Airbus
다쏘시스템 솔루션 덕분에 당사는 프로세스, 방법, 도구를 조화롭게 결합해 귀중한 시간을 절약할 수 있었고 기술 혁신에 더 많은 시간을 할애할 수 있었습니다.
Airbus는 ‘Future by Airbus(에어버스가 이끄는 미래)’ 프로그램의 일환으로 2만 명을 대상으로 2050년 항공 여행에 대해 질문했다. 그 결과 ‘항 공료가 저렴해지고 친환경적이며 보다 지속 가능 한 비행이 이뤄지고 스트레스가 줄고 더 조용하 고 재미있는 여행이 될 것’이라는 예상 응답이 나 왔다. 과거 승객들은 제시간에 안전하게 목적지에 도착하는 것으로 만족했다. 오늘날 항공사들은 승 객의 비행 경험에도 초점을 맞춘다. 최근 장거리 제트 여객기 제품군에 합류한 Airbus의 새 항공 기인 A350 XWB(초광폭 동체)를 제작한 항공기 제조업체는 승객의 비행 경험이 긍정적일 것이라 고 확신한다. Airbus의 항공기 700대 주문 예약 이 이미 완료된 것을 보면 고객들의 반응은 꽤 괜 찮은 것으로 보인다.
전혀 새로운 항공여행
A350 XWB는 모든 부문에서 고객 경험을 염두 에 두고 설계됐다. A350 XWB는 최첨단 기술을 적용해 설계한 공기 역학적 날개와 지능형 기체 로 이뤄져 있다. 기체와 날개 구조 모두 탄소섬유 로 제작됐는데, 탄소섬유는 제트 항공기 전체의 50% 이상에 사용됐다. Airbus의 A350 XWB 프 로그램 부문 부사장 겸 책임자인 디디에 에브라 (Didier Evrard)는 “A350 XWB는 경량 소재인 탄 소섬유를 광범위하게 사용한 최초 항공기로 연료 효율성이 크게 개선됐다”며 “더 조용하면서도 공 기 역학적 효율이 우수하기에 앞으로는 전혀 새로 운 항공 여행을 경험하게 될 것”이라고 말했다. 이 러한 목표를 달성하기 위해 Airbus는 다쏘시스템 의 3DEXPERIENCE 플랫폼을 배포해 엔지니어 링부터 제조에 이르는 가치 체인 전체에서 전 세 계 협업 솔루션을 구동하면서 과거의 프로그램에 새로운 개선 기능을 통합해나가고 있다.
다쏘시스템 솔루션 덕분에 당사는 프로세스, 방법, 도구를 조화롭게 결합해 귀중한 시간을 절약할 수 있었고 기술 혁신에 더 많은 시간을 할애할 수 있었습니다.
전례가 없었던 협업 혁신
Airbus 혁신 전략의 최우선 순위는 ‘전례 없는 수 준에 도달한 협업’이다. 에브라 부사장은 “당시 당 사에게는 A380과는 근본적으로 다른 방법과 도 구를 개발해 모든 참여 엔지니어가 동일한 설계 플랫폼에서 작업하도록 보장하는 동시에, 단일 환 경에서 원활하게 의사소통할 수 있도록 조치가 필 요했다”고 말했다. A350 XWB 프로그램의 경우 매일 최대 4,000명이 플랫폼에 접속했는데 이 중 85%가 가치 체인에 소속된 사람들이었다
2007년부터 2011년까지 Airbus에서 A350 XWB PLM 프로그램을 책임졌던 앙투안 스코토 (Antoine Scotto)에 의하면 이전 프로그램은 현 장별로 자체 디지털 실물 모형(Digital MockUp)을 보유하고 각자 작업했는데, 의사소통이 불 충분한 탓에 설계 시간이 늘어나고 오류가 속출해 비용이 상승했다. 이에 Airbus는 여러 개발 플랫 폼을 ENOVIA라는 하나의 플랫폼으로 통합해 내 부 직원과 외부 회사가 함께 액세스하도록 조치했 고, ENOVIA를 사용하면서 과거 며칠씩 걸렸던 동 기화를 단 몇 분만에 해결할 수 있었다. Airbus는 개발 프로세스를 리엔지니어링해 설계 단계부터 생산에 이르는 모든 부문에서 원활하게 협업을 진 행했는데 앙투안 스코토는 “3DEXPERIENCE 플 랫폼 덕분에 프로그램 관계자들이 서로 아이디어 를 자유롭게 교환할 수 있어 효율성이 높아졌다” 고 회상했다.
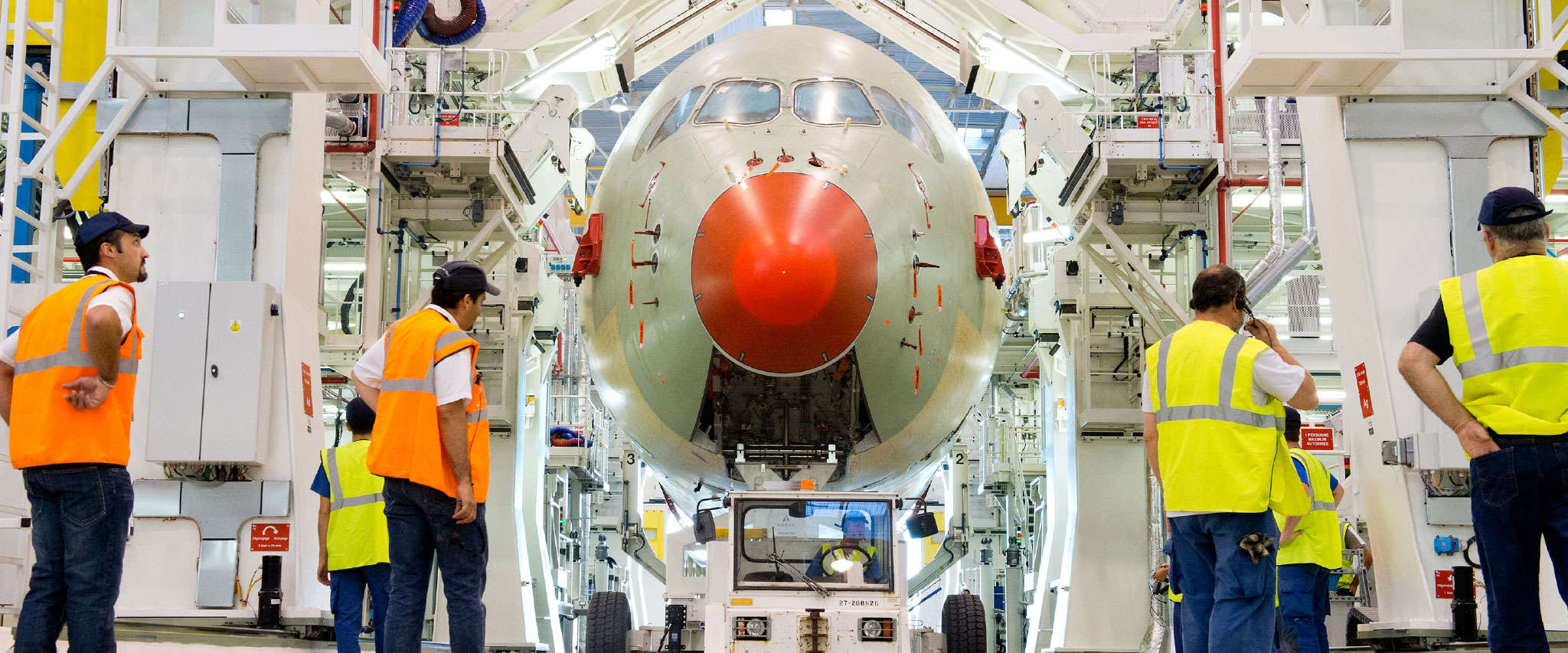
단순화된 프로세스로 품질과 서비스 개선
에브라 부사장은 “납품 기한을 지키기 위해 매우 촉박한 개발 일정과 신속한 생산량 증가 등 수많 은 과제에 직면했는데, 3DEXPERIENCE를 사용 하면서 설계 품질과 효율성이 크게 향상됐다”고 호평했다. 앙투안 스코토는 “CATIA를 사용해 항 공기 구조, 설비 시스템, 튜빙, 복합재료 부품, 전 기 시스템을 3D에서 완벽하게 설계했다”고 말했 다. 아울러 그는 이렇게 덧붙였다. “엔지니어들 이 설치 계획을 업데이트하는데 소요되는 시간이 50% 단축됐고 수작업으로 2D 도면을 제작할 경 우 유발되는 설계 변경 요청 건수가 25% 줄었습 니다. 모든 것을 컴퓨터 상에서 설치·장착·확인 했고 오류가 있을 경우에도 실제 설치 전에 수정 할 수 있었습니다.”
Airbus는 DMU를 사용해 제조 현장과 설계 사무 실을 연결했다. 앙투안 스코토는 “설계 사무실에 서 적용한 모든 변경 사항이 제조 현장에 실시간 으로 전달돼 툴링 제작 시간이 대폭 단축됐다”고 말했으며, 에브라 부사장은 “설계 품질도 매우 뛰 어나서 제조 현장에서 재설계 작업을 요청한 적이 거의 없었다”고 덧붙였다.
엔지니어들은 SIMULIA를 통해 실제적 비선형 분 석을 수행해 설계 프로세스의 초기 단계부터 항 공기 구조의 강도와 거동을 예측했다. Airbus는 CATIA 설계 정보를 기반으로 초대형 시뮬레이 션 모델을 제작하고 실물 크기의 비선형 구조 시 뮬레이션을 실행했다. SIMULIA를 사용해 근사 적인 선형 분석 기법에서 보다 정확한 비선형 분 석으로 전환함으로써 특정 상황에서 해당 구조가 실제로 어떻게 거동하는지 보다 정확하게 이해할 수 있었다.
제조, 엔지니어링에서부터 공장 운영에 이르는 모 든 부문에서 DELMIA를 사용해 프로그램 리드 타 임을 확보하고 항공기 제조 가능성을 보장했다. 또한, DELMIA를 통해 조립 현장에서 기본적인 조 립 운영과 지원 자동화에 이르는 산업 설계 및 최 적화 역량이 강화됐다. Airbus A330의 경우 최종 조립 라인 주기에 약 4개월이 소요됐지만, 객실을 조기에 설치한 A350 XWB 조립 프로세스는 30% 단축됐다. 다쏘시스템의 산업 서비스가 A350 XWB 전체 환경 구현 및 배포를 지원했다. 에브라 부사장은 “Airbus와 다쏘시스템은 매우 긴밀하게 협업했다”고 회상했다.
A350 XWB용 단일 DMU를 사용하는데 따르는 이점은 엔지니어링과 제조 프로세스에 머물지 않 고, 고객 서비스에 활용되는 하위 프로세스로 이 어진다는 것이다. 이전 프로그램에서는 고객 서 비스를 수작업으로 그린 2D 일러스트에 의존했 지만, Airbus는 3DEXPERIENCE 플랫폼이 제공 하는 디지털 연속성을 통해 DMU를 직접 재사용 하는 고객 서비스 프로세스를 구현했다. 예를 들 어 Airbus는 3DVIA를 사용해 DMU 내에서 액세 스, 조회, 탐색이 가능한 SRM(Structural Repair and Maintenance) 시스템을 구현해 구조 부품 에 허용치 손상이나 수리가 발생했는지 확인할 수 있다. 따라서 부품 확인이 훨씬 수월해진 것은 물 론, 2D 일러스트와 설명서 제작 시 더 이상 수작 업이 필요치 않다.
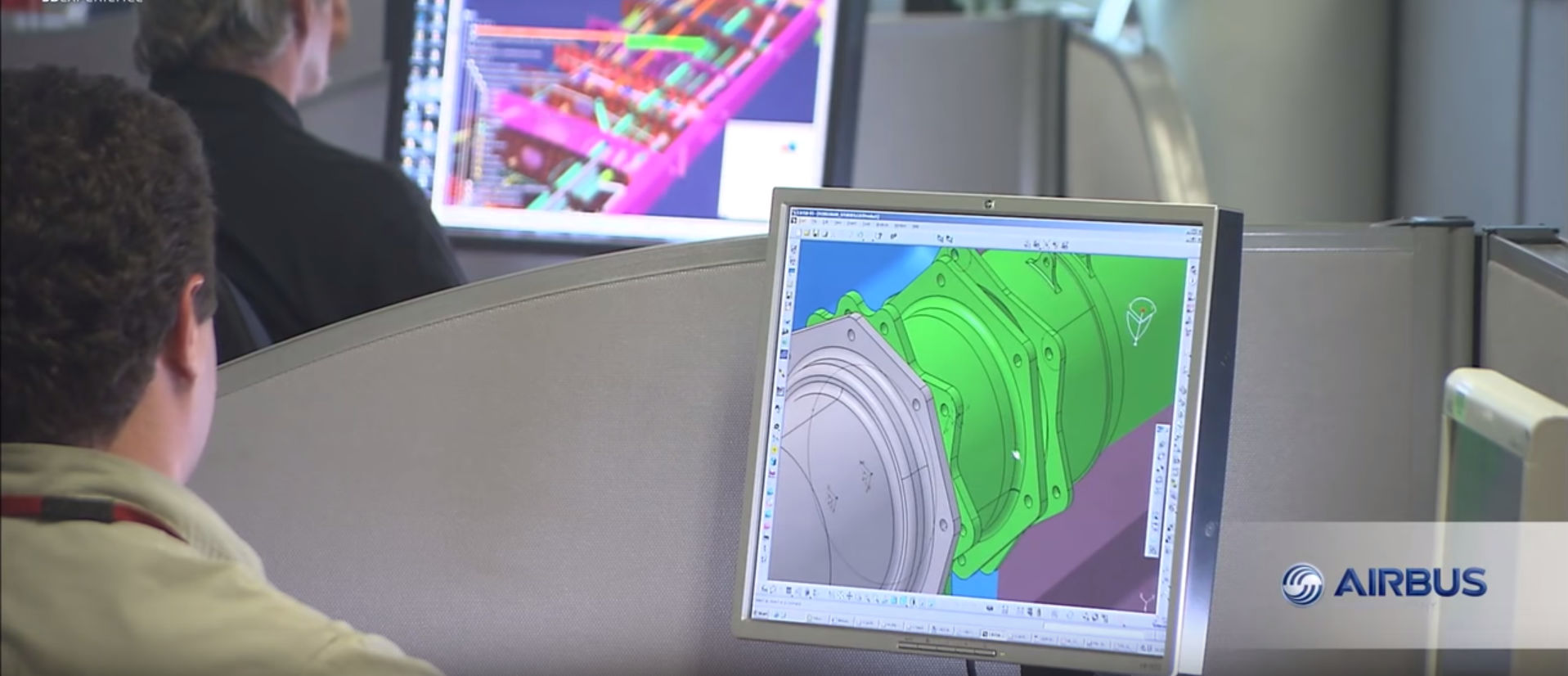
첫 비행, 그 이상의 경험
3DEXPERIENCE 플랫폼은 Airbus의 A350 XWB 프로그램이 성공할 수 있도록 지원한 핵심 요소 가 됐다. 2013년 6월 14일 A350 XWB가 첫 비 행을 시작하는 순간 모든 진실이 드러났다. 에브 라 부사장은 “첫 비행은 순조롭게 진행됐고 지난 2달 동안의 비행 시간은 이미 270시간을 넘었다” 고 말했다. 그는 마지막으로 다음과 같은 말을 남 겼다. “A350 XWB 프로그램을 진행하는 과정에 서 이 프로그램의 복잡성과 아웃소싱 관계자 수로 인해 기술 및 조직 면에서 어마어마한 과제에 직 면했습니다. 그렇지만 다쏘시스템의 솔루션 덕분 에 프로세스, 방법, 도구를 조화롭게 결합해 귀중 한 시간을 절약했고 기술 혁신에 더 많은 시간을 할애할 수 있었습니다. 이번 프로그램보다 더 설 레는 과제를 만나기는 힘들 겁니다.”