Identifying new performance drivers through a combination of AI and 3D technology
Digital transformation, artificial intelligence, IoT and deep learning provide opportunities for manufacturers to reinvent the way they think and operate.
Laurent Bertaud, head of Strategy, Sourcing & Standardization Intelligence at Dassault Systèmes’ subsidiary NETVIBES-EXALEAD, and Morgan Zimmermann, CEO of NETVIBES-EXALEAD, spoke to us about these major developments.
When you talk about artificial intelligence within a company’s purchasing function, what do you mean?
Against a background of increasing complexity, we believe that it is crucial for the purchasing department’s strategic position that it should have a say on design and engineering matters as early as possible. This involves machine learning algorithms, which are central to engineering operations, but guided by the purchasing department.
The algorithms make it possible for the two functions to talk to each other, opening up new ways of enhancing performance and reducing costs.
How can a purchasing department make use of AI, in practical terms?
In the aerospace sector, AI is used to cross-reference engineering and purchasing information about existing components between different programs and production sites. It helps the purchasing department to define context-specific standards, check that they are applied properly, and optimize sourcing on a global scale.
The resulting cost savings free up resources for innovation, which is vital for manufacturers.
Does the purchasing department have its own control interface?
Buyers have their own dashboard, which acts as an interface with the engineering department. Combining AI with the 3D signature of components allows purchasing staff to have a better understanding of the engineering department’s requirements, analyze existing orders and identify potential cost savings and other areas for improvement.
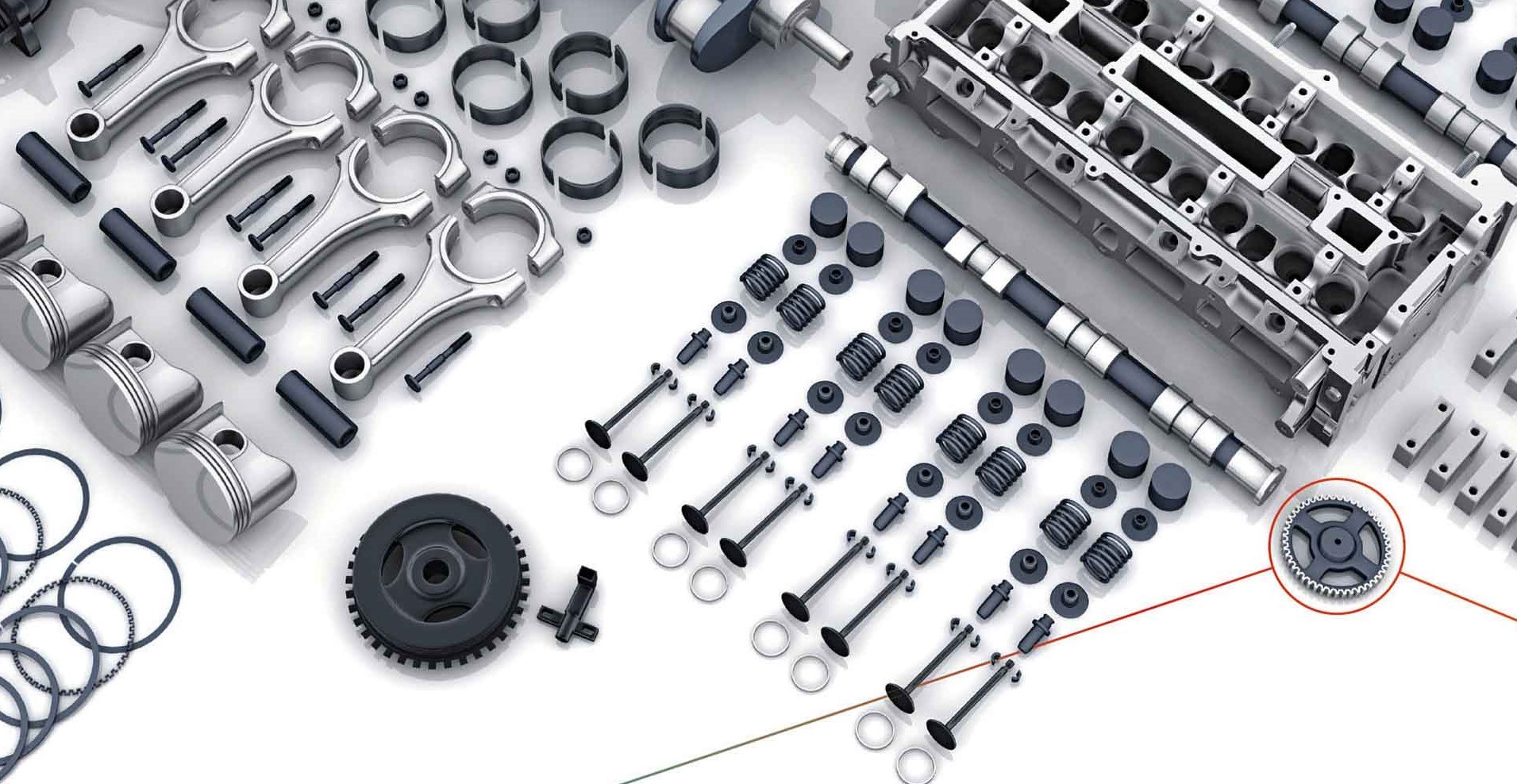
What results are your customers achieving?
One Tier 1 supplier of aerospace subsystems estimates that it has achieved annual savings of 15 million euros (US$16.83 million)., and an industrial machinery manufacturer puts its savings at 65 million euros (US$72.9 million) per year. This shows that there is untapped potential to optimize performance compared with standard technologies.
However, the sourcing and standardization phases are very hard to automate, unlike billing, for example. Manufacturers may say that they have adopted policies to improve sourcing and have tried-and-tested standardization rules, but mostly these involve manual processing on a spreadsheet. They remain dependent on the quality of data entered into an array of different systems.
So where should they start?
They need to start by connecting their engineering and financial systems globally, using 3D recognition as a universal language, and offer a simple collaboration solution. The 3DEXPERIENCE platform and its business analytics functionality, along with the Marketplace PartSupply service, make this possible.
With those capabilities, the purchasing department can strike the right balance between sales, finance and engineering. In two or three years’ time, it will be standard practice for purchasing departments to use advanced analytics applications. Now is the time to adopt this technology, in order to get a competitive edge.
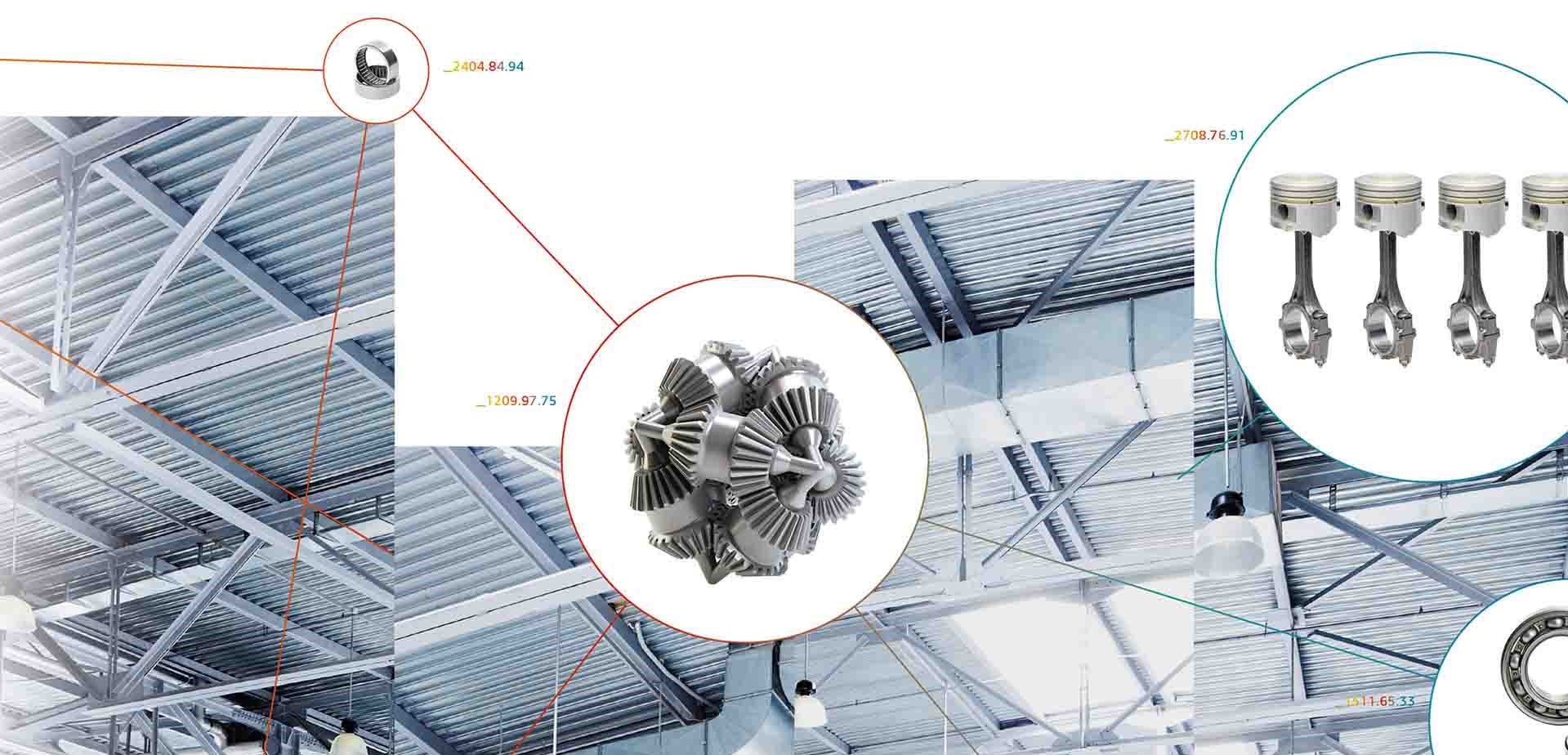
Learning from data through analytics, Interview with Morgan Zimmermann, CEO of NETVIBES -EXALEAD, Dassault Systèmes.
The “factory of the future” is a fashionable expression at the moment. What is your interpretation of it?
The factory of the future encompasses a number of buzzwords – internet, industrial, IoT, digital twin, etc. – all connected to digital transformation. Using new technologies, we can capture much more data than before. Many companies talk about digital twins, by which they mean that they can take data from the real world and create a representation of a physical object, which could be a machine, a production line or a whole factory. Analytics and advance prediction functions then allow them to anticipate problems.
However, that approach is seriously limited, because it only uses real-world data as the learning input. Without any reference base for projections, it is very hard to correlate, segregate, interpret and contextualize the data. This is why we decided that real-world data should not be projected onto a representation of the object (a “dead” image), but onto a complete virtual model, which can be fully configured and simulated, and this is what we call the 3DEXPERIENCE TWIN.
By reconnecting the virtual and the real worlds, we can generate infinite possibilities. For example, this allows companies to devise “What if?” scenarios and create new data for AI algorithms by simulating extreme usage conditions that are rarely, if ever, encountered in the real world.
How can data be used to support collaboration?
Twenty years ago, Dassault Systèmes made the first digital mock-up of the Boeing 777, and that became the catalyst for multi-discipline collaboration. Today, all business processes are digitalized. From program resource allocation to cost management and logistics, everything within these systems is digital.
Accordingly, analytics and artificial intelligence are providing opportunities to enhance performance and collaboration. They allow all staff members to understand how their decisions affect the company’s performance (program price, production costs, logistics), and so they ensure that everyone involved in performance enhancement complies with the company’s priorities.
How do you see the future of manufacturing?
Over time, manufacturing has moved from local optimization, at the factory level, to holistic optimization involving integrated operations. But the real challenge is to overhaul what we call the “Value Network.” In the new ecosystems, everyone will be able to rethink entirely their contribution to the overall value chain and establish new business models.
This will result in greater agility, infinite development opportunities and new ways of increasing competitiveness. So I’m very optimistic about the future of the manufacturing sector and the companies that work in it.