterstützen, aber auch auf der integrierten Web-Technologie. Wenn man einen Mitarbeiter von Jakob Müller befragt, welcher ENOVIA-Workflow heute am wichtigsten ist, so lautet die Antwort meist: der Engineering Change Order (ECO)-Prozess. Er dient dazu, Änderungen in die laufende Serie einzubringen, indem er das Auschecken, die Überarbeitung und die erneute Freigabe des geänderten Bauteils steuert.
„Wir wissen jederzeit genau, welche Produkte und Normteile wo verwendet wurden“, so Massimo Ratti, CAX/PDM Applications Manager bei Jakob Müller. „Und wir wissen, welche Änderungen vorgenommen wurden und so weiter. Außerdem werten wir den ECO-Workflow aus und sehen so, wie lange es dauert, eine Änderung in die Serie umzusetzen. Daraus wiederum lässt sich erkennen, wo die Flaschenhälse im Prozess liegen. Ich kann den Durchlauf einer ECO genauestens überwachen und gezielt ansetzen, um die Durchlaufzeiten zu verkürzen. Das ist auch für die Abteilungsleiter ein wichtiges Werkzeug für die Prozessoptimierung und -überwachung. Wenn ein Teil in den Änderungszyklus geht, wird dies dem Einkäufer angezeigt, damit dieser nicht zu viele veraltete Teile bestellt.“
ENOVIA besitzt eine Schnittstelle zum ERPSystem und ist das führende System, wenn es um Stücklisten und Stammdaten geht. Die Daten werden in das ERP-System übernommen. Vorher werden die Entwicklungsdaten in einem speziellen Workspace in ENOVIA gespeichert. Das hat den Vorteil, dass die Rechteverwaltung unter ENOVIA schon genutzt werden kann, bevor noch vollständige Stammdaten für jedes Teil existieren. Von jedem einzelnen Teil kann der Konstrukteur entscheiden, ob und für wen es sichtbar sein wird. Ist der Prototyp fertig und die Entwicklung abgeschlossen, wird der ECO angestoßen und die Stammdaten in das PLM-und weiter in das ERP-System übertragen.
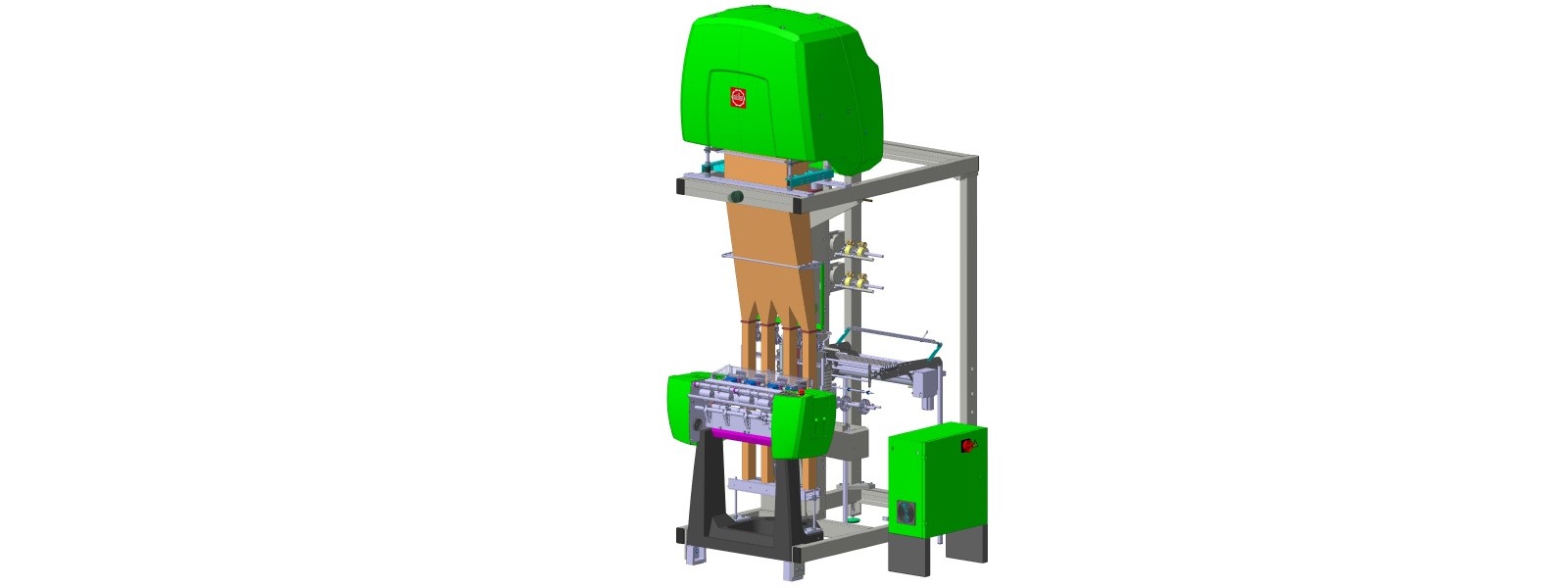
ENOVIA sichert den Datenzugriff
In der Rechteverwaltung ist jeder Jakob Müller-Standort ein eigener Mandant, und die Anwender eines Standortes können zunächst lediglich auf die lokalen 3D-Daten zugreifen. Jeder Konstrukteur kann seine Modelle jedoch „freischalten“, so dass sie von den anderen Standorten aus genutzt werden können. „So können wir genau bestimmen, welche Daten die Standorte beispielsweise in China zu sehen bekommen“, erklärt Brogle. „Und in einem speziellen Workflow laufen die Änderungen, die beispielsweise die indischen Kollegen machen, um Teile den dort verfügbaren Halbzeugen anzupassen, zur Freigabe über uns.“
Mit dem Hochfahren der Produktion an den weltweiten Standorten ist es von kritischer Bedeutung, diese Kontrolle aufrechtzuerhalten. Massimo Ratti dazu: „Das hätten wir ohne ENOVIA nicht geschafft. Es ist schon schwierig genug, an einem Standort eine Zeichnung zu finden. Sind die Zeichnungen an zwei oder mehr Standorten verteilt, wäre die Fehlerrate ohne PLM-System einfach zu hoch.“
Wichtig findet Ratti, dass überall mit denselben Werkzeugen gearbeitet wird, aber auch, dass die Methoden eingehalten werden. So wurde es in Frick unmöglich gemacht, Kopien von Zeichnungen lokal abzulegen - damit kann es nicht passieren, dass mit einer veralteten Zeichnungsversion gearbeitet oder gar gefertigt wurde.
Um zu gewährleisten, dass immer aktuelle Daten vorhanden sind – und als Maßnahme zur Datensicherung – checken die Konstrukteure mit Hilfe von ENOVIA morgens ihre Eingangsdaten und abends ihre Ausgabedaten. Damit ist gewährleistet, dass bei jedem Konstrukteur die Schnittstellen zu den benachbarten Teilen in der Anlage immer möglichst aktuell sind. So wird eine parallele Entwicklung vereinfacht
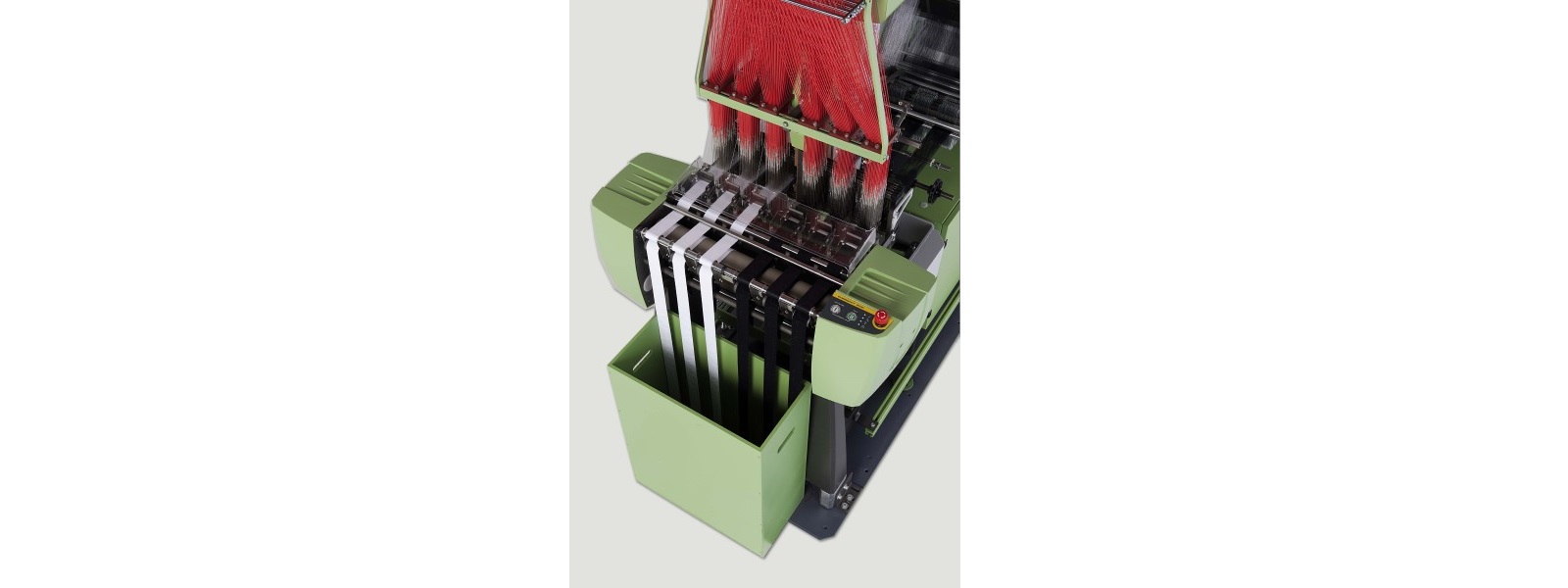
Die richtige Wahl
„Die tatsächlichen Potentiale unserer Entwicklungsumgebung erschließen sich auch uns erst mit der Zeit“, so Brogle. „So ergeben sich immer mehr Synergien, zum Beispiel kann unsere neue Messmaschine CATIA-Daten verarbeiten, so dass Soll-IstVergleichsmessungen sehr einfach werden. Wir haben zum Glück auf CATIA übergewechselt. Sonst hätten wir heute um einiges mehr Probleme. Zu der Zeit der Einführung waren unsere Niederlassungen in Indien und China noch unbedeutend, heute ist die abgesicherte und gelenkte Kommunikation mit ihnen ein entscheidender Punkt. Die Rechtevergabe wird von Europa aus gesteuert, so können wir das Know-how im Land halten.“
Rückblickend ist Massimo Ratti mit der Implementierung der Lösungen von Dassault Systèmes sehr zufrieden: „Wir haben zum richtigen Zeitpunkt das Richtige getan.“
„Die tatsächlichen Potentiale unserer Entwicklungsumgebung erschließen sich auch uns erst mit der Zeit. Wir haben zum Glück auf CATIA übergewechselt. Sonst hätten wir heute um einiges mehr Probleme.“