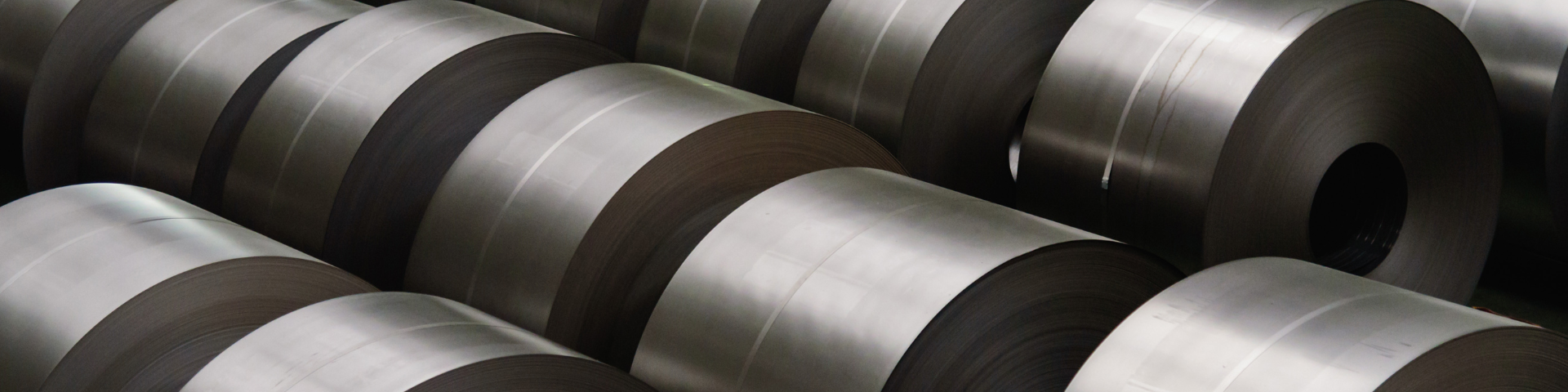
Ep: 37 Moving the Metals Industry Toward Sustainability
Tune in today to discover how the metals industry can make sustainability a reality
Gain Insight on DELMIA’s Green Metals Initiative
Listen to our experts as they discuss the challenges and opportunities in transforming the metals industry and making strides toward sustainability. Dassault Systemes’ Bertrand Orsal, Dorin George Derebei, and Prashanth Mysore dive deep into the importance of making a transformation toward green metals. You’ll hear about the importance of decarbonization, what new plans and processes lay ahead, and the role of virtual twin technology in steelmaking. The guests also highlight the need for balancing supply and demand, adopting circular economy principles, and leveraging Industry 4.0 technologies to optimize operations and reduce carbon footprint.
Discover more
Website: DELMIA Infrastructure, Energy & Materials Solutions
Website: Metals Factory of the Future
Website: Green Steel: Can We Make Heavy Industry Have a Lighter Impact?
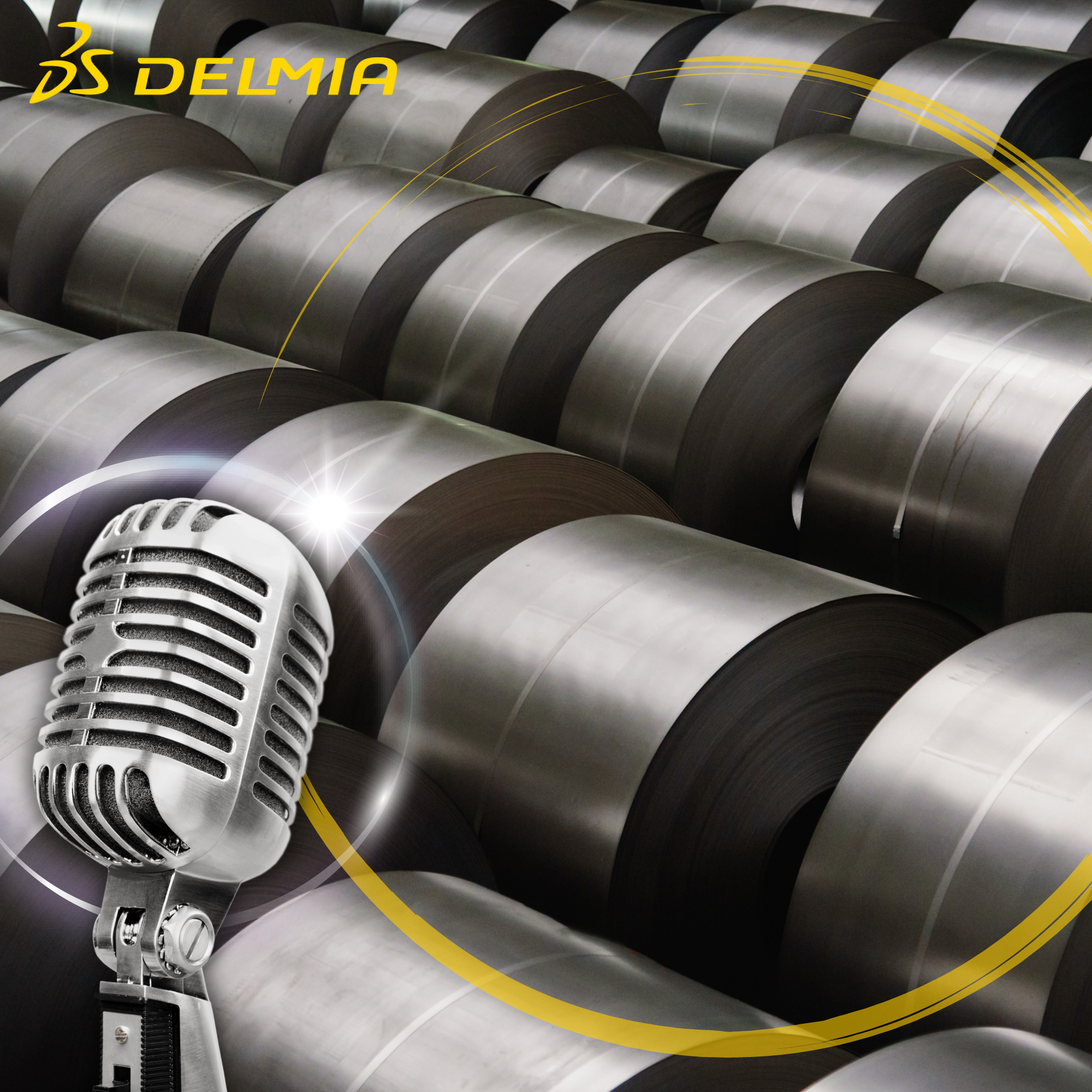
You can follow the DELMIA "Global Operations on the Go" podcast on Apple podcasts, Spotify, YouTube Podcasts, Deezer, by RSS or wherever you get your podcast
------------------------------------------------------Transcript-----------------------------------------------------------------
Moving the Metals Industry Toward Sustainability
Panelist discussion
[00:05 - 00:17] THERESE: Welcome to our DELMIA podcast, Global Operations on the Go. Tune in to this special edition featuring a panel discussion on green metals and sustainability.
[00:18 - 00:29] PRASHANTH: Good day everyone. My name is Prashanth, Mysore. I have two of my experts on green metals and sustainable metals industry. And I'll let them introduce themselves. Bertrand, do you want to talk about yourself, please?
[00:30 - 00:41] BERTRAND: Yes, hello, thank you very much. So I am the expert for metals and minerals for the system in the industry, infrastructure, energy and materials here at Dassault Systemes for two years now. And before this, I had a career in the metal industry.
[00:42 - 00:53] PRASHANTH: Thank you, Bertrand, and let's go to Dorin.
[00:54 - 01:17] DORIN: Hello, hello. I come from the industry processes team. I joined Dassault almost one year ago. I focus my expertise on the metal industry. And before that, I come with 20 plus years of experience in various positions in the business division east.
[01:17 - 02:05] PRASHANTH: Thank you so much. Myself, I am Prashanth Mysore. I’ve been with the DELMIA brand for 24 years and I'm loving it! And I belong to the world strategy team and marketing from DELMIA to support you on our journey towards sustainable metals in the industry—the sustainable green metals industry. So, on that note, let's introduce the topic. That’s a topic of greater interest; the topic of our infrastructure, energy and materials industry, which is steel. Let's introduce the steel and metals topic. Why are we focused on this lovely industry, which is being branded as evergreen. No infrastructure project can go without the metals in the steel? And to talk more about it, the most knowledgeable person on this topic. Bertrand, do you have a view on this, please?
[02:06 - 03:00] BERTRAND: Yes, of course. Thank you, Prashanth. So yeah, we are now facing a huge transformation in the metals industry, and especially for steel with the decarbonization of production. And this is a huge challenge because the requirement is to create new plans. One billion euros projects, every time, new processes, new ways of working. So we at Dassault Systèmes, we support this kind of transformation. We have the tools to help make mission happen. And this is why we are now focused on this industry. Regarding our experience, our footprint in this industry comes with a very mature solution from organization of the operation and with the virtual twin for the steelmaking.
[03:01 - 03:26] PRASHANTH: It’s all in billion dollars, isn't it, Bertrand? It's awesome. Adding that it's a great opportunity for us to really be on a transformation journey on a multi-billion dollar industry with a lot of references--which we already have a lot of good customers who are vouching for our solution in here. So on that note, Dorin, yourself, could you please share your thoughts on metals industry challenges, and how are we trying to address it?
[03:26 - 05:20] DORIN: Okay, so I will focus a little bit on the debate around Europe because to tackle this debate worldwide, it's job specific. The main challenges, nowadays, on Europe’s side is at the level of supply and demand balancing, despite if you've already tackled being green or if you're a little bit early into this adoption of the new technology. Basically…let's not forget that after the pandemic period, in the eastern part of Europe, we have a war that unbalanced the supply not only at the level of affordable coal and iron ore, but also at level of energy. This being said, without having the proper sourcing, a lot of businesses had to adapt fast. And how do we adapt fast? Of course, by having clear visibility, which we know by now that the Dassault Systèmes offer to integrate the supply chain as best as possible and extend the level of supply chain more and more for us to be able to adapt fast to this type of crisis. More than this, let's not forget that the demand vulnerability increased. Why? Because, as probably you know, and as Bertrand already mentioned, the race towards the green industry introduced some new legislation like the carbon border adjustment mechanism that entered this year into the sustainability path. And of course, all of this put together, put some pressure points not only on the external part of the integrated supply chain, but also inside the actual processes. These are currently the major challenges that Europe is facing.
[05:21 – 07:29]PRASHANTH: That's about sustainability and how we reduce our carbon footprint from this carbon intensive industry. It's always great to hear from experts like yourself, Dorin and Bertrand. Talking about the “how”, we, the beautiful brand DELMIA, have a vision regarding the industry and having considered the market sizing and potential. Let me take that up. You know, as you rightly said, global mandates call for decarbonization and the adoption of circular economy. The talk of the town is circular economy and circular principles. And we all know that based on some of your experiences as well, traditional methods of production and manufacturing is giving way to a very innovative solution. That's when you spoke about the move towards sustainable operations. It sometimes seems like a difficult task, but with DELMIA and Dassault Systèmes’ platform capabilities metals companies, including the upstream processes like mining, can confidentially transform their operations for more sustainable value growth and competitiveness and resiliency. Here at DELMIA which is a configurable solution which enables our customer on five distinctive business processes like optimizing plant operations, optimizing production process in metals industry, collaborative for innovation, collaboration for innovation for single source of information and obviously execution. Management is all about how you plan, you validate everything, but how do you execute it using industry 4.0 principles and IOTs and all? We also have a sustainability journey for lifecycle assessment. It’s a beautiful different step which DELMIA offers in facilitating all the metals companies to companies corporate development strategy towards automated operations this helps companies to improve enterprise-wise visibility, maximize utilization and centralizes data for decision automation or data-driven operations excellence. So, that's about DELMIA and that's the system's value towards this metal industry, right? So having said that, Dorin, I come back to you. Can you share the business model context for steel and metal opportunities nowadays well if i am to compare the current model nowadays?
[07:30 - 09:29] DORIN: There are fast-adopted versus the old models. I will say only two things. In the past, all the businesses were focused on optimizing their main delivery KPIs and their customer satisfaction KPIs. Nowadays, due to all the challenges put together and the pressure points given by the market, everyone is considering adopting more a push-pull model. Meaning the push model will be given by the demand challenges as I already mentioned. Together, the part of the customer approach is where, again, the demand vulnerability I have emphasized it in the past. And the pool model will be based on energy and supply, where basically they have to put together inside the business this constant balance between these two separate models. As you already mentioned we have the technology to do it we have the optimizing part where we have the technology to do it we have the optimizing part where we can treat inside our S&OP systems and in master planning this part. But we also have to track and follow that all of these steps are executed and all of these steps of course have a round back inside this new business models that are adapted quite fast. More on this a lot of businesses if in the past they worked on the made-to-stock and made-to-order type of models. Nowadays, due to all the challenges around the industry they adopt more and more the path to 100% going to make to order. So this being said, and as you already emphasized, we are able to sustain this type of challenges starting with the design going through optimizing and circling back to manufacturing follow-up tracking and quick feedbacks.
[09:30 - 10:32] PRASHANTH: Oh, it's all about balancing isn't it? Which are just in time or somehow in time principles based on lean principles as well. And we bring in Kaizen and Kanban as an overall part and parcel of the whole process. Dorin, thank you for that answer. If we talk about, you know, you spoke about planning and optimization. And if I ask you this question about which part of our DELMIA domain is considered as a flagship for the steel and metal industry. Now, let me take that question. There's no brainer here. This is all about planning and optimization, which is, you know, from Quintiq—DELMIA Quintiq, which is kind of a de facto solution on aluminum and steel in addressing most of their business process around master production scheduling and detail scheduling and manpower planning and sales and operations planning as well. Which is proven solution, which most of our customers are using it, happily using it. Happy customers like our partners enjoy deploying our solution at multiple customer places. Right?
[10:33 – 11:26] DORIN: This is why the (DELMIA) Quintiq integrated solutions are the flagship for our flagship for the metal industry. Due to the fact that you can see from a high level the balance between the supply and the demand with the clear visibility on a planning horizon given. You can focus on one site or multiple site being integrated at level of master planning. You can drill down to go and see your detail planning for each capacity or for each site individually, but you can follow it through and this is the beautiful part because by coordinating in with detail scheduling for each operation or for a series of operation given for this particular unit, you have a grip. You have the bridge between high level planning and plant site coordination.
[11:27 - 11:55] PRASHANTH: Multi-level planning, right? Yeah, that's the, that's the. Main thing actually. So that's a beautiful point, which is into what is our best practice? What are the industry process experiences, which DELMIA actually offers. Bertrand, if I bring in over here, I do know, you know, that, three or three of the main industry process experiences, which you are involved in defining, for the green steel production as well as for value path. Could you please share a bit of an overview on industry process experience, which DELMIA offers here?
[11:56 - 13:34] BERTRAND: We absolutely. And actually the, the wide range of solutions that DELMIA propose to the steel industry. But, it's beginning with the planning and scheduling of the production with several specific, uh, IPs, depending on the, on the level of operations. And it starts with sales and operations planning—S&OP of course, for the high level view of the production. But then when you dive deeper in details, you, you will. Go to the scheduling with a master of productions in the scheduling when it is at, uh, at a shorter term for the production. And then when you go really directly to the shop floor level, uh, you have what you call the detailed scheduling and then of course you can have many different kinds of adaptations of these, uh, IPs to some parts of the process, like the example of the hot charging between the continuous casting and hot hauling. Then, then when you have a nice plan, a nice schedule, you need to execute it. And this is then the next IP, which is called production execution. Sometimes in the field of the steel, we will call it MES or MOM for manufacturing operations management. So DELMIA is able to tackle all these steps of planning the pollution and execute it. But also of course, DELMIA can tackle solutions like Dorin said, for design and engineering with the plant layout definition with digital manufacturing and so on.
[13:35 - 14:16] PRASHANTH: Beautiful articulation. You know, Bertrand, that feels that you belong to the DELMIA brand, not to industry. Well articulated by an industry person like you. I know it speaks of volume of DELMIA value here for steel and the metals industry and steel and aluminum in particular. Detail scheduling, master production scheduling, and some of the specific IPs like production execution are really, really, the talk of the town in this industry and with most of our customers. Right. So Bertrand, you lead sustainable steel manufacturing, sustainable and green steel. And how's that? How does it look? Is it looking promising? Is it really helping us to really decarbonize our lovely planet? Do you want to say something on this?
[14:17 - 16:34] BERTRAND: Oh, yes, sure. It's one of the main topics worldwide now because actually, steel making nowadays, depending on the sources, people say that it represents between eight and 10% of the global CO2 emissions. And we are just talking about the CO2 emissions. There are other impacts of the steel industry. And so we, we are now on a roadmap, completely reduce almost and almost remove these CO2 emissions. With the first step over the, the current decade until 2030, most of the steel makers, they, they want to do, to make a first try of the new technologies to decarbonize and especially the direct reduction of the iron ore. And then there is a second step to the decarbonization that goes until 2050, where all the facilities, the conventional facilities will be completely stopped and changed into a new decarbonized process. And it tackles many, many challenges. So, the main one being this, uh, step of the iron ore reduction that I already mentioned the blast furnaces, they are generating most of these eight to 10% of CO2 emissions worldwide. And by changing the process and using green hydrogen and clean energy at this step, we will be able to completely remove this source. But then there is also all the downstream supply chain after this step. And the steelmaking, the casting, the rolling and so on where we will have also improvements to do and especially, uh, new ways of working like for instance, combining the continuous casting and the hot rolling mill into what we call the direct charging. And this will be also a challenge and, uh, we are here actually to help at all these steps on the thinking, the innovation, the design and engineering of these facilities, the simulation, but also the follow-up of the construction of these new facilities or the changes and of course the future operations and productions in this field.
[16:35 – 17:44] DORIN: If I am to complete Bertrand, there are various technologies to adopt this path. Neither of these technologies are at full maturity level. This means that, indeed there are two targets, 2030 and 2050. These targets will be achieved by getting all of this technology mentioned by Bertrand to a sustainable level of maturity. More than this, based on these new technologies we have to place also a sustainable circularity on into recycling because all of this technology will need a high quality scrap and sensing but also we will conflict with the communities around it depending on that as we go. If I have two new will have to have sustainable hydrogen supplies and also renewable power sourcing to be as sustainable as possible to fulfill and supply all of these new technologies. So. the challenge is a little bit more beyond the integrated supply chain description of the current actual technologies adopted.
[17:45 – 18:23] PRASHANTH: That's, you know, that's a great supplement, Dorin, yourself, talking about sustainability and circular economy and the energy source, which is predominantly in hydrogen. Indeed definitely contributes to reduction in carbon footprint management. So Bertrand and Doreen, do you think that, you know, we in Dassault will have a greater role to play until 2030 and we have our jobs till 2050? Long way to go, mate. Thanks for keeping our jobs safe till 2050, where we are contributing to sustainability and circular economy as well. And Dorin, yourself, what should be the main points considered while articulating message to our customers and steel manufacturers?
[18:24 - 20:04] DORIN: Main points, I already touched the maturity part. So even if we follow customer that is engaged already on the challenge towards greens, but even if we tackle a customer that is on the brown side of the industry, as we call it, the maturity level. It is always the key element for sustaining a potential customer that we have in front of us because either it is technological challenge and supply challenge, either it is business process maturity that we're speaking about. The metal industry, it is not a great model for industry. 4.5. So somehow they have internal and external challenges at the same time, meaning that we can tackle all the aspects of the business process maturity, industry maturity by design and engineering with the optimization part of our solution. We can always help them to add additional value to their supply chain processes and also increase the customer perspectives’ KPI. And from the execution part, we can always reduce the stock levels and the lead times from tap-to-tap operations. So this being said, if you or we are able to identify the proper need of the person in front of us, we have what?
[20:05 - 21:56] PRASHANTH: We have the “what”? You know, you beautifully articulated and touched on industry 4.0. What is that industry 4.0? How do we contribute and make this happen? Why? One of the crux of industry 4.0 is digital twin. Are we talking about digital twin? No, we are talking about virtual twin, which is beyond digital twin for steel and metals manufacturers to visualize and optimize new products, new product introduction, new facilities and new methods of production processing, including hydrogen as their energy input here. And virtual twins are an executable virtual representation of our supply chain and manufacturing and enables most of our, most of our customers to design, plan and optimize virtually before for implementing in the real world, right? And which leads to reduce in waste reduction and increase in efficiency, and obviously validate the what if scenarios on circular manufacturing and circular economy here. In virtual twin in FX helps you visualize and model our own or your own metals factory of the future as powered by 3DExperience platform. And this covers both supply chain as well as manufacturing and then captures all the complexities including contextualization of IT and OT data and which helps in metals production network and also validate the plan in integration with real-life data. And it also provides opportunities to improve process for better service and improved delivery experience. That's about virtual twin which a lot of our colleagues and customers normally ask about. How do we actually implement virtual twin here? That's about the virtual twin. And with that in mind, to talk more about virtual twin experience, none other than Bertrand Orsal, my colleague, who's an industry expert who has spent a lot of time in green steel manufacturing throughout his career. Let's hear from Bertrand. Bertrand, all to you!
[21:57 - 23:13] BERTRAND: You know, some companies, industry may be willing to take one solution for one part, one solution for the others. But I think it's important to understand that, you know, it's a lot of work, but with the fact that we cover many points at the same time. They can rely on us to have a combination of solutions that will work together in an easier way. And this is the main train that we see actually in the request from our customers, to have adaptable solutions that can cover at the same time the planning and scheduling and the execution for today. And this is really a big challenge. And tomorrow, which is the way and showed in the value pass that we issued recently in the industry for the green steel transformation. Tomorrow to use all this data, all this production data in the virtual twin of the plants and of the supply chain and of the product in order to go find new improvements, to simulate, to define the next investments. And all these functionalities that the virtual twin brings to the customer.
[23:14 - 24:15] PRASHANTH: Beautiful. Well articulated, Bertrand. Thanks to yourself and Dorin for making these two customers happen. They're fascinating customers. And they really talk very high about the Delmia solutions for this particular industry. Talking about, you know, to all of our audience, there are beautiful link on metals plant of the future to whatever you want to validate, whatever you heard today. Metal plants of the future talks about our virtual twin experience, all of our solutions around planning and optimization, manufacturing operations management, lean collaboration, and also the digital twinning, which is all about virtual twinning with respect to creating a new plant and planning and simulating of the whole new plant, including robotics and automation, all of them. You can visit our website, which is an experiential walkthrough. It has a beautiful 3D animation walkthrough to understand the whole steel manufacturing process. This is metals plant of the future, and which our team has actually developed. Oh, coming to the conclusion, Bertrand, what are the key takeaways that you want our listeners to take back in mind?
[24:15 - 25:05] BERTRAND: Well, the fact that we at Dassault Systèmes, we are, let's say the virtual twin experience company now, and this is the summary of what we can bring to the steel industry actually. And the fact that this is a unique offer on the market. Because in the competition, you will find solutions for planning and scheduling there, execution there, digital twin there, thought design and so on. But with this virtual twin experience that we provide, we can gather all this in a single environment. And this is the beauty of it. And also the beauty to go with this transition to the green steel. This is my main takeaway actually. And the thing that makes me wake up every morning.
[25:06 - 25:13] PRASHANTH: That's the passionate statement, Bertrand, the beauty of virtual twin experience and the new way of actually helping our customers on their sustainability journey. Dorin, any key takeaway for our listeners?
[25:14 - 25:41] DORIN: Yeah, talking about what makes me get up in the morning. It's simple. It is a long race. The challenge is on the green path towards metal industries to sustainability will imply a lot of challenges on this race. It is a long ride. And personally, I think that we all should be proud that we are part in this race with all the challenges implied.
[25:42- 26:03] PRASHANTH Proud to be part of in this race is a great comment, Dorin. Thank you so much for that. Thank you, Bertrand, for this lovely insight. Thank you so much. Thank you, listeners. Enjoy your day and think of the beautiful Delmia solution, which is as sturdy as steel.
[26:04- 26:10] THERESE: Thanks for tuning in. You've been listening to DELMIA’s podcast, Global Operations on the go.